Injection Molding Service
3DEXPERIENCE Make Online Injection Molding Service | Compare quotes online from different service providers.
SECURE PAYMENTS
Via payment card or purchase order
PROTECTED IP
Your data is confidential and secure with us. Use your own Non Disclosure Agreement
INSTANT QUOTE
For 3D Printing and CNC Machining, get quote in few seconds.
Discover 3DEXPERIENCE SOLIDWORKS for Makers
Injection molding service with 3DEXPERIENCE Make
3DEXPERIENCE Make is an On-Demand Manufacturing platform, which connects designers or engineers with industrial Injection molding service providers. Injection Molding service is today used for small series or large series, whatever your industry or your project.
Our network of Injection service providers offers hundreds of materials for your project, Plastic (ABS PC, ABS, PA, PVC, PEI, HDPE, LDPE, PEEK, PA, PC, POM, PP, PS, TPE, TPU, etc...), Metal (Stainless steel, Aluminium, etc...) or Composite (PA Glass, etc...), and processes Injection Molding, Casting, Blow molding and Vacuum molding.
Which Injection molding subprocesses, 3DEXPERIENCE Make offers?
Casting
Blow molding
Vacuum molding
Discover How 3DEXPERIENCE Marketplaces Boost Your Design to Manufacturing Process
You’re in good company. Thousands of leading companies from all industries use our solutions.
Online Injection molding service: how does it work?
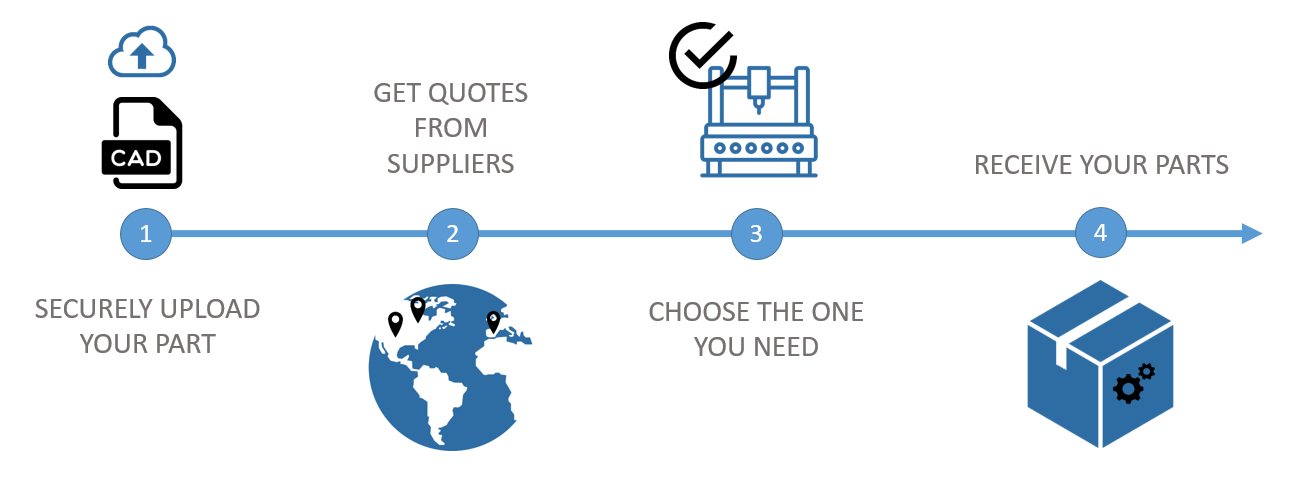
Materials of our Injection molding service Providers
Metal
Stainless steel, Aluminium...
Composite
PA Glass...
Plastic
ABS, ABS PC, HDPE, LDPE, PA, PC, PEEK, PEI, POM, PP, PS, PVC, TPE, TPU...
Features to help you
Check & repair or Geometry check is a feature that helps you to understand Geometry issue of your part and could repair it live and online.
Check & Repair
Check & repair or Geometry check is a feature that helps you to detect geometry issue on your part and repair it online and live.
Manufacturability Check
This feature is available only for 3D Printing service. It helps you check the manufacturability of your part, depending on the materials and the process.
Instant quote engine
Receive in seconds several quotes thanks to our instant quote engine.
What is Injection molding?
What is Injection molding?
Molding is a manufacturing process that involves shaping a liquid or malleable raw material by using a fixed frame, known as either a mold or a matrix. The mold is a hollow cavity receptacle, commonly made of metal, to pour liquid plastic, metal, ceramic, or glass material. In most cases, manufacturers derived the mold from the initial pattern or template of the final object; its main objective is to reproduce multiple uniform copies of the final product. The liquid must cool and harden inside the mold to achieve the final configuration. Injection molding services generally use a release agent or ejections pins to remove the mold.
We are surrounded by both ordinary and complex objects manufactured due to the molding manufacturing process. Molding has occurred throughout the millennia. Historians have discovered evidence of its usage as far back as the Bronze Age, where stones were used as molds to produce spear tips.
Modern molding processes include plastic injection molding, Liquid Silicone Rubber (LSR) molding, overmolding, and insert molding. The plastic injection molding process could produce customized prototypes and end-use parts. The standard process eliminates the use of embedded heating or cooling lines within the molds so that molders, also known as molding technicians, can carefully monitor fill pressure, aesthetics, and overall part quality.
- Liquid Silicone Rubber (LSR) molding is a highly flexible material, meaning its molded state is permanent and remelted; it is not possible at all, contrary to thermoplastic. For CNC Machining, you need a specifically designed LSR molding tool, thus providing different surface finish options for the end-use LSR part.
- Overmolding allows a single part to contain multiple materials. Once you have the molded substrate part’s entire run, you can set up overmold tooling on the press. It is then hand-placed into the mold and overmolded with either a thermoplastic or liquid silicone rubber material. Insert molding is similar to overmolding, but most commonly uses a preformed metal substrate part that overmolds it with plastic to create the final piece.
How to reduce the cost of Injection Molding Service?
Injection molding and injection molding service have gained global popularity. Worldwide, the injection molded plastics market was valued at around 265.1 billion U.S. dollars in 2020. The plastics injection molding industry is anticipated to grow at an astonishing rate of 4.6% each year from 2021 to 2028. Many determining factors set the market price for injection molded products. This market expense is set by the costs of:
- raw materials
- construction/equipment costs
- labor
Depending on the complexity of the process and final product, these numbers can translate to a costly injection molding plastics manufacturing process. Continue reading to follow Dassault Systèmes’ tips for costs without sacrificing the quality of the final product.
Tip 1: Eliminate Undercuts
The first tip to reducing the cost of injection molding is to eliminate undercuts in the design where it is possible. Undercuts tend to keep the product snagged in the mold, preventing proper ejection. These snags could result in full manufacturing line product losses. These more complex designs result in more expensive design costs and molding processes. In the injection molding world, complexity and difficulty usually translate to higher costs. The best solution is to eliminate undercuts. But, if elimination is not possible, choose one of the following solutions to make your undercut design more injection molding friendly:
- Design sliding shutoffs to create hook-and-clip mechanisms. These are also known as telescoping shutoffs, and they are commonly utilized when linking together two mold halves.
- Replace undercuts with bump-offs, instead of a side-action cam. This involves machining an insert so the undercut may be applied, and the area can be bolted to the mold where a pocket corresponds to the insert dimensions.
- Design the undercut around a parting line to intersect the standoffs. Perhaps even zigzag the parting line to intersect the features.
Tip 2: Core Cavity
Can the product have a hollow center? If so, it will require less for manufacturing, as well as lighter shipment to distribute. The optimal method to design an injection molded part for cost reduction is to machine the tool around the cavity shape, for a hollow core. This will result in a less complex design which allows for easier material flow during the injection molding process, reducing costs.
Tip 3: Cosmetics
The phrase “Try before you buy” can apply to so many industries, including injection molding. The professionals at Dassault Systemes provide cosmetic mockup technology to create a visual 3D product before going forward with the full manufacturing process. This option to build one product before moving forward with mass production can translate to lots of monetary savings.
Try to simplify your design from a visual standpoint. Look to reduce unnecessary design features which may not provide any structural value. Engraved or embossed features, finishes, textures, and similar features all add to tooling costs, setup, and efficiency of the production process. It is always wise to focus on quality and value to your customers versus a flashy, differentiating design. A rule of thumb is to focus on designing in quality, not aesthetics first. Then, if budgets allow, extraordinary design features can be added, improving overall aesthetics.
Tip 4: Moldability/DFM analysis
Design for Manufacturing (DFM) is an analysis technique that can pay dividends for a vast array of manufacturing processes, one of which is injection molding. DFM allows for personnel from engineering design and manufacturing engineering to come together and optimize a part from both perspectives. This alignment, in the design phase, is crucial to ensuring a part or assembly which is not only manufacturable but is cost-effective to manufacture. Consulting with the injection molding process experts when designing a part for injection molding will ensure your parts follow the simplest manufacturing processes possible. Experts in injection molding may also be able to provide insight on material selection, tolerancing, and finishing operations.
Failure Mode Effects Analysis or FMEA is a tool commonly utilized within the DFM process. FMEA is specifically an excellent method to assess risk, identify and address problems and review manufacturability. Within the scope of FMEA is an ability to check for, maintain documentation about and determine corrective actions for potential failure modes before a part even enters the manufacturing processes.
For a more software-based analysis approach, engineers often seek out simulation software to see the injection molding process come to life and receive feedback about key characteristics of the molding process. As part of the Dassault Systèmes My3DEXPERIENCE platform, the Plastic Injection Engineer role allows you to seamlessly perform design optimization for any injection molded plastic part. You start from SOLIDWORKS and connect easily to the 3DEXPERIENCE platform. Then select the Plastic Injection Engineer role to assess the warpage, filling, packing, and mold cooling phases of the injection molding process. This built-in moldability analysis feature allows product engineers to assess potential failure modes such as air traps, sink marks, short shots, or weld lines. Feed circuits and cooling circuit designs can be evaluated and optimized. A design change can be quickly made in SOLIDWORKS and then the analysis can be run again in a streamlined fashion.
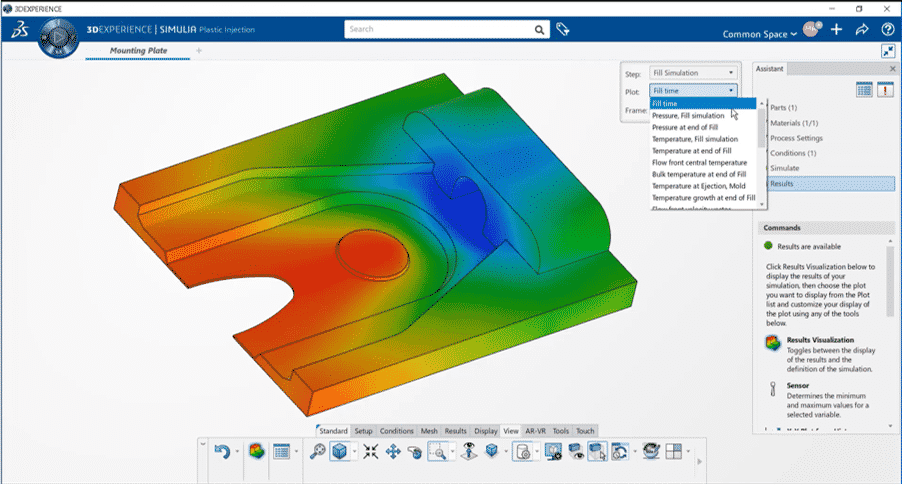
Tip 5: On-Demand Injection molding service to Reduce Cost
On-demand injection molding service can reduce cost by simply reducing bulk material or final product waste. The initial mold has been created, all that remains is manufacturing the amount/volume of final product required for market demand. The cost of injection molding can be greatly reduced by processing supply only when the demand is required. Ensuring that each injection molded product has the demand to be sold before beginning processing, ensures the highest return from minimized waste or products that have been overproduced. This is where labor costs will be factored in. The labor costs required for running a manufacturing process at full production, versus half production with the same number of employees, can be easily compared.
With Dassault Systèmes 3DEXPERIENCE Make online injection molding service, you are connected effortlessly to dozens of expert injection molding manufacturers for on-demand services, with the click of a button. We are proud to offer a vast array of subprocesses including casting, blow molding, and vacuum molding. In addition, select from materials such as metal, composites, and plastics.
Tip 6: Optimize your Part Size
The larger the size of the part, the more bulk product will be required to manufacture an injection molded product. This can be understood, simply by comparing the amount of material to make an object, versus comparing it to the amount of material that is twice the size. It will result in double the bulk material costs for the product that is twice the size. This cost reduction technique is simple: look for areas in the design where a size reduction may be tolerated and reduce the size. Note: Always ensure your design meets the structural and quality requirements before reducing the size of any feature.
Discover our other manufacturing services
Get multiple quotes for your parts in seconds