Powder Bed Fusion
Discover how Powder Bed Fusion, a 3D Printing process, also known as DMLS, SLS, SLM, MJF, EBM, works.
Introduction to Powder Bed Fusion
Powder Bed Fusion (PBF) 3D printing technology spawns products with precision. This 3D printing technique enables manufacturing a vast array of geometrically complex products using a heat source, mainly laser or electron beams, to fuse powder particles layer-by-layer, forming a solid part. Manufacturers can benefit from substantial design freedom, considering that PBF presents several viable technologies and materials.
The different Powder Bed Fusion methods notably include:
- Selective Laser Sintering (SLS) SLS 3D printing technology originated in the late 1980s at the University of Texas at Austin. Over the years, this technology has experienced remarkable advances. Basically, the process uses lasers to sinter, or coalesce, powdered material layer-by-layer to create a solid structure. The final product, rendered in loose powder, is then cleaned with brushes and pressurized air. The main materials used in the SLS 3D printing process include polyamide (Nylons), Alumide (a blend of gray aluminum powder and polyamide), and rubber-like materials. Nylons are strong and durable but do feature some flexibility, making them excellent for snap fits, brackets, clips, and spring features. Designers should consider the susceptibility for shrinkage and warping of thin parts during the conceptual phase.
- Selective Laser Melting (SLM), also called Direct Metal Laser Sintering (DMLS). The same technical principle is used to produce Selective Laser Melting (SLM) and Direct Metal Laser Sintering (DMLS) parts. Still, it is exclusively to make metal parts. SLM achieves a total melt of the powder so that single-component metals, such as aluminum, can create light, strong spare parts, and prototypes. DMLS sinters the powders and is restricted to alloys, including titanium-based alloys. These methods require added support to compensate for the high residual stress and limit distortion. Applications include jewelry and dental industries, spare parts, and prototypes.
- Electron Beam Melting (EBM) The EBM 3D printing technology attains fusion with the use of a high-energy electron beam and produces less residual stress resulting in less distortion. It uses less energy and can create layers faster than SLS. This method is most useful in high-value industries such as aerospace and defense, motorsports, and medical prosthetics.
- Multi Jet Fusion (MJF) by HP The Multi-Jet Fusion (MJF) 3D printing technique differs from the aforementioned methods because it utilizes an inkjet array to apply fusing and detailing agents, which are then fused by heating the elements into a solid layer. No laser is involved. Detailing agents are jetted around contours to improve part resolution, thus opening lifelike object production possibilities.
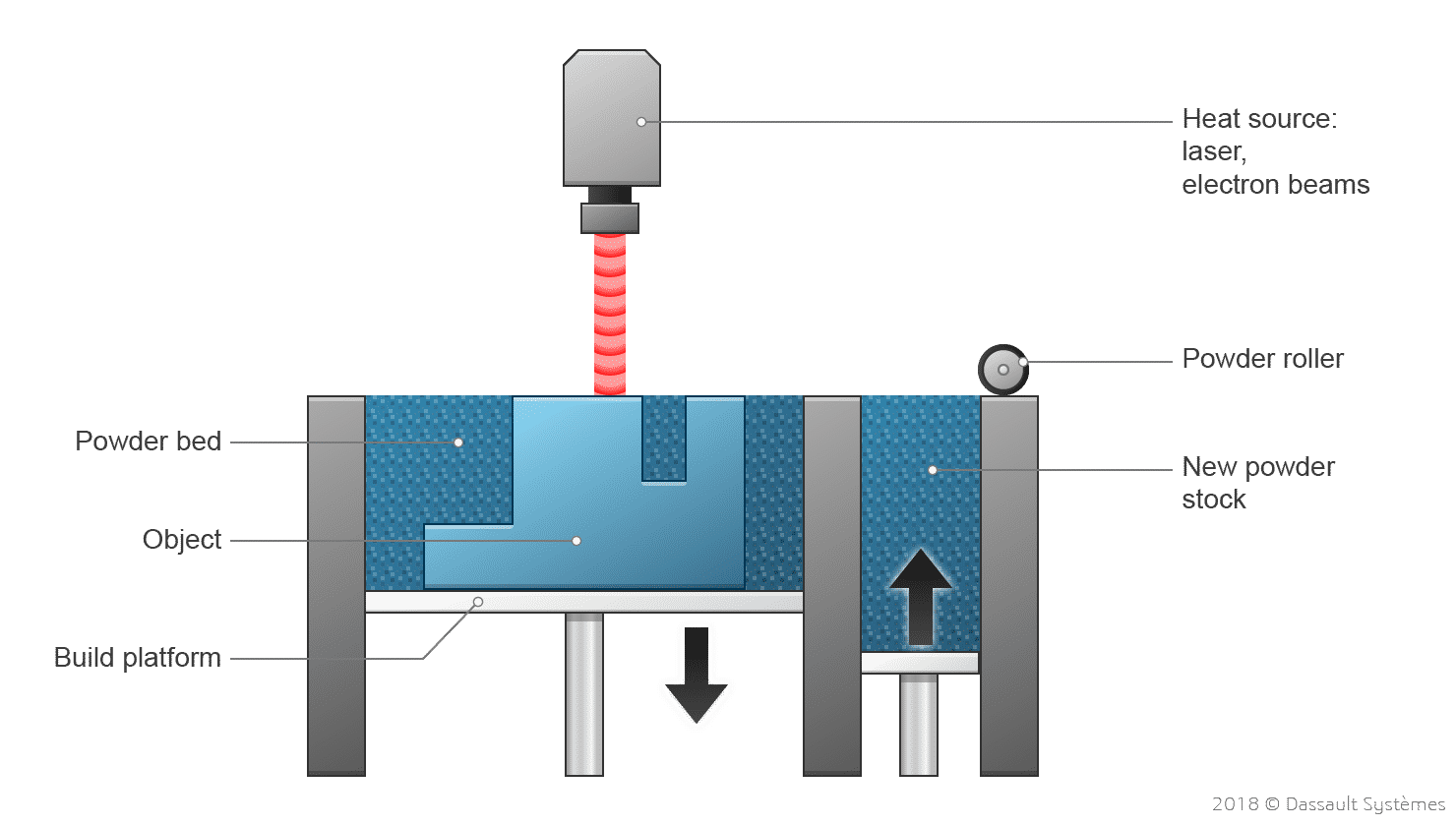
Discover how Powder Bed Fusion works with 3D Prod
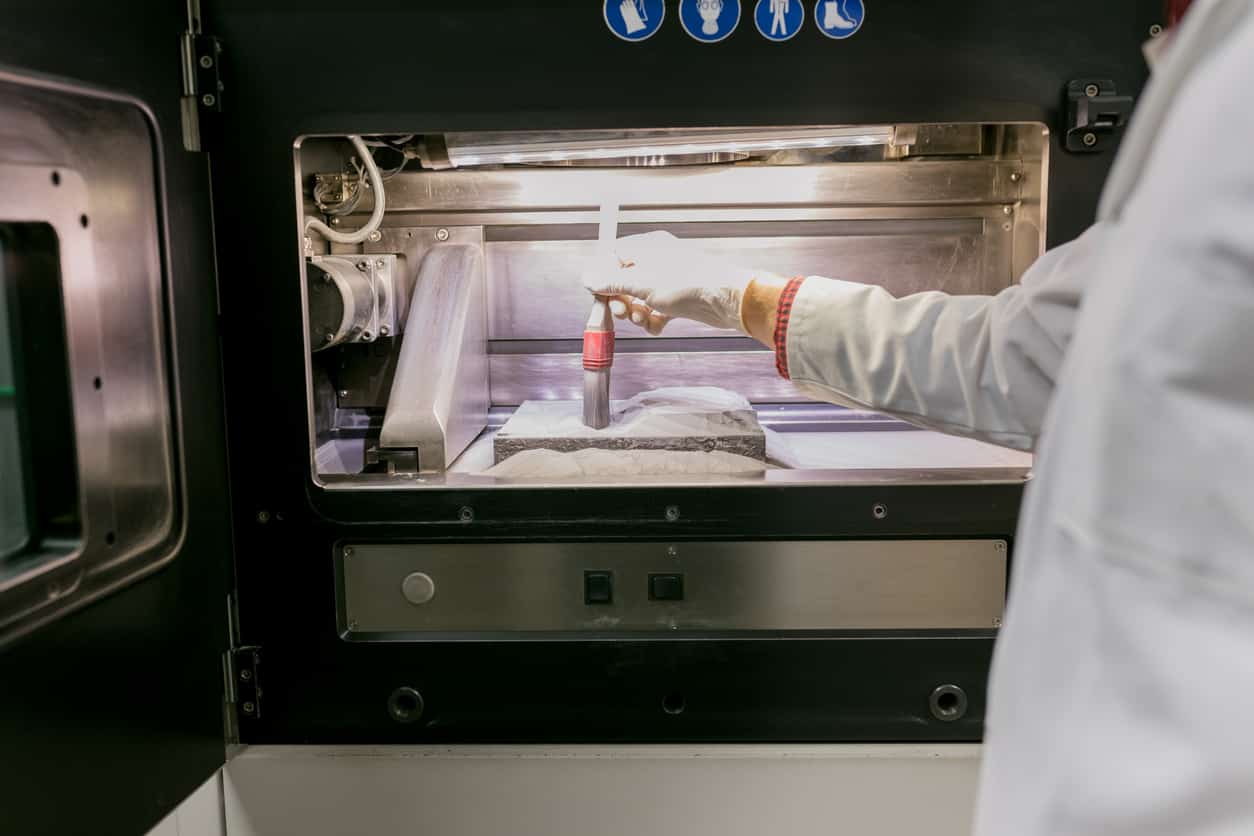
3DEXPERIENCE Make
Get multiple quotes for your parts in seconds