Plastic
Discover what is Plastic or polymere, a manufacturing material, and its usage in the industry.
Introduction to Plastic
Plastic is a material consisting of a wide range of synthetic or semi-synthetic organic compounds that are malleable and, therefore, can be molded into solid objects. Plasticity is the general property of all materials that involves permanent deformation without breaking. Polymers’ name is derived from their elastic and plastic properties.
Plastics are typically organic polymers of high molecular mass, but they often contain other substances. They are usually synthetic and most commonly derived from petrochemicals. However, today’s focus on the environment has led to a growing number of plastics derived from renewable materials such as polylactic acid from corn or cellulosics from cotton linters.
Plastics have been adopted in a significant and ever-expanding range of products thanks to their relatively low cost, ease of manufacture, versatility, and imperviousness to water. Plastics are everywhere in products as simple as paperclips or as complex as planes.
A significant source of diverse plastic material is available across a widespread manufacturing spectrum. One of the latest and exciting manufacturing domains is in 3D Printing. New applications for 3D Printing emerge almost daily, and a diverse array of plastic objects have already been produced using the 3D Printing process. The usages of these objects are mainly in prototyping labs, toys, mechanical gearboxes, medical prosthetics, and many more.
Material Engineers generally classify plastics by the chemical structure of the polymer’s backbone and side chains; some important groups in these classifications include:
- Acrylics
- Polyesters
- Silicones
- Polyurethanes
- Halogenated plastics
For clarity purposes, we focus in this documentation on a set of representative polymers, also known as commodity plastics, standard plastics, or engineering plastics.
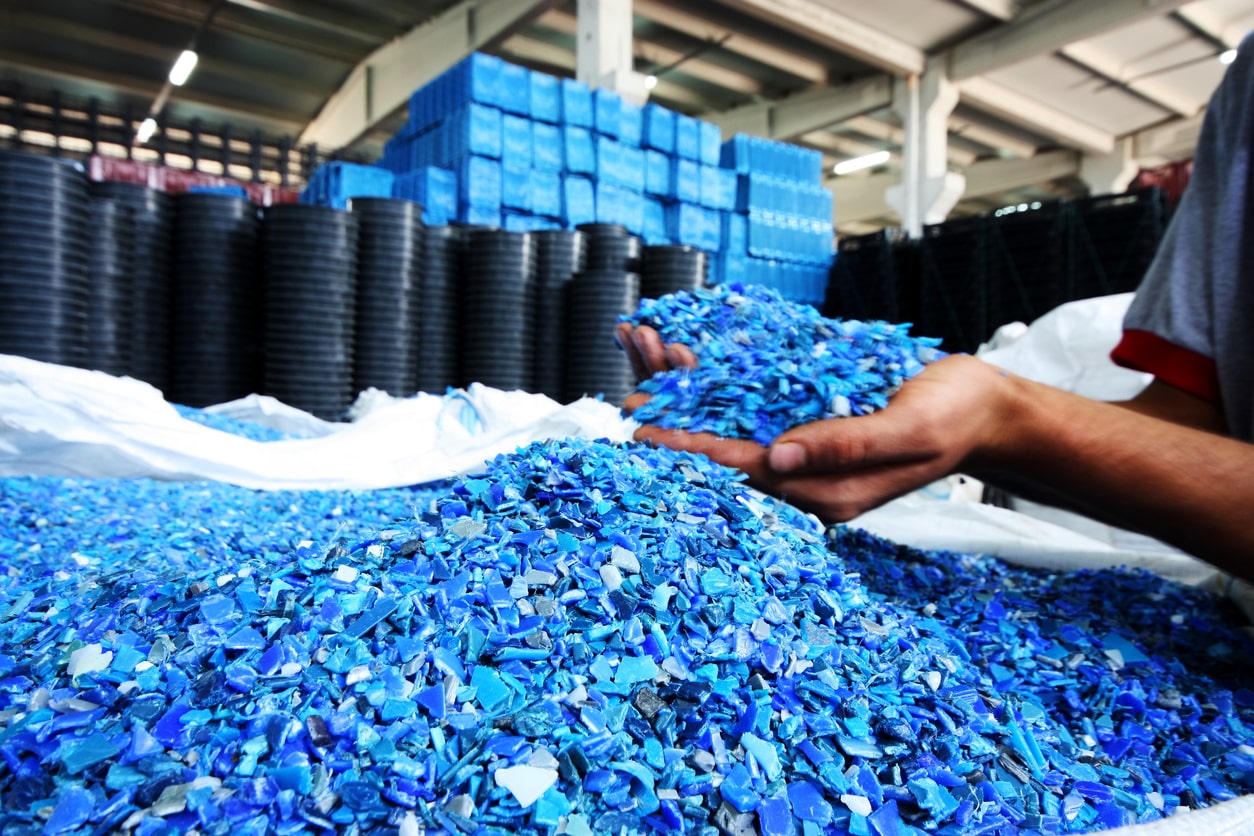
Discover 3DEXPERIENCE SOLIDWORKS for Makers
Generic plastic materials
- Acrylonitrile Butadiene Styrene (ABS) is a terpolymer produced by polymerizing styrene and acrylonitrile in the presence of polybutadiene. Most applications can withstand temperatures between -20–80 °C (-4–176 °F). Typical applications include electronic equipment cases such as computer monitors, printers, keyboards, and drainage pipes.
- Polyamide (PA) or nylon occurs naturally, for example, with wool and silk, synthetically as nylons, aramids, and sodium poly (aspartate). Industries such as fashion, automotive, carpet, or sportswear implement synthetic polyamides in the textile for their durable and strong properties. The transportation manufacturing industry is estimated to consume 35% of worldwide polyamide (PA) globally. Some key applications include fibers, toothbrush bristles, tubing, fishing line, and low-strength machine parts in engines or gun frames.
- Polycarbonates (PC) belong to the thermoplastic carbonate-containing polymer group. Their solid and rigid properties and the transparency of some grades make them suitable for engineering. Additionally, their elastic properties make them easy to work, mold, and thermoform. Many applications such as compact discs, eyeglasses, riot shields, security windows, traffic lights, and lenses use, therefore polycarbonates (PC).
- Polyester (PES) can occur naturally, such as in the cutin of plant cuticles, synthetically through step-growth polymerization such as polybutyrate. Natural polyesters and a few synthetic ones are biodegradable, but most synthetic polyesters are not. Polyesters can be found extensively in the clothing and textile industries.
- Polyethylene (PE) is the most common plastic, with an annual global production of approximately 80-million tons. The packaging sector mainly uses it to produce plastic bags, plastic films, geomembranes, and containers (including bottles).
- High-density polyethylene (HDPE), also known as polyethylene high-density (PEHD), is a thermoplastic derived from petroleum with a high strength-to-density ratio. The industry mainly uses it for detergent bottles, milk jugs, molded plastic cases, plastic bottles, corrosion-resistant piping, geomembranes, and plastic lumber. When used for pipes, it is sometimes called alkaline or polythene.
- Low-density polyethylene (LDPE) is a thermoplastic made from monomer ethylene. First produced in 1933 by Imperial Chemical Industries (ICI), its manufacture employs the same method today. Also, its implementation remains widespread in outdoor furniture, siding, floor tiles, shower curtains, and clamshell packaging despite competition from more modern polymers.
- Polyethylene terephthalate (PET), commonly abbreviated PET or PETE, is the polyester family’s most common thermoplastic polymer resin. Various industries utilize them in fibers to produce clothing, containers for liquids and foods, thermoforming for manufacturing, and with glass fiber for engineering resins. Brand names include Dacron, Terylene, or Lavsan.
- Polypropylene (PP), also known as polypropene, is a rugged and corrosion-resistant addition polymer that belongs to the thermoplastic polymer group. After polyethylene it is the second most widely produced synthetic plastic. A broad spectrum of applications could utilize it, such as packaging, labeling, textiles, stationery, plastic parts, reusable containers, laboratory equipment, loudspeakers, automotive components, and polymer banknotes.
- Polystyrene (PS) is a synthetic aromatic polymer made from monomer styrene and can be solid or foamed. General-purpose polystyrene is clear, hard, and relatively brittle, and inexpensive resin per unit weight. It is naturally transparent but can be colored. As one of the most widely used plastics, being produced in the millions of tons per year, industrial companies employed it for foam peanuts for packaging, food containers, plastic tableware, disposable cups, plates, cutlery, compact disc (CD), and cassette boxes.
- High-impact polystyrene (HIPS) is a graft copolymer produced by mixing polystyrene with the stretchier polybutadiene rubber during polymerization, which results in high-impact polystyrene (HIPS), often called “high-impact plastic” in advertisements. It is commonly injection molded to produce toys, refrigerator liners, food packaging, and vending cups. One brand name is Bextrene.
- Polyurethane (PUR and PU) is a polymer composed of organic units joined by carbamate (urethane) links. Although most polyurethanes are thermosetting polymers that do not melt when heated, thermoplastic polyurethanes are also available. Typical applications include cushioning foams, thermal insulation foams, surface coatings, and printing rollers. It is the most commonly used plastic in automobiles.
- Polyvinyl chloride (PVC) is also known as PVC, polyvinyl, or vinyl and is the world’s third most widely produced synthetic plastic polymer after polyethylene and polypropylene. PVC is available in either a rigid (RPVC) or flexible form. Typical applications for RPVC include plumbing pipes, gutters, doors, window frames, and bank or membership cards. Common applications for flexible PVC include shower curtains, flooring, imitation leather, signage, phonograph records, inflatable products, and various applications replacing rubber.
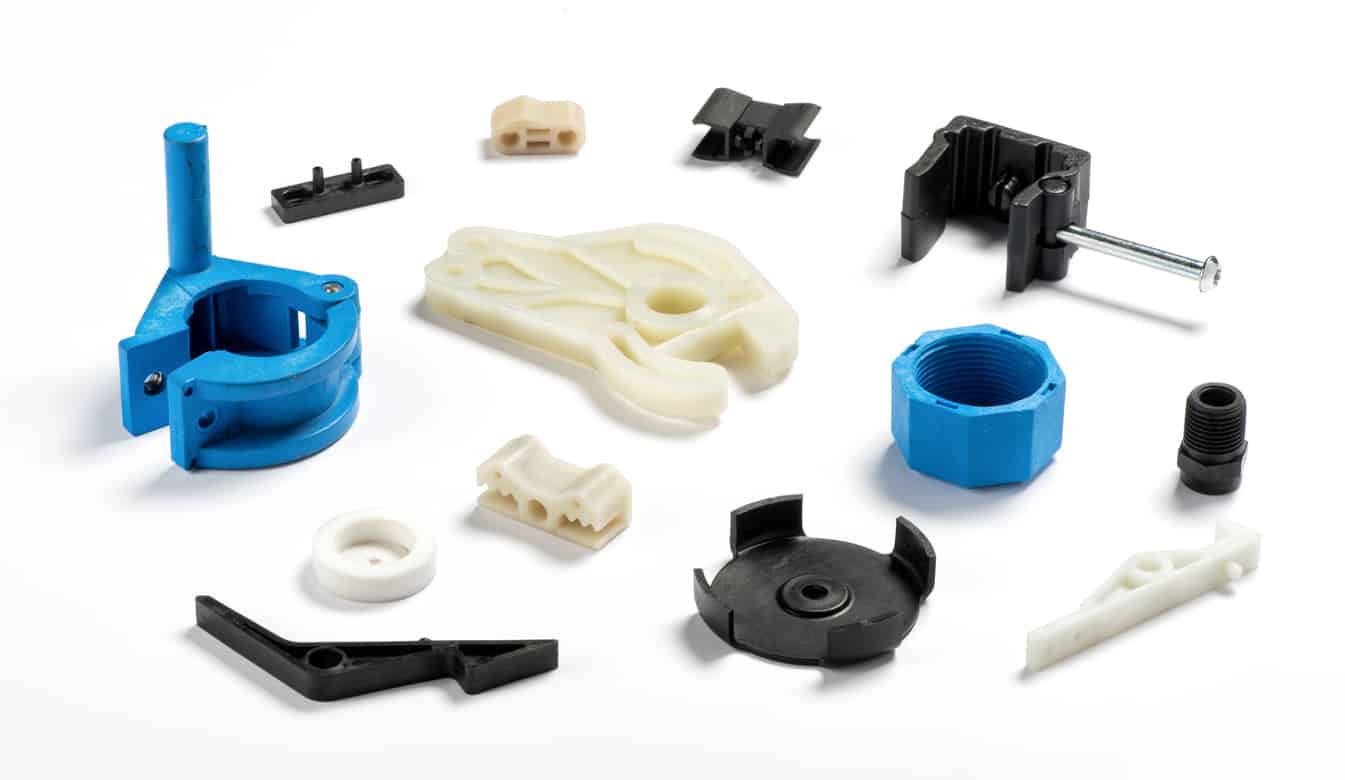
Plastic materials for 3D printing processes
Besides the generic thermoplastic materials, the 3D printing industry has adopted some plastics for their technical properties.
- Butadiene Styrene (ABS) is a thermoplastic and is the same flagship material that Legos. Automotive bodies and everyday household appliances also use it. ABS is particularly suitable for fully functional applications because its properties correspond to 80% of those used with injected production material. While ABS offers plenty of design freedom, printed details are considered moderate, although printing accuracy is high. The surface quality of ABS-printed objects is relatively rougher when compared with other materials. ABS is available in a natural finish in red, black, or white and is UV resistant.
- Simulated ABS delivers all the strength of ABS while also offering precision functional (injection) molds. Its key characteristics are strength, high-temperature resistance, fine details, and a beautiful, smooth surface finish. Simulated ABS also delivers high impact resistance and shock absorption. Tough and durable prototypes are prime candidates for simulated ABS, and it is the fastest and most affordable way to produce high-precision injection molds for small injection molding runs of 10–100 pieces.
- Nylon for the SLS (Selective Laser Sintering) manufacturing process employs laser sintering to deliver functional prototypes and end-use parts by melting extremely thin layers of powdered Nylon to shape and form a solid structure. Nylon makes it possible to produce complex designs that feature intricate details. It is mainly suitable for moving and assembled parts, cases, holders, or adapters. The drawback is that it can result in cavities within its design unless the designer makes use of escape holes.
Some 3D printers manufacturers tend to develop their own branding.
The different plastics for use in 3D Printing include prototyping plastic, rigid opaque plastic, rubber-like plastic, and transparent plastic. Each of those plastics has its own specific characteristics and applications.
- Prototyping plastic uses Fused Deposition Modeling (FDM) printers to produce prototypes. It is an ideal material for designers and engineers to cost-effectively produce and test a design and get products to market faster. Its key characteristics are rapid turnaround time, economically priced, and form and fit prototyping. Its limitations include a tolerance of +/- 1-mm, overhangs that require support and affect surface finish, visible print layers, and anisotropy (weak in the Z direction). Prototyping plastic is most suitable for fit or form checks but also for functional parts such as enclosures and custom piping.
- Rigid opaque plastic is the leading material for delivering realistic prototypes with distinctive details, high accuracy, and a smooth surface finish with up to 16-micron layer heights. Its key strengths include fine-detail models with smooth surfaces, suitable for form and fit testing, convenient for sales and marketing demonstration models, as well as its suitability for moving and assembled parts. Its one drawback is UV light sensitivity.
- Rubber-like plastic makes it possible to simulate rubber with various levels of elastomer characteristics, including Shore Scale a hardness, elongation at break, tear resistance, and tensile strength. The main technique used with rubber-like plastic is laser sintering. Finished products such as toothbrushes, non-slip or soft surfaces on consumer electronics, medical devices, and automotive interiors can be manufactured with rubber-like plastic. Fashion designers could use it for models that require shock absorption, gadgets, squeezable models, and functional models. One drawback is its UV light sensitivity.
- Transparent plastic is well suited for manufacturing translucent parts and prototypes with high precision. It is one of the most transparent 3D Printing materials on the market. Optimal for form and fit testing, transparent plastic offers a smooth surface finish ideal for fine-detail model construction of clear and tinted products such as eyewear, lighting covers, and medical devices. It is also particularly well suited for sales, marketing, and medical/scientific demonstration models. One drawback is its sensitivity to UV light.
- Polyamide for Selective Laser Sintering (SLA) 3D printing technique is a very fine, white, granular powder that employs laser sintering to produce complex, concept, and functional models as well as lamps and small series of models where there are several copies reproduced. Laser sintering of polyamide delivers the greatest design freedom compared with all other 3D Printing techniques. The final product results in a strong, relatively flexible object that can withstand minor impacts and resist some pressure under bending constraints. The natural surface is slightly porous with a sandy, granular appearance, and multiple finishing possibilities exist. Polyamide objects can be finished with a satin, polished, or velvet surface or dyed or spray-painted. A waterproof aqueous solution can also seal them.
- Polyamide (MJF) is a very fine, granular powder that employs HP Multi-Jet Fusion technology to produce complex, functional, or concept models, as well as a small series of models where several copies are reproduced. Manufacturing objects of polyamide (MJF) with the HP Multi-Jet Fusion technology offers the greatest design freedom compared with all other 3D Printing techniques. Ideal for more detailed surface resolution and thinner walls, this technique produces a higher density and lower porosity than its Selective Laser Sintering counterpart technique. The natural surface finish of polyamide (MJF) is fine, granular, and gray. There is a need for dyeing to achieve a uniform appearance.
Characteristics and applications of resin
The different resins for use in 3D Printing include High-detail Resin, Mammoth Resin, Transparent Resin, Gray Resin, and Standard Resin. Each of these resins has its own specific characteristics and applications.
- Usage of Photo-polymeric liquid: manufacture objects with High-detail Resin using PolyJet prototyping technology, stereolithography (SLA), and Digital Light Processing (DLP) technologies. High-detail Resin is particularly well suited for small and/or intricately detailed visual models. Models produced with High-detail Resin feature smooth surfaces, although their functional use is relatively limited. Users experience limited design freedom due to the need to remove their support material. The finishing process involves curing with UV light immediately following jetting. However, the model must avoid direct sunlight to prevent discoloration. It is possible to increase the UV resistance and improve appearance with paint or varnish.
- Usage of Mammoth Resin: produce high-quality show models and master molds, thanks to its excellent surface quality and potential for high-quality finishing by performing extra finishing steps. Stereolithography is the technique used to manufacture objects with Mammoth Resin. This technique requires a support structure during printing, therefore limiting design freedom. Finishing is available in either its natural state or can be spray-painted. Some layers remain visible in the natural, basic finish, and the object is sensitive to UV light.
- Usage of Transparent Resin: fabricate models that require a transparent or neat, smooth surface appearance, such as demo models of limited functionality. A hardened liquid is used to manufacture models with Transparent Resin; it is strong, hard, stiff, naturally water-resistant, and transparent. Stereolithography is the technique used to produce Transparent Resin objects, limiting design freedom because of the need for a support structure during printing. Well suited for demo models, accurate models, and limited-functionality models, its transparency is not 100% water clear but lies between translucent and water clear. Solid models with a thickness greater than 2 cm (0.8 inches) will feature a bluish luster. Natural finish also called a technical finish, involves curing the object under UV light followed by a coat of transparent paint to reduce UV light discoloration. It is also possible to add a small amount of color to the paint.
- Usage of Gray Resin: manufacture high-quality show models and visual prototypes using the stereolithography technique. The result is a gray color with a near-luxurious surface finish. Gray resin is particularly well suited for character and toy models but is also suitable for A-side visual models with limited functionality. It produces one of the smoothest surfaces of all other 3D printing materials. It also features a medium mechanical resistance and is sensitive to UV light discoloration. Design freedom is limited because of the requirement for a support structure during printing. The finishing surface of the B-side of Gray Resin is matte and visibly reveals small dots from 3D printing support structures.
- Usage of Standard Resin: manufacture high-quality show models and visual prototypes using stereolithography. The result is a translucent object with a tint of yellow color. Standard Resin is particularly well suited for character and toy models but is also suitable for A-side visual models with limited functionality. These models are particularly attractive when painted. Standard Resin produces one of the smoothest surfaces of all other 3D printing materials. Design freedom is limited because of the requirement for a support structure during printing. The finishing surface of the B-side of Standard Resin is matte and UV sensitive and visibly reveals small dots from 3D printing support structures.
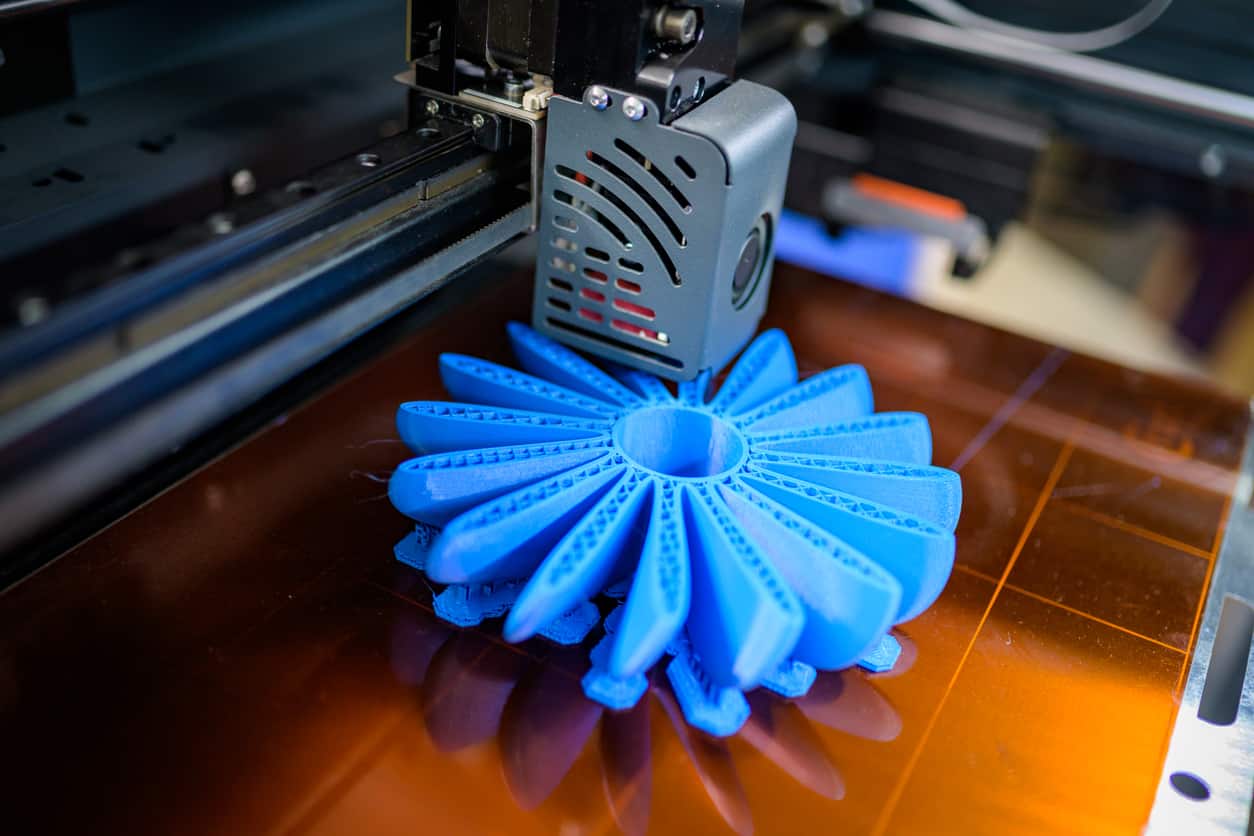
Get multiple quotes for your parts in seconds