CNC Machining in the aerospace sector
CNC machining has become indispensable to aerospace manufacturing, offering unparalleled precision, reliability and versatility.
What is CNC Machining?
Computer Numerical Control (CNC) machining is a precision production technique that uses computer-controlled machines to accurately cut, shape and form parts. It can create complex geometries from materials such as metal (aluminum, steel, titanium), plastic or wood.
The term ‘CNC machining’ covers several processes, including cutting, milling, turning, drilling, grinding, routing and polishing. By following pre-programmed instructions, CNC machines ensure high levels of consistency, accuracy and reliability.
CNC machining is also very cost-efficient as waste material, defects, manual work and setup times are all minimized. This makes it suitable for both large and low-volume production and for creating one-off custom pieces. Modern CNC machines are equipped with multi-axis capabilities, automated tool changers and advanced automation, further optimizing production efficiency.
The versatility of CNC machining has seen it adopted in every manufacturing sector, including automotive, aerospace, electronics, medical and more. Additionally, the advent of desktop-sized CNC machines has made the technology accessible to hobbyists, makers and DIY enthusiasts. These miniaturized machines are usually more user-friendly and tailored for smaller-scale projects.
To learn more, visit our 3DEXPERIENCE GUIDE TO CNC MACHINING
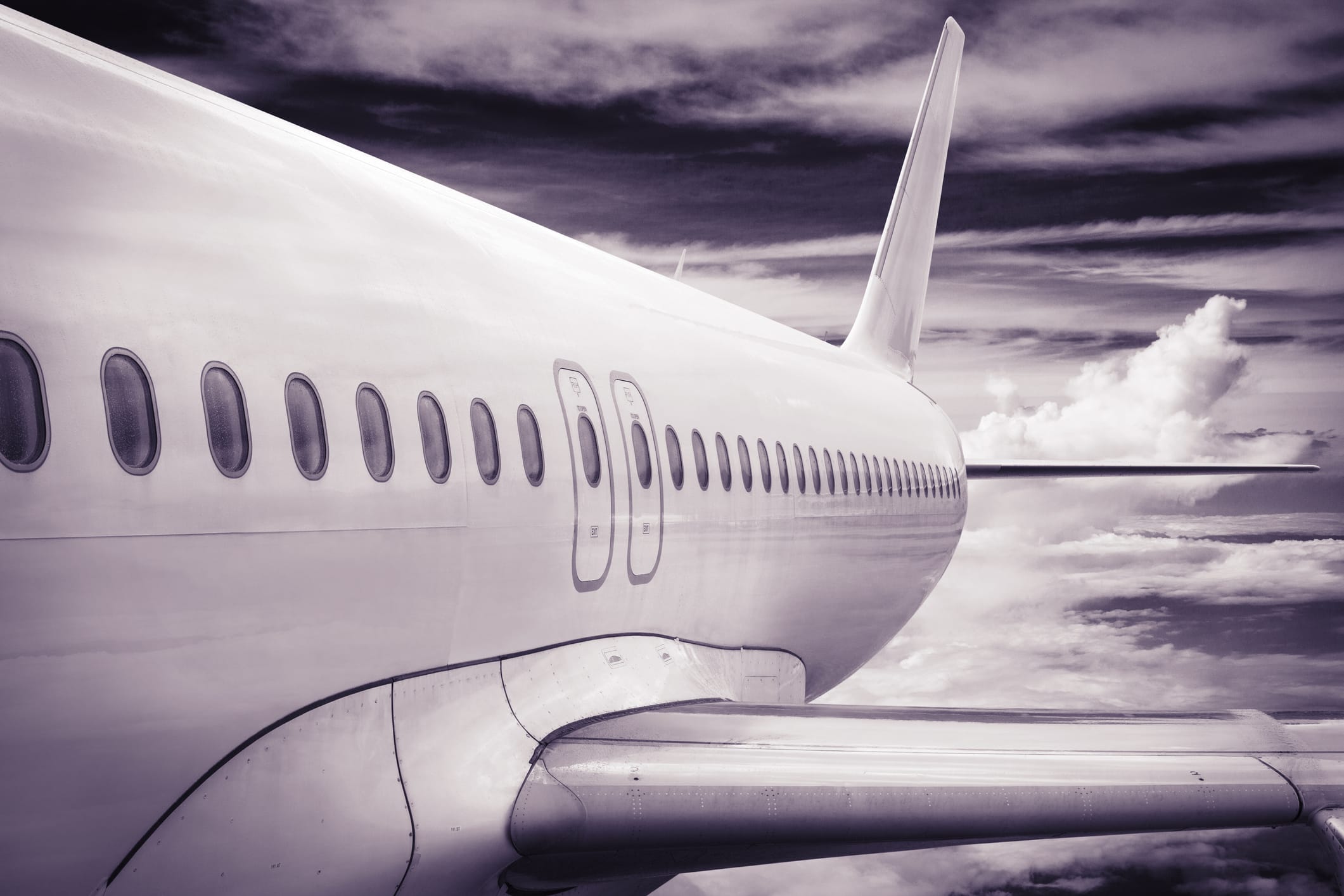
How CNC machining transformed the aerospace sector?
Aerospace manufacturing is soaring to new heights of innovation and efficiency, and CNC machining lies at the heart of this transformation. This cutting-edge technology has redefined the design, manufacture and performance of aerospace parts by combining precision and consistency with speed and versatility.
CNC machining brings many advantages to the aerospace sector, including:
-
PRECISION AND ACCURACY
The aerospace manufacturing sector demands the highest standards of precision and reliability. Components must meet strict tolerances and adhere to rigorous quality and safety standards. CNC machining delivers unrivaled precision and accuracy, ensuring that aerospace parts meet exact specifications. This is especially important for critical aerospace systems, such as turbine engines, landing gear and structural elements, where even a slight deviation can significantly impact performance, safety and durability.
-
EFFICIENCY AND PRODUCTIVITY
The automation and programmability of CNC machining have significantly boosted productivity in aerospace manufacturing. Once programmed, CNC machines can operate continuously with minimal human intervention between operations. Multi-axis CNC machines can perform multiple operations on different part surfaces at the same time.
CNC machines can be pre-programmed and re-programmed quickly and easily. This enables different parts to be made on the same machine during a single shift. These capabilities help reduce production cycles and downtime and increase overall output.
-
COMPLEX PART MANUFACTURE
Aerospace components often involve elaborate designs and complex geometries that balance strength and weight. CNC machining is well suited to this task as it can precisely produce high-value, highly complex parts with ease. With multi-axis capabilities, CNC machines can move cutting tools in multiple directions to carve out detailed components such as turbine blades, airfoils and engine casings. This has encouraged aerospace designers to push the boundaries of aerodynamics, weight reduction and fuel efficiency.
-
DESIGN FLEXIBILITY
The aerospace sector thrives on continuous improvement, especially in relation to lightweighting and safety. The combination of Computer-Aided Design (CAD) software and CNC machining enables aerospace engineers to design, refine and create parts with ease. This allows parts to be rapidly optimized, prototyped, brought to market and adapted to changing needs and design improvements.
-
CONSTANT INNOVATION
CNC machining plays a pivotal role in fueling innovation in aerospace manufacturing. CNC machining enables design engineers to unleash their full creative potential. Its ability to transform intricate designs into reality has paved the way for advancements in aircraft performance, weight reduction, structural integrity and safety. From advanced alloys and composites to new propulsion systems and flying taxis, CNC machining helps bring cutting-bring cutting-edge materials and novel concepts to life.
-
COST SAVINGS
While industrial CNC machines carry a hefty price tag, they offer significant cost-saving opportunities in the long run. By removing the need for dedicated jigs, fixtures and specialized tooling for each part, CNC machining helps minimize setup times, streamline production and reduce manufacturing costs.
The technology also reduces waste and cost through material optimization. This is particularly crucial in aerospace as parts are often made using high-value materials like precious metals. The improved efficiency and productivity CNC machining provides also contribute to cost savings over time.
Applications of CNC machining in the aerospace sector
CNC machining is used to produce numerous aerospace parts and components. Just some of them include:
-
ENGINE COMPONENTS
CNC machining is used extensively in the production of critical engine parts for aerospace, such as turbine and compressor blades, fan discs, fuel nozzles, engine casings and combustion chambers. CNC machining allows for complex geometries, intricate cooling channels and high-temperature materials necessary for efficient and reliable engine performance.
-
STRUCTURAL COMPONENTS
CNC machining plays a crucial role in manufacturing structural parts like aircraft frames, wing spars, bulkheads, brackets and landing gear components. These components demand exceptional precision and strength, high-quality surface finishes and proper alignment to withstand the extreme stresses of flight.
Composite structures are increasingly being used in aircraft structures to reduce weight and improve fuel efficiency. CNC machines equipped with specialized cutting tools and processes can shape, trim and finish components made from composites like carbon fiber and glass-reinforced epoxy.
-
AVIONICS AND ELECTRICAL COMPONENTS
CNC machining is commonly used to manufacture various electronics components used in aircraft systems such as control panels, connectors, sensor housing and instrument cluster components. These parts demand precise machining to ensure proper functionality, electrical connectivity and component integration.
The technology is also used to produce enclosures for avionics systems – the electronic, instrumentation and navigation systems used in aircraft. These systems are crucial for accurate data collection, control and communication in aircraft systems. Avionics enclosures require precise cutouts, holes and mounts to accommodate various components and ensure electromagnetic shielding.
-
INTERIOR AND EXTERIOR TRIM
CNC machining is employed to manufacture interior and exterior trim parts, including cabin panels, seating structures, winglets, fairings, airframe assemblies, emblems and decorative accents. CNC machining enables the creation of intricate designs, precise cutouts, and fine details that enhance the aesthetics and functionality of a vehicle's interior and exterior, while also being lightweight.
-
PROTOTYPING
Prototyping allows engineers and designers to create functional models of aerospace parts and assemblies, enabling them to evaluate the design, fit and functionality before proceeding to full-scale production. CNC machining enables the rapid production of intricate and precise prototypes that closely resemble the final components.
-
MAINTENANCE, REPAIR AND OVERHAUL (MRO)
CNC machining is used extensively in the MRO sector of the aerospace industry. It is employed for the repair and refurbishment of numerous components, such as engine parts, landing gear components, and structural elements. CNC machines allow for accurate re-machining and re-conditioning of worn or damaged parts, ensuring their continued safe and reliable operation.
Limitations of CNC machining in the aerospace sector
While CNC machining is a highly versatile and widely used manufacturing process in the aerospace sector, it does have certain limitations. Although many of these can be overcome through process optimization, tooling advancements and a thorough understanding of the design requirements.
-
COMPLEXITY OF SHAPES
CNC machining is well-suited for producing parts with relatively simple to moderately complex geometries. However, when it comes to extremely intricate or highly contoured shapes, CNC machining may have limitations. For example, there may be constraints related to undercuts, deep cavities or internal features that are difficult to access with standard cutting tools. Complex or highly intricate parts may require specialized tooling or additional operations, adding time and cost to the manufacturing process.
-
MATERIAL RESTRICTIONS
CNC machining can work with many materials commonly used in aerospace, such as aluminum, titanium and composites. However, certain materials may pose a challenge. For example, some advanced high-temperature alloys or superalloys used in aerospace engine components can be difficult to machine due to their hardness or heat resistance. Specialized tooling and techniques may be required to effectively machine such materials.
- SIZE LIMITATIONS
Industrial CNC machines come in various sizes. The size of the machine defines the maximum size of parts it can accommodate. Large-scale components, such as aircraft wings or fuselage sections, may exceed the capacity of standard CNC machines. Alternative manufacturing methods could be a better option to fabricate these oversized components.
-
COST CONSIDERATIONS
CNC machining can be a cost and time-effective method for making aerospace components, especially for medium to high-volume production runs. However, for low-volume or one-off parts, the setup and programming costs associated with CNC machining may make it less viable compared to additive manufacturing (3D printing), for example. Additionally, CNC machining can be a time-consuming process, especially for complex parts, due to the need for multiple machining operations and setup times.
-
SURFACE FINISHES
While CNC machining can achieve high precision and accuracy, the surface finish of machined parts may require additional post-processing. Aerospace components often have strict surface finish specifications, such as low roughness, absence of burrs or specific coatings. Achieving these requirements may involve secondary processes, such as grinding, polishing or coating, which add time, cost, and complexity to the manufacturing process.
-
OPERATOR SKILL AND TRAINING
CNC machining requires skilled operators to program, operate and maintain the machines effectively. The complexity of CNC programming and operation requires proper training and expertise. Finding and retaining skilled CNC operators can be a challenge, particularly where there is a shortage of qualified personnel.
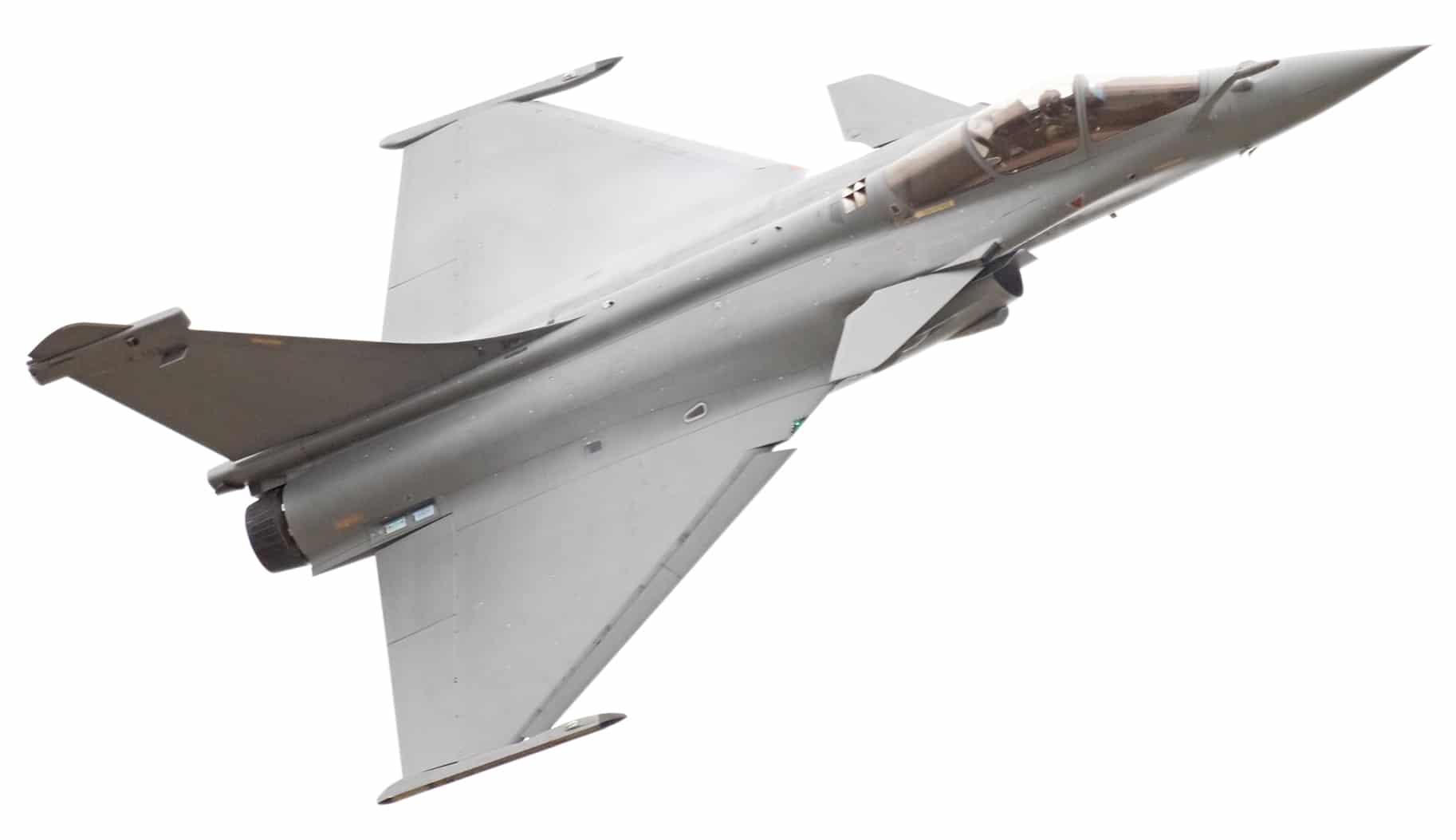
The future of CNC machining in the aerospace sector
The aerospace sector is being radically reshaped by factors such as technological advances, changing market demands and environmental considerations. Electric and hybrid propulsion systems, lightweight materials, autonomous flight and enhanced safety and comfort features mean the aircraft of the future will be very different to that of the past. Nevertheless, CNC machining will continue to be a vital technology in the aerospace sector, driving innovation, efficiency and precision in the production of components and aircraft.
-
ENHANCED AUTOMATION AND DIGITALIZATION
Automation is playing an ever-more vital role in CNC machining in the aerospace sector. The use of robotics, artificial intelligence (AI) and machine learning (ML) algorithms enable real-time data monitoring, predictive maintenance and adaptive machining processes. This will further enhance efficiency, productivity and quality control in the aerospace manufacturing process.
Increasingly, CNC machining is being integrated into connected manufacturing ecosystems, enabling seamless digital communication between machines, production planning systems, supply chains and quality control. This connectivity will facilitate real-time decision-making, optimize production workflows and enable continuous improvements in aerospace manufacturing.
-
CAPABLE OF GREATER COMPLEXITY
Aerospace applications often require complex and highly specialized components with challenging geometries. CNC machining will continue to evolve to meet the demand for these challenging parts. Advancements in multi-axis machining, simultaneous milling and adaptive machining techniques will enable the production of increasingly more complex components with tight tolerances and superior surface finishes.
-
ADVANCED MATERIALS
The aerospace industry is increasingly utilizing advanced materials and composites to enhance performance, reduce weight and improve fuel efficiency. CNC machining will play a crucial role in machining these materials, such as carbon fiber composites, titanium alloys, and other lightweight alloys. CNC machines will need to adapt to the specific characteristics of these materials, ensuring precise and efficient machining processes.
-
CUTTING-EDGE TOOLING
CNC machining is evolving with the introduction of advanced tooling and cutting technologies. Improved tool coatings, geometries and materials will all help enhance cutting speeds, tool life and surface finish quality. High-speed, multi-axis and adaptive machining techniques are also becoming more prevalent, enabling faster production and greater precision in complex aerospace parts.
-
INTEGRATION WITH 3D PRINTING
The integration of CNC machining with additive manufacturing processes, such as 3D printing, will unlock new possibilities in aerospace manufacturing. CNC machining can be employed for post-processing, surface finishing and adding final details to 3D-printed parts. This integration will enable the production of hybrid parts that combine the design freedom of 3D printing with the precision and quality of CNC machining.
-
SUSTAINABLE MANUFACTURING
With environmental concerns growing, the aerospace industry is increasingly focused on sustainability. CNC machining plays a crucial role in enabling sustainable manufacturing practices by optimizing material usage, reducing waste and implementing energy-efficient production strategies. Advanced machining techniques, such as near-net shape machining and optimized toolpath generation, will further contribute to minimizing material waste and energy consumption in aerospace manufacturing.
Get multiple quotes for your parts in seconds