Aerospace Manufacturing Methods for Prototyping and Production
Aerospace Manufacturing Methods for Prototyping and Production, Pre-Production Prototyping, Production, Material, and Quality for Aerospace Products. Learn more now!
Introduction: Aerospace Manufacturing Methods for Prototyping and Production
The aerospace industry has long been at the forefront of manufacturing innovation as companies have continually pursued cost-reduction methods, improved efficiencies, increased equipment utilization, enhanced profitability, and meeting and exceeding expectations. Advanced manufacturing practices have helped advance the ability to develop prototypes and production parts.
This article discusses Aerospace Manufacturing Methods for Prototyping and Production, the pre-production and prototyping process, methods, production, materials, and quality.
Aerospace Ascending
In 2022, the aerospace industry has been boosted by increased aircraft and military orders and the additional demand for air travel. While fuel prices impact air travel and overall costs, The growth of new technologies is improving efficiencies as the industry pursues more fuel-efficient, lower-emission product designs.
Based on surveys of aerospace business managers, the general business outlook for aerospace next year ranges from "somewhat to very positive." Agility is needed to stave off potential market instability, and technological growth has been at the forefront of the trends expected to lead the industry in the coming years. In addition to the need for adding more talent to the workforce, the aerospace industry trends include many cutting-edge programs that are defined below:
- 3D Printing – A component of additive manufacturing, 3D printing is building parts by joining material layer by layer from a 3D design such as a CAD file.
- Additive Manufacturing (AM) – The AM process creates an object by adding material. The opposite is called "subtractive manufacturing," where the material is removed by cutting and other methods. This differentiates from 3D printing, which adds material by layer.
- Artificial Intelligence (AI) –AI includes systems or machines that mimic human intelligence to perform tasks and can iteratively improve themselves based on the information they collect.
- Cloud Computing – Cloud computing uses a network of remote servers hosted on the internet to store, manage, and process data rather than a local server or a personal computer.
- Composite Manufacturing – Composites consist of two or more distinct materials, improving product performance and lowering production costs. These materials are developed for superior performance in specific certain applications.
- Distributed Manufacturing (DM) – DM is a form of decentralized manufacturing using a network of localized manufacturers. These manufacturers offer contracted services based on their manufacturing expertise. These services are coordinated using advanced information technology and cloud platforms.
- Digital Thread - A digital thread is a data-driven architecture that links information generated from a product lifecycle. It is envisioned as the primary or authoritative data and communication platform for a company's products at any given time.
- Industry 4.0 – Industry 4.0 is the next step in how companies manufacture, improve and distribute their products. Manufacturers are integrating new technologies, including the Internet of Things (IoT), cloud computing and analytics, and AI and machine learning, into their production facilities and operations.
- Internet of Things (IoT) – The Internet of Things (IoT) is the network of physical objects, "things," that have sensors, software, and other technologies to connect and exchange data with other devices and systems over the internet.
- Smart Factory - The smart factory is an interconnected network of machines, communication mechanisms, and computing power that comprises a cyber-physical system. This system uses advanced technologies such as artificial intelligence (AI) and machine learning to analyze data, drive automated processes, and learn to improve continuously.
- Machine Learning - Machine learning is the use and development of computer systems that can learn and adapt without following explicit instructions, using algorithms and statistical models to analyze and draw inferences from patterns in data.
- Supply Chain - The activities involved in providing a product through all stages, from raw material to finished goods.
- Sustainability – Sustainability consists of fulfilling the needs of current generations without compromising the needs of future generations while ensuring a balance between economic growth, environmental care, and social well-being.
Digital technologies and cutting-edge manufacturing methods have provided an advantage for aerospace manufacturing. Aerospace companies' reliance on these technologies will increase as they continue to streamline product design and development. Sourcing should continue transitioning towards regional suppliers and distributed manufacturing services to save time and money and improve quality. The industry is also pursuing new propulsion technologies, including hydrogen and hybrid models. Renewable energy is also an ongoing trend in the aerospace industry.
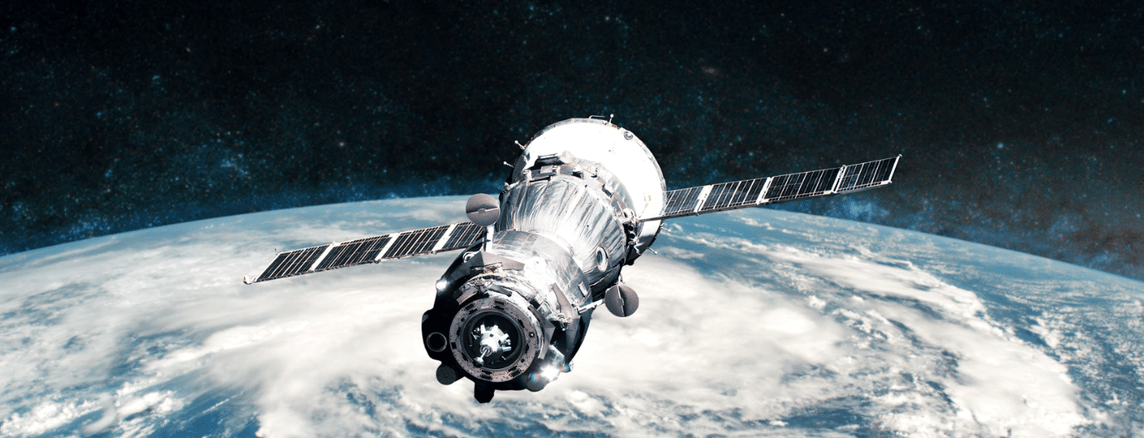
Additive Manufacturing Takes Off
Additive manufacturing technologies have been instrumental in these industry trends and continue their rapid growth with newly engineered materials. The three key technologies are 3D printing, composite manufacturing, and other additive manufacturing (AM) technologies.
These include; powder bed fusion, material and binder jetting, vat polymerization, direct energy deposition, and material extrusion.
These technologies have taken off due to the fragility of the global supply chain and the ability of additive manufacturing technologies. These issues have been critical when companies require more agile ways of developing, sourcing, and building products.
From 2010 to 2020, the additive manufacturing market doubled, projected to gain over 20% annually from 2022 to 2028. The industry is expected to continue to develop new composite materials and to integrate and develop advanced manufacturing technologies. The aerospace industry continues to pursue both dimensionally larger and smaller products, the attainment of volume production, and the manufacture of complex products that were once an assembly of many parts.
Pre-Production and Prototyping: Designing, Testing, Development
Additive technologies allow rapid prototyping to expedite the evaluation and testing of new products and materials. Products are quickly designed and evaluated for performance characteristics when combined with simulation software. This powerful software optimizes complex product designs in hours instead of weeks.
Simulation software evaluates the material performance in the office. Materials that fail can be easily replaced with superior materials. The product design is quickly improved for lighter, more robust designs with outstanding performance characteristics.
These complex simulations can predict the product microstructure, part defects, and performance characteristics and guide the designer through process optimization. By avoiding this wasted time, scrap production is avoided, equipment may be best utilized, and the time to market is expedited.
On-Demand, Low-Volume Production
The aerospace industry doesn't require high-volume manufacturing like commodity producers.
With on-demand production, inventories are reduced, as are storage and warehousing costs. The savings can add up quickly with expensive aerospace components. On-demand production is ideal for additive technologies, which often require part and weight reduction and rapid prototyping.
When considering the use of expensive materials in aerospace applications, additive manufacturing has a significant advantage over subtractive manufacturing technologies, where a large portion of the material machined is waste. The aerospace industry highly values component weight reduction. This translates to either less fuel or added range for the craft. Additive manufacturing can take several components and develop a single item while reducing weight and maintaining overall strength and performance.
Recently, hybrid manufacturing models have been developed for aerospace and other industries. The hybrid model combines subtractive manufacturing equipment with additive equipment. This may include post-processing finishing, drilling extremely accurate holes, or other subtractive manufacturing processes.
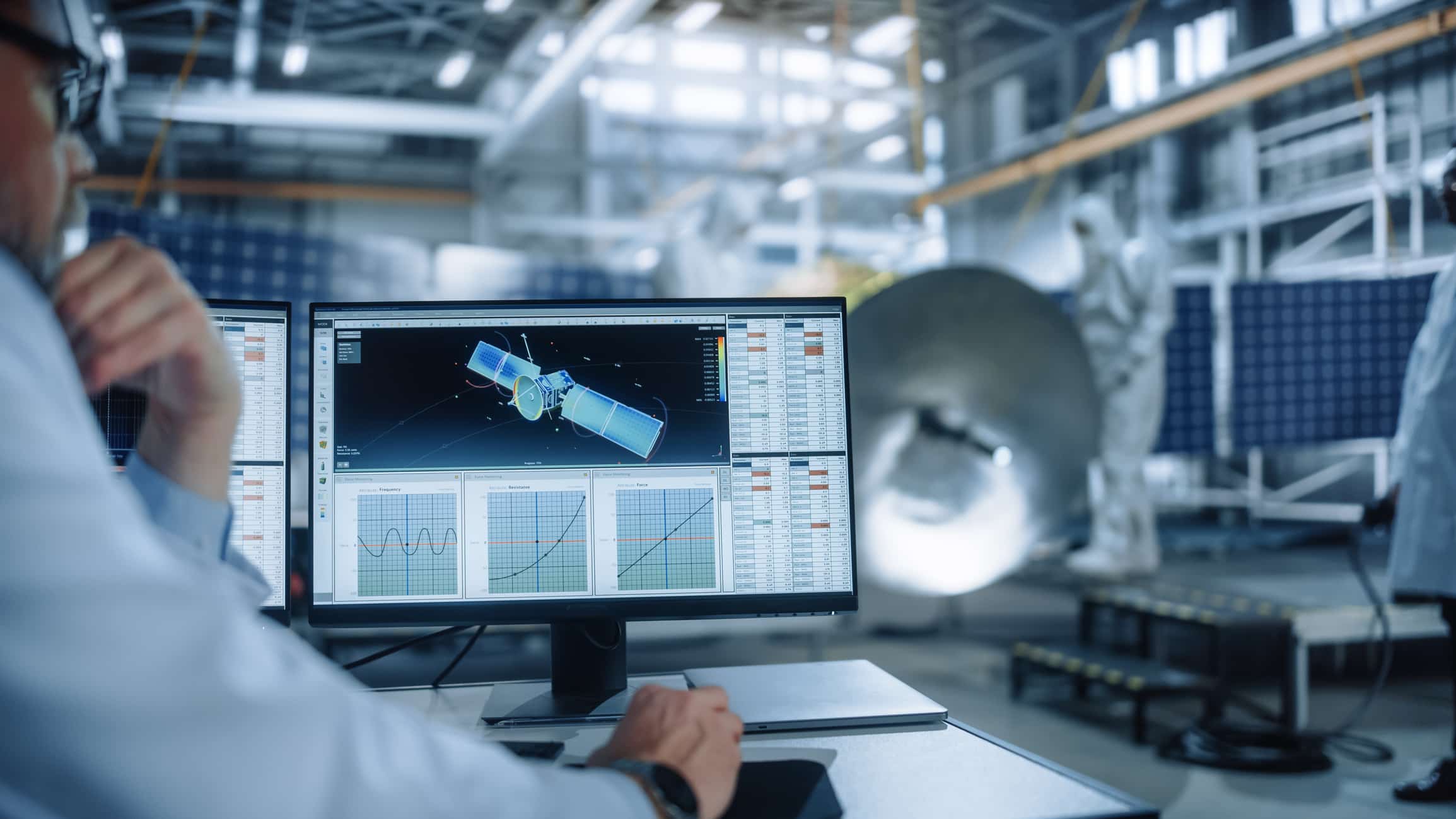
Materials Matter for Aerospace Parts
The development of metal additive technologies has been a significant factor in the growth of the overall additive manufacturing sector. Additive processes such as directed metal laser sintering (DMLS), laser powder bed fusion (L-PBF), electron beam powder bed fusion (EB-PBF), and directed energy deposition (DED) create parts with metals. The process manufacture parts from aluminum alloys, copper alloys, iron superalloys, nickel alloys, precious metals, refractory metals, titanium alloys, and more.
Other materials for unique non-metal applications include boron, carbon fiber, and liquid silicone rubber. New materials include meta-materials, a new class of performance-specific materials with properties not found in naturally occurring materials. Aircraft exhausts may use metamaterials for exhaust systems to reduce noise.
Inspections, Quality Controls, and Certifications
Since aerospace products are utilized in demanding and hazardous environments, the products must exceed the performance requirements of standard products. Finished products are evaluated for testing to ensure quality compliance and certification. This often includes coordinate measuring machines (CMMs), computed tomography, x-ray analysis, performance testing, and destructive testing methods. Lot traceability and comprehensive records are required in the event of product failure. Material certifications and product testing data are required for most products.
Industry certifications help companies identify manufacturers that meet the rigorous quality standards of the aerospace industry. The most important certifications for aerospace and defense companies include AS9100D, C, and B, ISO-9001:2015, AS-5553, and ITAR. AS9100 D is the ISO-9001 version of quality requirements for aerospace and was developed by the Society of Automotive Engineers (SAE) and the European Association of Aerospace Industries (EAAI). AS9100 D is the standard for aerospace quality.
AS9100 refers to aircraft maintenance and repairs. AS9100 B covers the storage and distribution of aircraft parts. AS -5553 is the Aerospace standard for the prevention and use of counterfeit parts. ITAR (International Traffic in Arms Regulations)is specific to the Defense industry and regulates exports overseen by the United States Department of State (DOS). Manufacturing any items intended for defense-related or military end-use applications requires ITAR compliance. These certifications are needed to operate in the aerospace industry.
Additive manufacturing parts also require certifications by different agencies such as the Federal Aviation Administration (FAA), European Space Agency (ESA), Directorate General of Civil Aviation (DGCA), The Center for Military Airworthiness & Certification (CEMILAC), etc. These agencies check the factors impacting product quality and process control. These agencies look for data regarding the material strength properties, testing, performance, process control, and lot traceability.
Get multiple quotes for your parts in seconds