3D printing in sports
3D printing in sports is rapidly growing due to its ability to deliver lighter, more durable and customized equipment that helps improve athletic performance.
What is 3D printing?
3D printing, or additive manufacturing, is a production technique that creates a three-dimensional object from a computer-aided design (CAD) file. The term covers several different processes that see one or more materials – typically plastic, metal, wax or composite – being deposited layer by layer to build a shape.
The entire process is controlled by a computer which makes 3D printing a cost-effective, efficient and accurate method to create objects of almost any geometry or complexity. Today, 3D printing is used in every industry to produce prototypes, tools and jigs, components and end-use parts.
3D printers come in various sizes, from small enough to fit on a benchtop to large-format industrial machines.
Large printers can produce bigger objects, but the machines take up more space and cost significantly more than benchtop printers. Achieving a successful print is also more complex on a large-format printer due to the volume of material and printing time involved.
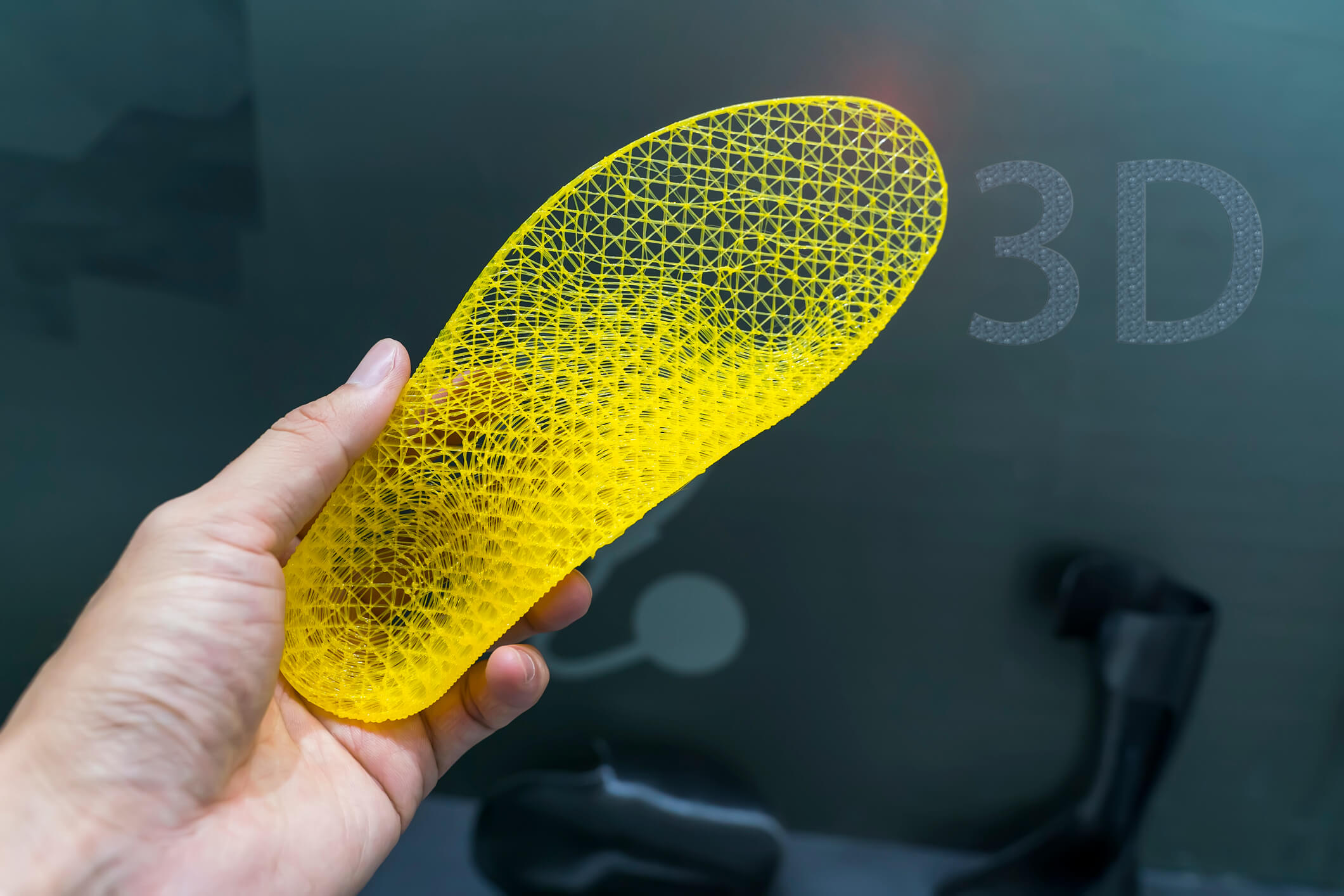
Discover 3DEXPERIENCE SOLIDWORKS for Makers
How is 3D printing transforming the sports industry?
3D printing in sports and fitness provides many advantages, including:
- Accelerated product design and development
- Greater design flexibility
- Faster product modification and improvement
- Lighter and stronger equipment
- Improved aerodynamics
- Enhanced customization options
In the world of sports, fractions of a second make the difference between winning or losing. Any time gained in an athlete’s reaction speed or how fast an injury heals can offer a unique competitive advantage.
Weight is equally important to athletes performing at their very best. Weight greatly influences the speed, endurance and power of an athlete and the equipment, vehicle or animal they rely on. Reducing weight can help an athlete perform better, recover quicker and compete at a higher level.
3D printing in sports is a key that unlocks previously unachievable time and weight savings. It does so by enabling the design and manufacture of lighter products that are as strong if not stronger than those made using more conventional manufacturing methods.
Additionally, 3D printing in sports offers much greater design freedom. The technology can produce highly complex geometries that would be hard if not impossible to make any other way. Pairing 3D printing with laser scanning technology also provides a new level of customizing a product to the unique anatomy and needs of the user.
Greater affordability and accessibility of 3D printing in sports have resulted in the technology providing a performance boost at every level, from amateurs to Olympians. Many of the world’s top sporting manufacturers, alongside a growing number of start-ups and market disrupters, are already harnessing the technology’s capabilities.
This activity has led to a rapidly growing range of applications for 3D printing in sports, from simple items like mouthguards and shinpads to more complex creations such as golf clubs and surfboards. Further innovations will surely follow as the awareness of 3D printing’s potential continues to build.
3D printing helps win paralympic gold
World Champion paracanoeist Emma Wiggs MBE knew that she could gain more power and propel the canoe faster with a stronger, lighter paddle personalized to her individual requirements.
The basic design of the paddle has barely changed in years and wasn’t adapted to the ergonomics of paracanoeists. While its length could be altered, the blade, shaft and handle were the same for all athletes regardless of their size, weight or grip style.
With the paddle identified as an underperforming element, the Paralympic Champion teamed up with engineers at the National Centre for Additive Manufacturing at the Manufacturing Technology Centre and the National Composites Centre to devise a solution.
The redesigned carbon fiber paddle was informed by a computer simulation model of Emma’s ergonomics and individual techniques, including the angle at which the blade entered the water. Various options for the handle were designed, customized to Emma’s hands, lightweighted and manufactured using high-performance polymer 3D printing.
The final paddle had a bespoke handle that was 50% lighter, a shaft that was 254% stiffer and a redesigned blade that was 154% stiffer with an improved angle to maximize Emma’s power output on the blade’s entry into the water.
With the redesigned paddle in hand, Emma took home her second gold medal at the 2020 Paralympics in Tokyo.
According to Emma, “Races are won on small margins and this demonstrates that the right adaptions to our equipment can make all the difference on race day. I won my gold medal in a Paralympic best time under extreme pressure, but knowing I had the best possible paddle in my hands made a huge difference and massively contributed to me securing the win.”
How is 3D printing used in sports?
- 3D-PRINTED CUSTOMIZED SPORTING EQUIPMENT
Examples include:
-
- Protective Gear – i.e., helmets, eye shields, pads and protectors, mouthguards, gloves and cleats
- Sportswear – i.e., shoes, insoles, boots and selected items of clothing
- Sports Equipment – i.e., bats, clubs, heads, seats and grips
- Prostheses
- Training Equipment – i.e., accuracy aids, weights and grips
One of the most celebrated advantages of 3D printing in sports is how easily it can produce tailor-made items for optimal fit, protection, support and comfort. This is currently the most common application of the technology.
3D-printed sporting goods can be customized in many different ways, from small changes like altering the color or updating a sponsor logo to more complex modifications such as quickly redesigning and producing a piece of protective gear for a more perfect fit.
Ill-fitting and uncomfortable equipment greatly affects sporting performance. It can cause pain, sores and blisters and even increase the risk of an injury. This is especially true of a prosthesis (a device designed to replace a missing body part). Yet, the traditional process of making customized one-off items is slow and expensive.
The combination of high-definition laser scanning, sophisticated computer modeling software and 3D printing has dramatically simplified and streamlined the process.
These technologies allow the swift production of custom-fit goods that precisely match a user’s anatomy, requirements and style. No longer having to take measurements manually or manufacture molds increases the accuracy and speed of the process. This enables significantly faster design, delivery and iterative improvement.
Additionally, 3D-printed products often utilize lattice or mesh structures, something other manufacturing methods struggle to replicate. These structures offer greater flexibility and shock absorption while also being lighter, more durable and more breathable. These attributes all help to keep athletes comfortable, cool and competitive.
- 3D PRINTING IN SPORTS MEDICINE
Examples include:
-
- Face masks, medical pillows, braces, casts, splints and boots
One of the fastest-growing applications of 3D printing in sports is in the field of medicine. When an injury occurs, sports teams and athletes face significant pressure to return to fitness as soon as possible. 3D printing provides new and innovative ways to speed up recovery and reconstruct broken bones.
Not only are 3D-printed items optimized to accelerate recovery off the field, but they also enable sportspeople to continue competing while their injuries heal. 3D-printed face masks, for example, allow footballers to play while recovering from a broken nose, cheek or other facial injuries.
Similar to the protective gear and sports equipment discussed above, 3D-printed medical products can be quickly and easily customized to achieve the optimal fit and support for recovery.
- 3D PRINTING IN MOTORSPORTS
Examples include:
-
- Trim Components – i.e., dashboards, seat frames, control panels, electrical boxes, cooling vents and ducting, covers and console accessories
- Mechanical Parts – i.e., mounting brackets, suspension wishbones, brake components, exhaust systems, engine parts and some support structures
Speed and weight are essential factors in many sports but particularly motorsports. From Formula 1 and MotoGP to the World Rally Championship and the Tour de France, competitors are constantly seeking an edge to make them go faster.
These sports have long used 3D printing for ultra-rapid, early-stage prototypes which could be tested in a wind tunnel and designs modified as needed. Once optimized, the final part was then typically made using more conventional manufacturing techniques like injection molding or CNC machining.
Increasingly, 3D printing in sports is also being used to produce low-volume production final parts in all manner of materials and complex shapes. The current grid of Formula 1 cars, for example, each contains dozens of 3D-printed lightweight components which in some cases cost 90% less than those produced via conventional methods. An important consideration in sports with strict spending caps for competing teams.
- 3D PRINTING ON DEMAND
The ability to manufacture parts on demand is another key capability driving the adoption of 3D printing in sports. Bringing the production process in-house provides greater control over the process and reduces the time between design and manufacture.
Additionally, many sports teams frequently compete far away from their headquarters and associated engineering facilities. This makes having an easily accessible supply of spare parts challenging.
Teams don’t have the capacity or the budget to carry a replacement part for every eventuality, nor do they have the time to manufacture one using traditional methods. As a result, it’s not uncommon for a part to be flown first class to a race location, for example.
The speed, flexibility and efficiency of 3D printing in sports allow parts to be quickly and cost-effectively manufactured when and where needed. Digital CAD files also help to optimize stock and eliminate the need to maintain large storage facilities.
3D printed implants could elminate career ending injuries
Knees, ankles and elbows are the most common body parts damaged in sports-related injuries. Injuries to these bones, from small cracks to pieces that break off, can be painful and often stop athletes’ careers in their tracks. It can also lead to disabling arthritis.
Though athletes are disproportionately affected by these injuries, they can affect everybody.
Scientists at Rice University and the University of Maryland have engineered a 3D-printed scaffold that replicates the physical characteristics of osteochondral tissue (hard bone beneath a compressible layer of cartilage that appears as the smooth surface on the ends of long bones).
Researchers have previously struggled to replicate the gradient of cartilage-into-bone and its porosity. The Biomaterials Lab at Rice University printed a scaffold with custom mixtures of polymer for the cartilage and ceramic for the bone. Embedded pores allow the patient’s cells and blood vessels to infiltrate the implant, eventually allowing it to become part of the natural bone and cartilage.
This proof-of-concept could lead to a range of new regenerative medicine solutions. The next step in the project is to determine how to create an osteochondral implant that perfectly matches the patient’s autonomy; a challenge 3D printing is ideally suited to solve.
What are the limitations of 3D printing in sports?
3D printing in sports represents a game-changer with almost limitless growth opportunities for amateurs to pro athletes. Exciting innovations are being driven by improvements in the quality and detail of printed objects (known as resolution), the industry’s greater familiarity with the technology, and continued research in more resilient materials such as advanced composites.
Yet, the technology does have limitations. 3D printing in sports is well suited to the upper levels where products are needed in low quantities and companies have sizeable R&D budgets. Despite its potential, the technology isn’t yet able to deliver on its promise of producing mass-customized products at a high street volume or price point.
- LARGE SCALE PRODUCTION
In many cases, 3D printing in sports can produce a single item or small batch of items faster and more efficiently than conventional manufacturing methods. However, the technology still struggles when it comes to larger volumes.
Each machine can only print a certain number of objects at any one time, depending on machine size and object, so 3D printing may not be the quickest or most cost-effective technique for many products that could benefit from mass customization.
- REGULATORY STANDARDS
3D printing in sports is subject to the same quality checks as any other technology or manufacturing method. These assessments are an important step in taking innovations out of R&D labs and into widespread use. With the sports industry still in the early stages of adopting 3D printing, many of these checks have yet to be completed or in some cases started.
The approval process for safety-critical components or protective equipment is especially rigorous. Replacing tried and tested production techniques with something new carries a level of risk some manufacturers or sports governing bodies aren’t comfortable with.
This may change as 3D printing applications and materials gain the relevant approvals and appropriate regulatory standards are developed and introduced.
- INCONSISTENT QUALITY
3D printers can’t yet print perfect results every time. Failure rates depend on the machine and material used and the object printed. Also, removing surface irregularities or textures may require additional manual processing steps to achieve the desired finish.
Factors like failure rates and post-processing will likely reduce as the technology improves and people become more familiar with 3D printing in sports. For objects based on a scanned model, the quality of the finished print will also be determined by how sophisticated the scanning equipment is. Higher-quality prints may require investing in a more expensive scanner and 3D printer.
- PART SIZE
3D printers have inherent size constraints that make them incapable of producing large components. In some cases, multiple smaller parts can be joined together, though this may not always be an ideal solution.
Manufacturers of 3D printers are working to address the size limitations of existing machines, such as by removing the barriers present in typical print chambers.
3D printing ushers in a new era of head protection
Helmets are a critical piece of safety wear that defends against skull fractures and serious brain injuries. How well a helmet fits the wearer’s head and whether it moves around or not affects how much protection it provides.
Riddell is a company specializing in sports equipment for American football and is widely known for its line of helmets and head impact monitoring technologies. To advance on-field protection for players at all levels, Riddell has teamed up with Carbon 3D to create the next generation of helmet.
The Riddell SpeedFlex Precision Diamond helmet model combines Riddell’s Precision-Fit head scanning and helmet fitting process with a customized 3D-printed helmet liner precisely contoured to the player’s head.
Each helmet contains more than 140,000 individual struts carefully arranged into lattice design pads designed for maximum impact absorption with superior comfort and fit. The lattice structures are printed in a custom resin designed specifically by Carbon to meet Riddell’s rigorous performance requirements.
The liner pads go between the outer helmet shell and the player’s head and their design has been informed by analyzing more than five million on-field impacts captured by Riddell’s smart helmet technology. This database allows each lattice structure to be customized and individualized depending on a player’s size, position and style.
According to a senior spokesperson for Riddell, no two players play the same way, they all have different styles and tendencies on the field. With the SpeedFlex Precision Diamond, players are not only experiencing the latest in head protection but can also dictate where the helmet is positioned to improve sightlines and maximize field vision.
Get multiple quotes for your parts in seconds