3D Printing in consumer electronics
3D printing is helping redefine many aspects of consumer electronics, from bringing innovations to market faster to making custom accessories and circuit boards.
Introduction 3D printing in consumer electronics
This guide will help you to understand:
- What is 3D printing?
- How is 3D printing disrupting consumer electronics?
- Can electronic circuit boards be 3D printed?
- How is 3D printing used in consumer electronics?
- What are the limitations of 3D printing in consumer electronics?
- 3D printing is helping eliminate e-waste
What is 3D printing?
3D printing, or additive manufacturing, is a production technique that creates a three-dimensional object from a computer-aided design (CAD) file. The term covers several different processes that see one or more materials – typically plastic, metal, wax or composite – being deposited layer by layer to build a shape.
A computer controls the entire process, making 3D printing a cost-effective, efficient and accurate method to create objects of almost any geometry or complexity. Today, 3D printing is used in every industry to produce prototypes, tools and jigs, components and end-use parts.
3D printers come in various sizes, from small enough to fit on a benchtop to large-format industrial machines.
Large printers can produce bigger objects, but the machines take up more space and cost significantly more than benchtop printers. Achieving a successful print is also more complex on a large-format printer due to the volume of material and printing time involved.
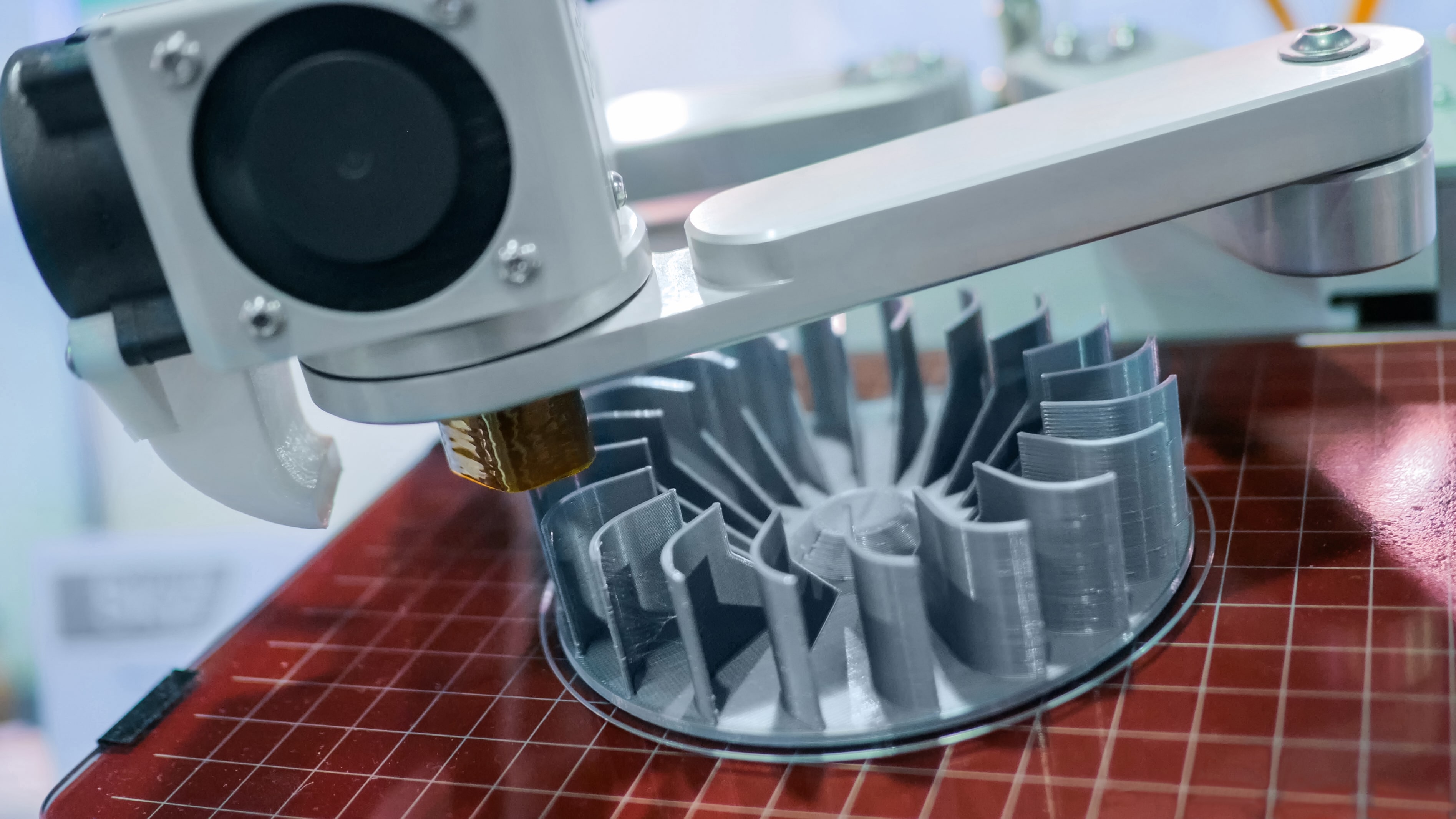
How is 3D printing disrupting consumer electronics?
3D printing in consumer electronics provides many advantages, including:
- Streamlining and simplifying product development
- Greater design freedom
- Faster time to market
- Producing lighter and better-performing components
- More customer personalization options
- Increased cost and resources efficiencies
- Consolidating previously separate parts into a single unit
- Optimizing inventory and supply chain management
Speed to market is crucial to the success of every product but especially so for consumer electronics. With technology advancing faster than ever, the release window for new products is continually becoming increasingly shorter.
Where once you could measure the lifespan of a device in years, today it is months. It took Apple half a decade to release its first five iPhone models compared to five variations in 2022 alone. One reason for this is strong customer desire for new models, features and innovations at ever-cheaper prices.
Another factor driving the growth of 3D printing in consumer electronics is the explosion of devices containing digital technologies. Traditional consumer electronics devices were primarily entertainment and communication focused – televisions, music players, computers, gaming consoles and phones.
Recently, we have seen the arrival of more and more products offering some form of internet connectivity. These include all manner of lightweight wearables, streaming devices and ‘smart’ home appliances.
Unsurprisingly, consumer electronics manufacturers are turning to 3D printing to stay ahead of the competition and satisfy market demand more cost-effectively. Examples of 3D printing are present in all stages of production, from research and development (R&D) and manufacturing to personalization and aftermarket accessories.
All the world’s most recognizable consumer electronics brands, including Apple, Samsung, Sony, Microsoft, Panasonic and HP, are already using 3D printing. As are many start-ups and market disruptors.
Alongside using the technology in their operations, several larger electronics companies also manufacture 3D printers for the industrial market. Indeed, smaller desktop 3D printers are themselves consumer electronics.
Despite growing adoption, 3D printing in consumer electronics is still relatively low. It is primarily used for rapid prototyping and modeling or producing protective or customized cases rather than final parts.
That may change as researchers continue to develop ways to 3D print circuit boards and electrical or conductive elements. This work could see 3D-printed devices with electronics embedded inside.
This would be faster and less resource intensive than having to manufacture both electronics and enclosures. It could also remove the need for separate circuit boards.
Can electronic circuit boards be 3D printed?
3D-printed circuit boards (PCBs) are a much-discussed application for 3D printing in consumer electronics. The attraction of 3D-printing PCBs includes the opportunity to bring manufacture in-house and avoid supply chain disruptions, and being able to produce more complex circuits while doing so faster and more cost-effectively.
PCB fabrication usually involves many repetitive milling and etching steps. The number of steps increases as circuits become more complex. The process is time-consuming, uses hazardous chemicals and generates significant waste. 3D printing PCBs helps overcome all these issues.
Standard printed circuit boards are also rigid and come in a handful of standard shapes. 3D-printed PCBs offer almost limitless design freedom and can be made using flexible, even stretchable, materials.
There are two types of 3D-printed PCBs – printing with conductive material to form the circuit directly or printing a circuit board with hollow channels to be later filled with conductive material. Some printers can also print boards, whereas others need them adding.
While there has been some success in 3D-printed PCBS, it has mostly been restricted to proofs-of-concept and small-scale production. Much greater research and development is needed for 3D-printed PCBs to seriously challenge traditional mass-production techniques.
Trials are currently ongoing regarding possible uses in biomedicine, renewable energy, aerospace and defense. Some 3D printer companies have also released dedicated machines for 3D printing electronics.
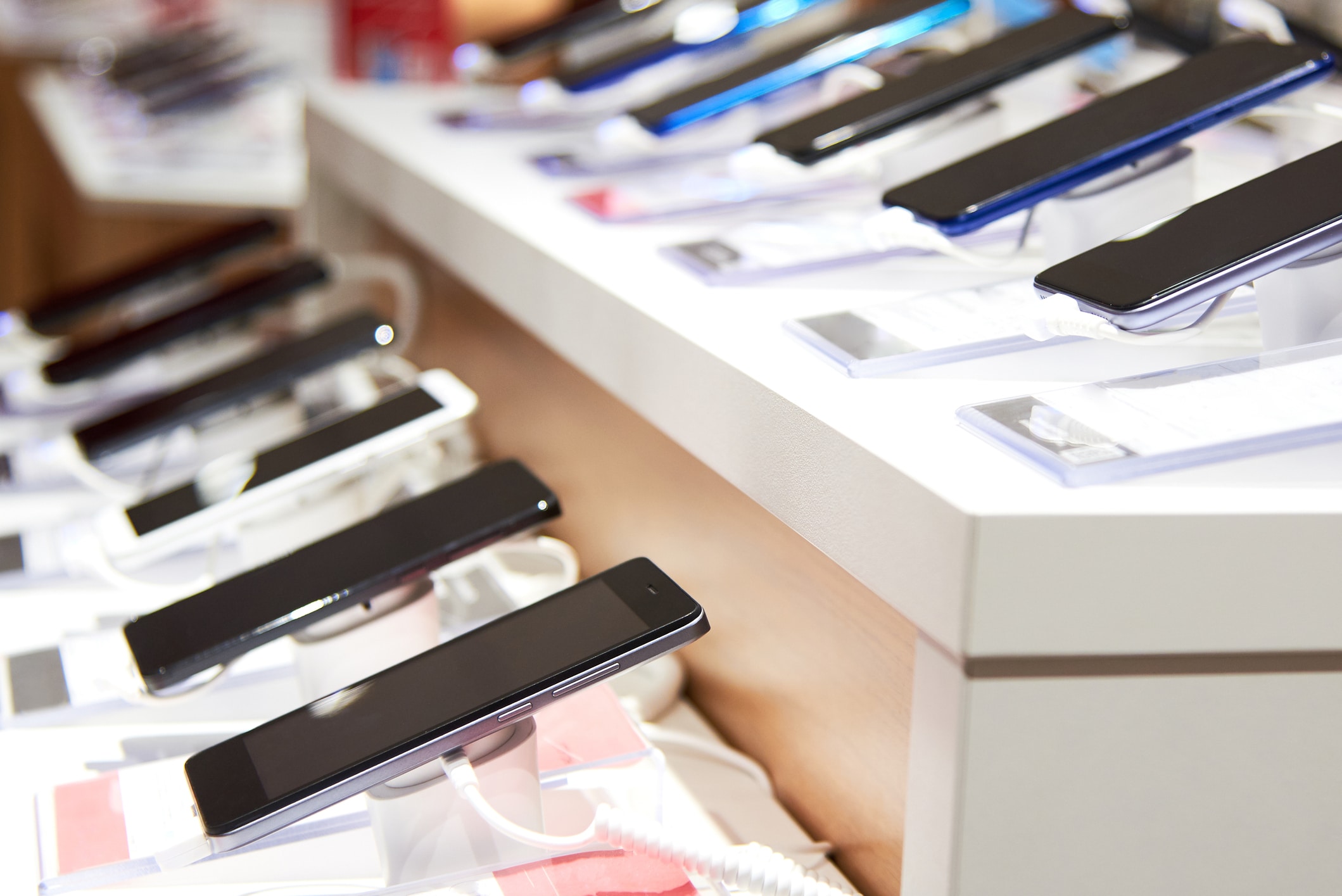
How is 3D printing used in consumer electronics?
-
RAPID PROTOTYPING
Physical prototypes, whether simple mock-ups or detailed scale models, are a vital part of product development. Early-stage concept models allow designs to be validated, functionality to be tested and to see how products truly look and feel.
Prototyping helps show potential issues or improvements earlier in the manufacturing process and ensures the final project meets the design specification. The downside is the time and cost involved. Prototyping and testing are the most time-consuming part of product development. At least, they used to be.
3D printing compresses the product development cycle by allowing parts to be designed, printed and tested in a fraction of the time and cost of traditional manufacturing methods.
Reducing the time between design iterations allows more tests to be carried out in the same or shorter period. This enables manufacturers to optimize and release new products much faster, critical in a market as competitive as consumer electronics.
-
ELECTRONICS ENCLOSURES
Enclosures are another common use of 3D printing in consumer electronics. The technology helps overcome a key design challenge for electronics manufacturers – how do you securely and safely hold the internal electrical components together while ensuring the whole product remains stylish and user-friendly?
An enclosure (or housing) protects sensitive electronic equipment such as circuits, switches and displays while preventing electrical shock to users. Additionally, visual appeal is crucial in the consumer electronics market, with modern devices thin, sleek and touchscreen-enabled. Meeting such goals requires a well-designed, optimized enclosure that fits with the overall product form. It must also be reliable and easy to make.
3D printing can uniquely achieve these goals thanks to its ability to produce lighter parts that are as strong, if not stronger, than those manufactured using traditional methods. The speed of 3D printing also means a physical enclosure can be quickly measured against what it has to contain, with any changes to dimensions made as needed.
Furthermore, 3D printing brings a new level of design freedom. It can produce highly complex, custom shapes that would be hard or impossible to produce any other way. This helps product engineers to not only design better enclosures but also 3D print objects with internal cavities already inside them.
-
PROTECTIVE CASES
Another use of 3D printing in consumer electronics is cases to protect devices from falls, knocks and spills. Similar to enclosures, 3D-printed cases can be made quickly with an optimized balance between weight and strength.
Cases can also be easily customized to individual requirements with a wide selection of designs, colors, textures and materials. Depending on the material chosen, cases can be clear, flexible, rigid, highly accurate, ergonomic, smooth to the touch or budget-friendly.
Aftermarket accessories like cases have long been available but only in a limited range of designs. On-demand manufacturing with 3D printing offers an infinite choice in terms of customization options. Examples include custom cases, grips, controls, inserts, stands and holders.
Designs can often be viewed, changed and chosen using an app and then collected in-store or delivered direct. The cost of 3D printing one item is the same as thousands, regardless of how complex it is, and the entire process is done in days, sometimes hours.
3D printing brings custom-fit devices to the mass market
Challenges around speed, scalability and cost have traditionally hindered customized manufacturing from becoming mainstream. Advancements in 3D printing technology have started to change that.
The recent development of skin-safe biocompatible materials has led to a growing range of customized 3D-printed headphone tips and earbuds. These provide a secure fit with a greatly reduced possibility of the earphones falling out of the ear. Comfort and noise isolation are also improved.
Bringing a custom-fit solution to the earphone market relies on a simple, accessible and scalable workflow that combines the latest digital, CAD automation and 3D printing technologies.
Global audio brand Sennheiser Ambeo recently teamed up with Formlabs, a leading 3D printing company, to develop such a process. One that enables customers to affordably and easily customize their earphones for a unique fit.
Customers can now use a smartphone app to scan their ears, replacing the more traditional and time-consuming ear impression process. The use of artificial intelligence (AI) delivers a scan in less than 60 seconds. AI also improves scan quality and reconstructs parts of the ear not captured by the phone.
The scan is sent directly to a cloud-based system that uses machine learning to quickly convert the scanned shape into a specific earphone design ready for 3D printing.
The finished 3D-printed custom ear tips are highly accurate and can be produced in several materials and colors. Initials and logos can also be engraved for extra personalization.
This is just one example of how companies are using 3D printing to change how customers interact with their products by giving a more user-centric approach to product development. Additionally, the largely automated process and smooth final surface finish reduce the manual labor required for mass-customized production.
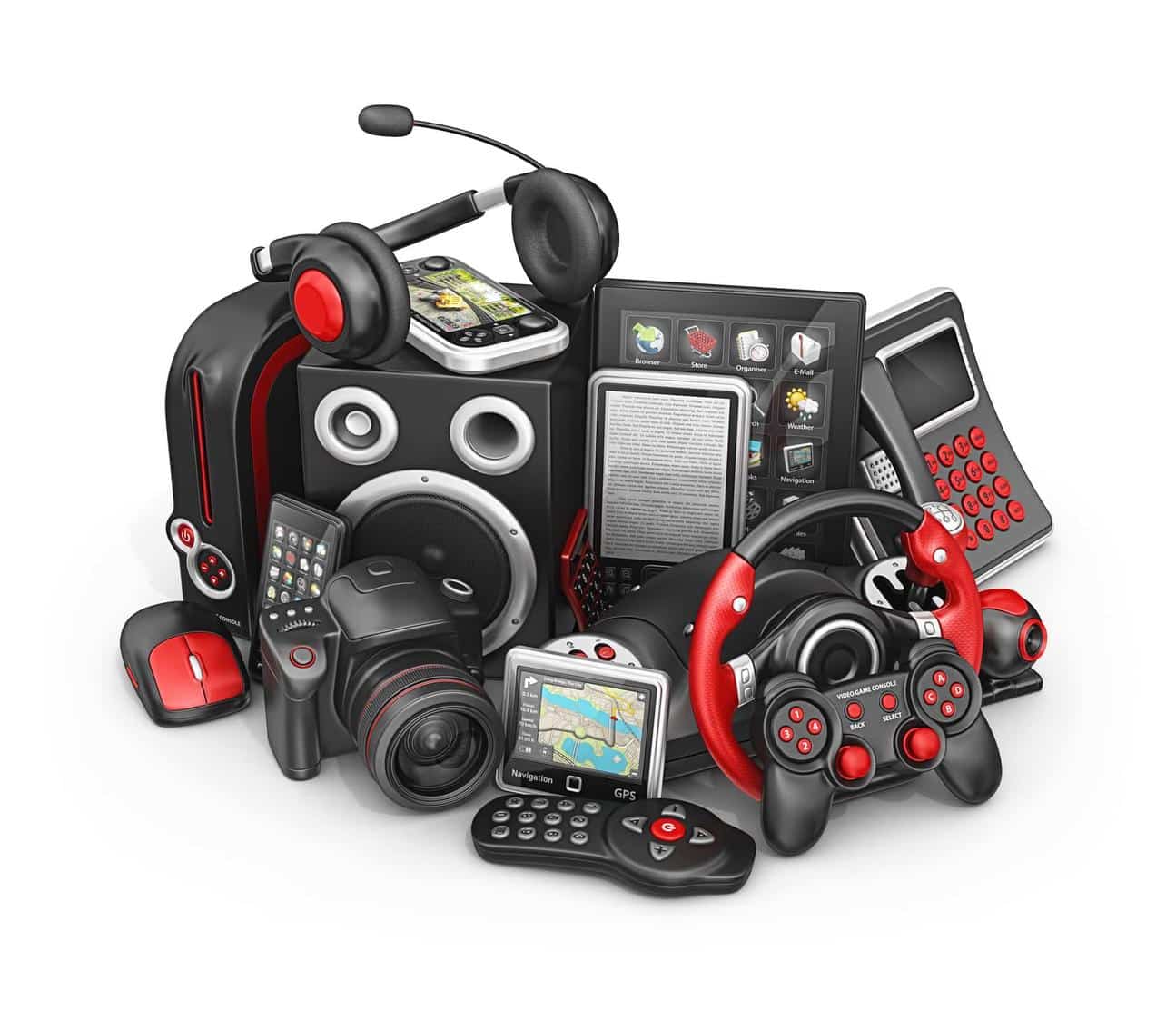
What are the limitations of 3D printing in consumer electronics?
-
LARGE SCALE PRODUCTION
3D printing technology can often produce a single item or small batch faster and more efficiently than conventional manufacturing methods. However, it still struggles when it comes to high-volume production.
A 3D printer can only print a certain number of items at any time, depending on machine size and object, so it may not be the quickest or most cost-effective technique for large production runs.
-
LACK OF FAMILIARITY
Though adoption is growing, 3D printing in consumer electronics is not yet ubiquitous. Use cases largely revolve around making prototypes, enclosures, protective cases and luxury goods. Higher-level applications are in the process of being realized, but for now, 3D printing remains secondary to traditional production methods, particularly for mass-market, high-volume manufacturing.
-
INCONSISTENT QUALITY
3D printers can’t yet print perfect results every time. Failure rates depend on the machine and material used and object being printed. Achieving the desired surface finish may also require additional manual processing steps.
Failures and post-processing steps will reduce as the technology improves and people become more familiar with 3D printing.
For custom objects based on a scanned model, the quality of the finished print will also be determined by how sophisticated the scanner or software is. Higher-quality prints may require more capable yet more expensive equipment.
3D printing is helping eliminate e-waste
Electronic waste is the world’s fastest-growing waste stream. More than 50 million metric tons of e-waste were generated in 2021. Consumer electronics is a common source, with televisions, computers and mobile phones among the most discarded items.
Many such devices could have been reused, refurbished or recycled rather than replaced. The fault is often as minor as a broken switch, screen or similar component. However, it’s not always easy, affordable or convenient to source and fit replacement parts.
Increased emphasis on reducing the world’s carbon footprint has led companies to explore more sustainable and circular alternatives. They have discovered that 3D printing technology offers several solutions to help combat e-waste.
Consumer electronics manufacturers and third-party companies are increasingly using 3D printing to provide cost-effective replacement parts on demand at the point of need.
Other companies, such as have Germany-based Reco-E, found pioneered an innovative solution to process existing e-waste.
Electrical components typically contain precious and rare earth metals. These are typically extracted by incinerating the waste and separating the metals from the melted plastic slag.
Reco-E uses a cleaner, chemical-free grinding method that sees all material recovered and given a second life. The extracted metal is turned into high-value, high-purity metal powders for metal 3D printing (or additive manufacturing). The granulated plastic is collected and turned into sewer pipes, for example.
Scientists are also working to develop a biodegradable plastic that can be used to produce 3D-printed circuit boards. Traditional PCBs are made from glass fibers, resins and metal wiring. This mix of materials makes them difficult and costly to recycle. A biodegradable PCB would be highly beneficial for single-use electronic devices as well as consumer electronics more broadly.
Get multiple quotes for your parts in seconds