Medical 3D Printing
Medical 3D printing is creating truly personalized healthcare thanks to its ability to quickly and cost-effectively produce patient-specific devices, implants, prostheses, and even tissue.
What is 3D printing?
3D printing, sometimes referred to as additive manufacturing, is a production technique that creates a three-dimensional physical object from a digital design file. The term covers several different processes, all involving one or more materials – typically plastic, metal, wax or composite – being deposited layer by layer to build a structure.
The entire process is computer controlled, which makes 3D printing a very cost-effective, efficient and accurate method to create objects of almost any geometry or complexity. 3D printing is used in almost all industries to produce everything from models, prototypes, tools and jigs to components and finished goods.
3D printers are available in various sizes from those small enough to fit on a benchtop to large-format industrial machines.
Large printers are capable of producing bigger objects but the machines take up more space and are significantly more expensive compared to benchtop printers. Achieving a successful print is also more complex on large-format machines due to the material volume and printing time involved.
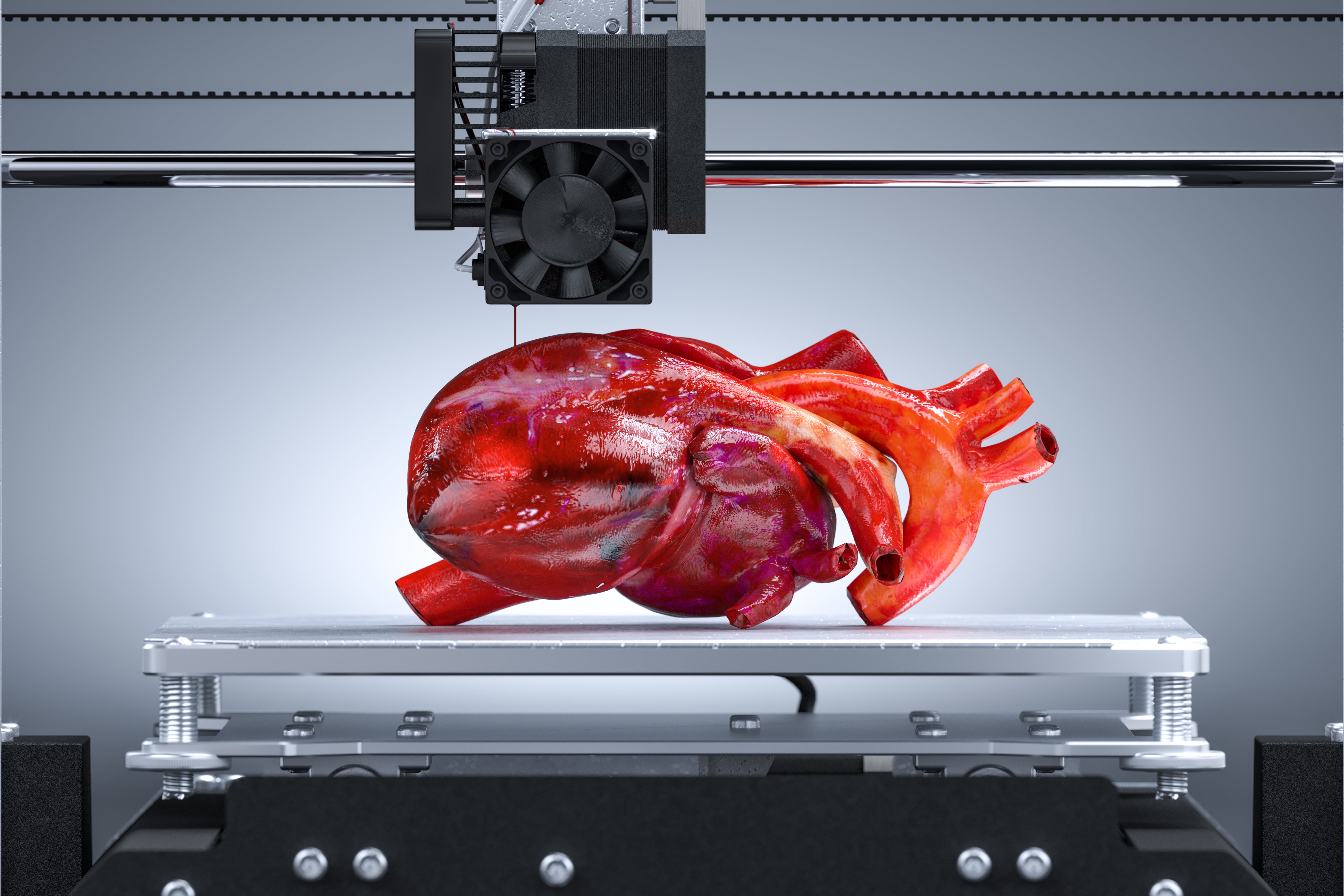
How does 3D printing benefit the healthcare industry?
3D printers help the medical sector in three key ways:
- Improved patient outcomes
- Time and cost savings
- Accelerated research and development cycle
The freedom to produce patient specific objects is the opposite of traditional methods that rely on mass-produced, standardized implants, tools and prostheses (artificial limbs).
Manufacturing unique products on a made-to-order basis isn’t a new concept but it is typically prohibitively expensive and has a long lead time (the period between ordering and delivery).
With 3D printing, however, the cost of producing one object is the same as making thousands, regardless of how unique or complex the item is. Production can also take place closer to where demand is rather than in a factory on another continent. This greatly reduces lead times and allows for a more agile, iterative manufacturing process.
Medical 3D printing also compresses the research and development timeline by reducing the time between design improvements, allowing more testing to be conducted in the same or shorter time period and highlighting potential issues earlier in the process.
Medical 3D printing in time of crisis
During the Covid-19 pandemic, the world faced critical shortages of essential medical goods due to soaring demand and disruptions to manufacturing and transportation. The most needed items were those in the shortest supply, namely personal protective equipment (PPE) and ventilators.
The flexibility and speed of 3D printing saw the technology come to the fore during this time, with many organizations putting printers to work to produce much-needed items.
UK-based Photocentric was one such example. The company used its patented medical 3D printing technology to rapidly deliver millions of face shields to protect frontline workers. Its Peterborough warehouse was transformed into a streamlined, purpose-built factory where a fleet of 45 large-format printers manufactured more than 50,000 components daily.
According to a Photocentric spokesperson, the success shows that medical 3D printing is no longer reserved for slow, expensive prototyping but can make the quantity needed, when needed, where needed and at a competitive price.
How is medical 3D printing being used?
Medical 3D printing covers many disciplines and serves a wide spectrum of needs. The four most common are:
-
PROSTHESES
An improperly fitting prosthesis can greatly affect a patient’s health and daily life, causing pain, sores and blisters and an increased risk of a fall or other accident. Additional consultations or even surgeries to improve the fit cost the patient and healthcare provider extra time and money.
The combination of high-definition digital scanners and 3D printers enables the creation of a comfortable, affordable prosthesis that perfectly matches a patient’s unique anatomy or injury.
This removes the need for manual measurements and mold-making, increasing the accuracy and efficiency of the process. This enables significantly faster design and delivery of customized solutions from simple devices to complex, multijointed creations.
Medical 3D printing is primarily used to produce parts of the prosthesis that come into direct contact or interact with the patient’s body. Traditional manufacturing techniques and materials are typically used to produce the other components and support structures.
-
IMPLANTS (ORTHOPEDIC, ORTHODONTIC AND DENTAL)
Like prostheses, a wrongly fitted implant can have a negative impact on patient wellbeing. Medical 3D printing allows surgeons to create personalized implants that are used to replace or strengthen bones and joints.
The ability to create complex structures with a 3D printer has improved the design of orthopedic implants, for example, by providing better bone binding surfaces and more durable materials.
Some studies have shown that 3D printed structures and meshes, depending on the printing material used, can last longer, perform better and offer greater functionality than traditional implants made from titanium and zirconia ceramic.
Dental implants such as false teeth, caps and bone repair have long been a vital part of dentistry. As with other applications, medical 3D printing allows dentists to customize and produce implants with higher speed, accuracy and efficiency and a superior fit.
The technology also allows for better control over the implant structure, and dentists can choose from hard-wearing materials such as ceramics, polymers and composites.
-
ANATOMICAL MODELS
Surgeons use digital 3D scanning and imaging techniques to extensively plan surgical procedures before performing them. Highly detailed internal images are routinely provided by ultrasound, magnetic resonance imaging (MRI) and computed tomography (CT) machines. However, these images are typically viewed on a 2D screen which limits visibility and understanding of the surrounding anatomical structures.
3D printers use these digital files to build ultra-realistic and accurate 1:1 scale models of an organ or body part. These models enable doctors to better plan and rehearse actions ahead of time. This is especially beneficial for more complicated procedures or those the surgical team hasn’t routinely performed.
Practicing procedures makes surgical interventions safer, faster, more accurate and personalized which results in better outcomes for patients. Additionally, these models can be shown during preoperative consultations to better explain to patients what their medical situation is and the treatment.
Models also provide medical students and junior doctors with a fuller education. Being able to hold, inspect and manipulate models of real-world tumors, fractures, abnormalities and other injuries provides the opportunity to better understand and therefore treat them.
-
SURGICAL INSTRUMENTS
Cutting and drilling guides assist surgeons in placing implants with more precision, efficiency and safety. As a result, procedures are faster, less invasive and requires a shorter patient rehabilitation time.
Medical 3D printing is fast replacing conventional methods of producing these guides as it is faster, easier, can be completed on-site and most importantly, can be customized to a patient’s exact morphology.
Surgical or medical instruments that have been 3D printed include a wide range of forceps, retractors, clamps and tool handles. The primary benefit of a 3D-printed instrument is how easily it can be customized to a specific surgeon’s requirements, unlike 3D-printed guides where the main benefit is how easily they can be customized to an individual patient.
In some cases, a medical practitioner can provide feedback on a 3D-printed instrument and have a revised version in their hands that same day.
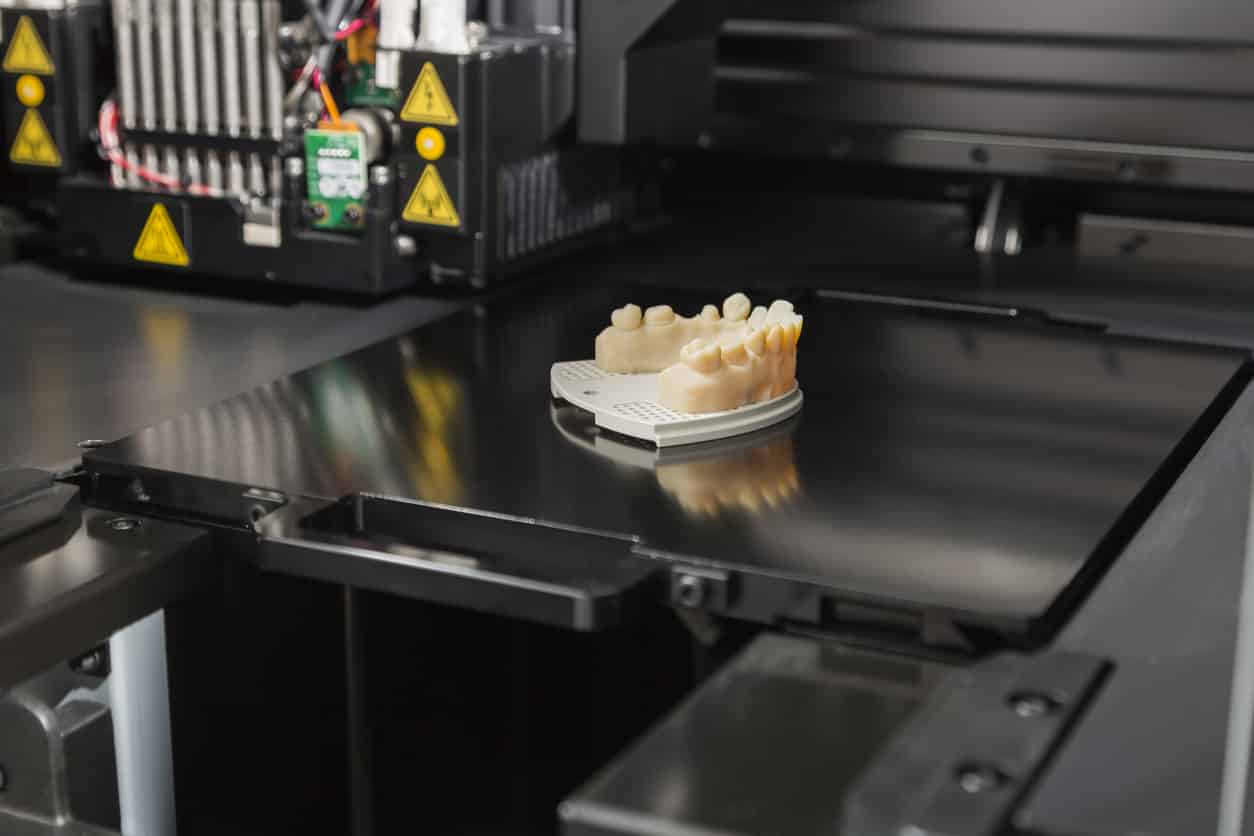
The value of a 3D- printed anatomical model
Bradley was born with a heart tumor and underwent several open-heart surgeries including having a defibrillator fitted to protect him from sudden cardiac death. At 16, he found himself back in hospital for yet another procedure to stop the electrical interference caused by the large tumor.
Looking for additional information on how best to treat his tumor, the medical team contacted 3D printing services provider Materialise to create a 3D-printed replica of Bradley’s heart from his CT scan data.
The model allowed the physicians to better understand the complex relationship between the tumor (printed in a hard opaque material) and surrounding anatomical structures (printed in a flexible transparent material).
Having the model enabled the team to confidently proceed with surgery and also allowed Bradley and his family to better understand his unique anatomy.
What are the growth opportunities for medical 3D printing?
Constant research means new applications for medical 3D printing are always emerging. The areas expected to see significant growth over the next five to ten years include:
-
PERSONALIZED MEDICINE
3D printed drugs are accelerating the pharmaceutical industry’s move away from the traditional high-volume, one-size method of production toward a more personalized and precise model.
The main benefit of using 3D printers to produce medicine is the ability to manufacture small batches of any shape and size with dosages set for each patient. Printing drugs on-demand dramatically reduces waste, costs and time, particularly in the development of new drugs.
Pfizer estimates that bringing a new medicine to market takes an average of 12 years and costs more than $1 billion. Furthermore, for every 10-20 medicines identified in the laboratory, only one will ever reach patients. The others will fail along the way for any number of reasons.
Medical 3D printing increases the speed and affordability of clinical trials of drugs as test batches can be manufactured in small quantities rather than mass-produced. Eventually, we could see 3D printers installed in pharmacies, hospitals and clinics, especially in remote areas, producing personalized drugs as and when needed.
-
MEDICAL DEVICES
More than 90% of the top 50 medical device companies use 3D printing to create high-speed, low-cost prototypes of medical devices, as well as jigs and fixtures to simplify testing, according to 3D printing specialist, Formlabs.
Beyond rapid prototyping, medical 3D printing is being used to produce components and cases for end-use medical devices and, in some cases, the entire device itself. This capability came to the fore in the wake of Covid-19 when 3D printed alternatives to traditionally sourced supplies become commonplace, nasal swabs being just one example.
Other 3D-printed medical devices include inhalers, injectors, needle holders, surgical tool trays, splints and testing equipment. The technology is also improving traditional manufacturing processes by producing bespoke tooling such as models, patterns, casts and dies for use in a range of molding and casting machines.
-
BIOPRINTING
3D bioprinting is similar to 3D printing except that it prints layers of living cells, known as bio-ink, rather than plastic or metal. Bio-ink is used to create artificial skin tissue, bone, blood vessels and potentially whole organs used for transplants, grafts, training or research purposes.
Bioprinting is still in its infancy due to the complexity involved in reproducing living material, particularly organs such as hearts, livers and kidneys. Advancements are happening, however, thanks to the pioneering work of universities, researchers and private enterprises around the world.
What motivates them is the prospect of eliminating the need for donated organs and the risk of rejection by 3D printing new organs using a patient’s own cells.
3D printing bone
Bone reconstruction procedures are performed millions of times annually, from congenital bone defects to victims of accidents and cancer patients. Currently, these patients receive a harvested bone piece or a titanium implant that remains in their bodies for the rest of their lives.
Danish MedTech company Ossiform has developed a disruptive patented technology to reconstruct the patient’s exact anatomy with 3D printed, patient specific implants with a natural bone porosity. The implants are made from natural biomaterials that degrade over time and remodel into real living bone tissue.
The P3D bone implants can be designed to deliver additives, including antibiotics and chemotherapy, which can be released over a controlled and prolonged period. These provide wide ranging benefits for patients and open new options for treatments of bone defects.
The technology is also used to produce a 3D printed R&D product, the P3D Scaffolds, for enhancing bone research. The first P3D bone implant for human use is expected to reach the market in the second half of 2022.
What are the limitations of medical 3D printing?
-
REGULATORY STANDARDS
Medical 3D printing must undergo the same assessment process as any other healthcare technology. Regulatory approval is fairly straightforward for objects that assist medical staff like anatomic models, instrument trays and tool handles as these have minimal contact with a patient, if any.
Internal objects such as bone implants, artery stents and heart valves are subject to more rigorous safety requirements. Gaining approval is made more difficult due to a lack of a comprehensive regulatory framework.
Several regulatory bodies are working on developing appropriate standards for 3D printing in healthcare, the US Food and Drug Administration (FDA) being one example.
Confusingly, one of the key advantages of medical 3D printing also makes regulatory approval – and therefore its more widespread use – more difficult. Compared to an off-the-shelf standardized product, custom-made devices are much harder to approve as each must be tested and certified.
-
INCONSISTENT QUALITY
3D printers don’t print perfect results every single time. Failure rates depend on the machine and material used and what is being printed. Also, removing any surface irregularities or textures may require additional manual processing steps to achieve the desired finish.
Failure rates and post-processing will likely reduce as 3D printers improve and people become more familiar with using the technology.
-
LARGE VOLUMES
In many cases, medical 3D printing can produce a single item or small batch of items faster and more efficiently than traditional manufacturing methods. However, each machine can only print a certain number of objects at any one time, depending on machine size and object, so might not be the most suitable or cost-effective method for large production runs.
Get multiple quotes for your parts in seconds