Vacuum Forming Plastic
Vacuum Forming Plastic is an easy method of forming plastic parts. It is used in a wide variety of applications. Learn more now!
Introduction: Vacuum Forming Plastic
Vacuum forming is a widespread manufacturing method to shape plastic materials. The process is popular with manufacturers due to its low price and design flexibility. It is best suited for products that require precision forming on one side. It is often used to protect delicate items like electronics and certain foods and is used for a wide variety of products. Invented in the 1800s, the first vacuum forming machine was built in 1938 for the Spitfire aircraft, but it wasn’t until 1964 that the first vacuum forming machine was patented.
This article discusses Vacuum Forming Plastic, its advantages, typical applications, and benefits.
What is Vacuum Forming?
Vacuum forming is a simple process that uses a mold to form the product geometry with a plastic sheet placed securely in a frame clamp that is then heated. It is placed onto a mold with numerous small holes drilled through the form. This allows a vacuum to form the heated plastic pressed over the mold. Once cool, the formed plastic is removed, and excess material is trimmed. It is a reasonably quick process taking only a few minutes, although the intricacy of the part being manufactured may require more cooling and trimming time.
Vacuum-formed molds come in two basic types, male (positive) or female (negative). The male molds are convex and conform to the inside dimensions of the plastic part. Female molds are concave and form the outer dimensions.
The Vacuum Forming steps are as follows:
- Clamp the plastic sheet in the frame
- Heat the plastic sheet until pliable
- Vacuum as the sheet is placed over the mold
- Cool the plastic sheet forming around the mold—fans and misters may be required
- Release the plastic from the frame
- Trim off the excess material
- Optional: post-processing may include sanding, painting, etc.
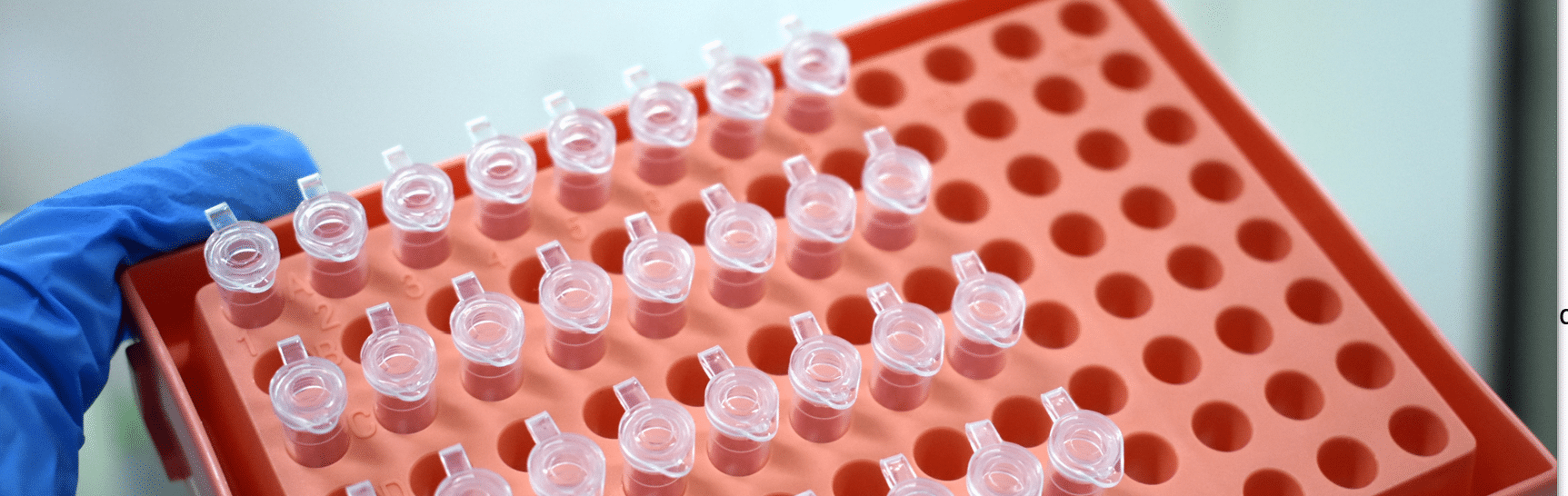
What is Plastic?
Plastic is derived from numerous synthetic materials from either fossil fuels or renewable materials such as cotton or corn. The plant cellulose allows corn and cotton to be processed into plastics. These materials are lightweight, durable, and inexpensive to manufacture.
Physics defines plasticity as the property of a body that does not oppose a deforming force, and the body is permanently deformed. The word “plastics” originates from the term “plasticity.”
The basic types of plastic materials are based on chemical structures, including acrylics, halogenated plastics, polyesters, polyurethanes, and silicones. In manufacturing, plastics are classified based on the product design purpose; this includes biodegradable plastics, conductive polymers, elastomers, engineered plastics, thermoplastics, and thermosets.
With all of the different plastics classifications, polymer families are categorized as to whether the material is reversible after the deformation process. These two polymer families are:
- Thermoplastics — The chemical composition of these plastics does not change when heated. These plastics become pliable again when reheated. Some popular materials are acrylic, nylon, polypropylene, polyethylene, polystyrene, and polyvinyl chloride (PVC).
- Thermosetting Polymers—Also called “Thermosets,” these polymers can only be melted to shape once. These polymers never soften again when heated. Standard materials are polyester, vinyl ester, and polyimides.
Plastic use is widespread in many of our packaging and products. Over 10 billion tons of plastic have been used in the past 70 years, and its use is increasing exponentially.
Application of Vacuum Forming Plastic
Vacuum-formed plastics are used in most of the products we purchase and use daily. A few of these applications include:
- Automotive and Transportation—Bumpers, floormats, body parts, consoles, air ducts, bed liners, trailers, skid plates, …
- Consumer Goods—Toys, home décor, refrigerator liners, Tupperware®, vacuum cleaner covers, appliance covers and parts, …
- Electronics—Stands, casings, covers for printers, monitors, …
- Food Packaging—Food storage, clam shells, egg crates, divider trays, …
- Industrial—Crates, containers, trays, …
- Medical—MRI and X-ray components, medical carts, heating pads, surgical kits, fingerguards, blister packs, …
- Packaging—Containers for toothbrushes, cosmetics, razors, electronics, …
- Other Applications—Trade show displays, custom décor, …
Below are some of the many thermoplastics that are used in vacuum forming:
- Acrylic (PMMA)
- Acrylonitrile butadiene styrene (ABS)
- Polycarbonate (PC)
- Polyethylene (PE)
- Polyethylene terephthalate glycol (PETG)
- Polypropylene (PP)
- Polystyrene (PS)
- Polyvinyl chloride (PVC)
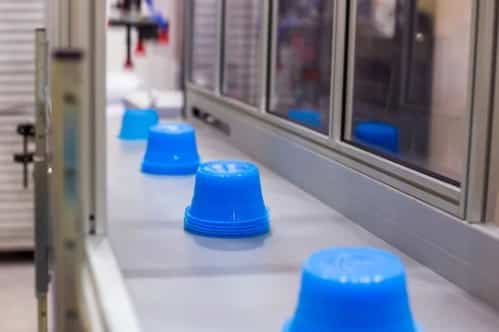
Benefits of Vacuum Forming Plastic
The vacuum forming of plastics is an affordable manufacturing process that is easy to prototype and manufacture. The tooling is far less expensive, and product turnaround is faster because tooling is easier to manufacture. The production time is less than half that of injection molding. The product is rugged and robust, and the process is scalable.
The vacuum forming allows the flexibility to test new designs and prototypes without significant losses in productivity and utilization. Because it is cost-effective, it is the preferred process for small to medium-sized production runs. Color options are plentiful, and product customization is not complicated. Vacuum forming manufactures food-grade products that are sterile. Engineered materials are available for various applications.
All of these advantages translate to a faster time to market with a relatively inexpensive and durable product.
Get multiple quotes for your parts in seconds