SLS 3D Printing Metal
SLS 3D printing metal is a new method of printing metal parts. It is used in a wide variety of applications. Learn more now!
SLS 3D Printing Metal
Selective laser sintering (SLS) three-dimensional (3D) metal printing is a method of manufacturing objects from engineering design files through sintering, the laser fusion of layers of powdered material to create an object. First developed in the mid-1980s, SLS is popular with engineers and manufacturers as the preferred method for prototyping parts due to its affordability, speed, accuracy, and strength.
This article discusses SLS 3D printing metal, its advantages, typical applications, and benefits.
What is SLS?
SLS is the most common powder bed fusion 3D printing system used today. It is an additive manufacturing technology (AM) that creates an object by constructing (printing) it layer by layer. A high-powered laser builds the part in a bed of preheated powder, layer by layer, per a three-dimensional computer drawing.
The laser fuses the powder particles, and the powder bed supports the product as it is built; this eliminates the need for internal product structural support. The powder bed has a roller system that spreads thin layers of powder before the sintering process. The finished product must cool, and any loose powder must be removed in a post-printing cleaning procedure. The remaining unsintered powder can be used for the next production run, making SLS a zero-waste technology.
SLS is ideal for rapid prototyping, small-batch production, and custom manufacturing. The printing process is perfect for complex geometries, including thin walls, undercuts, reverse dimensions, tapers, and other intricate design features.
What is Metal SLS 3D Printing?
Metal SLS 3D printing is a widespread additive manufacturing process with exceptional accuracy, the ability to print complex geometries, and mechanical properties similar to injection molded parts. The process is ideal for functional prototyping and small-batch production.
SLS printed parts utilize nylon materials, polymers, ceramics, and metals. They are strong like standard metal parts but lighter. SLS printing systems are often associated with plastic-based materials, including carbon fiber nylon and aluminum nylon, which are also lightweight, high-performance materials. These materials provide even greater strength with the appearance of metals while maintaining a lighter weight.
Nylon materials with carbon fiber and aluminum are used as alternatives to metal parts. They are used in various applications typically reserved for metals. This includes jigs, fixtures, tooling, and functional prototypes.
The SLS printers can also print aluminum and stainless steel alloys through a derivative process called direct metal laser sintering (DMLS). It is also called selective laser melting (SLM). The printing process is the same but with different materials.
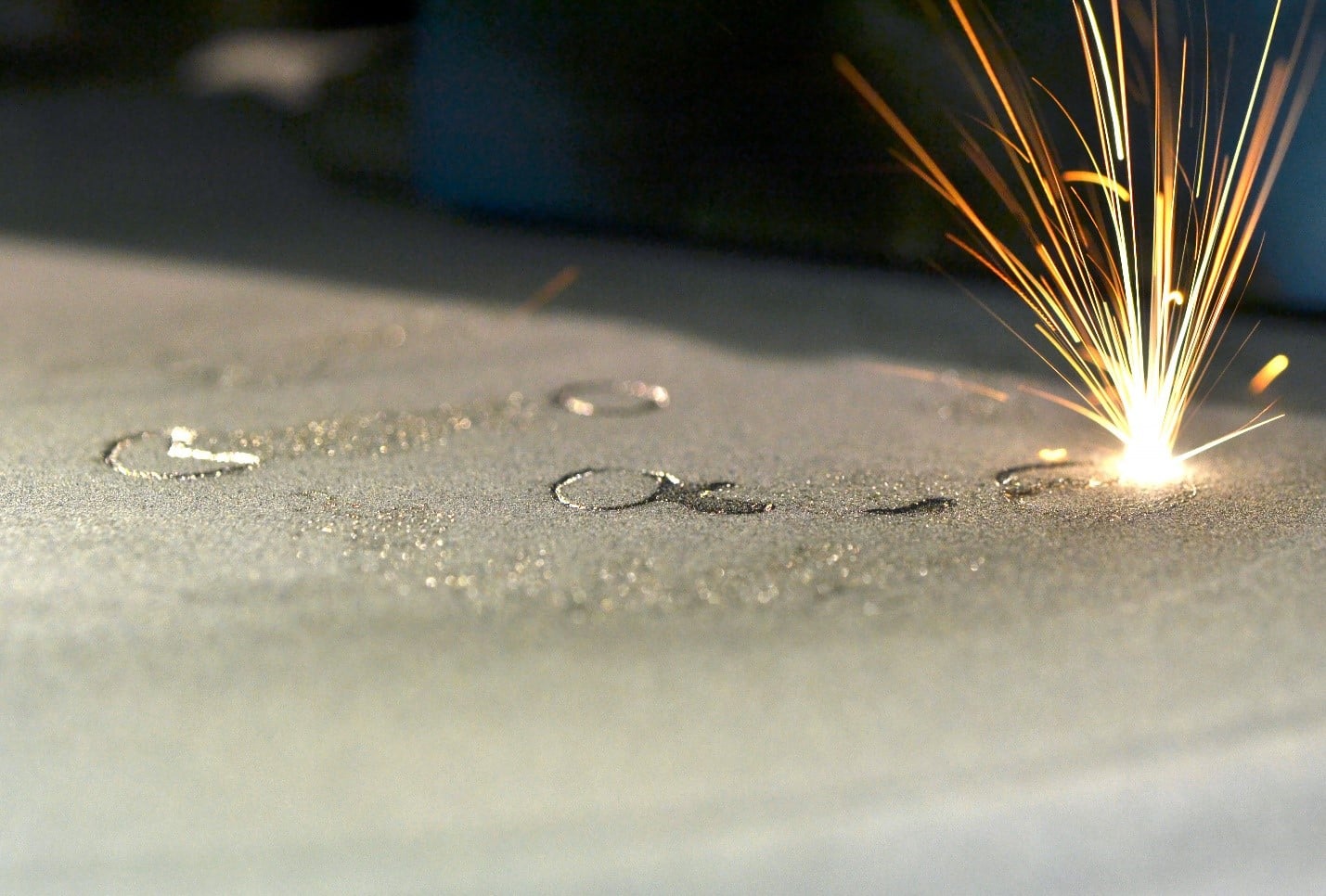
Advantages of SLS 3D Printing Metal
With mechanical properties similar to injection-molded products, SLS 3D-printed metal is the preferred process for functional metal prototyping and final end-use products.
The list of advantages of SLS 3D Printing Metal includes:
- Accurate
- Complex Geometries
- Dimensionally Accurate
- Fast
- High Productivity
- Lightweight
- Low Cost per Part
- Replaces many Metal Applications
- Strong
Benefits of SLS 3D Printing Metal
SLS ABS printing has many benefits besides replacing many much heavier metal products. It is among the most rapid 3D printing technologies for manufacturing highly detailed, durable, and functional products. The strong, lightweight, and affordable products make SLS-printed metals the preferred choice for quick prototyping and production.
Batch printing is quick and easy, and multiple parts can be printed simultaneously when tightly arranged. The printed products do not require support structures and can accommodate complex geometries, including undercuts, interlocking segments, living hinges, and thin walls.
SLS printed materials are used for jigs, fixtures, tooling, patterns for castings, and final commercial-use products. The materials are conducive to many post-processing operations, including vibratory tumbling, electroplating, ceramic coating, painting, powder-coating, dying, and liquid polymer coating.
Technological advances, machinery, materials, and software have made SLS printing more accessible. Tools that were once limited to large, high-tech industries are flexible and reasonably priced alternatives to traditional metal manufacturing methods.
Get multiple quotes for your parts in seconds