Reducing 3D Printing cost
Discover how to reduce 3D Printing cost
Introduction: Reducing 3D Printing cost
The rise of additive manufacturing in 3D printing has introduced an unparalleled level of rapid prototyping, manufacturing, and material/design testing down to the footprint that can fit on a small desk. There are numerous methods and technologies in the 3D printing space, and as a whole, it is a 13.7 billion USD market in 2020, expected to grow at a CAGR of 29.48% to a value of 63.46 billion USD in 2026. There are different methods of technologies within the spectrum of 3D printing, all sharing the ability to manufacture parts layer by layer within hours. Fused deposition modeling (FDM) is the most popular and easiest access technology where a nozzle deposits and builds designs from the bottom up - 67% of firms with access to 3D printing use FDM. Stereolithography (SLA) and Digital Light Processing (DLP) are more precise technologies that use a laser UV diode to cure resin, or in the case of DLP, flash images of cross-sections. The most sought-after, and fastest-growing technology is Selective Laser Sintering (SLS), which fuses nylon power in full-fledged designs.
How can 3d printing help you save money?
3D printing’s major advantage for low-cost and independent manufacturing is its affordable ease of access, simplified workflow, and cost reduction compared to more traditional manufacturing methods. The footprint required to set up and operate 3D printing equipment saves a massive amount of money, allowing for new talent to enter the manufacturing space without inflexible machinery and shop floors. Set-up for 3D printing requires minimal calibration and minimal maintenance through its life cycle. One printer can print a wide-ranging multitude of uploaded files, typically only needing part removal and slight clean-up between prints. 3D CAD software like Dassault’s SOLIDWORKS makes the process even easier by allowing end-to-end integration of designing, analyzing elements, evaluating, and printing a fully-fledged product from the same program, within a matter of hours. The flexibility of in-house printing of parts and designs for testing and manufacturing saves invaluable time and resources versus outsourcing to more traditional manufacturing methods.
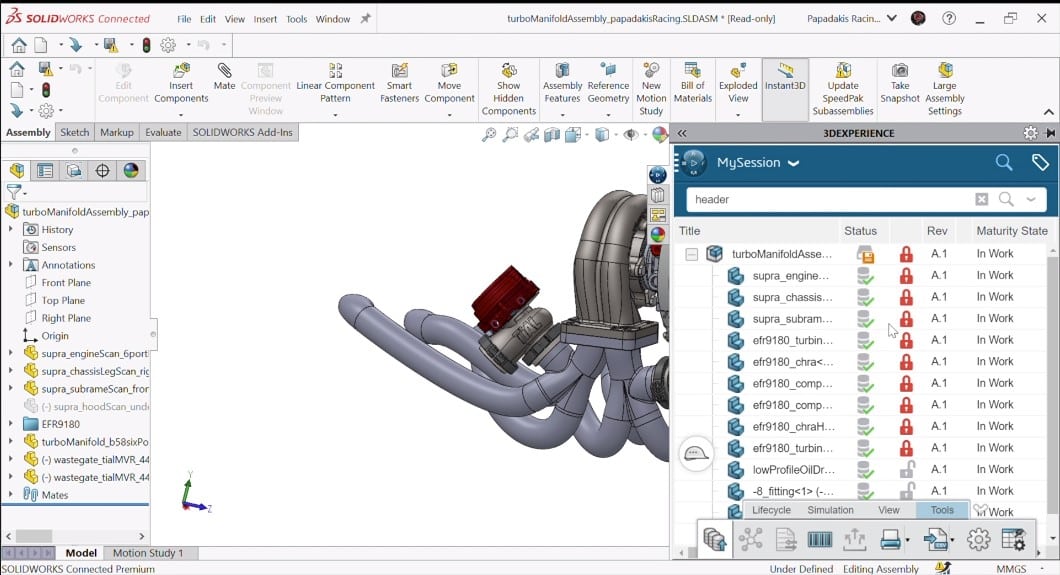
The size of your part, scaling down
The main criteria in impacting the cost of 3D printing is reducing filament or material use. Additive manufacturing through 3D printing is not intensive in energy usage compared to other methods, especially FDM printers which do not require post-process curing. Most printers work with a variety of materials, most commonly plastic polymers, nylon compounds, ceramics, and even metal alloys, including steel, aluminum, and copper. Most plastic and resin printers require the use of supports to assist in the bonding and structural stability during the printing process, and up to a third of the total material could be wasted in printing support material.
Changing the orientation of parts where the flatter/larger surface area of a design is on the heating bed or surface plate increases printing strength and reduces the number of supports needed. Monitoring a print to make sure it does not fail halfway through because of a bonding failure at a support point is also crucial - failed prints result in lost material. Additionally, certain support designs use fewer materials than others, such as “tree” supports. Simpler and some organic designs require little to no support at all, consulting other designers through Dassault’s network on 3DEXPERIENCE can assist in analyzing structural support.
In the case of most metal and nylon 3D printers that rely on laser sintering like SLS printing, the material is manufactured out of a powder, rather than filament or resin. This does not require supports like FDM, SLA, and DLP printers, however, the cleanup process requires brushing and removal of material products as if one were excavating an artifact. This is a more intensive post-process which also requires curing, however unused material powder can be reused on the next print, depending on the recycling rate. Because of this, SLS printing makes it possible to manufacture multiple high-quality parts in one print session without supports, changing filament, and constant monitoring.
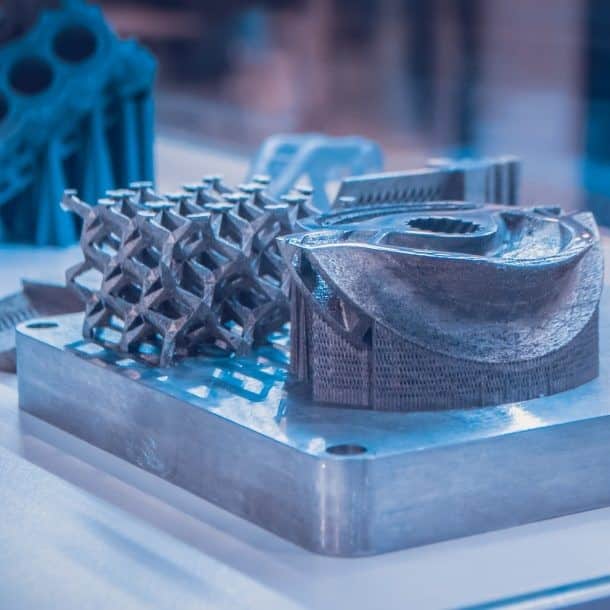
Hollowing out your 3D model to reduce 3D printing cost
Some printers are capable of printing products down to micrometers; while that may not be a necessity, it is possible to scale down full designs to test the effects of general design parameters depending on the size of the nozzle or print pattern. Aerodynamics of aerospace and automotive bodies, the tensile strength of limbs, and other factors can be tested scaled-down rather quickly than custom manufacturing and clay modeling. 3D printing can also accommodate full-scale manufacturing in more common FDM printers like their more expensive SLS counterparts, and some FDM printers can be oriented to run prints on a conveyor belt print bed to balance out the single part printing quality and batch production.
Support, optimizing the need for support
Previously mentioned was the need to optimize supports as a factor to reduce material waste. The surface area of the product itself is known as the shell and can be several layers thick, inside of that is the in-fill. Having the in-fill set at 100% sets the entirety of an object to be filled with material. This takes an extraordinary amount of time, and material without necessarily creating a stronger product as the laser or nozzle must set material across every area of a cross-section throughout every layer. More effective in-fill patterns can be selected, with certain cross-hatching patterns and geometry being able to not only increase the strength of a material but vastly reduce the amount of in-fill. In-fill is set lower for quickly prototyping general ideas or fitment and set higher for production parts and products.
Most of the 3D Printing cost reduction is accomplished in the CAD stages, where various points of failure, and material waste can be avoided in the design and analysis. It is wise to not only prepare correctly but also consult others for assistance in the process.
Get multiple quotes for your parts in seconds