Plastic Injection Molding
Plastic injection molding is a common manufacturing process that is desirable for many parts production projects because of its low cost and wide-ranging selection of materials.
What is Plastic Injection Molding?
Plastic injection molding is a manufacturing method utilized for high volume production of identical plastic parts. In this plastic injection process, molten plastic is inserted into a mold to produce a component in the form of the mold cavity. Plastic injection molding is often used to meet the following criteria:
- When large quantities of components need to be manufactured fast
- When cost per part must be kept to a minimum
- When all parts being produced have the same design
Plastic injection molding is extremely cost effective at high production volumes—usually volumes of thousands to hundreds of thousands of components. An additional benefit of plastic injection molding is that it can be done using a wide range of materials and colors, which gives product designers more freedom in their designs.
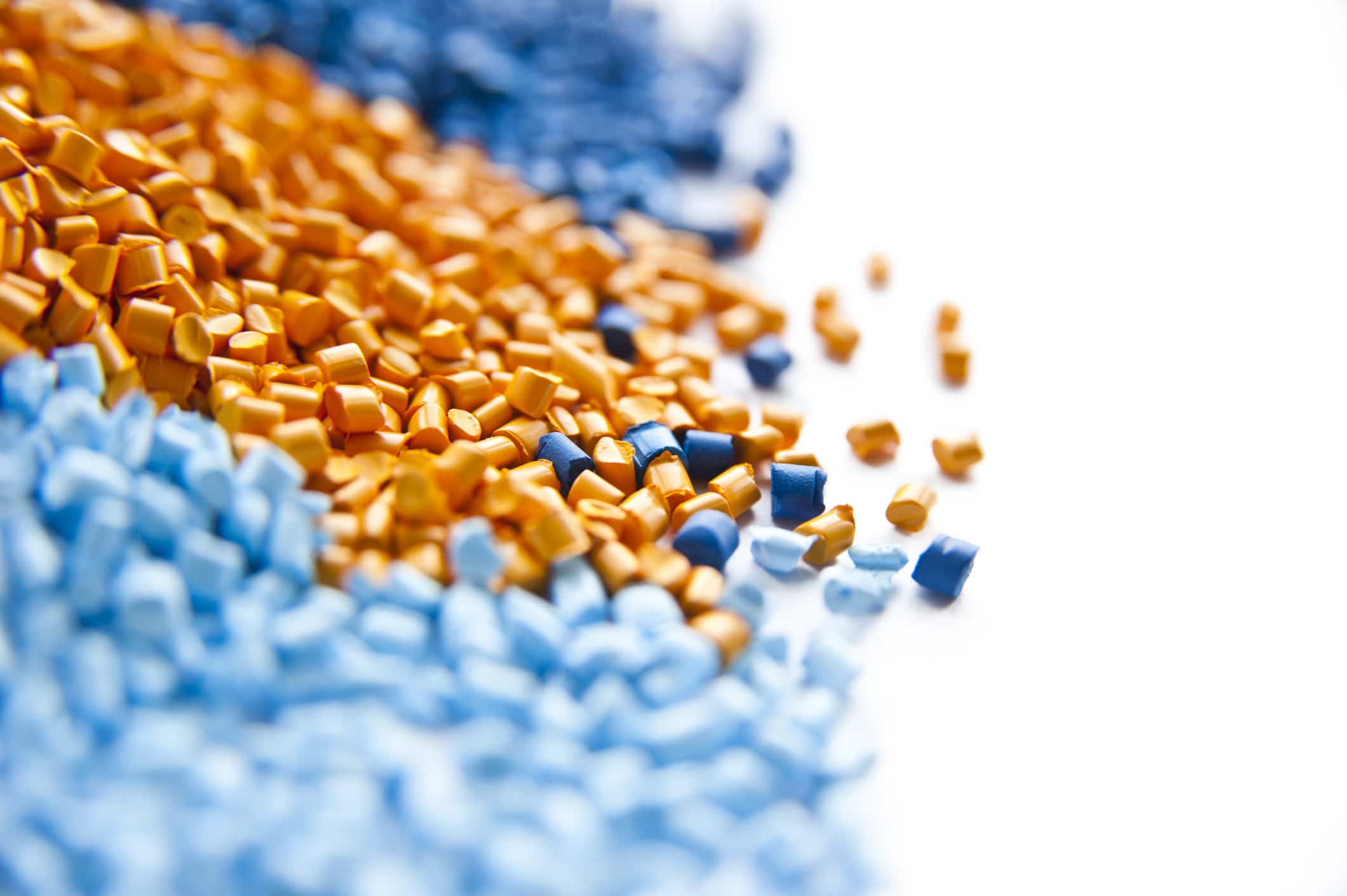
What Products are Made from Plastic Injection Molding?
Plastic injection molding is a highly effective manufacturing process for products in many different industries. Here are some of the most common examples:
- Consumer products such as storage containers are often manufactured with injection molding using durable, low-cost plastics such as PVC.
- Aerospace parts such as pump gears, turbine blades, and valve seats can be made with injection molding using engineering plastics such as PAI and PEEK because these plastics can withstand extreme temperatures experienced by airplanes.
- Electronics parts such as connectors and wire cables are often made with overmolding using static dissipation plastics such as ABS blends.
- Parts used in medical devices, monitor support arms, infusion pumps, and more are made with injection molding using plastics such as PEEK, polycarbonate, and polystyrene because they can be easily sterilized and they don’t absorb moisture.
- Injection molding can be utilized to make parts in the energy industry such as insert molded valves, seals, pipe liners, and more with heat resistant plastics such as PEEK and PTFE.
- Injection molding is often used in the automotive industry to make parts such as door panels, engine components, and much more. Common materials used for these parts include glass-filled nylon, PBT, PPE-PS, and polyether imide.
What is the Plastic Injection Molding Process?
The plastic injection molding process injects molten plastic into a mold, which subsequently cools and solidifies into a part. There are four basic steps in the injection molding process:
- Clamping - The halves of the metal mold are held together tightly using clamps so that it can withstand the pressure from injecting the molten plastic material.
- Injection – Resin pellets are heated to a molten state and injected into the mold. After most of the plastic is injected, packing and holding applies pressure to cause the plastic to fill all parts of the mold.
- Cooling – When injection is completed, the molten plastic cools and forms a solid part.
- Ejection – After cooling is completed, the solid plastic part is ejected and the process repeats.
How a Plastic Injection Molding Machine Works
Plastic injection molding machines are made up of three main parts, which are the injection unit, the mold, and the clamping/ejector unit. The injection mold tool itself contains the sprue and runner system, the gates, two halves of the mold cavity, and optional side actions.
Mold Cavity
Mold cavities have an A side and B side. The B side—also known as the “core”—is usually the non-cosmetic, interior side that has the ejection pins used to push the finished part out of the mold. The A side—also known as the “cavity”—is the other side of the mold that gets filled with molten plastic. Mold cavities contain vents that enable hot air to dissipate so the parts don’t overheat.
Runner System
The runner system channels the molten plastic from the screw feed to the cavity. For cold runner molds, the plastic solidifies in the runner system and the part cavities. This means that the runners are ejected with the parts. Many cold runner systems will automatically eject the part and runners separately via a three-plate mold. With a three-plate mold, the runner is separated using an extra plate between the injection point and the part gate. By contrast, hot runner molds don’t create runners attached to the part since the feed material is maintained in a molten state up to the part gate. Hot runner systems are advantageous because they decrease waste and improve molding control.
Sprues
Sprues channel the molten plastic from the nozzle. Sprues intersect with a runner, which leads to the gate where the molten plastic enters the cavities. The sprue channel has a larger diameter than the runner channel, which allows a sufficient amount of material to pass from the injection unit.
Gates
A gate is a small opening that enables molten plastic to enter the mold cavity. You can usually see the gates on the molded part because they appear as a small rough patch or depression called a gate vestige.
Parting Line
The parting line of an injection molded plastic part is seen where the halves of the mold close together for injection. It’s a thin line of plastic that covers the outside diameter of the part.
Side Actions
Side actions consist of inserts placed in molds that cause the material to flow around them to create undercut features. It’s important to remember that side actions must be designed to allow for proper ejection of the part.
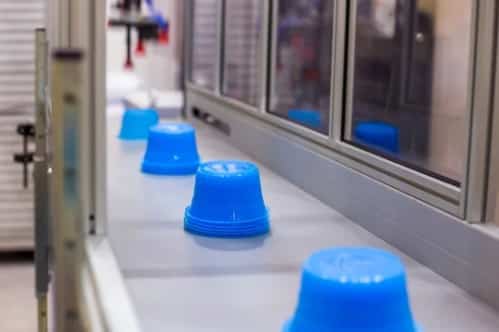
What Plastic is Used for Injection Molding?
There are three types of plastic that are most commonly used in injection molding because of their low cost and durability: polycarbonate, polypropylene, and nylon. Let’s take a closer look at these three plastics, as well as others used in injection molding.
- Polycarbonate (PC) is resistant to chemicals and abrasions and has very high impact strength.
- Polypropylene (PP) is a durable plastic that is extremely moisture and chemical resistant. It’s also safe for foods and an effective electrical insulator.
- Polyamide (nylon) is desirable because of its durability, high melting point, thermal resistance, and chemical resistance.
- Acrylonitrile butadiene styrene (ABS) is durable and scratch resistant. It also offers excellent dimensional stability.
- High-density Polyethylene (HDPE) is durable and also lightweight, which makes it desirable for many applications. Additionally, it offers high tensile strength, good chemical resistance, and excellent electrical insulation.
- PC-ABS is a blend of ABS and PC, which offers toughness and heat resistance. Additionally, it offers good dimensional stability.
- Additional plastics used in injection molding include polystyrene (PS), SAN, PVC, PET, PBT, PEI, PPS, PMMA, TPU, and TPE.
Get multiple quotes for your parts in seconds