How to Select the Right CNC Material
When designing your next prototype or part, it’s important to know how to select the right CNC material.
Introduction How to select the right CNC Material
CNC machining employs a wide variety of metal and plastic material. While it’s nice to have many different material options, trying to determine which one is best for your unique part or prototype can be a bit daunting.
In today’s article, we take a closer look at the most common CNC materials, what their basic properties are, and the most common kinds of uses for these materials in CNC machining.
Overview of the CNC Materials Selection Process
Step 1
Determine your material requirements. Some of the most common types of requirements include thermal, surface finish, mechanical, and cost. It’s also very important that you factor in what environment your part will function in, as well as any other parts it will need to work with.
Step 2
Make a short list of the most desirable materials for your part or prototype. You can make this list by identifying the materials that satisfy most, if not all, of your requirements from Step 1.
Step 3
It’s time to make your decision of which CNC material is right for your application. In some cases, you may need to forgo one or more of your preferences in order to choose the material that is the best fit from an overall perspective.
Helpful Guidelines for CNC Material Selection
When approaching the CNC material selection process, there are some basic guidelines to keep in mind. Parts requiring more hardness, strength, and thermal resistance use metals. Plastics, on the other hand, are lighter weight and they have a lot of variances when it comes to physical properties. Most often, plastic CNC material is preferred when it comes to electrical insulation and chemical resistance.
By far, Aluminum 6061 is the most commonly employed CNC machining material, and it comes at an affordable cost compared to other metals. From a plastics perspective, POM (Delrin) is the most affordable and it offers great machinability. For engineers who place a high priority on hardness, strength, and temperature resistance, metal alloys may be your best option.
Common CNC Metal Alloys
Aluminum Alloys
Aluminum alloys have great machinability and are very affordable compared to other metals. For these reasons, aluminum alloys are great for prototyping and part production. It’s also helpful to note that aluminum alloys have a high level of electrical and thermal conductivity. Aluminum alloys have a desirable strength-to-weight ratio and also offer corrosion resistance. While aluminum alloys are weaker and not as hard as steel, anodization can be applied to give the aluminum a hard surface layer.
Here are some aluminum alloys for CNC material:
- Aluminum 6061 is a versatile aluminum alloy that offers great machinability and a desirable strength-to-weight ratio.
- Aluminum 6082 is quite similar to aluminum 6061. The main difference is that it’s used more in Europe because it meets British Standards.
- Aluminum 7075 is a great CNC material for aerospace parts that need to be lightweight. Plus, it can be heat treated to increase its hardness and strength.
- Aluminum 5083 is stronger than most other aluminum alloys and it also offers resistance to saltwater. Use 5083 for parts in marine, welding, and construction applications.
Stainless Steel
Stainless steel alloys—depending on their specific compositions—can be magnetic or non-magnetic. These alloys offer high degrees of ductility, strength, and corrosion resistance. Moreover, stainless steel alloys have great machinability. They can also be welded and polished.
Here are some stainless steel alloys for CNC material:
- Stainless steel 304 is the most common stainless steel alloy utilized in CNC machining. It offers good machinability and is also corrosion resistant. Additionally, it offers excellent mechanical properties.
- Stainless steel 316 has similar mechanical properties to Stainless steel 304. However, it offers more corrosion resistance compared to 304, especially in marine applications due to the presence of salt water.
- Duplex 2205 stainless steel offers the highest amount of strength of any of the stainless steel alloys. As a result of its high strength, employ it in applications involving high levels of tension and force. In addition to its superior strength, Duplex 2205 also provides strong corrosion resistance.
- Stainless steel 303 doesn’t offer as much corrosion resistance as 304, but it’s still very tough. It also offers great machinability and is commonly utilized for high-volume production.
- Stainless steel 17-4 (SAE grade 630) provides similar mechanical properties as 304. An interesting fact about 17-4 is that it can be precipitation hardened so that it’s similar to tool steels. 17-4 also offers great chemical resistance, which makes it ideal for high-performance parts.
Mild Steel
Low-carbon steels—commonly called “mild steels”—provide excellent machinability, as well as good mechanical and weldability properties. Mild steels are also very affordable. However, it’s important to understand that mild steels are vulnerable to damage from chemicals and corrosion.
Here are some mild steels for CNC material:
- Mild steel 1018 is an alloy that offers high amounts of hardness, durability, and strength. 1018 is also very machinable and weldable. For these reasons, 1018 is the most frequently employed mild steel alloy in CNC machining.
- Mild steel 1045 is considered a medium carbon steel. 1045 is strong and resistant to impact. It also offers good machinability and weldability.
- Mild steel A36 for construction applications because of its desirable structural properties and weldability.
Alloy Steel
Alloy steels are noteworthy because they have more alloying elements besides carbon. These additional elements increase the durability and hardness of the alloy. It’s also important to be aware that alloy steels are not chemical or corrosion resistant.
Here are some alloy steels that are used as CNC material:
- Alloy steel 4140 offers sound mechanical properties evidenced by its durability and strength. 4140 is useful for a wide variety of applications except for those requiring welding.
- Alloy steel 4340, on the other hand, is weldable. Moreover, it can be heat treated making it even harder and stronger, yet still remaining durable. This alloy is weldable.
Tool Steel
Tool steels are some of the toughest metal alloys available for CNC machining. These steels offer superior hardness, as well as thermal and abrasion resistance. Specifically, as the name implies, tool steels are used for CNC machining manufacturing tools such as molds, dies, and stamps. In order to become hard and durable, tool steels must be heat treated.
Here are some tool steels for CNC material:
- Tool steel D2 can maintain hardness up to 425°C. D2 is often used for CNC machining dies and cutting tools.
- Tool steel A2 is frequently utilized for CNC machining injection molding dies. A2 offers toughness and dimensional stability at high temperatures through air hardening.
- Tool steel O1 is frequently used for CNC machining knives and cutting tools because of its hardness (65 HRC), which achieved through oil-hardening.
Brass
Brass is an alloy that offers great electrical conductivity. Brass is a potential CNC material option for applications that need to be smooth and have a low amount of friction. Brass C36000 is a specific alloy offering lots of tensile strength and it is also very machinable, which makes it a candidate for high volume production.
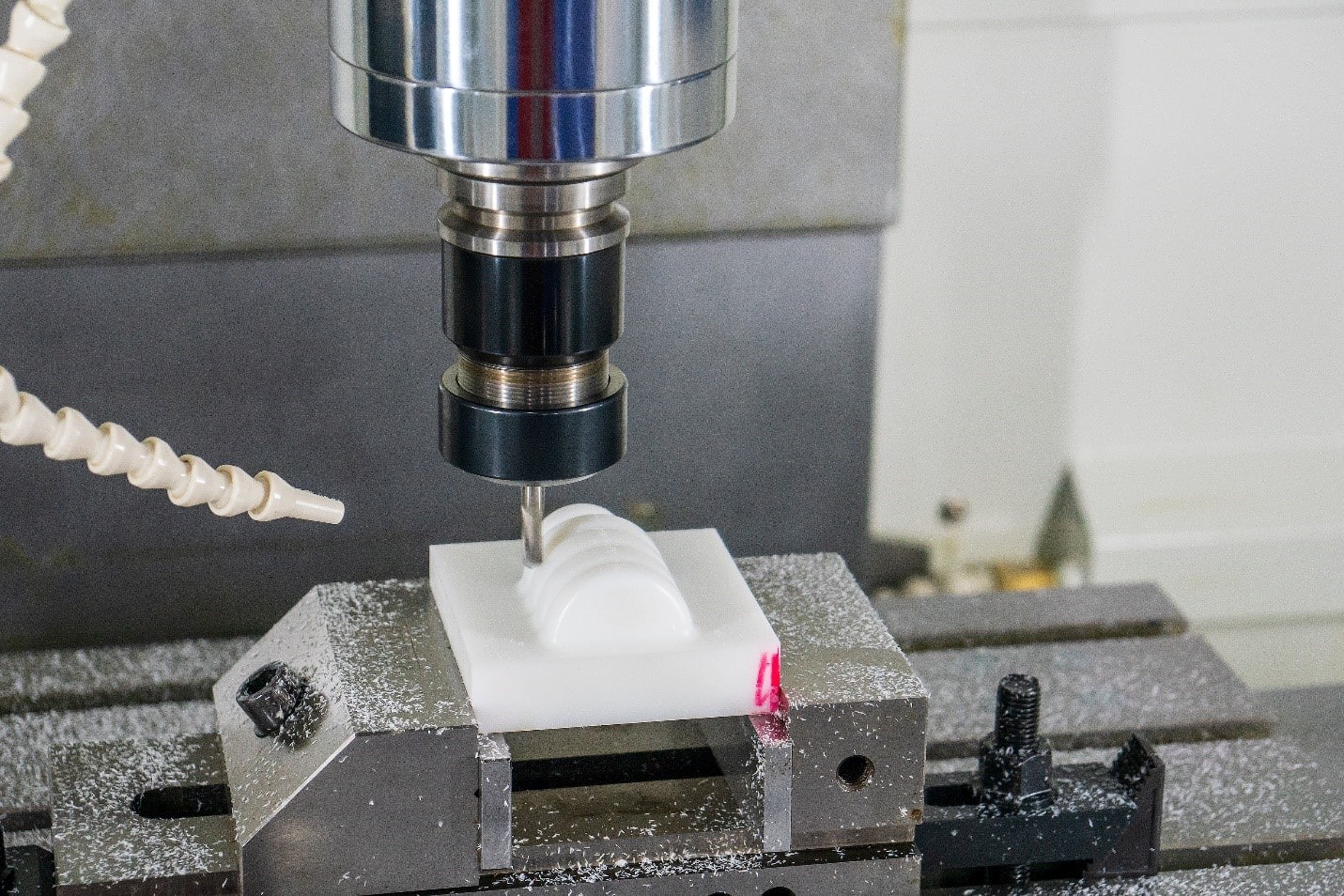
Common CNC Plastics
ABS
ABS is a thermoplastic material that is frequently CNC machined because it has great strength, high heat resistance, and good machinability. ABS is also light weight, which can be useful for weight-sensitive applications. Another common use of ABS material is to CNC machine prototypes before production with injection molding.
Nylon
Polyamide—commonly called nylon—is a thermoplastic with decent strength, great mechanical properties, and high resistance to abrasion and chemicals. One notable aspect of nylon is that it can absorb water. The nylon material frequently used in CNC machining is nylon 6 and nylon 66.
Polycarbonate
Polycarbonate is a very durable thermoplastic that provides good machinability. It’s notable for having superior impact strength compared to ABS.
POM (Delrin)
POM—also called by its marketed name Delrin—offers the most machinability of any thermoplastic. For this reason, POM is a great option for precision CNC machining parts. POM is very stiff and provides great dimensional stability at higher temperatures. POM also has low friction and low water absorption.
PTFE (Teflon)
PTFE--commonly called Teflon—has the lowest friction coefficient of any known solid. It can also maintain operations in temperatures higher than 200°C and is a great electrical insulator.
HDPE
HDPE stands for high-density polyethylene. HDPE provides good water resistance and a high strength-to-weight ratio. As a lightweight thermoplastic, HDPE is great for piping. Additionally, similar to ABS, HDPE is frequently used to create prototypes before production with injection molding.
PEEK
PEEK is a thermoplastic that provides amazing thermal stability across varying temperatures. It is also resistant to most chemicals. Having great mechanical properties, PEEK material can replace metal material in some part applications because of its high strength-to-weight ratio.
Get multiple quotes for your parts in seconds