FDM ABS 3D Printing
FDM ABS 3D printing is one of the most common 3D printing processes. It is used in a wide variety of applications. Learn more now!
Introduction to FDM ABS 3D printing
Fused Deposition Modeling (FDM) 3D printing began in the early 1990s. FDM was the third significant 3D printing technology to be developed. Today, it’s one of the most widely used 3D printing processes. Over the years, as FDM technology evolved, so did printing materials. Acrylonitrile butadiene styrene (ABS) was one of the first materials to be utilized in 3D printing. In fact, ABS was already in use in traditional manufacturing processes such as CNC machining, so it was no surprise that ABS was adopted into FDM 3D printing. Fused Deposition Modeling (FDM) 3D printing began in the early 1990s. FDM was the third significant 3D printing technology to be developed. Today, it’s one of the most widely used 3D printing processes. Over the years, as FDM technology evolved, so did printing materials. Acrylonitrile butadiene styrene (ABS) was one of the first materials to be utilized in 3D printing. In fact, ABS was already in use in traditional manufacturing processes such as CNC machining, so it was no surprise that ABS was adopted into FDM 3D printing.
What is ABS?
ABS is one of the most common thermoplastic polymers. ABS plastic has good impact strength and is lightweight. It’s also chemical and abrasion resistant. These properties, combined with its affordability, make ABS one of the most desirable 3D printing materials. It’s important to keep in mind that ABS plastic has a low melting point, which means it’s not recommended for applications involving extremely high temperatures.
What is FDM 3D Printing?
FDM 3D printing (sometimes called fused filament fabrication (FFF)) is an additive manufacturing method that uses material extrusion. FDM 3D printing creates parts layer by layer by depositing material in a programmed path. FDM 3D printing utilizes thermoplastic polymers in the form of filaments.
FDM 3D printers use digital design files that are programmed into the printer and subsequently translated into precise 3D printing dimensions. FDM 3D printing typically uses polymer materials including ABS. The first step in the FDM 3D printing process is to load the spool of ABS thermoplastic filament into the printer. When the nozzle is heated, the FDM 3D printer feeds the ABS filament through an extrusion head and nozzle. The extrusion head can move across the X, Y, and Z axes. The FDM 3D printer extrudes melted ABS material in thin strands and deposits them layer by layer along a pre-programmed path specified by the design inputs. After the ABS is deposited, it cools and forms a solid. Additionally, fans can be attached to the extrusion head to speed up the cooling process.
To completely fill an area of your part, multiple passes by the FDM 3D printer extrusion head are required. Once the FDM 3D printer completes a layer, the build platform is automatically lowered, and the printer starts printing the next layer. Additionally, there are some FDM 3D printers where the extrusion head moves up as each layer is completed rather than the build platform descending.
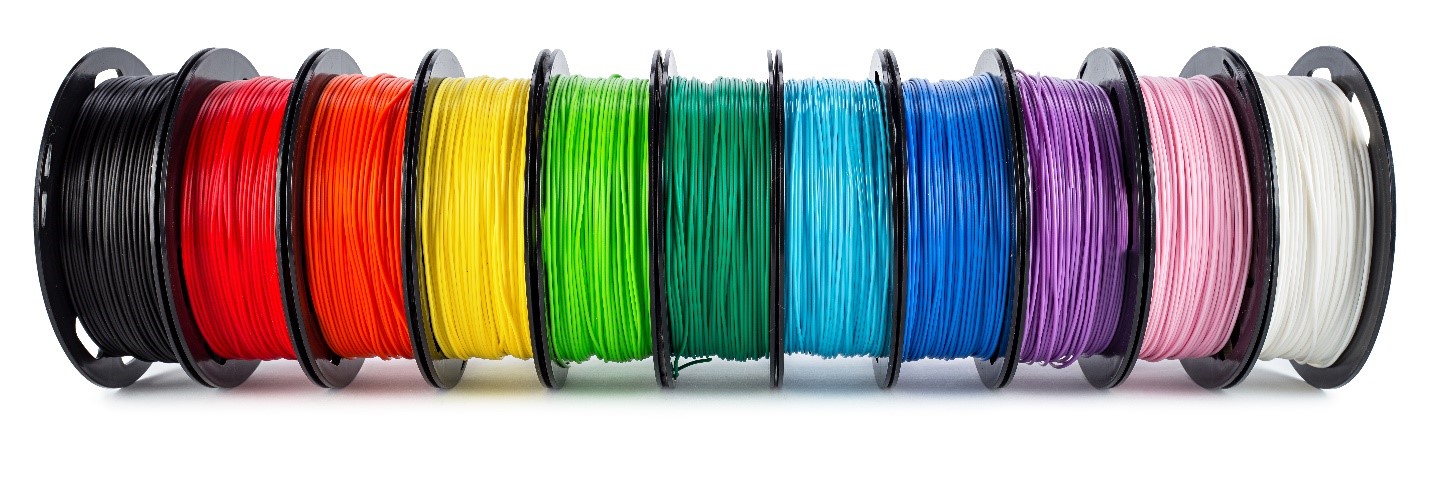
Applications of FDM ABS 3D Printing
ABS material offers a high degree of machinability, which makes it a great option for mass production of a wide variety of consumer products. Moreover, FDM ABS 3D printing is also used in automotive applications and kitchen appliances because of its chemical resistance and high impact strength. Additionally, as a result of its electrical insulation properties, FDM 3D printing with ABS material can be useful for applications involving the casing of electrical components. The end result is a wide variety of applications including automobile dashboards and bumpers, protective equipment like headgear, kitchen appliance housings, and even Lego bricks and toys. Additionally, FDM ABS 3D printing is a potential option for creating affordable prototypes such as medical prosthetics and architectural models.
The Benefits of FDM ABS 3D Printing
ABS thermoplastic material has many benefits and desirable properties. ABS is strong and durable. It’s also an excellent electrical insulator. FDM ABS 3D printing is also one of the more affordable 3D printing processes both in terms of the ABS material and the FDM 3D printers themselves.
As a result of these beneficial factors, ABS polymer material and FDM 3D printing make for an ideal additive manufacturing solution for many different parts. Moreover, FDM 3D printed parts using ABS provide chemical resistance in a variety of applications. Additionally, the cosmetic appearance of ABS material can be easily customized during post-processing.
Get multiple quotes for your parts in seconds