DMLS vs. EBM: Differences and Comparison
A comparison of DMLS vs. EBM Powder Bed 3D printing technologies. Learn more now!
Introduction
3D printing includes a variety of different technologies and material types to produce a 3D printed part. Powdered materials are used instead of filament with several printing methods. Direct Metal Laser Sintering (DMLS) is one of the more popular technologies compared to Electron Beam Melting (EBM),
but there are several similarities. The differences are the powder melting process.
DMLS uses a high-powered fiber laser to melt metal powder, layer by layer, to build 3D objects. EBMs use an electron particle beam called electron beam melting (EBM) to melt the powder to produce parts. An electron gun generates the electron beam directed across the powder bed at high speed. The heat from the electron beam melts the powder, forming a solid layer.
Other 3D printing technologies that use powder material to produce parts include the following:
- Selective Laser Sintering (SLS)
- Selective Laser Melting (SLM)
- Binder Jetting
- Multi Jet Fusion (MJF)
- PolyJet 3D Printing
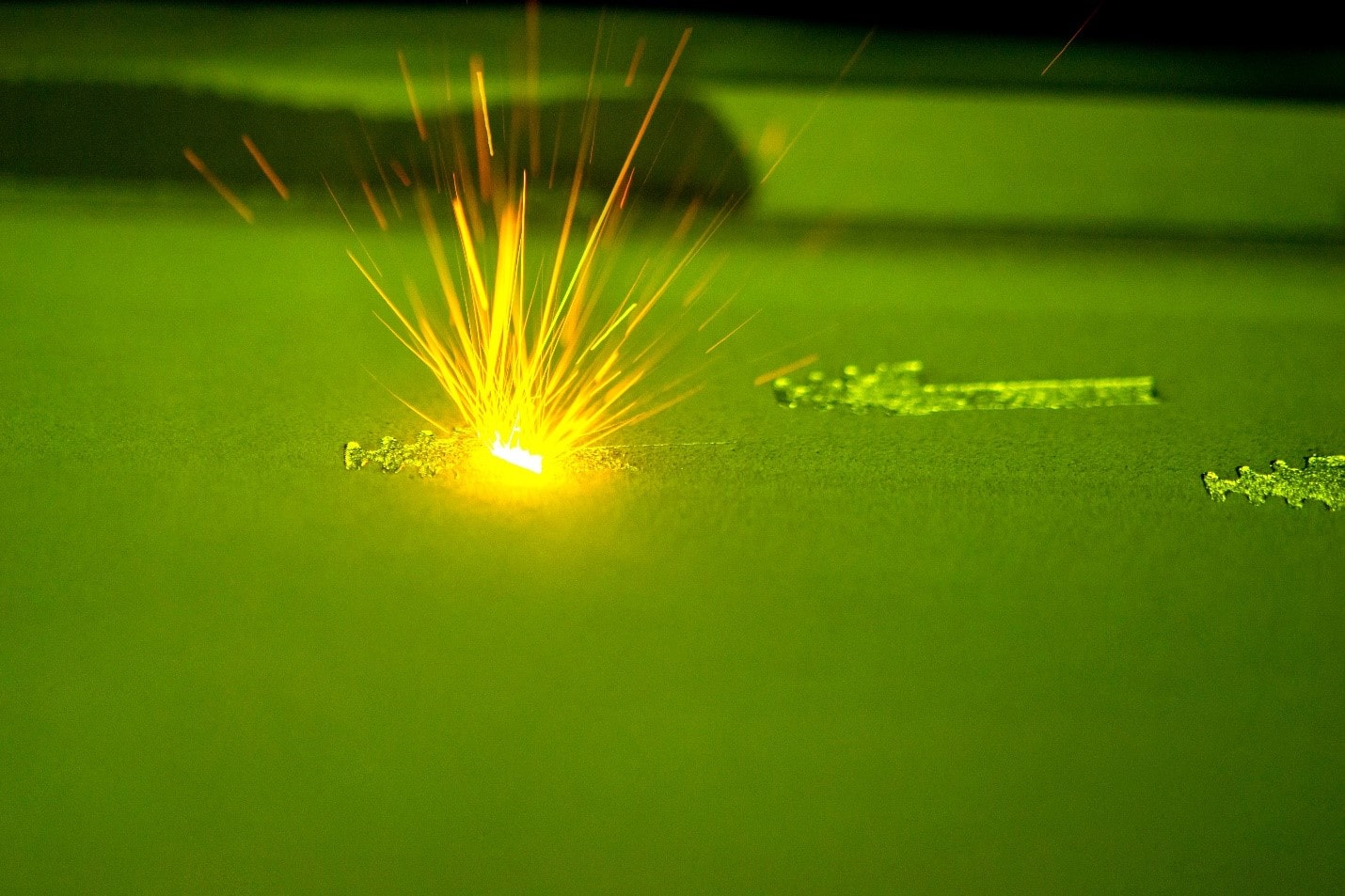
DMLS Definition and Comparison to EBM
Direct Metal Laser Sintering (DMLS) is a 3D printing technology that utilizes a powder bed and a laser to manufacture metal products, including rapid prototyping and mass production. These parts are produced from a three-dimensional Computer Aided Design (CAD) drawing converted to print each product layer. Limited to metal alloy powders and metal derivatives, DMLS sinters the powders (not melt) with a fiber laser to create each product layer. Sintering heats the powder particles into an excited state to weld the particles together. The parts are more porous due to sintering, allowing plastics can even be combined with metals.
The DMLS build chamber has an inert gas to prevent oxidation while printing the product. An EBM printer prevents oxidation with a vacuum chamber. Added supports are necessary to restrict product distortion. The various applications for DMLS include aerospace, medical, dental, jewelry, jewelry, and prototypes.
DMLS 3D printing characteristics:
- Direct material printing and printing of mixed powders
- Wide selection of materials
- Good surface finish
- Metal powder that is not sintered can be reused
- Reasonably strong parts
- Porosity issues
- Small build volumes
- Expensive equipment
The advantages of DMLS vs. EDM include the following:
- High-resolution printing
- Larger material selection
The disadvantages of DMLS vs. EBM are listed below:
- DMLS parts have porosity, which can be controlled but not eliminated
- DMLS cannot print materials or product designs with high melting points
- DMLS parts incur internal stress while the EBM relieves stress with its higher temperature environment
EBM Definition and Comparison to DMLS
Electron Beam Melting (EBM) is an additive manufacturing 3D printing process that uses powder bed fusion to print products. Powdered metal is melted by a high-energy electron beam that produces an electron stream. A magnetic field guides the electron stream to develop parts in a layer-by-layer process using the three-dimensional product drawing. The EBM process is contained in a vacuum chamber to protect the process from oxidation of the prone metal materials. The build chamber can be heated to 1,000°C and higher.
The difference from DMLS is that EBM utilizes a powerful electron beam to melt the material, while DMLS uses a laser. The electron beam disperses more energy than the laser and can move at higher speeds. The beam can be split and melt several areas simultaneously. As such, the beam can pre-heat each layer prior to melting and produce a stronger, high-density end product. Although new materials are being developed for EBM, the uniqueness of this process makes EBMs material selection limited to conductive materials and alloys. In addition, since EBM parts are stronger, fewer supports are required during printing.
The commercially available materials for use in EBM include:
- Cobalt chrome
- Copper
- Nickel alloy
- Stainless steel
- Tantalum and titanium tantalum alloy
- Tool steel
- Titanium and titanium alloys
EBM products have superior mechanical properties, which makes them ideal for aerospace, automotive, defense, medical, and petrochemical industries. Plus, the process has a high degree of sustainability, with 95%-98% of the unused powder being recycled.
EBM 3D Printing Characteristics:
- High-density parts
- Few supports required
- Excellent mechanical properties
- Heat treatment is seldom required
- Up to 98% recycling of unused powder
- Typically fast part processing
- Limited material selection (only conductive materials and alloys)
- Expensive machines and materials
- Requires post-processing to negate poor surface finish
- Extensive post-printing cooling down period.
- Limited to smaller parts
The advantages of EBM compared to DMLS include the following:
- EBM is faster by spreading its powerful beam to multiple locations and pre-heating each layer
- EBM can process much high melt-temperatures
The disadvantages of EBM vs. to DMLS include the following:
- EBM can only print conductive metals
- EDM must print in a vacuum chamber
- Limited material selection
- More expensive equipment
What Are the Mutual Alternatives to DMLS and EBM?
The alternative to DMLS and EBM is Selective Laser Melting (SLM), a similar additive manufacturing technology that uses a laser to melt the metal powder. It also melts the powder layer by layer to produce 3D parts. SLM 3D is often used for medical, aerospace, and automotive applications. SLM also prints in an inert gas environment.
Other technologies comparable to DMLS include Binder Metal Jetting (BMJ). The BMJ technology uses a binder to join metal powder particles for each layer. BMJ does not require supports like DMLS; it prints fast and produces an excellent surface finish. Post-processing is required with BMJ products.
Technologies similar to EBM (in addition to DMLS) include Directed Energy Deposition (DED). DED feeds a metal wire through a heated print nozzle to print. The end product has excellent mechanical characteristics, similar to EBM products.
Summary
To summarize, DMLS and EDM are both powder bed fusion metal 3D printing technologies that utilize a heat source to melt a metal powder. Both require a vacuum chamber and post-print cooling. EBM (Electron Beam Melting) produces highly dense parts but has a poor surface finish. DMLS also makes highly dense parts but has an improved surface finish.
Get multiple quotes for your parts in seconds