The Best Resins for 3D Printing
3D Resin Printing and the Best Resins for 3D Printing. Learn more now!
Introduction
The list of materials used in 3D printing is continually expanding. Resin is a thick, photosensitive liquid material used with 3D resin printing. Liquid resin is a mixture of various chemicals and additives that enhance the resin’s mechanical and chemical properties.
3D printing is making three-dimensional solid objects from a digital file. A 3D-printed object is created using additive processes, where successive layers of material are laid down in different shapes. 3D printing is used in a wide variety of industries, including automotive, aerospace, medical, and consumer products.
This article discusses resin 3D printing and the best resins for the 3D printing industry.
Resin 3D Printers
The four most common resin 3D printers that produce quality parts with liquid-based photosensitive resins include:
- SLA 3D printers – Stereolithography (SLA) printers use a laser to cure liquid resin one layer at a time to create a 3D object. This type of 3D printer is known for its high accuracy and smooth surface finishes.
- DLP 3D printers – A Digital Light Processing (DLP) 3D printer is a type of 3D printer that uses light to harden photopolymers resin to create a three-dimensional object. Instead of slowly layering plastic filament, DLP 3D printers use a digital light projector to project a 3D image onto a vat of resin, hardening the resin layer by layer until the object is complete. This 3D printing is faster than traditional FDM or SLA methods and produces high-quality, detailed prints.
- LCD 3D printers – LCD stands for Liquid Crystal Display, a type of 3D printer that uses liquid crystal displays (LCDs) to expose the UV-sensitive resin to light selectively. This type of printer produces detailed prints with a higher level of accuracy than other types of 3D printing. It is also generally faster than other 3D printing methods.
- MSLA 3D Printers – Masked Stereolithography (MSLA) is a 3D printing process that uses photosensitive resin and ultraviolet light to cure and solidify the resin layer by layer. The masking layer creates intricate details, such as small gaps or thin walls, that would be impossible to create with traditional 3D printing techniques. The printer is built around a vat of liquid resin. The light source is projected through a mask to determine what portions of the resin will be cured into a solid. MSLA 3D printers provide a high degree of accuracy and detail in the printed parts, making them ideal for prototyping and producing complex shapes.
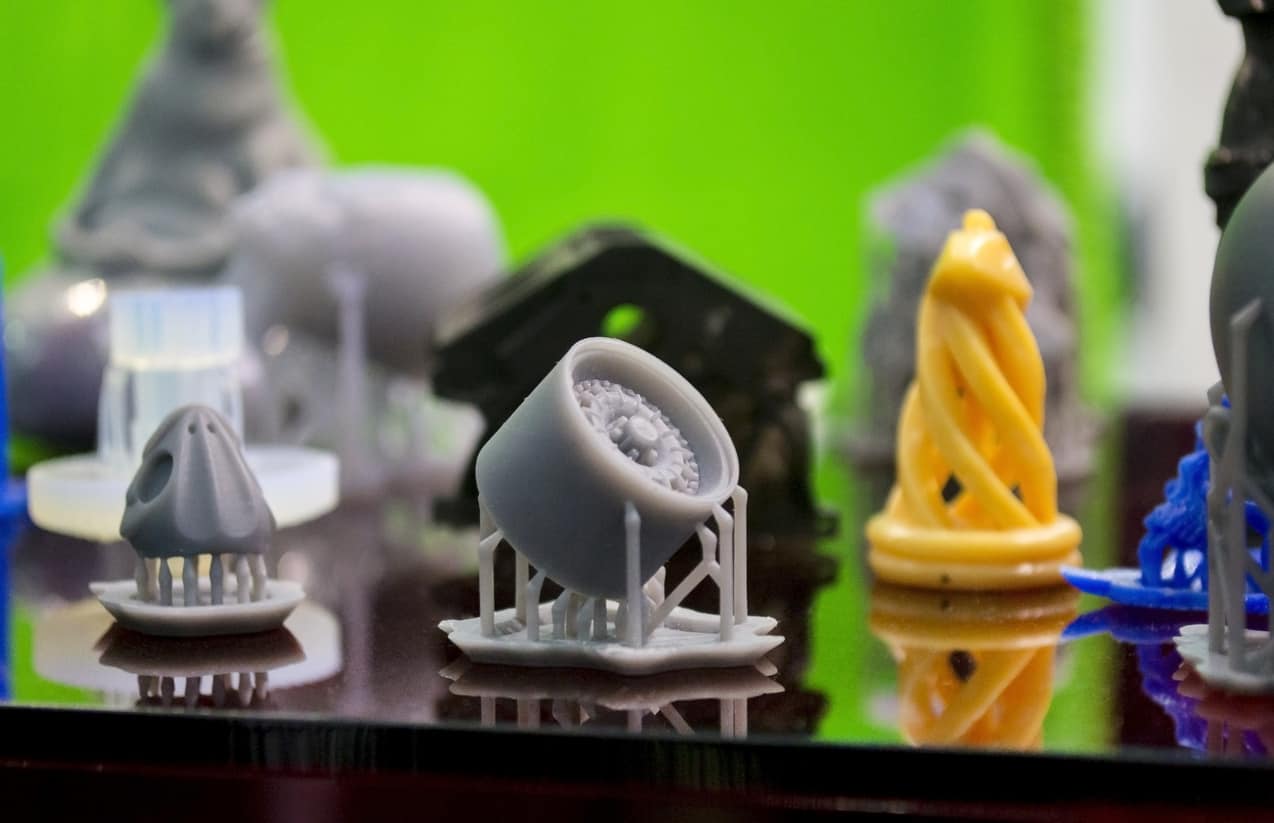
The Best 3D Printing Resins
The best resin types for 3D printing depend on the specific application. Generally, the most popular resin types are ABS, PLA, PETG, nylon, polycarbonate, and resin. Each resin type has unique properties that make it suitable for different applications. Resin performance depends upon the printer in use and the object being printed.
The increase in industrial, commercial, and consumer resin 3D printers has helped the resin industry expand. Standard resins are available for dental, engineering, ceramic, jewelry, and other unique applications. In general, the most popular resins for 3D printing are:
- ABS – ABS resin, or Acrylonitrile Butadiene Styrene, is a thermoplastic polymer commonly used to manufacture consumer products such as toys, appliances, automotive parts, and electronic components. It is a lightweight, rigid material resistant to chemicals, abrasions, and impact.
ABS does have some issues of concern, including shrinkage, thermal expansion, poor chemical resistance, UV degradation, and it is a highly flammable material requiring flame retardant additives in specific applications.
- Nylon – Nylon resin is plastic made from long-chain synthetic polymer molecules. It is widely used for various products and applications, such as clothing, electronics, automotive components, and industrial machinery. Nylon resin is known for its strength, durability, and flexibility, making it an ideal material for many applications.
The downside of nylon is poor weather resistance, poor chemical resistance, high shrinkage, poor machinability, and higher cost.
- PETG – PETG resin is a type of thermoplastic polymer resin. It is a polyester derived from glycol and terephthalic acid and is commonly used to manufacture film, fiber, food packaging, and other consumer products. It is highly durable and resistant to heat and chemicals. PETG resin is also known for its flexibility and transparency, making it an ideal material for 3D printing.
Yet, there are negatives. It is vulnerable to hydrolysis, and it can be challenging to print. It requires a heated bed and a cooling fan to maintain a consistent layer height, and it is more expensive than other types of filaments.
- PLA – PLA resin is a type of plastic made from renewable resources such as corn starch, sugarcane, and tapioca roots. It is a biodegradable, non-toxic material that can create 3D-printed parts and components. It is a popular choice for 3D printing due to its ease of use, low cost, and strong mechanical properties.
The disadvantages of PLA resin are that it is not suitable for high-temperature environments and is not food safe. PLA is not UV resistant and is not as easy to work with as other materials. Therefore, it requires more time and effort to produce a quality product. Plus, PLA resin is not as strong or durable as other materials, such as ABS or PETG.
- Polycarbonate – Polycarbonate resin is a thermoplastic resin made from the monomers bisphenol A and phosgene. It is an incredibly strong, heat-resistant, and lightweight material used in many applications, such as automotive components, medical devices, aircraft, and even bulletproof glass. Polycarbonate resins are also often used to make engineering plastics, injection molded parts, and thin films.
The drawbacks to polycarbonate resins include susceptibility to UV degradation, vulnerability to attack from solvents and acids, prone to stress cracking caused by mechanical stress or thermal shock, and it is also more expensive than other plastic resins.
For prototyping and general-purpose projects, PLA and ABS plastics are popular choices. For more specialized applications, such as medical models or detailed miniatures, resins such as nylon or polycarbonate may be better suited. Resin materials like epoxy, polyurethane, and silicone can also be used for high-strength and flexibility projects.
Get multiple quotes for your parts in seconds