4 Best Metals for 3D Printing
The 4 best metal materials for use in 3D printing. Learn more now!
Introduction
3D printing creates parts from a 3-dimensional drawing and prints products by placing layers of material in succession resulting in a finished product. 3D printing is an additive manufacturing technology that can manipulate metal materials to produce an almost unlimited selection of objects. Metal materials are available in powder and filament form for use with several 3D printing technologies. 3D printing allows the creation of complex metal geometries that are difficult or unattainable with conventional machining methods.
Metals for 3D Printing
Metal 3D printing produces stronger parts that are lighter in weight than items produced by traditional subtractive processes such as machining. Studies have shown that 3D-printed metals can be much stronger than metals manufactured by conventional methods. Metal printing is a high-energy process that requires much higher melting temperatures than traditional plastic materials.
Direct Laser Sintering (DMLS) is a 3D printing process that uses a powder bed for the material printing shaping the metal dust into a completed part. The metal dust is shaped in the printer into a formed part. After printing, DMLS parts can be electro-polished to improve the surface finish. DMLS can also electro-polish parts to improve the overall surface finish.
Additional metal 3D printing powder bed technologies include; printing Selective Laser Sintering (SLS), Direct Metal Printing (DMP), and Laser Powder Bed Fusion (LPBF). The other metal 3D printing technologies include; Electron Beam Melting (EBM), Direct Energy Deposition (DED) – both powder and wire, Binder Jetting, and Bound Powder Deposition (BPD) – also referred to as Bound Powder Extrusion.
The constraints to metal printing are whether the metal powder can be effectively bound to form objects and product availability.
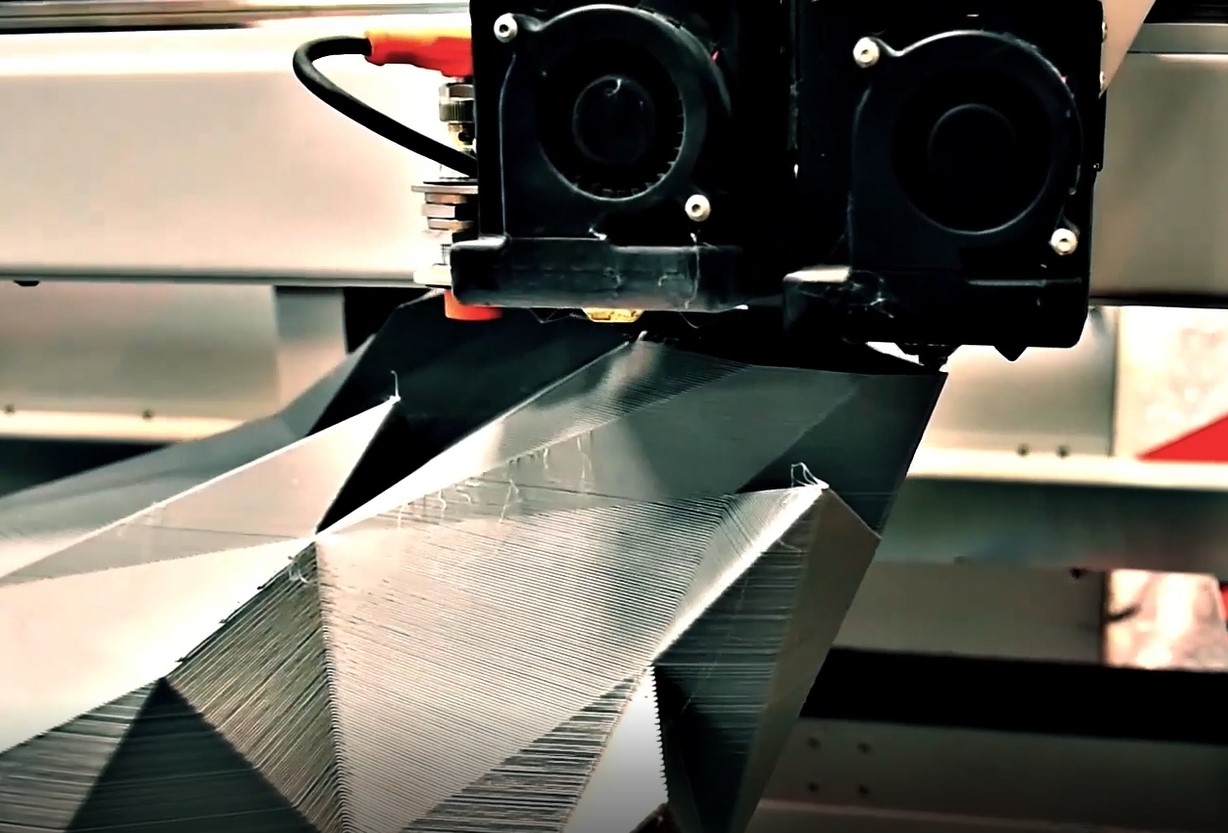
Stainless Steel
Stainless Steel (SS) is a popular metal alloy composed of steel, chromium, and other elements known for its strength, durability, ductility, and corrosion resistance. It is used in a wide variety of applications and is popular in the aerospace, oil and gas, food service, and healthcare industries. While the material is somewhat expensive, it is less costly than titanium and nickel. Testing shows that 3D-printed stainless steel parts as 2 to 3 times as strong as steels manufactured by conventional manufacturing methods.
For 3D printing of stainless steel alloys, below are the more commonly used materials, materials types, and technologies:
Common Materials:
- 316L
- 17-4GPH
- 15-5 PH
Material Types:
- Powder
- Filament
Common 3D Printing Technologies:
- Direct Laser Sintering (DMLS)
- Binder Jetting
- Direct Metal Deposition (DMD)
Tool Steel
Tool steel is a hard, tough material with a high tensile strength that is quite expensive due to its resilient performance characteristics. It is a steel superalloy that includes nickel, cobalt, and carbon. Tool steel is known to be able to weather significant abuse. Tool steel is also called maraging steel and is known for its exceptional strength-to-weight ratio. Tool steel is widely used in a variety of tooling applications, including cutting tools, dies, molds, and heavy-duty parts for aerospace and automotive.
3D-printed tool steel can also be heat-treated for exceptional hardness and durability, as is common with tool steel products developed from traditional subtractive manufacturing methods. There are exceptions where 3D printed tool steel can be CNC machined or polished. The mechanical properties of 3D-printed tool steels are also quite similar to those of traditionally produced tool steel items. 3D-printed tools steel has high wear resistance and good heat transfer.
There are two types of tool steel used in 3D printing. They are:
- Carbon-free maraging steel
- Carbon-bearing tool steels.
For 3D printing of tool steel, below are the more commonly used materials and technologies:
Common Materials:
- A2
- H13 (1.2344)
- M2 (1.3343)
- MS1
- 18Ni300 (1.2709)
- 18Ni1400
- 18Ni1700
- 18Ni1900
- 18Ni2400
Material Types:
- Powder
- Filament
Common 3D Printing Technologies:
- Direct Laser Sintering (DMLS)
- Fused Filament Fabrication (FFF)
Titanium
Titanium is known for its excellent strength, durability, and high corrosion rate. It is often used in some of the most unforgiving environmental applications. Titanium products are used in various applications, including aerospace, automotive, and healthcare.
3D-printed titanium has yielded remarkable results, including significant weight reductions while maintaining excellent strength and corrosion resistance. Since the material is strong, lightweight, and inert, it is perfect for custom-printed implants in the medical field.
For 3D printing of titanium, below are the more commonly used materials and technologies:
Common Materials:
- Ti6AI4V
- Ti64
- TiGr5
- TiGr23
- TiGr1
Material Types:
- Powder
- Filament
Common 3D Printing Technologies:
- Laser Powder Bed Fusion (LPBF)
- Direct Laser Sintering (DMLS)
- Direct Metal Printing (DMP)
Inconel 625
Inconel 625 is a nickel-chromium-based superalloy designed to withstand high temperatures, stresses, and harsh environments (including chloride). Repeated heat cycles have little effect on Inconel 625. The strength, temperature, and corrosion resistance make the material ideal for aerospace applications. It is also used in automotive, chemical processing, and offshore applications such as the petroleum industry.
The Inconel 625 superalloy is expensive. This is why additive manufacturing techniques such as 3D printing are preferred to traditional subtractive manufacturing methods – there is little wasted material. Another is that the exceptional material characteristics make it extremely difficult to machine. Fortunately, it is reasonably easy to 3D print with DMLS. Direct Energy Deposit and Binder Jetting are also used to produce parts with Inconel 625.
A new additive manufacturing technology to produce Inconel parts is Atomic Diffusion. This technology is a powder 3D printing method similar to FDSM printing. After printing, the product is washed in a debinding solution and sintered in a furnace. The furnace burns away the plastic binder, and the metal powders form a more robust part. The process is highly accurate and a cost-effective alternative to producing the expensive material.
For 3D printing of Inconel 625, below are the more commonly used materials and technologies:
Common Materials:
- Ni625
Material Types:
- Powder
- Filament
Common 3D Printing Technologies:
- Direct Laser Sintering (DMLS)
- Direct Energy Deposition (DED)
- Binder Jetting
- Atomic Diffusion
Get multiple quotes for your parts in seconds