Additive Manufacturing
Additive manufacturing offers many advantages for product designers when it comes to precision, speed, and the ability to produce intricate features.
Introduction to Additive manufacturing
The manufacturing industry continues to evolve and some of the most ground breaking innovations are occurring in additive manufacturing. Additive manufacturing is known for its amazing speed and precision, which is increasingly making it a go-to option for the production of a wide variety of industrial and consumer products and applications.
While traditional manufacturing technologies like CNC machining require longer lead times and fall short when it comes to producing complex features, 3D printing can serve as an augmentation or even a substitute to CNC machining for many projects needing greater precision and shorter lead times.
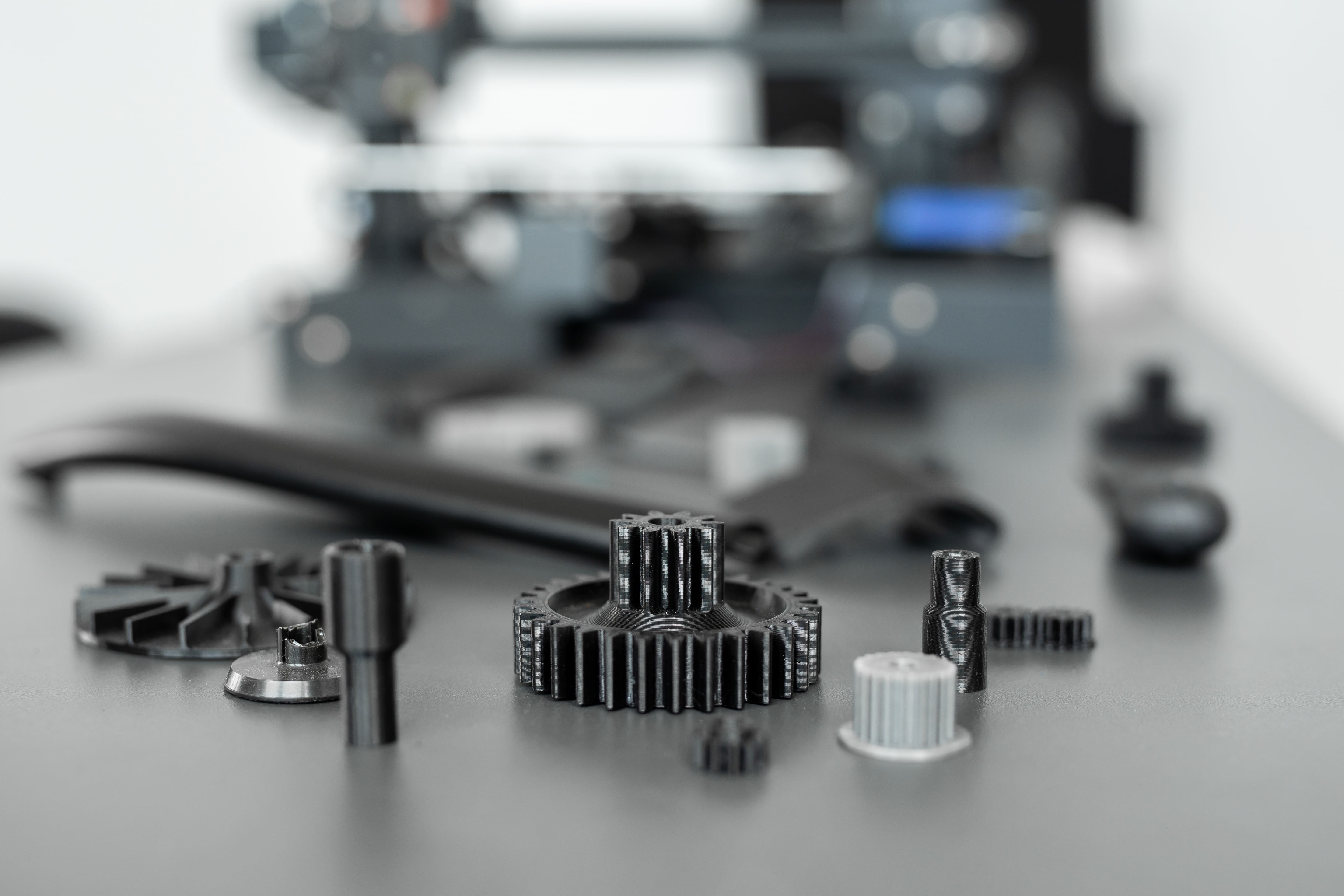
What is Additive Manufacturing?
Additive manufacturing is a process that builds parts and products by adding material rather than by taking away from it as in CNC machining. One of the most common forms of additive manufacturing is 3D printing. Additive manufacturing utilizes computer-controlled machinery and CAD software. This machinery follows the programming of the CAD software to produce the intended part or product design by adding material.
How Does Additive Manufacturing Work?
Additive manufacturing machines—known as 3D printers—are made up of many small and intricate parts. For this reason, it’s imperative that regular, specialized maintenance and performance testing are undertaken to ensure accurate prints.
Raw materials used in additive manufacturing often require delicate handling and are known to have a shorter shelf life compared to other manufacturing materials. While it is true that some 3D printing processes include the option to recycle excess build material, it’s important to keep in mind that repeated use of recycled material can compromise the properties of the material if it’s not replenished frequently enough with brand new material.
One of the biggest advantages of 3D printing is that most additive manufacturing machines do not require monitoring once the print process has started. The reason for this is that the 3D printer is controlled by a pre-programmed, automated process. In fact, one of the only ways that the additive manufacturing process can be interrupted is if the 3D printer has an insufficient amount of material.
For many additive methods, you can simply remove the printed component from the build platform. For other additive methods that are more industrial in nature, removing the print can involve a high degree of skill and precision as the print may still be attached to the build plate or encased in build material. For these additive methods, more complex removal procedures run by manual human operators are required, as well as a closely controlled environment and special safety precaution.
After the printed part is removed from the build unit, a variety of post-processing methods can be employed. For example, SLA additive manufacturing cures printed parts under UV light and SLS metal parts may need to be heat-treated in an oven. Moreover, some additive manufacturing methods use supports, which will need to be carefully removed during post-processing. Additionally, many additive materials can be sanded, tumbled, or polished during post-processing.
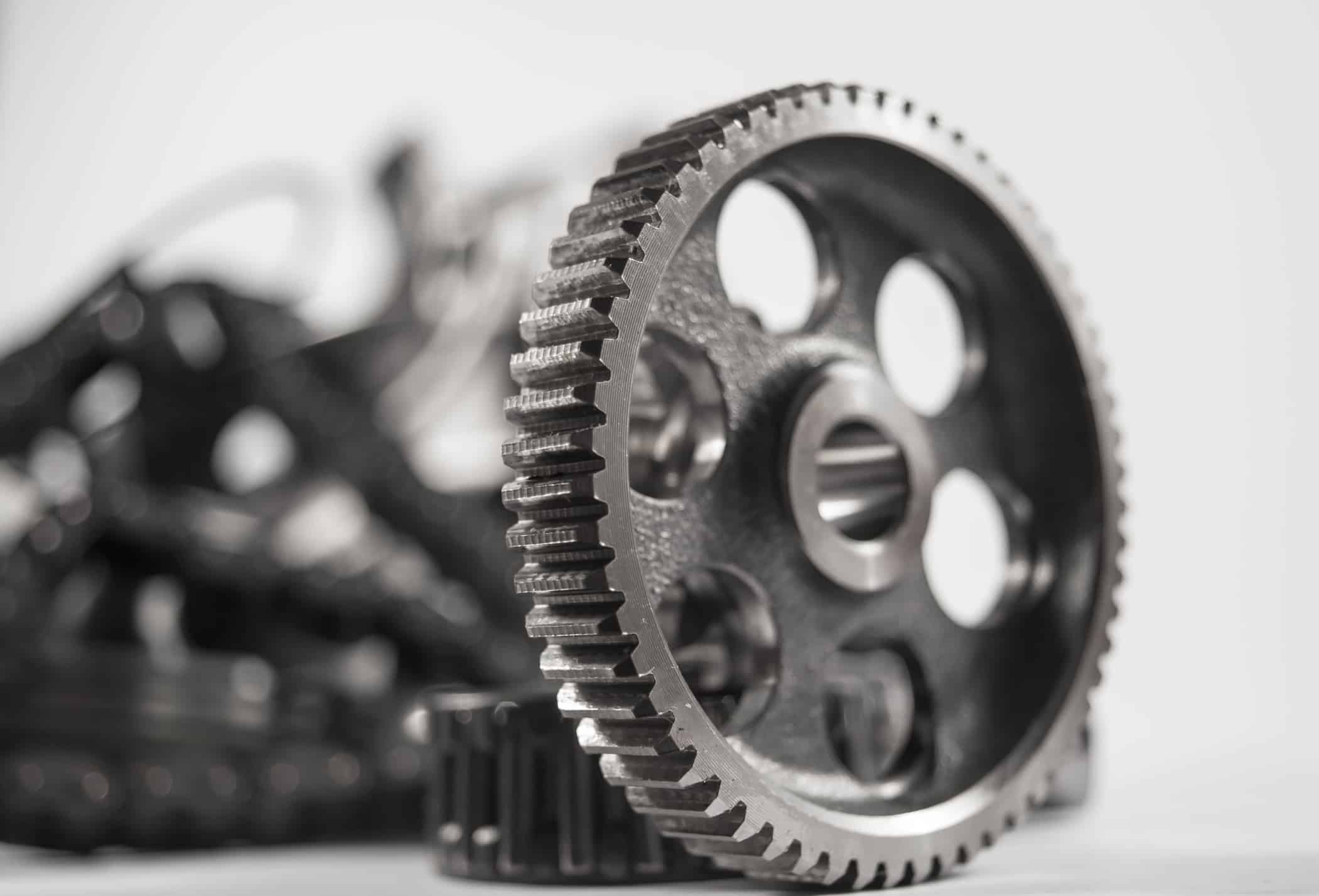
The Applications of Additive Manufacturing
Additive manufacturing has become a valuable manufacturing method in a wide variety of industries including aerospace, medical, automotive, consumer goods, and robotics. Some of the reasons for this popularity include the fact that additive manufacturing offers remarkable efficiency, affordability, and quality for many different product designs.
Here are some of the most common applications of additive manufacturing:
Low Volume Parts with Quick Turnarounds
Additive manufacturing methods are great solutions for on-demand, low volume part production. The reason for this is that traditional manufacturing methods often demand large volume production in order to decrease the unit cost because of the tooling requirements. In contrast, additive manufacturing involves no added expense for tooling, which means small quantities of 3D printed parts can be easily manufactured on demand.
3D Printing of Assembled Parts
Additive manufacturing enables the consolidation of separate components into one single 3D printed part. These consolidated prints often have complex geometries or moving parts. Additive manufacturing allows the entire assembly of the part to be produced in one print as opposed to multiple components having to be assembled later as is the case with traditional manufacturing. The result of this amazing capability is that less time and money is spent on assembly, and project delays can be avoided.
Manufacturing of Extremely Small Parts
One of the drawbacks to CNC machining or subtractive manufacturing is that it can be challenging for small parts. In contrast, additive manufacturing is an excellent solution for producing smaller parts at lower volumes. Moreover, as small part production increases by using additive manufacturing, economies of scale take place and overall project costs decrease. One of the best examples of using additive manufacturing to produce small parts is in the medical industry where parts need to be highly customized for individual use in applications such as implants or prosthetics.
Enhanced Customization
Compared to CNC machining, additive manufacturing is far superior when it comes to customization options for product designers. Since 3D printing doesn’t have the costs and time demands associated with the tooling requirements of CNC machining, engineers can customize 3D printed parts for highly specialized applications. These customization options include factors such as aesthetics and advanced functionality. Some common examples of enhanced customization using additive manufacturing include the consumer products industry as unique features such as logos can be easily added and modified by adjusting the design file that inputs to the 3D printer. Additionally, the dental industry enjoys the high degree of customization offered by additive manufacturing for applications including dental trays that can fit the patient’s teeth with a high degree of accuracy and precision.
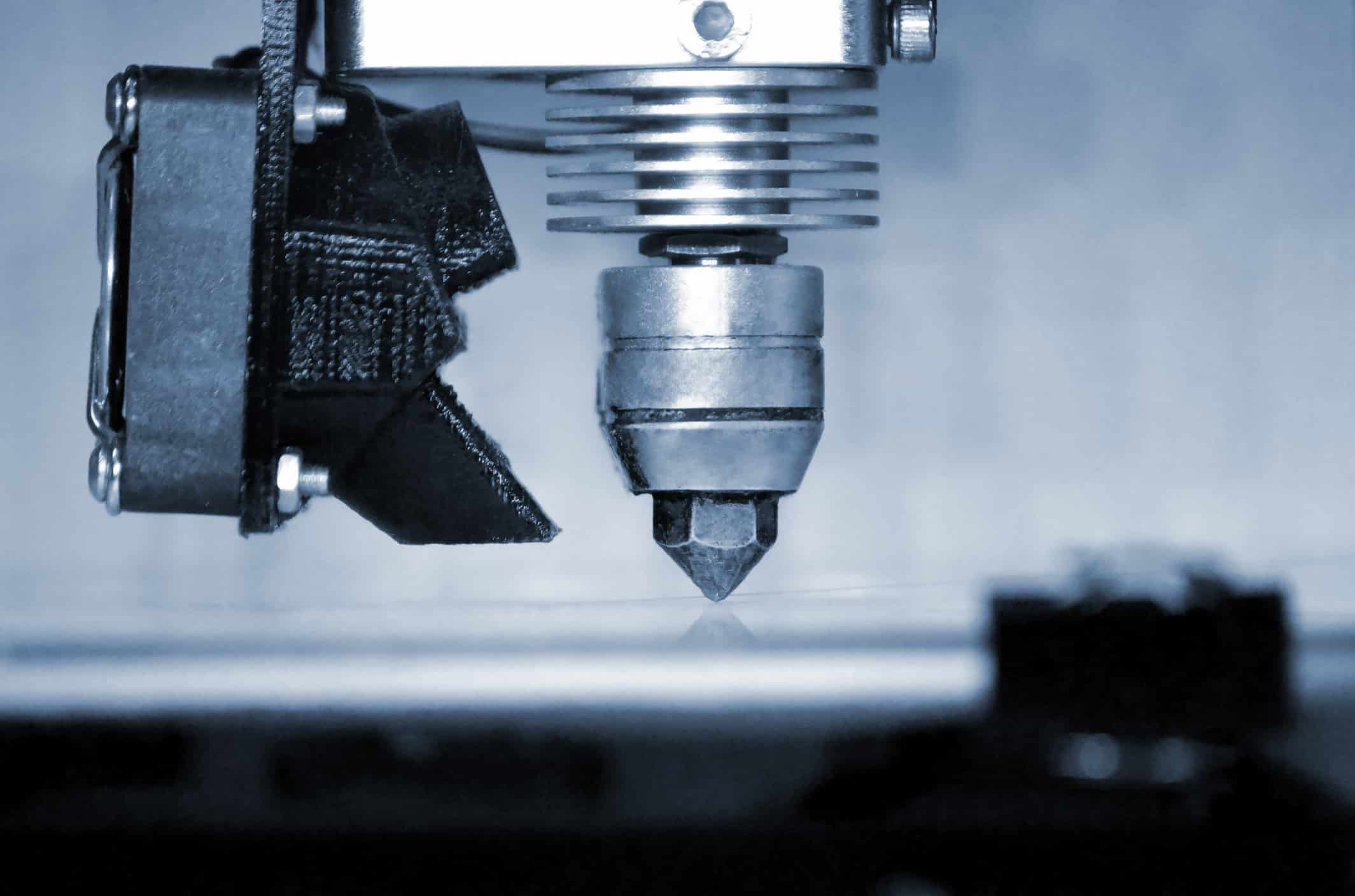
3D Printing vs. Additive Manufacturing: What’s the Difference?
The terms “3D printing” and “additive manufacturing” are often used interchangeably, but they are not exactly the same. The primary difference between additive manufacturing and 3D printing is that 3D printing produces parts by adding material layer by layer. Additive manufacturing, on the other hand, also produces parts by adding material, but the material may or may not be added in layers.
Specifically, 3D printing is a manufacturing process that builds a part or product layer by layer using a highly sophisticated machine and CAD software. The CAD software programs the 3D printer on the exact quantity of material to use and the exact location to deposit it. Most 3D printers use polymer-based printing material because it’s versatile and also easy to source for 3D printing projects. In addition to polymers, there are some 3D printing technologies that can also use metals, alloys, and ceramics.
Based on these characteristics, there’s no denying that 3D printing is indeed an additive manufacturing process. However, the difference between the two lies in the fact that additive manufacturing is a broader category that includes a wider variety of processes compared to only 3D printing. For example, selective laser melting and electron-beam manufacturing are also classified as additive manufacturing methods. Moreover, neither of these methods builds parts layer by layer like 3D printing does, but they still entail the manufacturing of parts by adding material rather than subtracting it like CNC machining.
Get multiple quotes for your parts in seconds