Waterjet cutting service
Waterjet cutting is one of the most common material cutting processes. It is used in a wide variety of applications. Learn more now!
Waterjet Cutting Systems
Waterjet cutting is an accelerated erosion process using a high-pressure water stream to remove material. It was first developed in the 1800s for hydro-mining in the New Zealand and Russian coal mines. The process was updated in the 1930s to cut paper. By the 1950s, waterjet technology included abrasive materials added to the water to cut hard materials. Significant advancements occurred from the 1950s through the 1970s when the technology yielded commercially available hypersonic water streams. Waterjet technology has improved over the last 70 years with the addition of CNC controls, taper compensation, and high-pressure pumping systems.
This article discusses Waterjet Cutting Systems, their typical applications, and their benefits.
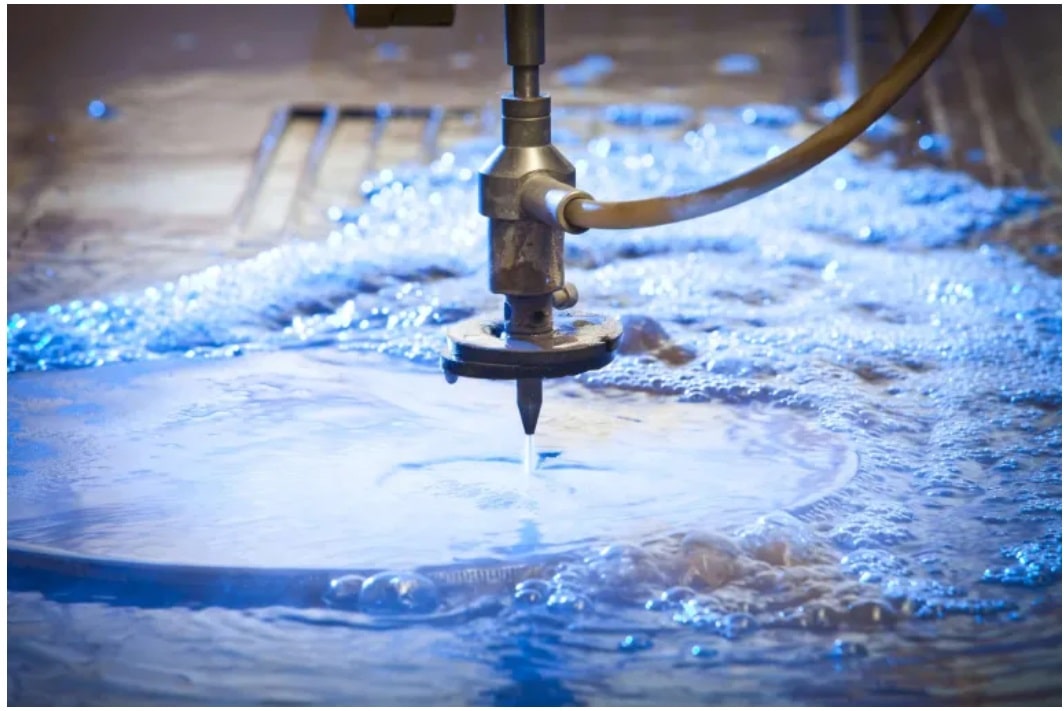
What is Waterjet Cutting?
Waterjet cutting utilizes intense water pressure from 30,000-90,000 psi to cut various materials. Commercial machinery uses computer numerical controlled (CNC) systems to position the water jet nozzle with an accuracy of up to 0.005”. Water pressure is intensified by either a direct drive pump or an intensifier pump forcing water through a hard jewel orifice at speeds up to 2,500 mph (Mach 3) into a mixing chamber. This creates a vacuum in the chamber, where an abrasive may be added to increase the cutting erosion. The stream is fired at the object at a hypersonic velocity to erode the material in the cutting process. The hard jewel nozzle uses a commercial-grade ruby, diamond, or sapphire.
Taper compensation allows the defection of the water stream to avoid tapering the cut. The cutting head is adjusted to counter the drag from the water stream. This allows the waterjet cutter to produce sharp corners, bevels, and even small radii. The cut is clean, and with supersonic velocities, the waterjet can cut almost any known material.
“Pure Waterjet” cutting uses only water in the cutting process. This is often used for softer materials such as paper, textiles, foam, and food. An abrasive is introduced into the stream to cut denser materials for more aggressive cutting applications. The term “Abrasive Waterjet” is used for waterjet cutting systems with an abrasive mix of water and a hard abrasive. The most common abrasive used is garnet, a group of silicate materials used as abrasive and gemstones. Aluminum oxide is another abrasive used in the process. These machines typically use ½ -1 gallon per minute of recycled water.
Application of Waterjet Cutting Service?
Applications for waterjet cutting involve almost every known material. This includes wood, paper, textiles, rubber, plastic, foam, leather, food products, composites, stone, marble, tile, glass, and metals. Waterjet cuts products for automotive, aerospace, architecture, electronics, marine, medical, military, mining, and manufacturing. The process is also well-suited for products with delicate materials, reflective materials, hard metals, and materials sensitive to heat intensity.
Some of the many products that utilize waterjet cutting services include:
- Automotive components
- Medical and laboratory equipment
- Gaskets
- Carpet
- Mirrors
- Dashboards
- Stepping stones
- Boat shells
- Tabletop inlays
- Jet turbine blades
- Engine parts
- Electronic and microelectronic components
- Food processing, including meat, fruit, vegetable, snack, and frozen food slicing.
Benefits of a Waterjet Cutting Service
Powerful, versatile, and efficient, waterjet cutting services provide a smooth, accurate finished surface. Waterjet services can perform detailed work cutting more complex designs than plasma or laser cutting equipment. 2D and 3D cutting are available, and with accuracy up to 0.005”, the waterjet process can produce small, intricate parts. The small kerf width (the slit or notch made by the cutting device) allows for complex cutting and a smooth, burr-free edge.
The system is designed for speed and accuracy, with no tooling changes necessary with product changeovers. Waterjet cutting systems are faster than traditional cutting methods and create no stress or molecular modifications to the material. No heat is transferred during the cold waterjet cutting process, so it is ideal for thermally sensitive applications such as foam, electronics, fabrics, and wood. Plus, there is no warping or microscopic cracking associated with the waterjet process.
This technology is used in meat-cutting and other food-processing applications eliminating the risk of cross-contamination and increasing shelf-life and food safety. The cutting process is robust enough to slice through hard metals up to 12” thick, and thin materials can be stacked and cut simultaneously in a “stacking“ procedure.
The waterjet cutting equipment has a closed-loop system where the water is recycled. And In addition, the operator and work environment are healthier, with little/no toxic fumes, airborne dust, or smoke.
Get multiple quotes for your parts in seconds