Sheet Lamination
Discover how the manufacturing 3D Printing process Sheet Lamination, also known as LOM, SL, works.
Introduction to Sheet Lamination
The Sheet Lamination (SL) 3D printing manufacturing technique, also known as Laminated Object Manufacturing (LOM), consists of superpositioning several layers of material composed of foil to manufacture an object. The operator cut each foil to shape with a knife or laser to fit to the object’s cross-section.
Helisys Inc. was the first to develop this additive manufacturing technique. Much later, Solido, an Israel-based company, has made it popular. Solido 3D printers contain LOM technology and produce parts made with a combination of PVC (PolyVinyl Chloride) and a proprietary adhesive, which results in rugged, yet inexpensive models. Later, the Ireland-based company Mcor Technologies Ltd invented a sheet lamination technique based on paper. The latest developments of SL made possible the use of carbon fiber sheets and various composites, a technique mastered by the EnvisionTEC company and the Impossible Objects startup. Their manufacturers still honed this technique, but it remains not very well known.
- The paper material is taken from standard copy paper in paper-based laminated object manufacturing. First, the paper goes through a normal inkjet 2D printer before the colorization. Then the operator stacks all the colored pages required to build the final part in the 3D printer, which uses them one by one. The process thereby removes each page from the stack, glued to the previous one, and then precision-cut with a knife. Layer by layer, the workpiece is completed. The operator can remove the remaining paper manually. Then he could color Paper models, works on wood-like characteristics. The result's precision depends mainly on the thickness of the layered material used, like a paper sheet, for example. A standard sheet of paper has a thickness between 50 and 100 microns.
- Composite Based Additive Manufacturing (CBAM) by Impossible Objects, a US-based startup, patented the Composite-Based Additive Manufacturing (CBAM) technique. The machine fuses Fiber-reinforced composites with a thermoplastic to create robust parts.
- Selective Lamination Composite Object Manufacturing (SLCOM) by EnvisionTEC. The EnvisionTEC company developed the Selective Lamination Composite Object Manufacturing technique. SLCOM uses thermoplastics as a base material and woven fiber composites.
What is the application of Sheet Lamination?
Applications for 3D Laminated Object Manufacturing parts include ergonomic studies, topography visualization, architecture models for paper-made objects. Thermoplastics and fibers make it possible to directly manufacture functional, lightweight technical components for aerospace and automotive industries at a very competitive cost.
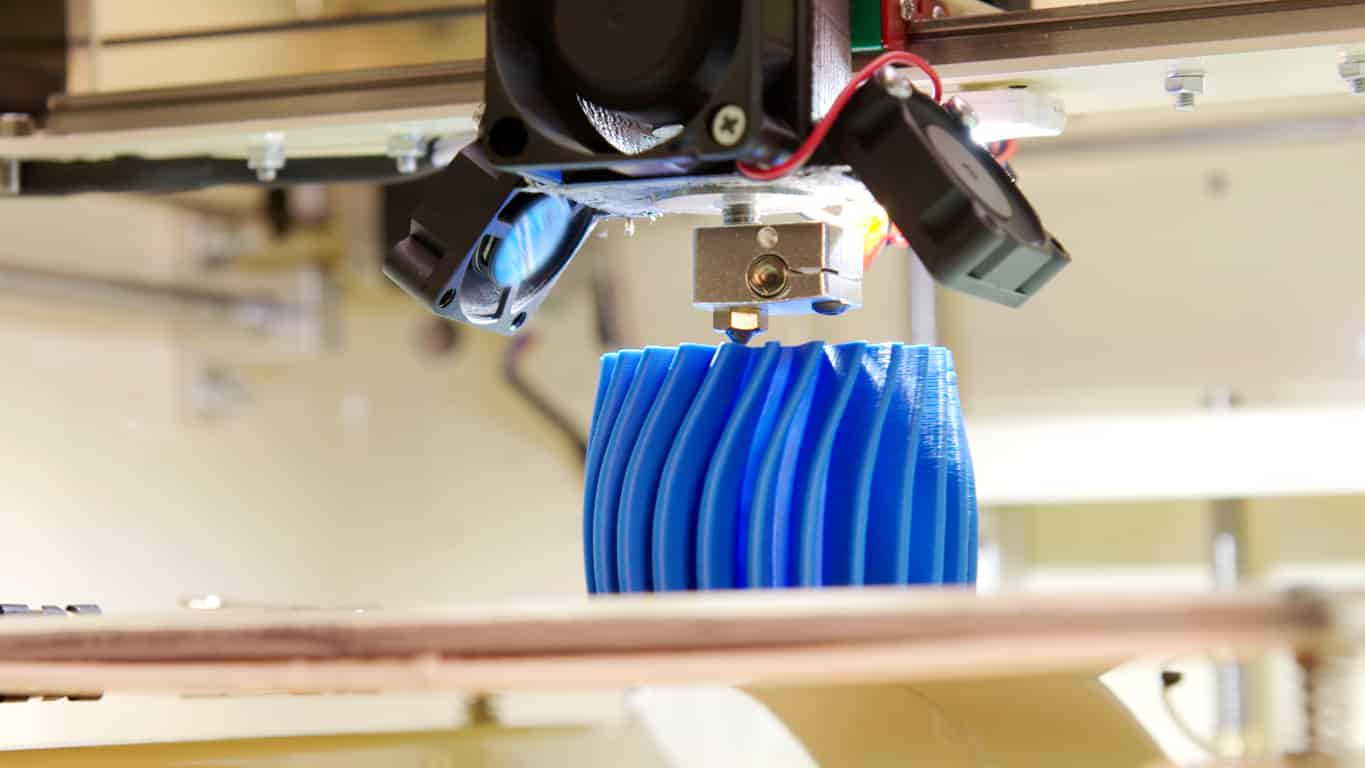
Get multiple quotes for your parts in seconds