Forming
Discover what is Forming, how does it work, and its usages in the industry.
What is the forming process?
We generally classify Forming operations according to the differences in effective stress. Compressive forming involves a uni- or multiaxial compressive loading and includes processes:
- rolling, where the material passes through a pair of rolls,
- extrusion, where machine push the material through an orifice,
- die forming, where a press stamps the material around or onto a die,
- forging, where localized compressive forces shape the material
- indenting, where a tool is pressed into the object.
Other forming processes exist:
- tensile forming, by uni- or multiaxial tensile stress (stretching, expanding, and recessing),
- combined tensile and compressive forming (stamping, pulling through a die, etc.),
- bending under bending load,
- shearing.
Forming can be hot (forging, stamping, deep drawing…), cold (extrusion, bending, drawing…), or electromagnetic.
The Metal Extrusion Forming Process
Extrusion consists in shaping a material by pressing it with a mechanical or hydraulic tool. It can be hot or cold, continuous or semi-continuous. This process can produce compressive and shearing forces in the base material. During the operation, the metal alloys undergo considerable deformation without being torn. The objects then obtain a cross-sectional profile and are suitable for a wide range of applications. One of the main drivers in the materials extrusion market remains the growing demand for packaged ready-to-eat foods (ready-made pasta, cereals, snack bars, etc.).
Aluminum remains the most commonly extruded material, hot or cold. The size of the aluminum extrusion market may increase by 6.76 million tons from 2020 to 2024. The products are widely used in various applications, including roofing for prefabricated buildings. Yet, the growth of the automotive, logistics, pharmaceutical, consumer goods, and retail sectors will further stimulate this demand. On the other hand, forming services use brass to extrude non-corrosive rods, automotive parts, pipe fittings, and technical parts.
The Stamping Forming Process
During stamping, a press around or a die deform the metal. Like molds, this tool is usually adapted to the product. Products made using dies range from simple paper clips to complex parts applied in advanced technologies.
Manufacturers can use two tools to form sheet metal, such as automotive body components. One, termed the punch, performs the stretching, bending, and/or cutting operation. The other, called the die block, firmly clamps the part and serves a similar stretching, bending, and/or cutting process.
The global metal stamping market is valued at USD 140,300 million in 2020 and is expected to reach USD 165,950 million by the end of 2026.
Sheet Metal Forming
Sheet metal is one of the basic forms used in metalworking and can be cut and bent into various shapes. The global market for sheet metal reached $265 billion in 2018. From 2019 to 2025, it will probably gain a CAGR of 5.0%. Countless everyday objects are made from this material: car and truck bodies, airplane fuselages and wings, medical tables, building roofs, and more.
Various techniques can carry Sheet Metal forming out:
- stamping, where the metal is lengthened on a form or die,
- expanding, consists of cutting or stamping slits in an alternating pattern, then stretching the sheet in an accordion shape. It is perfect for applications where there is a need for air and water flow,
- laser cutting, in which the laser beam heats and burns the material, making it possible to cut the metal sheet.
- Photochemical machining, which is a closely controlled corrosion process. The objective is to produce complex metal parts with very fine details,
- press brake forming, utilized to design long and thin sheet metal objects,
- punching, consists of placing the metal sheet between a punch and a die mounted in a press.
- Rolling, during which one or more pairs of rolls reduce the thickness of the part. It is employed to make thickness uniform,
- stamping,
- water jet cutting, for controlled erosion in metal or other materials using a high speed, high-pressure water jet or a mixture of water and an abrasive substance.
Discover 3DEXPERIENCE SOLIDWORKS for Makers

What is metal forming?
The forming of a material aims to give it a particular shape, following a series of specific techniques. This process makes it possible to reshape a part without adding or removing material in metallurgy. Manufacturers can carry it out thanks to various methods. Facing numerous demands, the global market for metal forming machine tools will reach $48.67 billion by 2026.
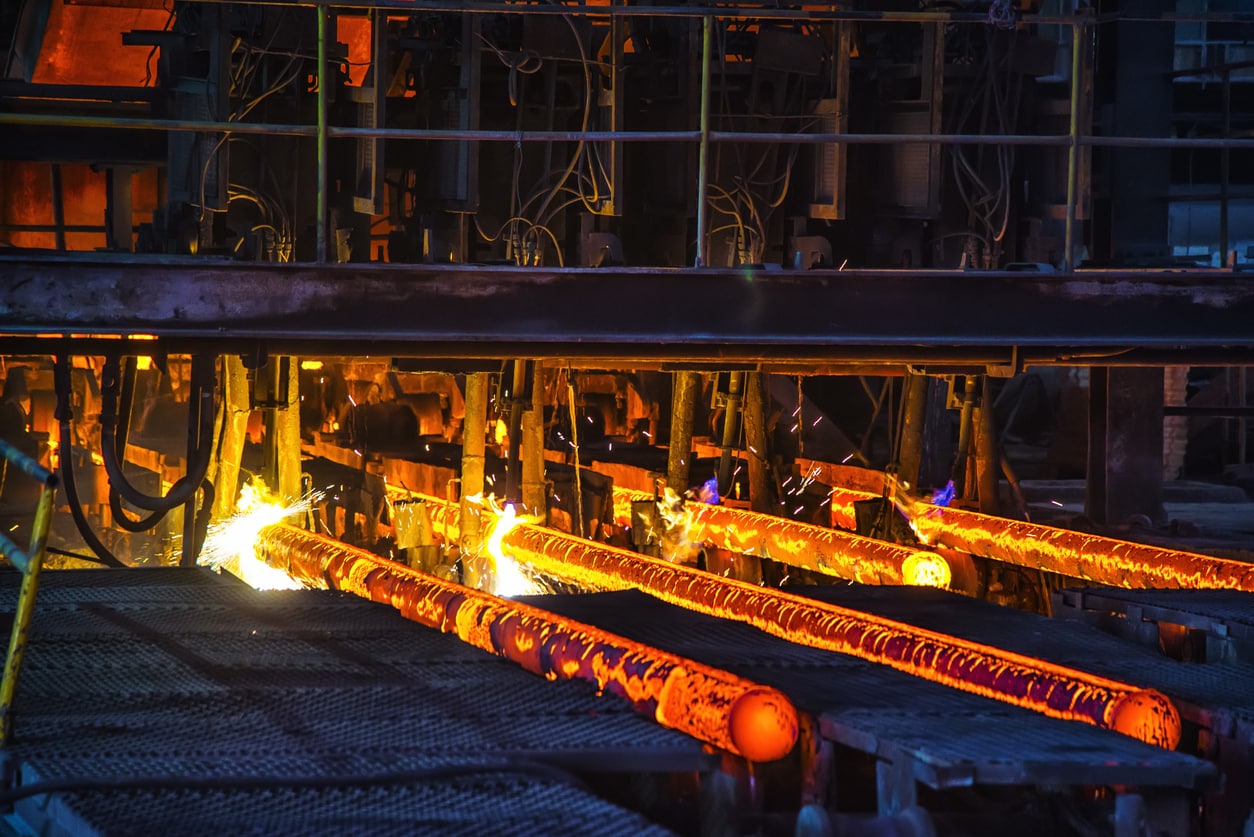
Which material to choose for metal forming?
Specific metal forming techniques could reshape parts such as extrusion, stamping, or sheet metal forming. Among the most commonly used metals are aluminum, steel, and brass, but also copper, tin, lead, magnesium, zinc, and titanium.
The selection of material for forming depends on the method. Depending on the properties of the metal, it will be more or less easily processed. Metals with a higher yield strength and higher spring back (stainless steel, structural steels, HSLA [High Strength Low Alloy] steels, etc.) require more work to be formed. Materials with lower yield strength and lower spring back (mild steel, aluminum, red metals such as bronze, brass, copper, etc.) generally need less labor. A stainless steel strip may require twice as much force as the same length of mild steel.
Aluminum
Aluminum has an excellent strength-to-weight ratio, high thermal and electrical conductivity, and natural corrosion protection.
This metal is favored for the extrusion process whether hot or cold. The automotive industry uses it extensively, as aluminum contributes to the manufacture of greener, more fuel-efficient cars, thereby reducing the carbon footprint of companies and their customers. The material is easily recyclable and resists all forms of corrosion, ensuring the long-term durability of the vehicle.
Sheet metal forming also relies primarily on this material. The interest of this technique lies in the elastic and plastic deformation it causes.
Brass
Brass has good machinability and excellent electrical conductivity. It is therefore ideal for applications that require low friction. It is also utilized in architecture to create gold-looking features for aesthetic purposes.
Brass is used to extrude non-corrosive rods, automotive parts, pipe fittings, and technical parts. It is also perfect for stamping processes that need metals with soft to medium hardness and a low flow coefficient.
Steel
Stainless steel can easily be welded, machined, and polished. It is used extensively in stamping processes. Mild steel, or low-carbon steel, is used to manufacture machine parts, jigs, and fixtures. On the other hand, Alloy steel contains other alloying elements, in addition to carbon, to improve hardness, toughness, fatigue, and wear resistance.
While we ordinarily use carbon steel for extrusion processes, it is also possible to make it with alloy steel and stainless steel.
Sheet metal forming often employs this metal. In 2018, steel accounted for the largest volume share of the sheet metal market at 91.7%. The resulting products are in high demand in the automotive, construction, and heavy industries (oil and gas), food, and chemical sectors. Stainless steel sheet is used to manufacture cookware and utensils such as sinks, grills, stoves and pots and pans. The usage is also possible to build for dishwashers, countertops, refrigerators, and washing machines.
Copper
Copper can be formed by extrusion to produce, for example, pipes, wires, bars, tubes, and welding electrodes. Beryllium copper is also suitable for stamping processes.
Tin and Lead
Tin and lead forming are carried out to manufacture pipes, wires, tubes, and cable sheaths. Molten lead can also be used instead of billets on vertical extrusion presses.
Magnesium
Aircraft and the nuclear industry also extrude magnesium to obtain parts. Magnesium appears to be about as extrudable as aluminum.
Zinc
Manufacturers use zinc forming to shape rods, bars, tubes, hardware components, and fittings during extrusion. This metal is also great for stamping processes.
Titanium
Titanium is extruded to make aircraft components, including seat rails, engine rings, and other structural parts.
The stamping processes could also utilize Silver, gold, platinum, and nickel.
Which industries are involved in metal forming?
Metal forming is one process that enables a part to be reshaped without adding or removing material, using various techniques. The increasing evolution of manufacturers towards better productivity has led to the adoption of automated tools in recent years. The automotive, aerospace, and construction industries are the most involved in metal forming.
The Automotive Industry
The automotive sector has the largest market share of metal forming tools for passengers, commercial and electric vehicles and already held 43.8% of the market in 2018. The key pillar of its growth is technological advances that offer lightweight design solutions, seamless connectivity, and automated driving. Stringent emission standards, reduced car weight, and increased fuel economy demand are expected to stimulate the metal forming market in the coming years.
Innovation in this industry depends on new technologies. Therefore, software and IoT remain valuable aids for sheet metal forming. For example, in 2018, Audi was working on designing rotors and stators used in electric motors. The ability to produce in-house resulted in savings of $17.15 to $28.58 per motor, as well as significant efficiency and autonomy.
The aerospace industry
The aeronautics and space industry often require components with high tolerances, complex geometries, and light density for rockets, but also aircraft.
This sector exploits forming for:
- structural elements and cladding panels, from small shallow to large deep parts, in aluminum alloys, stainless steel, and titanium.
- engine components, including stamped parts, made of high-strength and heat-resistant materials.
Sheet metal hydroforming is used to form low-volume parts and prototype components economically. Stamping remains a preferred method for the same reason, particularly for forming high-strength alloys used for jet engine components.
The consumer goods industry
This sector makes extensive use of metal forming for pots, cans, and coatings in general.
In the case of containers, sheet metal forming must not only provide a standardized quality but also be adapted to their particular application. For instance, some grades of stainless steel, such as 430, are resistant to mild acids and alkalis, but salt corrodes them easily. If the food manufacturing process involves large amounts of salt, 316 stainless steel is a much better choice. Some more specialized equipment may also require metal trays or baskets to be of a very specific size to ensure a consistent fit. The metal mold will have to meet a tight part tolerance during forming.
Today, virtual tests are performed to meet the needs of custom forming. This quality assurance process is produced within minutes and allows any design flaws to be corrected immediately.
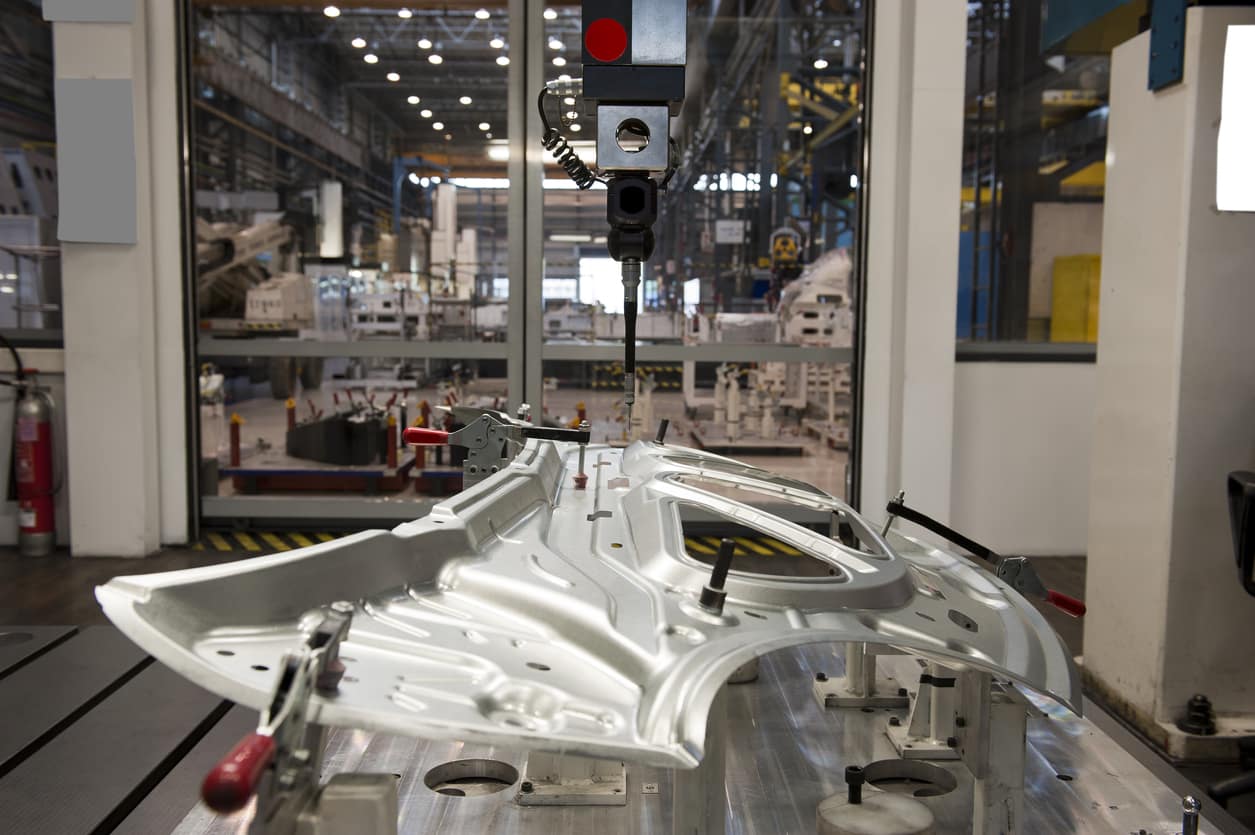
Get multiple quotes for your parts in seconds