Extrusion
Discover what is the manufacturing forming process Extrusion and its usage in the industry.
Introduction to Extrusion
The extrusion process can create objects with fixed cross-sectional profiles by pushing a material, most commonly metals, polymers, ceramics, concrete, modeling clay, and foodstuffs, through a die of the desired cross-section. This is beneficial for creating very complex cross-sections and with fragile materials because the material is only exposed to compressive and shear stresses. One key advantage is the excellent surface finish. Another is the increased strength of metal objects produced with extrusion.
Two types of extrusion exist: continuous or semi-continuous. Continuous extrusion involves the production of an indefinitely long material; semi-continuous involves the production of many pieces. The material can be either hot or cold. Extrudates is the term for objects produced with extrusion.
In 1797, the English inventor Joseph Bramah patented the first extrusion process for making pipe out of soft metals. The metal was preheated and forced through a die via a hand-driven plunger. Later, in 1820, Thomas Burr implemented this process with a lead pipe and a hydraulic press called “squirting.” Alexander Dick went on to expand the extrusion process to copper and brass alloys in 1894.
The extrusion process also has some drawbacks. They include surface and internal cracking, surface lines, and a “pipe,” which is a flow pattern that draws surface oxides and impurities to the center of a product.
Five extrusion processes
The five different extrusion processes are:
- Hot extrusion is performed above a material’s recrystallization temperature to keep the material from work hardening and to make it easier to push the material through the die.
- Warm extrusion is performed above room temperature but below the material’s recrystallization temperature. The temperature can range between 800 °F to 1800 °F (424 °C to 975 °C). The common usage is to balance required forces, ductility, and final extrusion properties.
- Cold extrusion is performed at room temperature or near-room temperature. Lack of oxidation, higher strength due to cold working, closer tolerances, better surface finish, and fast extrusion speeds if the material is subject to hot shortness are key advantages to cold extrusion.
- The Welding Institute in the UK invented friction extrusion and patented it in 1991. Initially, the usage was to produce homogenous microstructures and particle distributions in metal matrix composite materials. Friction extrusion differs from conventional extrusion in that the charge (billet or other precursors) rotates about the extrusion die. An extrusion force is applied to push the charge against the die. In practice, either the die or the charge may rotate or counter-rotate.
- Microextrusion is a microfilming extrusion process performed at the submillimeter range. Like extrusion, metal is pushed through a die opening, but the resulting product’s cross-section can fit through a 1 mm square.
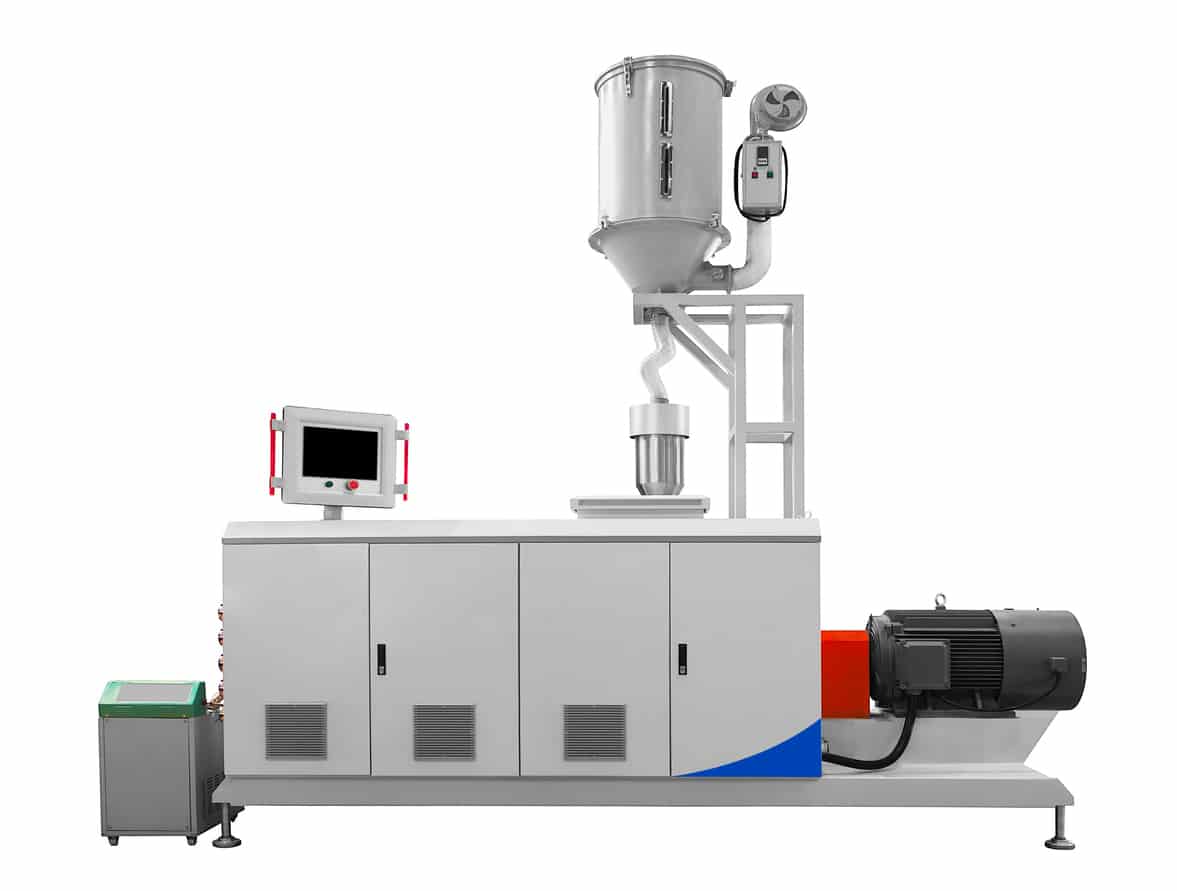
Get multiple quotes for your parts in seconds