Cutting
Discover what is the manufacturing process Cutting, how it works, and its usage in the industry.
What is the history of CNC cutting machines?
What does cutting mean today?
Any pointed tool is capable of cutting if it is harder than the object you want to work on and if you apply it with sufficient strength.
Even liquids can operate in this way, as long as they are applied with the necessary power. This is the case of the water jet cutting machine in CNC (Computer Numerical Control) machining.
Early types of water jet cutting adapted traditional devices, such as mechanical pantographs and CNC systems, based on John Parsons’ 1952 NC milling machine. The challenges inherent in this technology revealed the shortcomings of G-code. Dr. John Olsen of OMAX Corporation developed methods to position the water jet nozzle precisely while finely specifying the speed at each point along the path. He used ordinary PCs as the controller.
Cutting has remained at the heart of manufacturing throughout history. Many processes exploit metals. The idea is to produce a part by removing unwanted material from a block of metal in the form of chips. Methods can be similar to milling or drilling, punching, polishing, laser cutting, electro-erosion machining (EDM), etc.
Each technique has its limitations in terms of accuracy, cost, and effect on the material. For example, heat can damage the quality of heat-treated alloys, and laser cutting is less suitable for highly reflective materials such as aluminum.
What is the history of metal working and cutting?
Today’s machining includes many machine tools capable of creating an accurate and useful item from metals.
The earliest archaeological evidence of copper mining and working is the discovery of a pendant in northern Iraq dating from 8,700 BC. The material was hammered until it switched brittle and then heated to be further labored. This technology appeared around 4000 or 5000 BC.
Later, the link between heat and the release of metals from the rock became evident, and rocks rich in copper, tin, and lead were more in demand. Ore mining developed wherever they were found. Ancient civilizations knew seven metals: iron, tin, lead, copper, mercury, silver, and gold.
These same advances and materials were discovered and employed outside of Southwest Asia. China and Great Britain began to use bronze rather than the neglected copper. Japan started to exploit bronze and iron almost simultaneously.
With the historical periods of the pharaohs in Egypt, the Vedic kings in India, the tribes of Israel, and the Mayan civilization in North America, among other ancient populations, precious metals commenced being valuable. In those times, metallurgists were very skilled at creating ornamental objects, religious artifacts, and trade instruments from precious (nonferrous) metals, as well as weapons usually made of ferrous metals and/or alloys.
Over the past, metal items have become more common and increasingly complex. The need to acquire and work with them was more important. The availability of metals and metallurgists has strongly influenced the fate and economy of entire civilizations.
Metallurgists depend on extracting precious metals to make jewelry, building more efficient electronic devices, and industrial and technological applications ranging from construction to shipping containers, rail, and air transportation. Without them, goods and services would cease to flow around the world on the scale we know today.
We generally split Metalworking into three categories: forming, cutting, and assembly. Most cutting is done utilizing high-speed steel or carbide tools.
How are metals cut now?
Cutting represents a set of processes in which the workpiece is brought to a specified geometry by removing excess material. This operation is carried out using various types of tools that come into a finished part that meets the required characteristics. Two products are the net result of cutting: the waste or excess material and the finished part.
Cutting processes fall into one of three main categories:
- Chip production processes, better known as machining. For example, drilling a hole in a metal part;
- Burning, a set of operations by which the material is cut by oxidizing a notch to separate pieces of metal. For example, the use of an oxy-fuel cutting torch to divide a steel plate into smaller parts;
- Various specialization processes do not easily fall into one of the above categories—for example, chemical milling, which removes excess material through the use of etching and masking chemicals.
There are many technologies for cutting metal, including:
- Manual technologies: saw, chisel, shears, or metal shears;
- Machine technologies: turning, milling, drilling, grinding, sawing;
- Welding/combustion technologies: laser combustion, oxy-combustion, and plasma;
- Erosion technologies: by water jet, electrical discharge, or abrasive flow machining;
- Chemical technologies: photochemical machining.
A coolant is used when there is significant friction and heat at the cutting interface between the tool, for example, a drill or a milling cutter and the workpiece. The idea is to avoid excessive tool wear.
Discover 3DEXPERIENCE SOLIDWORKS for Makers
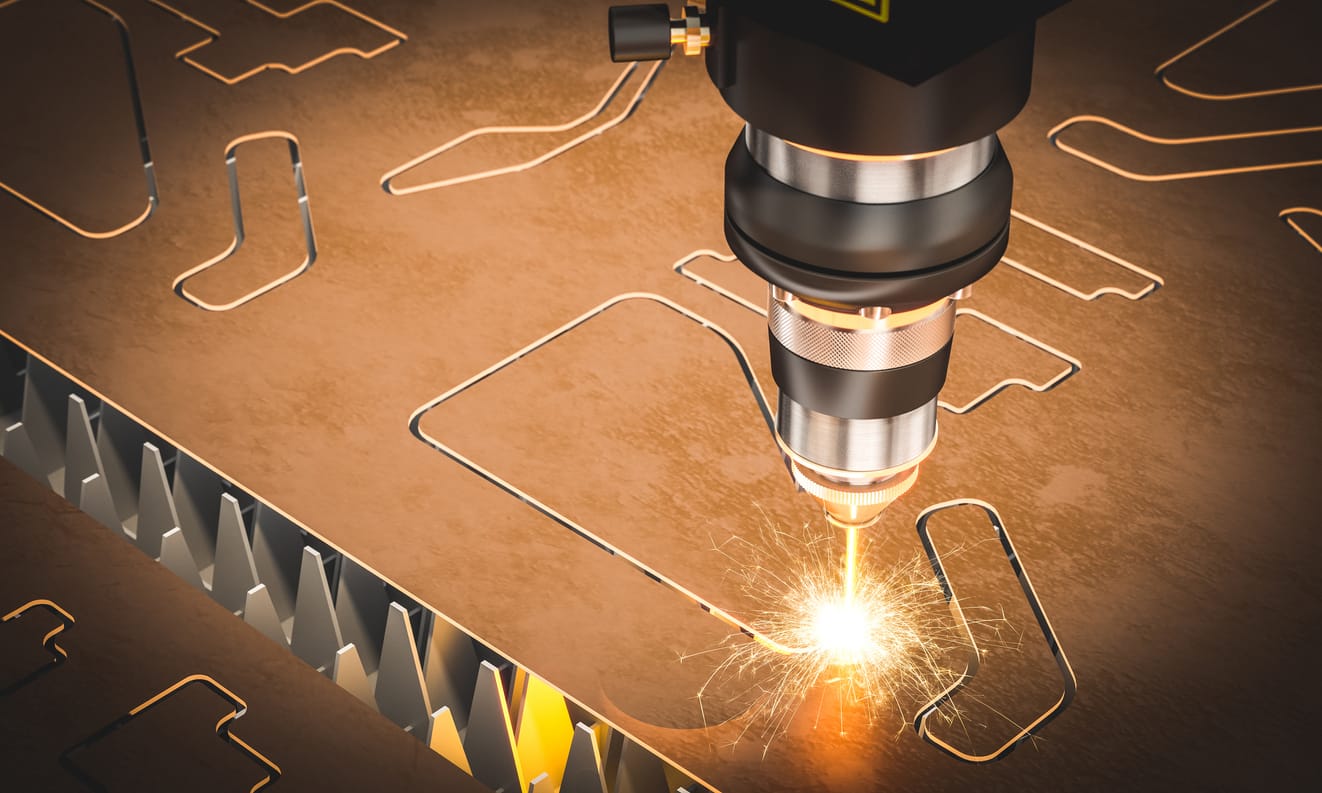
What is the cutting process?
Cutting is often associated with metal machining; however, cutting wood or other material can also be attributed to this process. In 2016, the global market for CNC metal cutting machines was estimated at $5.99 billion. By 2025, specialists expect the market to reach $105.3 billion, with a growth of 6.5% per year.
What are the cutting methods?
Cutting is a set of operations in which the material is brought to a specified geometry. Different types of tools are used to remove excess material and obtain a finished product. Various techniques are employed to cut metal, such as manual (saw), machine (milling, drilling), welding (laser), erosion (water jet), or chemical technologies.
- Milling is done using a machine tool whose cutter rotates around the spindle axis (like a drill) and a work table that can move in several directions. Milling machines can perform many complex operations, such as slotting, planing, drilling and threading, grooving, routing, etc.
- Turning: the workpiece is rotated on a spindle, and the cutting tool is inserted radially, axially, or both. Among the objects produced on a lathe are spark plug holders, crankshafts, camshafts, and bearing supports.
- Threading consists in creating a screw thread. It is used when a complete thread depth is required, for example, when the blank is not very precise or when the material is fragile.
- Grinding involves an abrasive process, utilizing a grinding machine as a tool. This produces excellent finishes, light cuts, or high-precision shapes well suited to aerospace and other applications.
- Filing is mainly employed for finishing operations, i.e., in deburring operations.
There are also other cutting methods such as electron beam machining in which high-speed electrons are directed at a part, creating heat and vaporizing the material, or ultrasonic machining which uses ultrasonic vibrations to fabricate very hard or fragile materials.
The different types of CNC cutting
1. Blade cutting
A saw is a tool consisting of a blade, wire, or strong chain with a hard toothed edge. Most blade teeth are made of tool steel or carbide. Carbide is more rigid and holds a cutting edge much longer. The saw is commonly used to cut hard materials, especially wood and sometimes metal or stone. An abrasive saw has a motorized circular blade designed to separate metal or ceramics.
2. Laser cutting
Laser cutting is employed to prepare workpieces, including drill holes for the riveting process. This method allows parts to be assembled using rivets, which provide permanent fixation. Laser welding is utilized as a final assembly technique to achieve the strength and endurance essential for rail vehicles, for example.
This technology uses a laser to slice materials. The process involves directing the output of a high-power laser, usually through an optical system. The laser beam is directed onto the material, which melts, burns, and vaporizes. A gas jet may also blow it away, leaving an edge with a high-quality surface finish.
The world market for laser cutting machines generated a $3 billion turnover in 2015 and will reach $5.7 billion in 2022.
3. Water cutting
A water jet cutter can cut a wide variety of materials using a very high-pressure water jet or a mixture of water and an abrasive substance. The term abrasive jet machining refers explicitly to the use of a mixture of water and abrasives to cut hard materials such as metal or granite, as opposed to pure water jet or water-only jet cutting. These techniques are used for softer materials such as wood or rubber.
The manufacture of machine parts makes particular applications of water jet cutting. This method is ideal when the materials to be cut are sensitive to high temperatures. This process is used in various industries, including mining and aerospace.
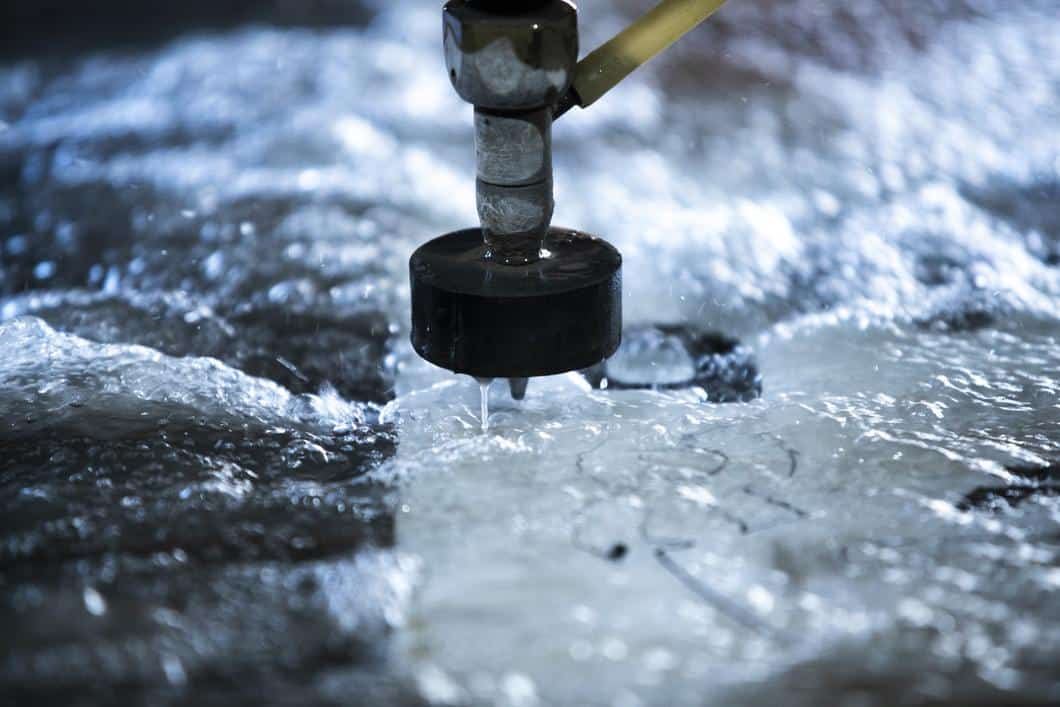
Which material to choose for cutting?
Cutting is a technique that separates an object into a minimum of two parts, following the action of a force-directed with extreme precision. In industry, we find cutting processes by blade, laser, or water jet.
Metal, an Optimal Material for Cutting
Due to its natural rigidity and thermal resistance, metal remains a simple part to cut, as it withstands deformation. By metal, we mean aluminum, stainless steel, mild steel, alloy steel, tool steel, or brass.
We generally cut metal according to different processes:
- the production of chips, better known as machining. Drilling a hole in a metal part is the most common example. This can be done manually (saw, metal shears) or with CNC machines (turning, milling, drilling, grinding, sawing), or electrochemically, such as electroerosion machining;
- burning during which oxidation separates the metal fragments. For example, a flame-cutting torch that divides a steel plate into small pieces. This may involve welding or burning techniques such as laser or plasma cutting;
- various specialization processes that do not fall into one of the above categories. This is the case of chemical milling, which allows excess material to be removed by the use of etching and masking chemicals, similar to erosion methods such as water jet cutting.
Each method has its limitations in terms of accuracy, cost, and effect on the material. In particular, heat can damage the quality of heat-treated metal alloys, and laser cutting is less suitable for highly reflective materials such as aluminum.
Plastic, a Common Material
Plastics are still very present in the industrial and consumer world, mainly due to their chemical resistance and electrical insulation properties. Thermosetting plastics are generally preferred for cutting because they are consolidated by fibers such as glass-reinforced nylons, acrylic, or PEEK. Less rigid plastics tend to deform and bend when the cutter attempts to cut the workpiece.
As the plastics industry transforms and innovates, creating more exciting products for consumers to buy, it continues to use some of the best technologies to work with this new material, such as:
- die-cutting, either manual or automated;
- hot knife cutting for the softest materials. For example, blocks of foam and expanded polystyrene;
- punching for the thinnest thermoplastic and thermosetting foils;
- water jet cutting for fiber-reinforced thermoset components, which would be difficult to separate by other processes;
- laser cutting and drilling of certain types of acrylic and other plastics, but not thermosetting. The industrial laser, controlled by a computer, melts the plastic in most cases.
- Ultrasonic cutting for thinner, softer plastics. The high frequency generated by the ultrasound of the tool has the effect of melting the material locally.
Composite, the Challenge of Precise Cutting
Composites are made up of several materials with different physical and chemical properties, which, combined together, make a stronger, lighter, or more flexible product. Examples include reinforced plastic, carbon fiber, graphite-reinforced materials, fiberglass, or resin.
Composites are cut using such technologies:
- water jet cutting uses a hyperbaric water jet. Cutting can be done with pure water, for composites separated with a cutter, or with abrasive water, for all other parts;
- Laser cutting slices the material using a large amount of energy generated by a laser and concentrated on a tiny surface. The laser can be pulsed or continuous (CO2 or nitrogen laser).
Which industries use cutting processes?
The global automotive, aerospace, medical, energy, and electronics industries, among others, cannot do without cutting equipment, with its many advantages and varied uses. Today’s techniques offer a new level of quality and reliability thanks to technologies such as laser or waterjet cutting.
The Aerospace Industry
Laser cutting is very applicable in this field. However, unlike the automotive sector, everything has to be done on a much larger scale, and products must withstand much more pressure. As a result, the processes involved must be even more precise and reliable.
To design jet engine and turbine blade components, we can use waterjet cutting, as well as composite materials for aircraft. Indeed, high-pressure water combined with an abrasive water jet makes extremely precise cuts necessary for aircraft fuselage, tail, and wings, or even rotating blades.
The Automotive Industry
The automotive industry uses water jet cutting to make headliners, door panels, and carpeting. The machines create smooth, flat, and deburred surfaces, even when the materials are not uniform, leaving no rework.
Automobile manufacturers may prefer laser cutting for very small and complex parts and components, such as openings for antennas. This technology can also be used to cut materials such as fabric for airbags. By melting the edges at a very high speed, no fraying remains. The laser can also cut composites, which is useful for interior parts.
The Food Industry
Water jet cutting has significant time-saving advantages that are very precious to the food industry. There is no need to change knives or sharpen the blades since the cutting is done with pure water. This technology has enabled bakeries to double their output. The absence of blades promotes a healthy, sanitary cutting environment without the risk of contamination. In addition, the machine tool is easy to use, which promotes its democratization. Its fineness of cut has thus become widespread in the sector and brings added value to products whether fruit or vegetables, meat or pastries.
The Electronics Industry
As the world becomes more and more digital and technological, there is a growing need to develop electronic parts and products. As technologies progress, electronic objects become smaller and smaller, for example, computers or smartphones. Products adapt, as do manufacturing processes. Laser cutting is used primarily because of its ability to segment tiny and complex parts.
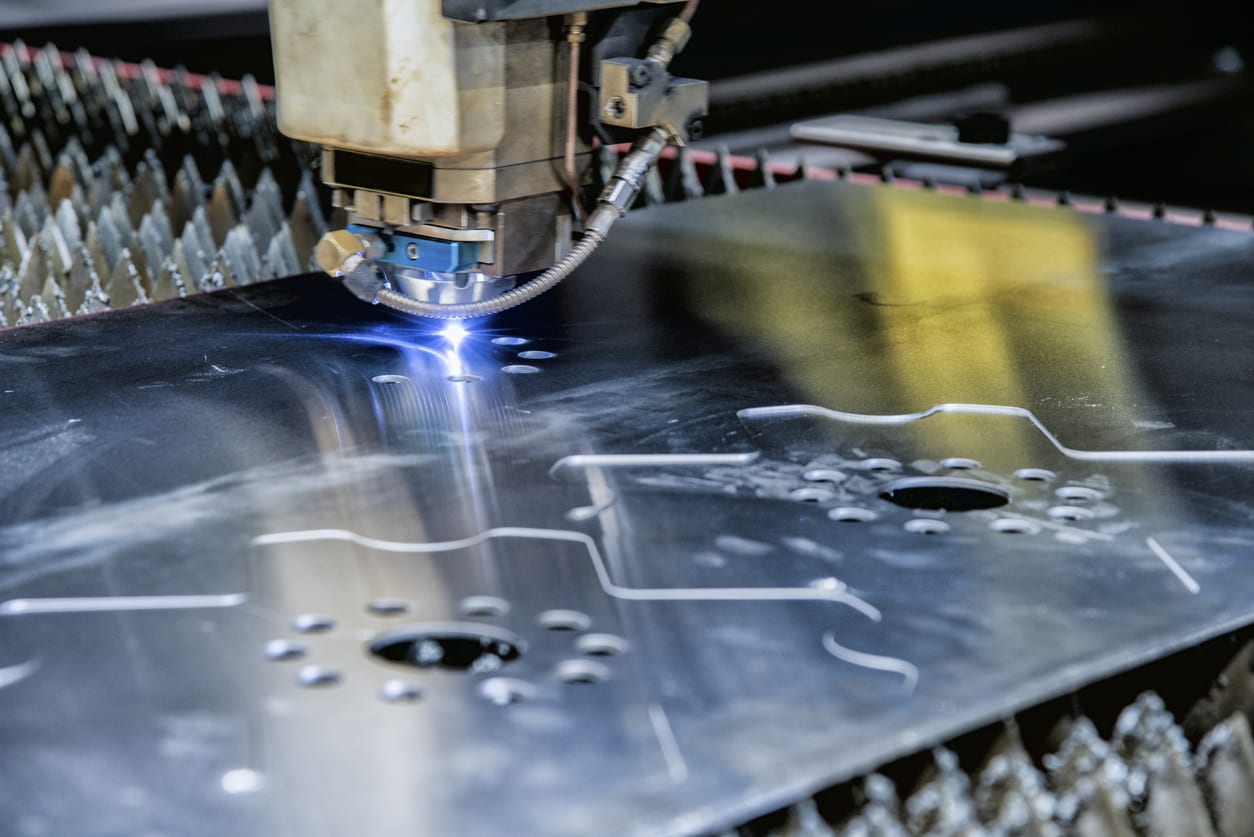
Get multiple quotes for your parts in seconds