Lean Manufacturing Essentials: What You Need to Know
Lean manufacturing uses the principles of lean to minimize waste and maximize productivity. Learn how you can harness the power of Lean manufacturing to enhance your business processes.
What is Lean manufacturing?
Manufacturing companies face a wide range of challenges. One of the most critical is how they can make the most of their available resources to avoid waste and maximize productivity. Lean manufacturing is a system of analyzing manufacturing processes using the core principles of what is known as Lean philosophy, also called Lean management, or even more directly, Lean.
The core Lean management principles
A Lean management system is designed to remove waste, cut down on overall operating costs, enhance innovation, and boost production levels. The Lean principles enable better collaboration across all levels in a company, can optimize production processes, reduce time to market and help you make the most of your workforce’s skills.
Lean methodology – a definition
So, what are Lean management and Lean manufacturing exactly? Lean is a methodology that was first developed by the Toyota automotive company in the 1940s. The basic idea behind Lean management principles is to focus on every process that adds value and remove any process that does not add value. With Lean methodology, an emphasis is placed on the need for continuous improvement. Lean techniques also place a focus on obtaining input from personnel at every level, from the factory floor to the boardroom. In this way, optimum methods of production can be identified and implemented.
Discover Dassault Systèmes store solutions for Lean management
Take your team to the next level with Delmia Lean Team Player Dassault Systèmes. Delmia Lean Team Player is a widget-based web app that provides you with a modern, interactive cloud environment where your team can communicate, collaborate, and innovate easily and securely.
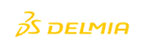
DELMIA Lean Team Player
Make collaboration effective, intuitive and easy with a cloud-based whiteboard designed to fuel innovation
What is the difference between Lean management and Lean manufacturing?
When considering any type of Lean-based methodology, it is important to understand that while the implementation can differ, all Lean techniques derive from the same underlying philosophy. Lean thinking, in essence, is about continuously striving to add value and maximize productivity.
At first glance, you may not recognize the difference between Lean management and Lean manufacturing. However, there is a distinction between these two Lean strategies.
Lean management is focused on senior management and business leaders committing to implementing a system of attaining excellence via continuous improvement. Lean manufacturing places the focus on continuously assessing processes to remove waste and enhance operational efficiencies across the board.
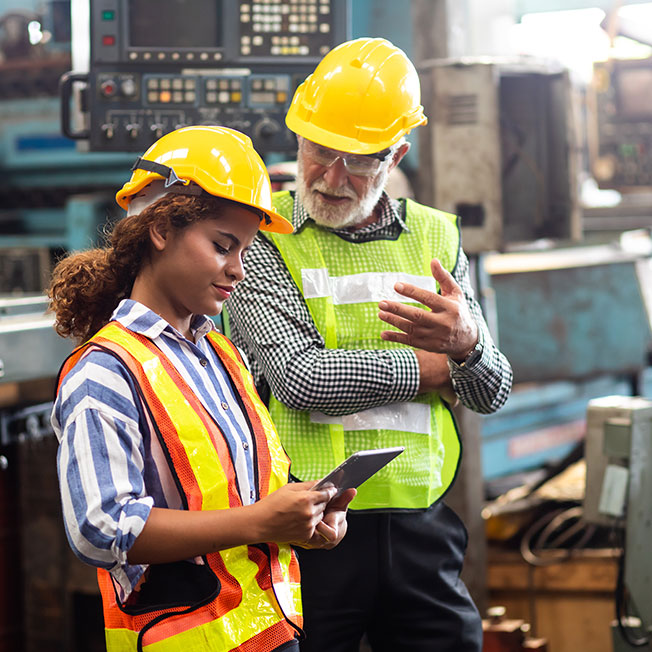
What is the difference between traditional and Lean manufacturing?
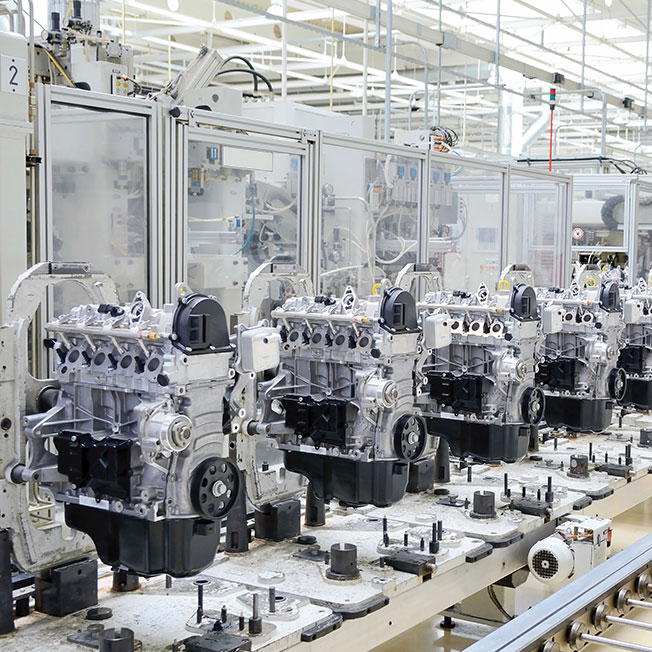
There are significant differences between traditional and Lean manufacturing techniques. A traditional manufacturing system will be driven by sales forecasts, products are produced based on expected customer demand; this is known as push manufacturing, whereas Lean manufacturing is driven by actual customer demand, known as pull manufacturing.
In a traditional manufacturing system, problems are seen negatively, change is driven by management, systems are not changed if they are working, all work processes are standardized, and processes rely on workers not making mistakes.
Under a Lean manufacturing system, however, mistakes are viewed as opportunities for improvement, all employees are empowered to promote change, the focus is on continuous improvement, standardized processes can be updated, and processes are error-proofed to eliminate any chance of mistakes occurring.
Who invented Lean manufacturing?
The philosophy of Lean is usually credited to the Japanese automotive company Toyota. In the 1940s, Toyota developed and implemented a strategy known as the Toyota Production System.
The Toyota Production System came about due to the efforts of three men: Sakichi Toyoda, who came up with a waste elimination concept known as Jidoka, Kiichiro Toyota, who developed the concept of Just-in-Time manufacturing, and Taiichi Ohno, who integrated the Just-in-Time system with the principles of Jidoka. Under the Toyota Production System, the focus is placed on continuously developing value-added processes to remove waste and enhance efficiency.
However, the story of Lean did not start with Toyota. Lean principles can be traced back to the early 1890s when American mechanical engineer Frederick Taylor published The Principles of Scientific Management. Taylor’s book outlines many of the grounding principles of scientific management techniques.
Taylor’s writings inspired Henry Ford to create a revolutionary assembly-line strategy based on continuous production and waste reduction. Sakichi Toyoda, Kiichiro Toyota, and Taiichi Ohno were all heavily influenced by Henry Ford’s methods.
Today, Lean manufacturing principles are used by a wide variety of industries, including the aerospace sector, automotive companies, the electronics industry, and even healthcare and fashion companies. Major corporations such as Harley Davidson, the Ford Motor Company, Intel, and Nike are well known for implementing Lean methodologies.
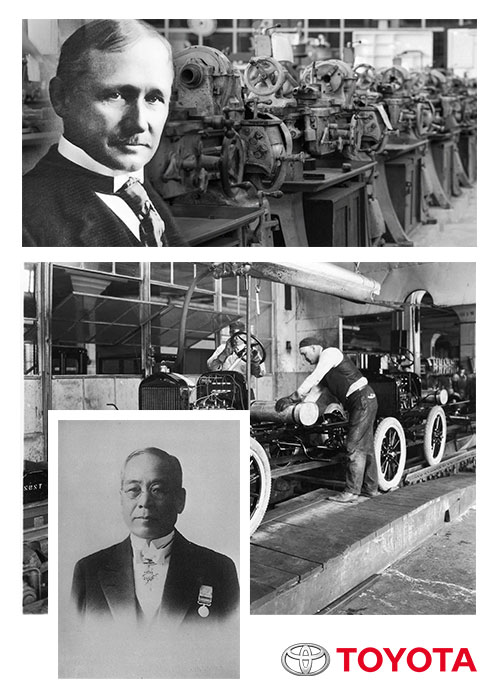
What are the tools of Lean manufacturing
Applying Lean manufacturing principles requires the use of a set of Lean tools that allow for the identification and elimination of waste. Common Lean manufacturing tools include:
5S system
A methodology that aims to enhance organization and productivity by focusing on five key principles: Sort, Straighten, Shine, Standardize, and Sustain.
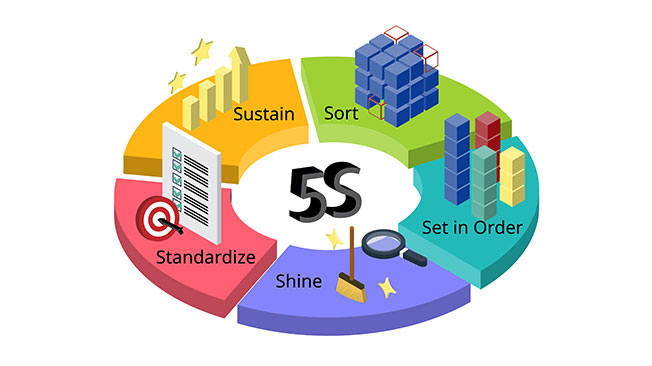
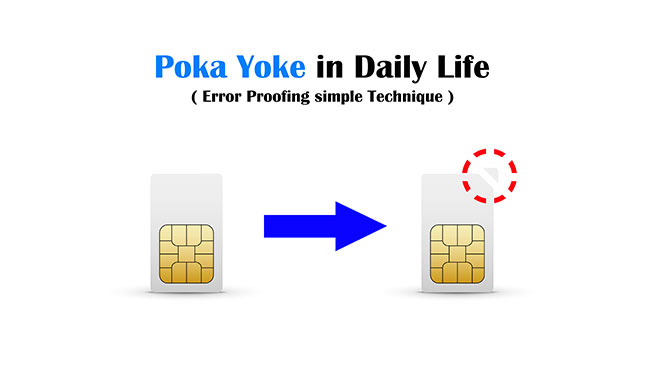
Poka Yoke
A Japanese phrase that translates roughly to ‘avoid unexpected surprises’, Poka Yoke is a system where errors are eliminated by ensuring that a set of conditions must be met before each step of a process can be completed.
Just-in-Time
The just-in-time manufacturing model involves producing goods in response to demand, rather than creating an excess inventory or producing them beforehand.
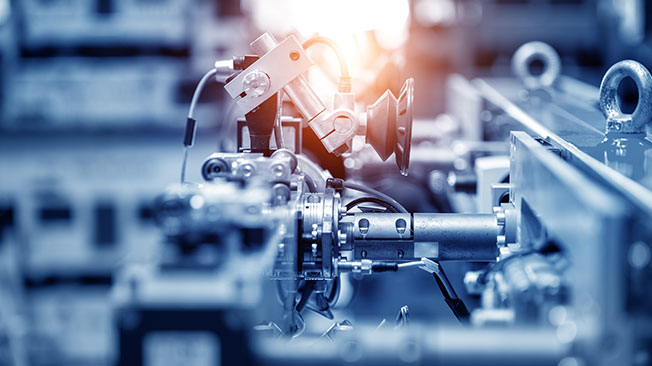
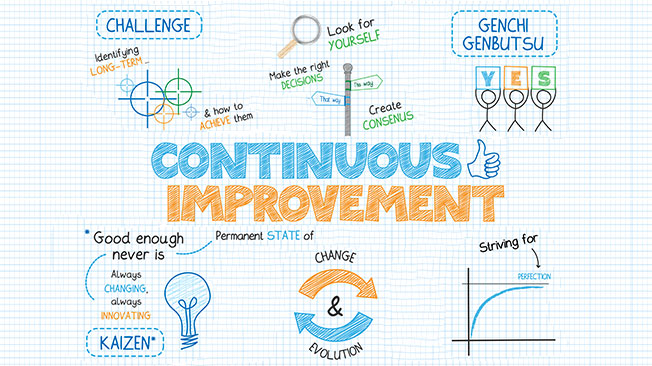
Kaizen
The Kaizen philosophy is based on focusing on making small ongoing changes to attain continuous improvement.
Total Productive Maintenance
Also known as TPS, this system focuses on ensuring that manufacturing machinery and processes are always kept in optimal condition.
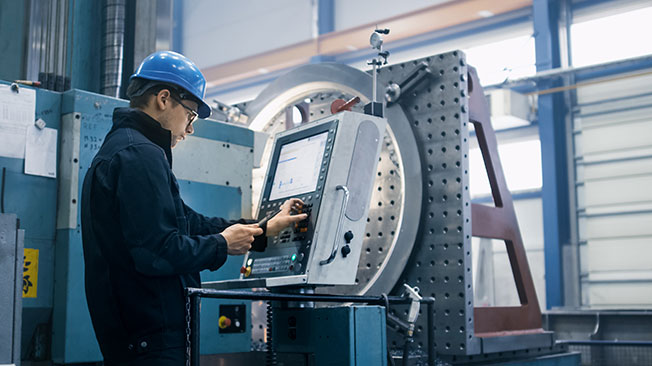
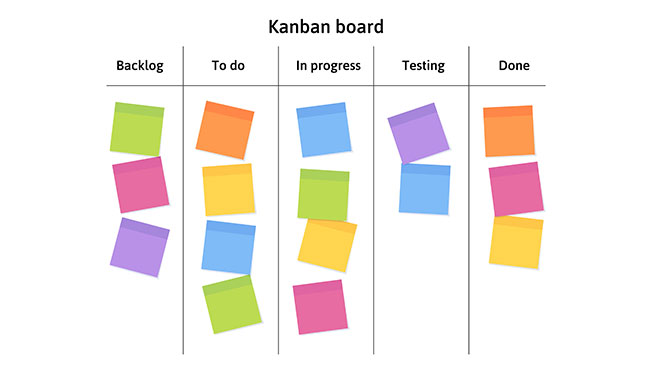
Kanban
The Kanban system is a well-known Lean management technique that works in conjunction with Just-in-Time methods to improve and manage workflows.
What are the five principles of Lean manufacturing?
- Customer-Value
- Value Stream Mapping
- Creating Flow
- Implement a Pull System
- Focus on Continuous Improvement
Customer-Value
Focus on what is valuable for the customer. Optimize your processes to remove anything that does not add value for the customer.
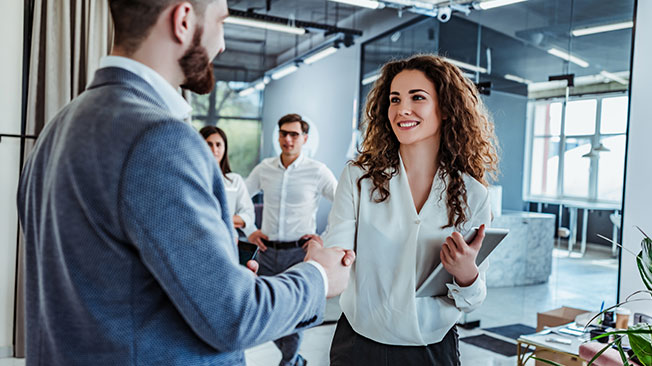
Value Stream Mapping
Maximize value and minimize waste by visualizing each step in the production process and identifying waste and opportunities for improvement.
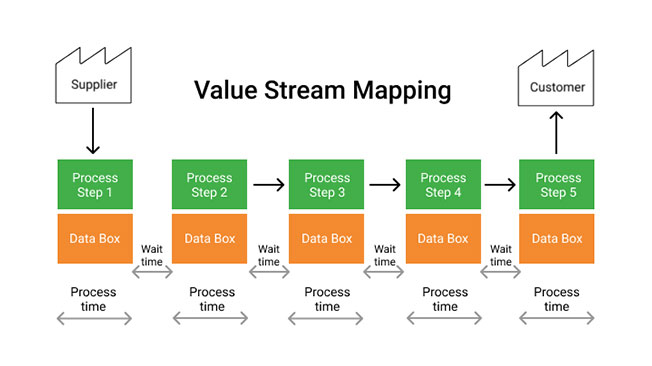
Creating Flow
Remove all barriers to ensure that cycle time is optimized and that processes flow smoothly.
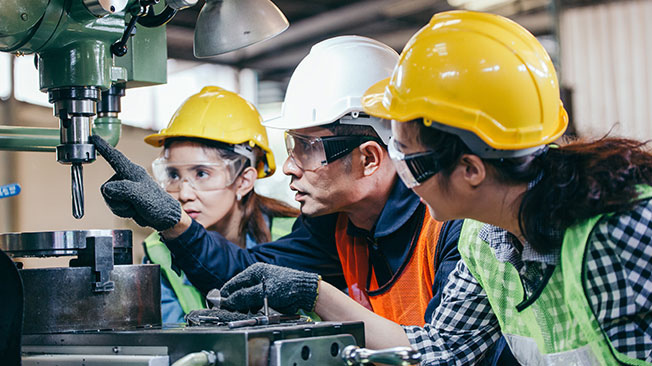
Implement a Pull System
Operate on a Just-in-Time basis where production is based on actual customer demand.
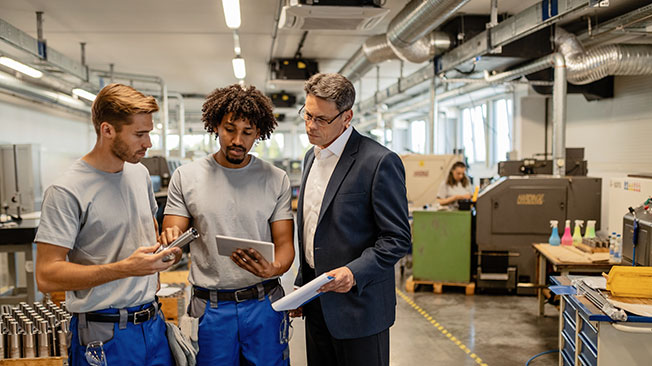
Focus on Continuous Improvement
always strive to find areas to eliminate waste and improve efficiency.
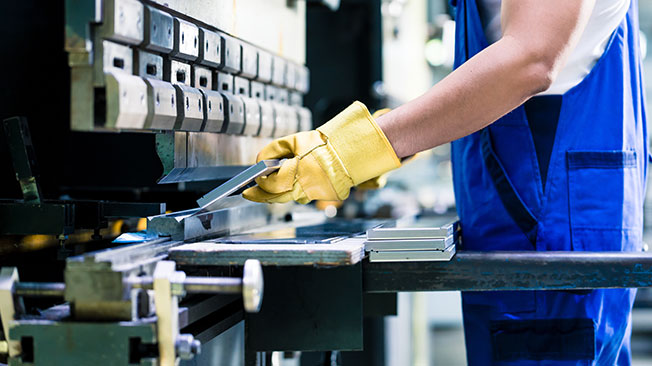
Browse all the Dassault Systèmes store applications
We feature in our store some of our best software to design, collaborate and innovate throughout the entire product lifecycle.
Content related to Lean management
What are the seven wastes in Lean manufacturing?
Waste can be a complicated concept to grasp. To make it simpler to recognize waste, Toyota’s Taiichi Ohno developed seven types of waste to avoid:
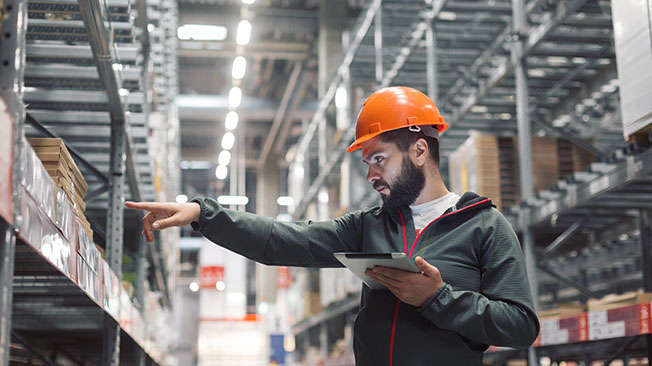
Excess Inventory
Inventories must be kept to a minimum. This helps to identify defects and minimize lead times.
Inventory means raw materials, work-in-progress, and finished goods that are not immediately needed. Excess inventory can lead to waste due to increased carrying costs, obsolescence, and increased lead times. In addition, excess inventory can hide quality issues and defects, making it more difficult to identify and correct problems.
Wasting Time
There should never be idle workers or equipment that is not being used.
Time is a precious resource in Lean manufacturing. Wasting time occurs when workers or equipment are idle and not contributing to value-added activities. This can be due to inefficient processes, poor scheduling, or inadequate training.
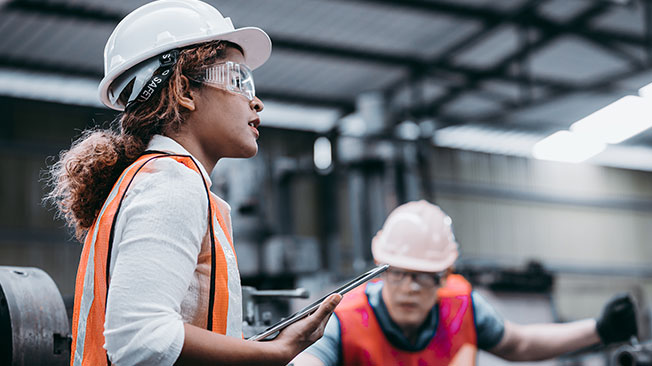
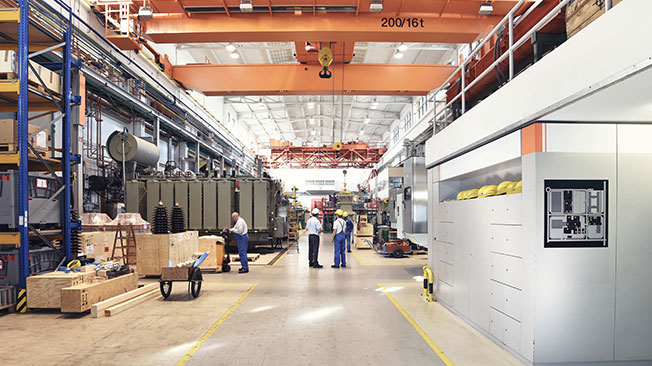
Motion
Unnecessary motion refers to any movement of machinery, equipment, or workers that does not add value to the product. Examples of unnecessary motion include excessive walking, reaching, or bending.
Transportation
Transportation waste are unnecessary movement of goods, equipment, or people. This can be due to poor factory layout, inefficient processes, or lack of coordination between departments.
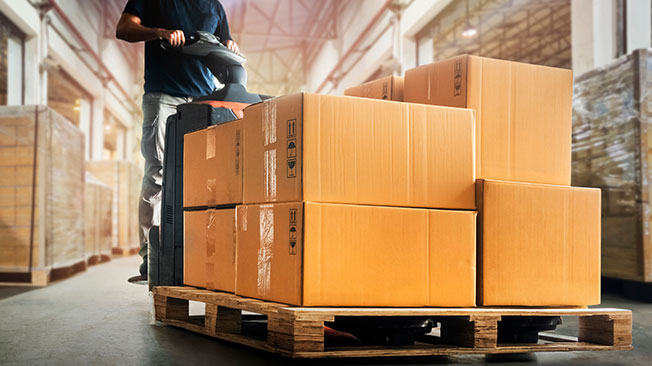
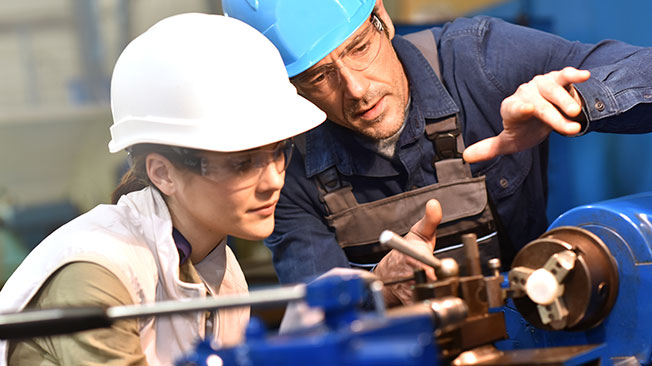
Defects
Defective products cause waste and must be eliminated.
Defects relates to errors or mistakes that result in scrap, rework, or customer complaints. Defects can be caused by poor quality control, inadequate training as well as design flaws.
Over-processing
Products should have only the features that add value to the customer.
Over-processing are any activites that adds cost but does not add value to the product. This can be due to over-engineering, excessive inspection, or use of high-cost materials.
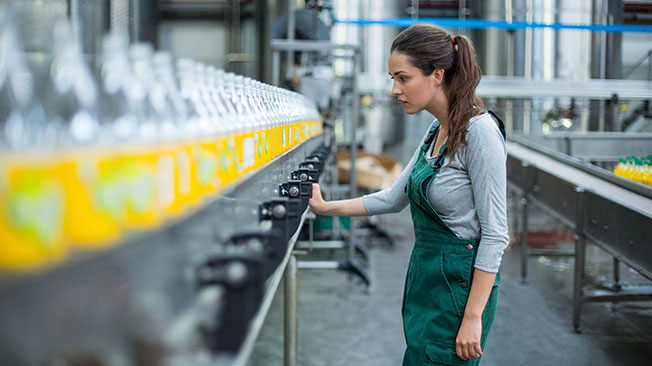
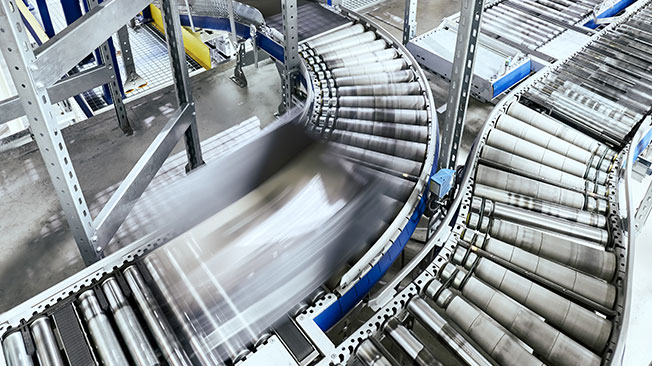
Overproduction
Companies should implement Just-in-Time processes to ensure they produce only what the customer demands.
Overproduction occurs when a company produces more than what the customer demands. This can lead to excess inventory and increased costs. Just-in-Time (JIT) production is a Lean technique used to minimize overproduction by producing only what is needed, when it is needed, and in the quantity needed.
Challenges of Lean manufacturing
Changing to a Lean manufacturing model is not an easy process. It will not happen overnight or even in a matter of weeks. It takes considerable time to fully implement an optimal lean manufacturing strategy. There may be inherent organizational resistance to change. Lean principles can represent a major cultural shift and some workforces may be opposed to adopting them. It can be complicated to implement the new technology required for a lean system. Many companies find it hard to properly identify bottlenecks in their old processes. Once a Lean system is in place, it can be hard to properly maintain the improved systems.
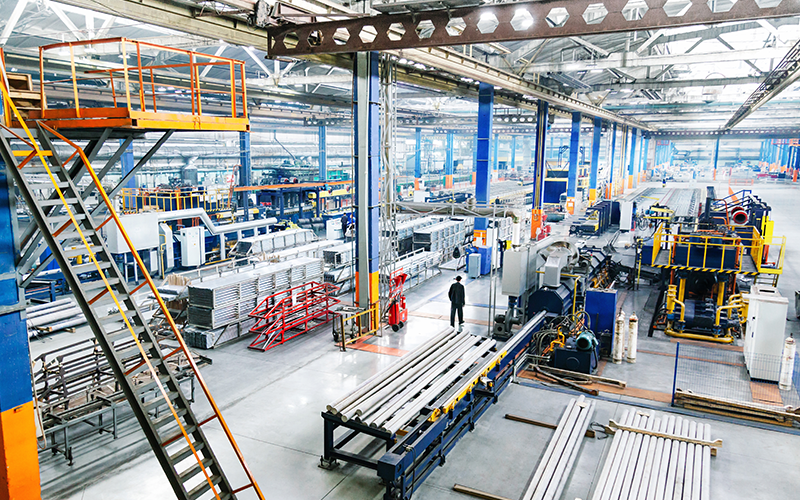
Find out how the Dassault Systèmes solutions for Lean manufacturing can meet your needs
Maximize your efficiency, enhance collaboration, and make sure you get the most from your team with the Lean management software solutions from Dassault Systèmes. All of our innovative software can be accessed via the powerful cloud-based 3DEXPERIENCE platform.
- Project Planner
- Delmia 3D Lean Team Player
- 3DSwymer
Project Planner
Stay on top of every detail of your next major project.
Learn more
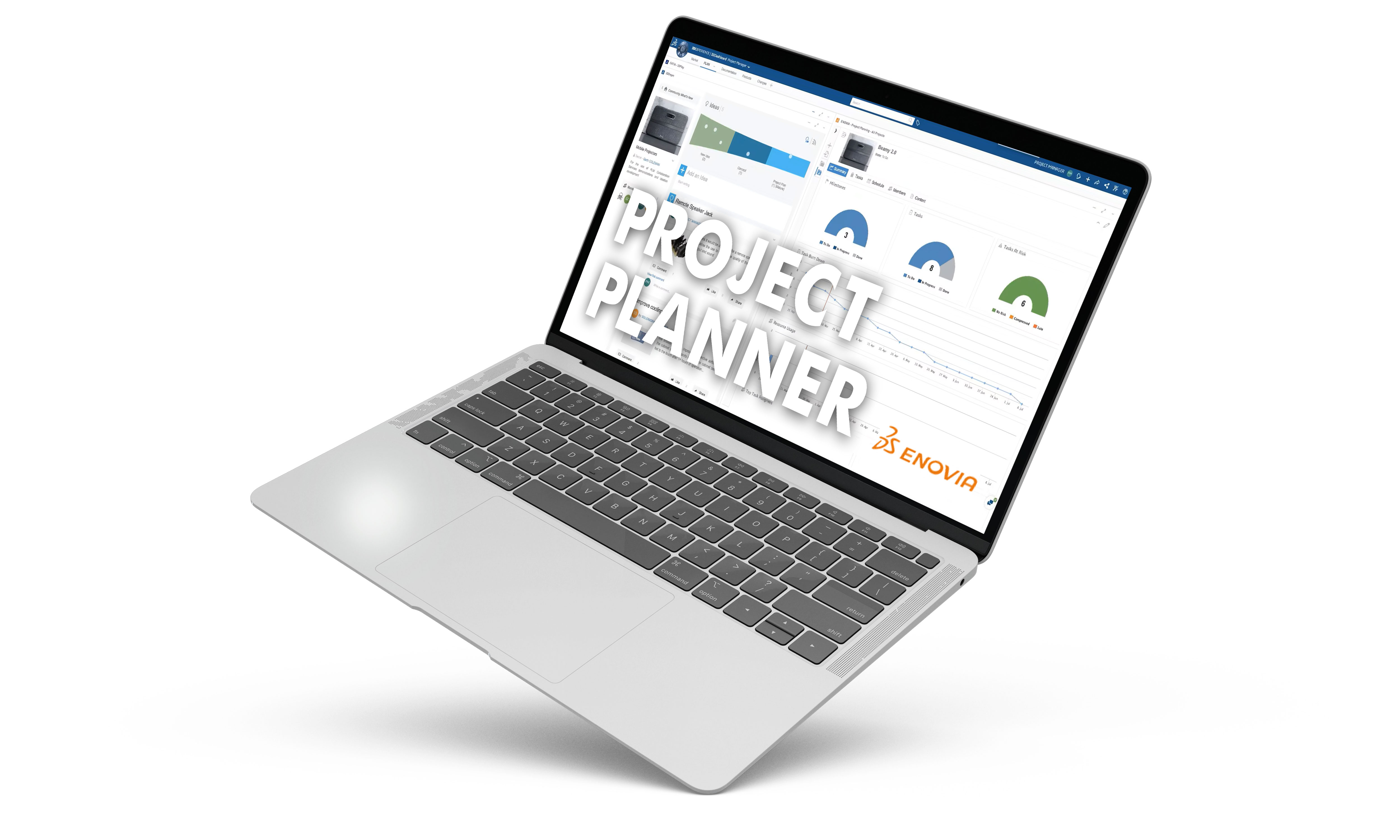
Delmia 3D Lean Team Player
Enable effective communication between team members.
Learn more
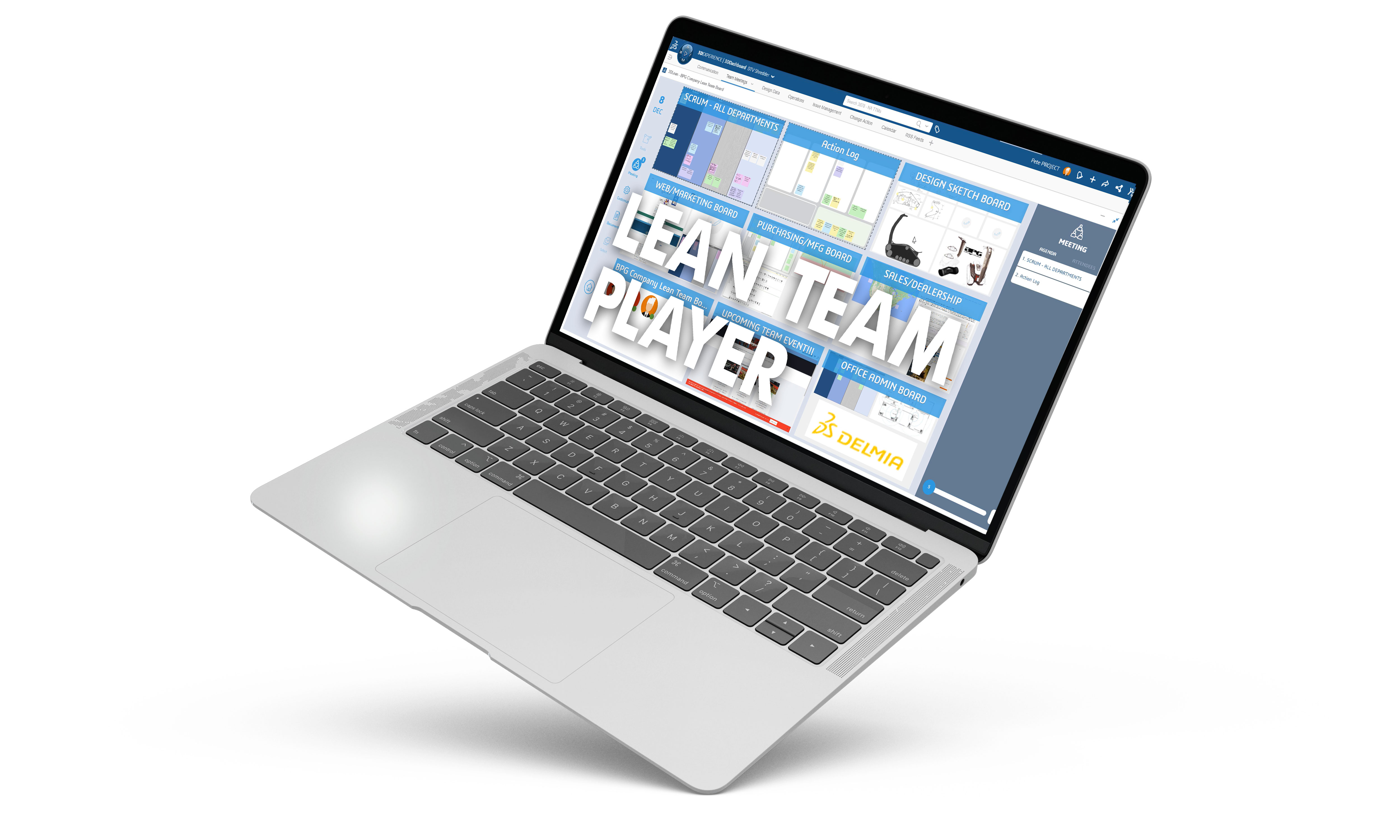
3DSwymer
Connect stakeholders, manage groups, and engage your customers.
Learn more
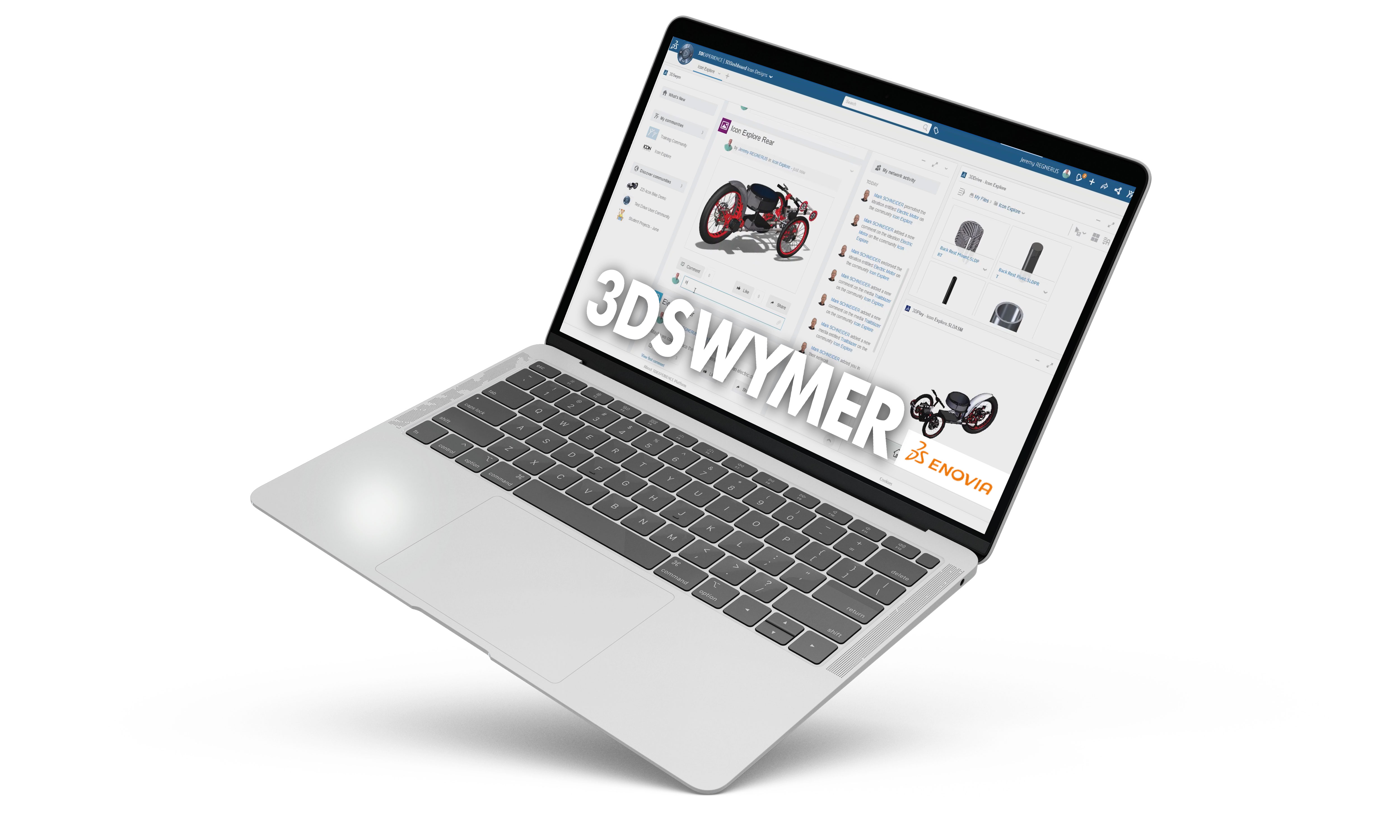
Lean manufacturing - Conclusion & Perspectives
Lean manufacturing processes in combination with Lean management tools can provide companies with powerful methodologies to enhance efficiency and boost production.
The waste elimination aspects of Lean manufacturing techniques can reduce overheads and dramatically improve productivity. Incorporating Lean daily management techniques such as the Gemba walk can raise morale and ensure that all possible ways of optimizing processes are identified.
Lean cost-reduction principles and the Lean philosophy of continuous improvement are used by top multinational corporations. However, any enterprise can utilize Lean manufacturing and Lean management techniques to become more agile, more dynamic, and more profitable.
Why choose Dassault Systèmes for your Lean manufacturing needs?
Use the power of the 3DEXPERIENCE platform to enhance your business
Collaborate with team members at any time, on any device, regardless of where you or they are located. Access a huge range of powerful software solutions from Dassault Systèmes. Get massive computing power with cloud technology. Save money, enhance your agility, and eliminate the constraints of traditional IT infrastructures. All this, and more, is possible with the 3DEXPERIENCE platform.
The 3DEXPERIENCE platform is a revolutionary concept in lean management, PLM, and CAD software. You can communicate with your people, via one secure digital environment and gain access to our unique applications to grow your business. Eminently scalable and incredibly flexible, the 3DEXPERIENCE platform gives you what you want, when you want it, without waste.
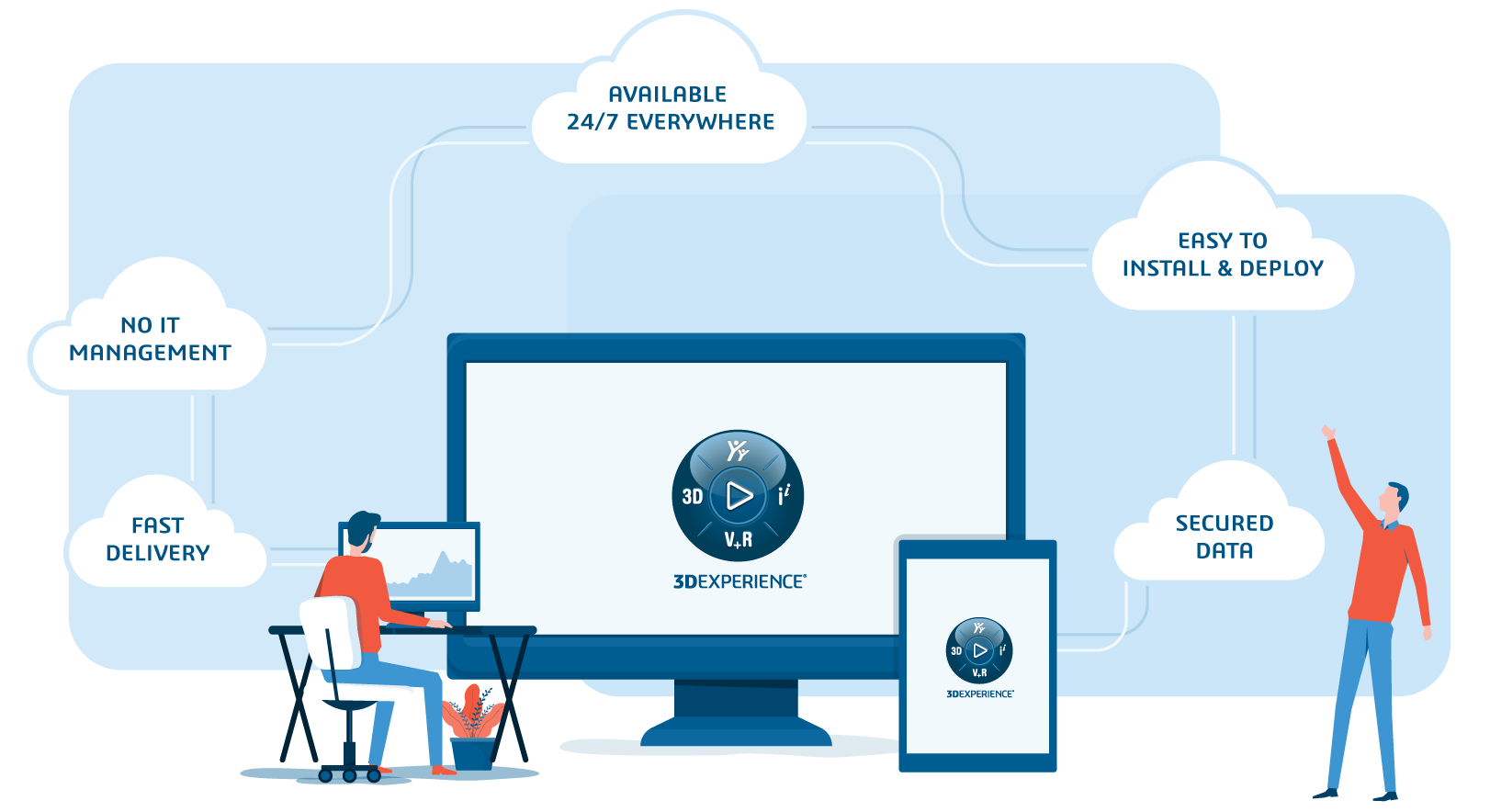
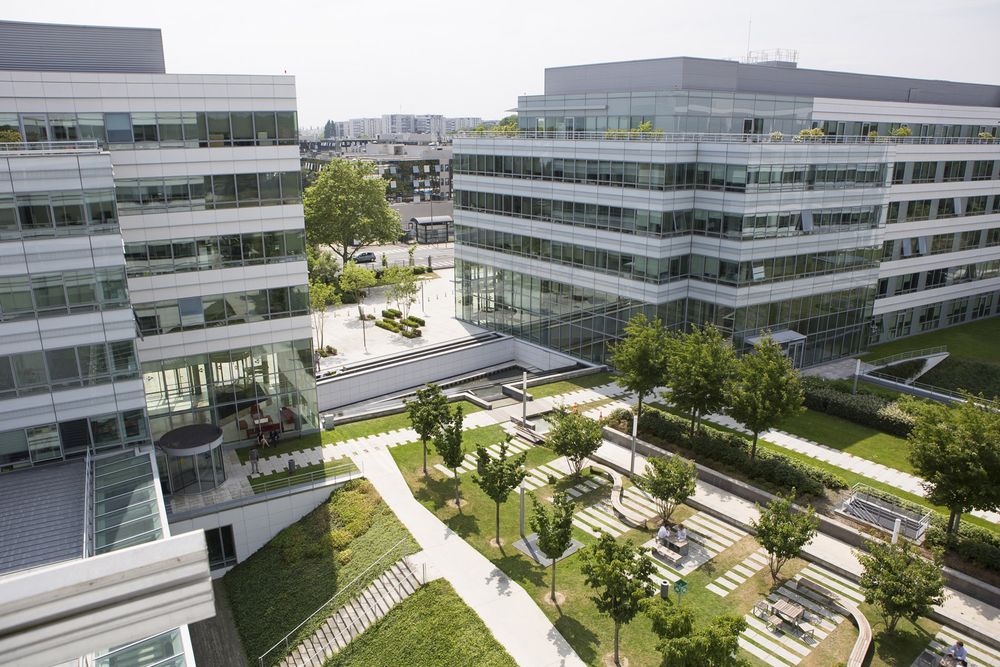
Complete Lean manufacturing software solutions
With roots in the aerospace industry, Dassault Systèmes is now one of the leading drivers of innovation in a wide range of sectors. Our suite of roles is used by major construction companies, leading architectural firms, healthcare conglomerates, and multinational manufacturers. Dassault Systèmes specializes in 3D design solutions, digital mockup (DMU) technology, product lifecycle management (PLM) software, and now offers you access to the revolutionary cloud-based 3DEXPERIENCE platform.