Using digital manufacturing in industrial production
Manufacturing companies of all sizes across a wide range of sectors are harnessing the power of cutting-edge computing to enhance and improve their operations. Join us as we discover just how digital manufacturing is transforming production systems across the globe.
What Is Digital Manufacturing?
Technology is intrinsic to every part of our lives. The impact of computing is not just seen in the products we use, but also in how we manufacture them. Increasingly, the same sophisticated computer systems that power our devices, our homes, and our vehicles are also used to manufacture them.
Companies are now applying powerful computing technologies to enhance their manufacturing operations. Using digital manufacturing solutions, manufacturers can link every aspect of their production systems, optimize their processes, speed up manufacturing times, and reduce overall costs.
But what is digital manufacturing exactly? And how is digitalization in manufacturing changing the face of the industry?
Direct digital manufacturing is often called the fourth generation in manufacturing referred to as industrial 4.0 technologies. In essence, digital manufacturing involves using complex computer systems and software to integrate every stage of the manufacturing process, from the design phase to the production stages right through to providing after-care services for consumers.
Discover the digital manufacturing solutions from Dassault Systèmes
Drive innovation and discover new ways of enhancing your manufacturing operations with the powerful direct digital manufacturing solutions from Dassault Systèmes.
How many different types of digital manufacturing are there?
Three types of digital manufacturing techniques are commonly used by companies across the globe. Each type of digital manufacturing relates to a different stage of the manufacturing process. Let’s take a look at three main ways that companies use digital manufacturing: Product life cycle, smart factories, and value chain management.
Product life cycle
By applying digital manufacturing techniques, companies can optimize the entire product life cycle, from the engineering design stage to sourcing, production, serving, and even after-sales customer service. Digital solutions make it simpler to iterate designs, calculate the need for raw materials, monitor production techniques, and provide services to customers.
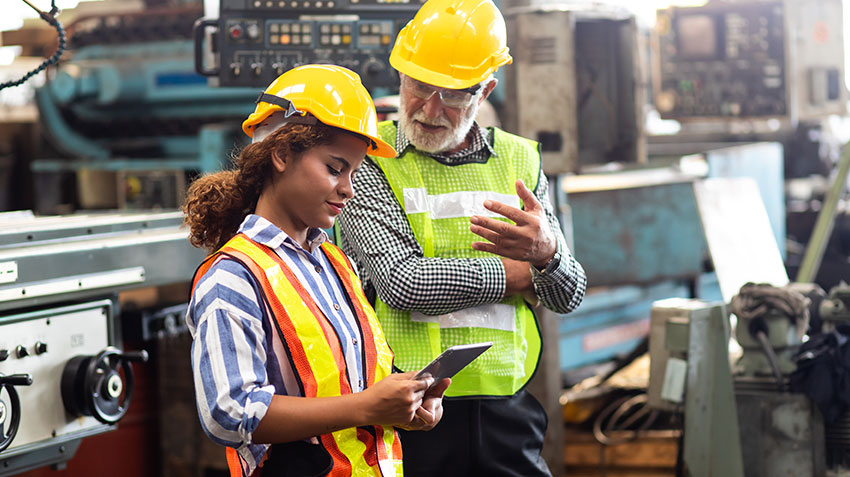
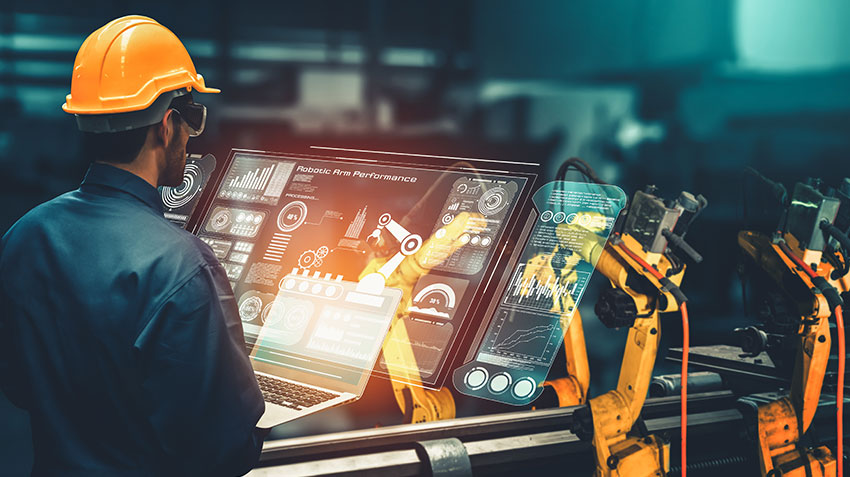
Smart factories
The 21st-century smart factory incorporates sensors, mobile devices, smart machines, and Internet of Things (IoT) devices to collect data in real time that can then be used to enhance the efficiency of the manufacturing process. Digital business intelligence tools allow for the precise analysis of production methods and give stakeholders the information they need to make decisions on how best to improve manufacturing operations.
Value chain management
Lean manufacturing and agile manufacturing techniques both involve scrutinizing every aspect of a production system to cut costs and maximize productivity. Digitization can help a manufacturing company create an effective lean and agile production system by providing data that evaluates every stage of the value chain.
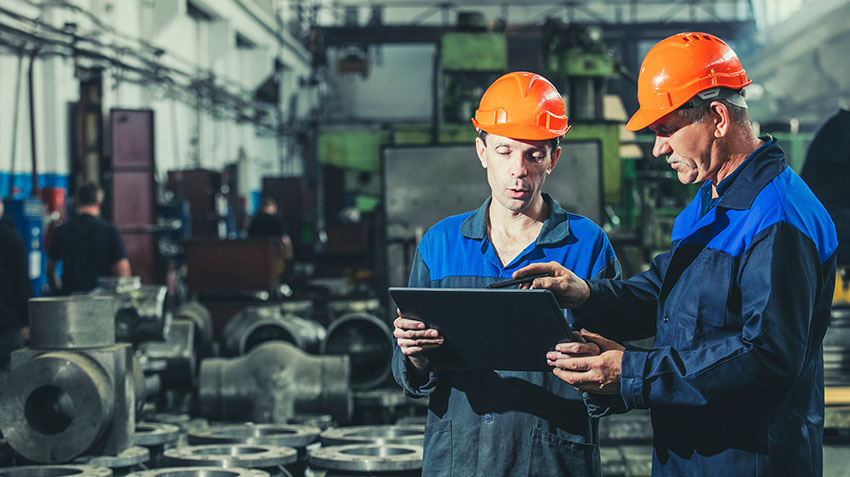
Browse all the Dassault Systèmes store applications
We feature in our store some of our best software to design, collaborate and innovate throughout the entire product lifecycle.
Content related to digital manufacturing
What are the key technologies used in digital manufacturing?
There are some cutting-edge technologies that are providing to be crucial drivers of how the digital revolution is continuing to transform manufacturing.
What are the benefits of digitalization in manufacturing for a business?
Focusing on digital manufacturing and design enables companies to achieve complete cohesion and streamlines every stage of the manufacturing process. Costs can be reduced by not only optimizing performances but also by eliminating previously wasteful methodologies.
The design stage is greatly enhanced by digitalization. CAD tools enable designers and engineers to produce highly detailed 2D and 3D models that can be used for showcasing proposed products and for simulation testing. Allowing for much of the product development and testing stages to be done in digital environments and negating the need to produce expensive physical prototypes. Design iterations can be done in less time and with more informed insights gained from big data analytical tools.
Companies can use digital lean manufacturing to reduce waste and increase efficiency during every phase of production. Activities that were previously paper-based and reliant on manual work can be automated, resulting in more precise and faster operations. Human error can be minimized or eliminated, and more control can be exerted over operations. Manufacturing also benefits greatly from digital twin technologies. Creating a digital shop floor allows companies to simulate their operations and then develop ways to better optimize processes.
At the end of the chain, customer satisfaction and loyalty can be increased as digital tools can provide greater levels of insight into what consumers want.
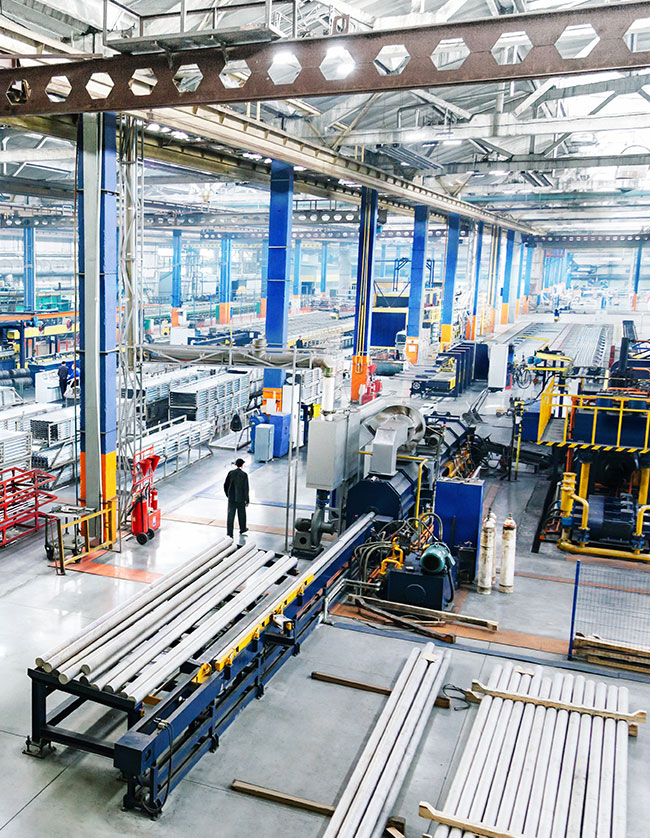
How has digital manufacturing evolved?
- The 1950s
- The 1990s
- The 2010s to today
- The future of digital manufacturing
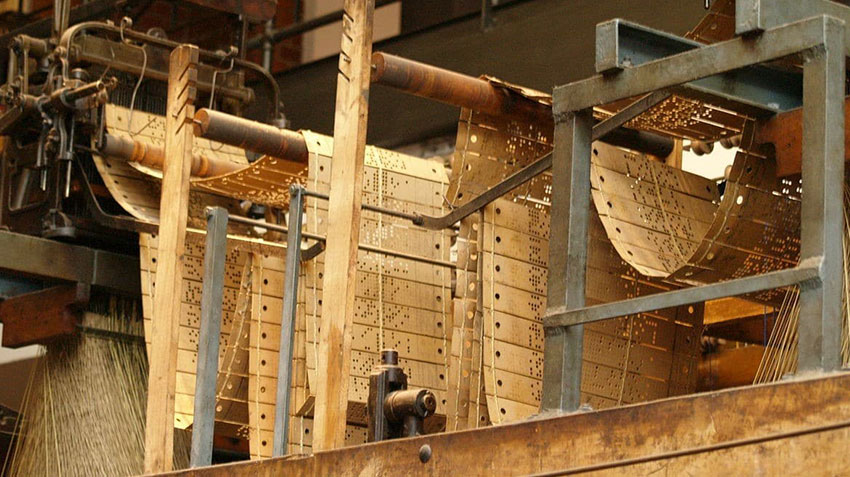
The journey toward industry 4.0 began in the 1950s with the advent of computerized numerical control (CNC) technology. Early CNC systems used machine tools that gathered instructions from punch cards. CNC was further developed by MIT who invented a programming language that automated numerical code instructions. This code is still used today and forms the basis of digital manufacturing.
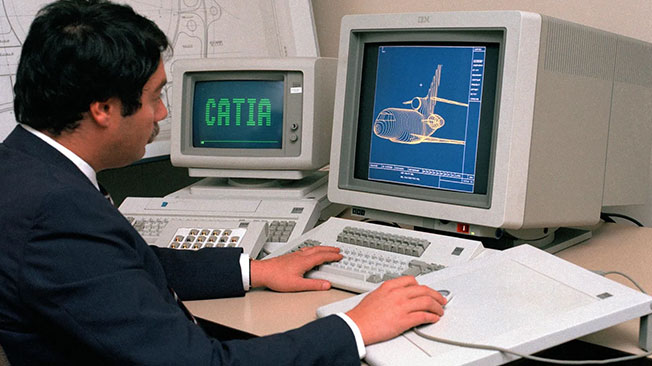
During the 1990s, digital manufacturing was pushed along by advances in CAD software. Designers and engineers could use CAD and PLM software to create 3D models that could then be used to provide manufacturing instructions for CNC machines.
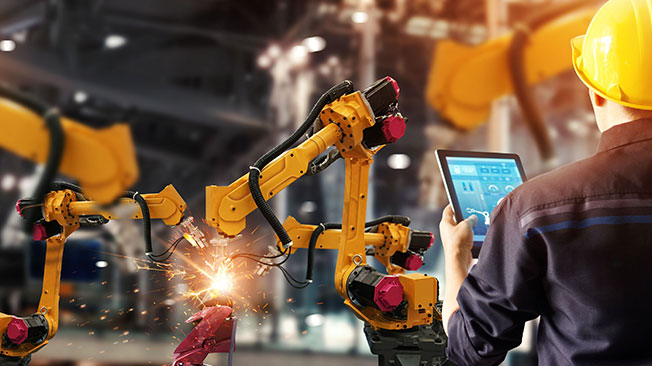
From the 2010s into the current day, digital manufacturing has advanced rapidly. New technologies such as artificial intelligence, augmented reality, machine learning, and IoT devices have delivered more agility, increased efficiency, and brought about new levels of productivity.
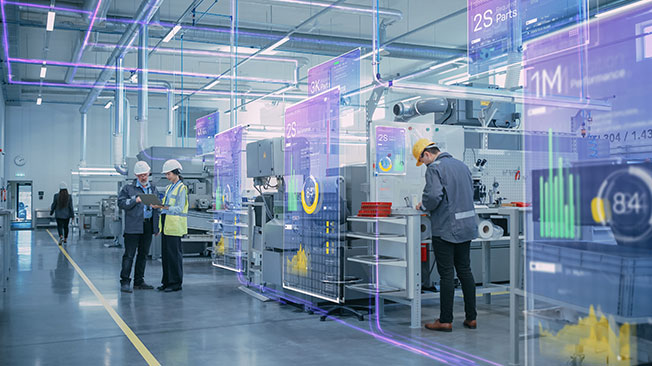
Artificial intelligence and machine learning technologies are currently entering a new phase of development. The implications for digital manufacturing are huge. More advanced robotics will result in increased automation and faster production times.
The ability of AI to generate thousands of answers to a single query will allow engineers and designers to develop ever more efficient means of production and more environmentally friendly products.
IIot and IoT will continue to advance. The means of production will use new IIoT technology to develop better manufacturing techniques. IoT devices will provide greater levels of insight into customer behavior.
What are the challenges and limitations of digital manufacturing?
It can be difficult for some companies to realize the full potential of digital manufacturing. A lack of internal IT skills, poor digital transformation strategies, fluctuating customer needs, and internal resistance to change can be impediments to making the most of digital manufacturing possibilities. Additionally, the costs involved in adopting a digital manufacturing process can be prohibitive.
However, with the right planning and corporate mindset, companies of all sizes can achieve an optimum return on investment from transition to a digital manufacturing model.

Digital manufacturing - Conclusion & Perspectives
Lean manufacturing and agile manufacturing techniques have been greatly enhanced by the use of digital manufacturing.
Because digital manufacturing can provide stakeholders with accurate data in real-time, more dynamic and responsive agile production manufacturing systems can be achieved. Areas of waste can be pinpointed, and solutions developed.
Design iterations can be produced and iterated in less time using fewer resources. Prototyping and testing can be done using 3D models in simulated digital environments, resulting in a shorter time to market, reducing costs, and encouraging innovation.
Lean and agile methodology in manufacturing is not the only area where digital manufacturing is having an impact. The customer is also better served by the new breed of digital tools. Companies can respond to consumer demand faster and collect more accurate data on what customers want and need from products.
Why choose Dassault Systèmes for your digital manufacturing needs?
Enhance collaboration and innovation with the 3DEXPERIENCE Platform
The 3DEXPERIENCE Platform represents a new development in how companies can work together to develop better ways of designing and manufacturing products.
Powered by cutting edge cloud technology, the 3DEXPERIENCE Platform allows you access to intuitive, effective, and powerful lean management and digital manufacturing tools such as Delmia Lean Team Player, Enovia Project Manage, and Enovia 3DSwymer. Using the 3DEXPERIENCE Platform, your team can collaborate, share and store files, and communicate with each other in any time zone, in any location, from any device.
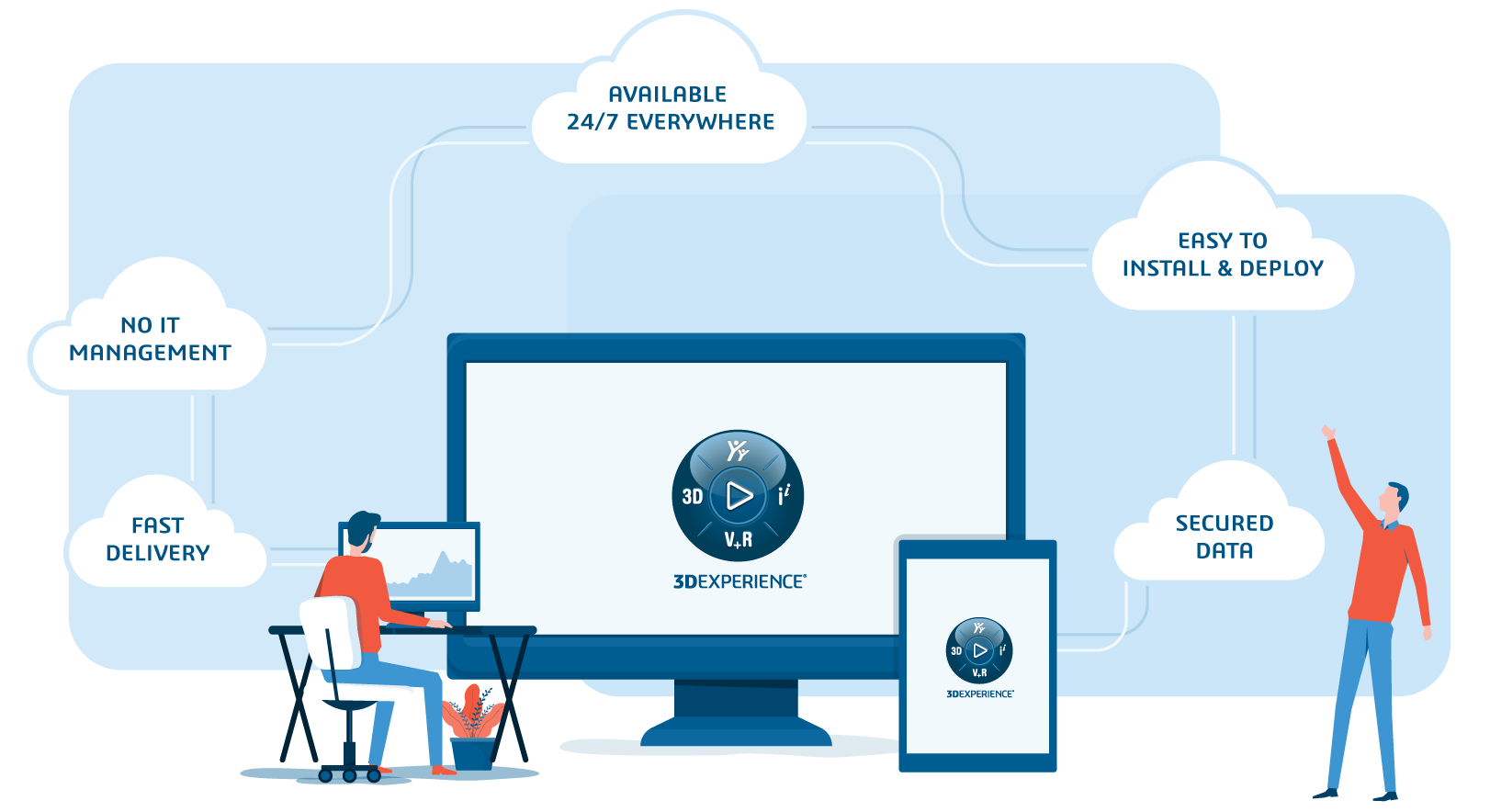
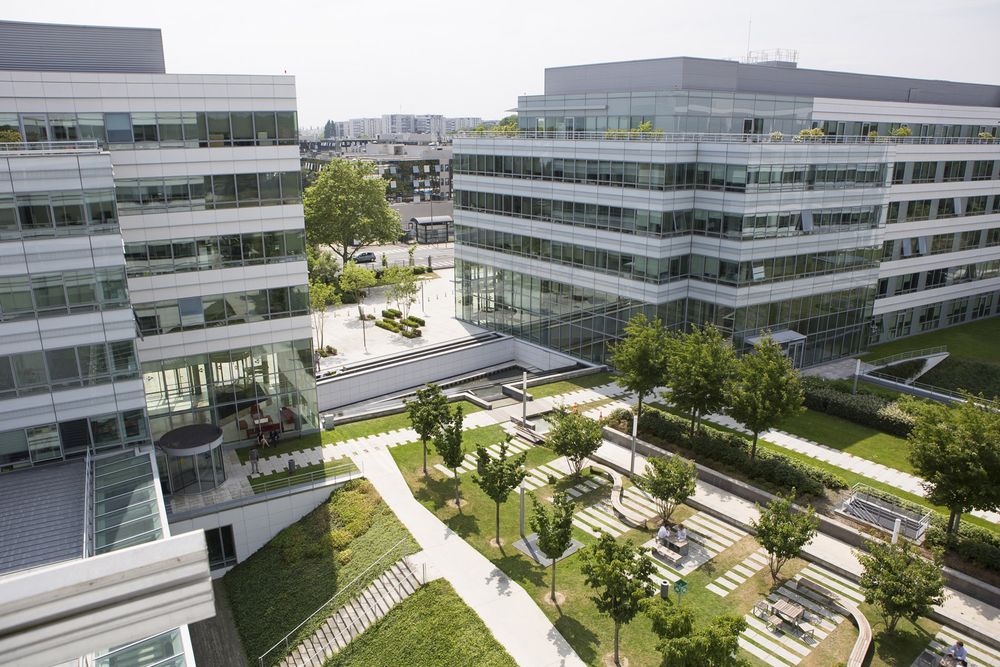
Discover powerful PLM solutions for all industry sectors
Many business leaders are resistant to taking up digital manufacturing techniques for reasons of cost, security, and simply being resistant to change. You can ensure the success of your move to digital manufacturing by partnering with a software development company with more than four decades of experience.
Top international manufacturers across diverse sectors such as the automotive industry, the construction industry, consumer product manufacturers, and the aeronautical industry rely on our PLM and CAD tools to streamline their operations.