Moulage par injection
Découvrez ce qu'est le procédé de fabrication moulage par injection et ses applications dans l'industrie.
Quelle est l’histoire du moulage ?
Le moulage est le procédé qui met en forme une matière première liquide, ou souple, à l’aide d’un cadre rigide appelé moule. Ce procédé, qui est très populaire aujourd’hui dans de nombreuses industries, prend son essor en pleine Seconde Guerre mondiale pendant laquelle les besoins en produits de masse se multipliaient.
L’essor industriel du moulage : une production de masse
En 1872, l’inventeur américain John Wesley Hyatt et son frère Isaiah créent la première machine de moulage par injection. Il s’agit d’une machine simple qui recourt à un piston pour pousser le plastique à travers un cylindre chaud dans un moule. L’appareil s’emploie en premier lieu pour fabriquer en série des produits tels que des boutons et des peignes.
Le chimiste allemand Arthur Eichengrün a développé la première presse à injection en 1919. En 1939, il dépose une demande de brevet pour le moulage par injection d’acétate de cellulose plastifié, beaucoup moins inflammable que les solutions alors exploitées.
Lorsque la Seconde Guerre mondiale éclate, le besoin de produits fabriqués en masse et à bon marché s’accroît. Par exemple, la guerre en Asie et les attaques en mer perturbent la production de caoutchouc. Les chars et autres applications de guerre ont créé une énorme demande de métal. Le plastique est intervenu pour combler ces manques, offrant un substitut abordable. James Watson Hendry crée alors le premier outil de moulage par injection à vis, qui devient rapidement populaire en raison de son degré de précision et de contrôle, et par conséquent, d’une meilleure qualité de production.
Pendant toute la période de l’après-guerre, le plastique est resté populaire. Lorsque les chefs d’entreprise ont reconnu les énormes avantages en matière de coûts par rapport aux matériaux concurrents, ils ont réévalué les chaînes d’approvisionnement mondiales. Les plastiques se sont fermement ancrés dans l’économie et les processus de fabrication du milieu du XXe siècle.
L’invention du moulage par injection jusqu’à nos jours
Hendry développe ensuite dans les années 1970 le premier système de moulage par injection assisté par gaz. Cette technique permet de manufacturer des pièces complexes, qui pouvaient être rapidement refroidies. Cette création améliore considérablement la flexibilité et la résistance des objets confectionnés tout en réduisant le temps et le coût de production. En 1979, la production de plastique a dépassé la production d’acier, et en 1990, le moulage par injection a largement recours aux moules en aluminium. Aujourd’hui, les machines d’injection à vis représentent la grande majorité des machines d’injection. Parmi les autres méthodes de moulage répandues encore aujourd’hui, on peut citer le moulage par soufflage, par compression ou sous vide (thermoformage).
De nos jours, le moulage par injection représente un marché de 300 milliards de dollars. Ce procédé produit plus de 5 millions de tonnes de pièces en plastique chaque année dans le monde. Presque tous les secteurs manufacturiers l’exploitent : électronique, automobile, électroménager, articles ménagers, etc. Le moulage par injection de plastique reste une méthode abordable et efficace pour produire des pièces et des produits de haute qualité. Récemment, la demande de matériaux biodégradables a augmenté pour des raisons environnementales.
La technologie utilisée aujourd’hui est assez semblable à celle utilisée dans le passé. Toutefois, les ordinateurs ont facilité l’ensemble du processus de conception et de fabrication. Les résultats sont également plus précis, et les pièces en plastique sont maintenant souvent le choix préféré pour les applications technologiques et scientifiques avancées.
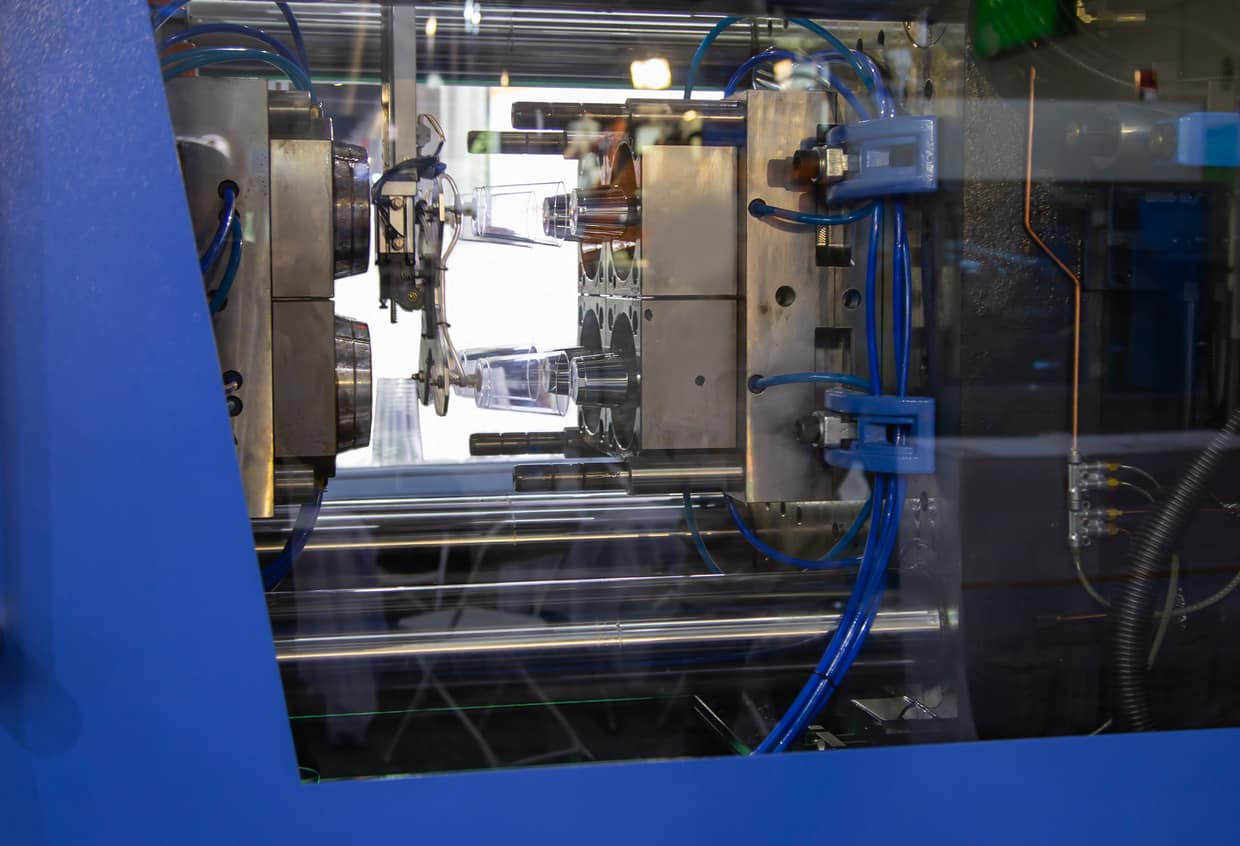
Qu’est-ce que le moulage par injection ?
Le moulage donne une forme à une matière première, liquide ou souple, à l’aide d’un cadre rigide appelé moule. Ce dernier est un bloc creux rempli d’un matériau comme le plastique, le verre, le métal ou les matières premières céramiques. Celui-ci durcit ou se fige à l’intérieur du moule, adoptant ainsi son aspect final. Parmi les différents procédés qui existent, les plus répandus sont le moulage par injection, soufflage, compression et sous vide.. Alors que la conception des moules et de leurs prototypes peut constituer un frein en matière de complexité et de financement, l’impression 3D devient une solution pertinente grâce à sa vitesse d’exécution et sa précision dans la réalisation.
Le moulage par injection
Lors du moulage par injection, la matière fond puis s’injecte sous pression dans un moule. Le plastique liquide y refroidit et se solidifie. L’opération peut se réaliser avec une multitude de matériaux (métaux, verre, thermoplastiques, etc.). Cependant, les plus couramment utilisées sont :
- le polypropylène (PP) qui représente environ 38 % de la production mondiale. Les bouchons de bouteille l’exploitent, par exemple, car il est adapté au contact avec les produits alimentaires,
- l’ABS qui en constitue 27 %. Lego l’apprécie pour sa grande résistance aux chocs. Chaque brique est ainsi conçue avec des tolérances allant jusqu’à 10 micromètres,
- le polyéthylène (PE), 15 %,
- le polystyrène (PS), 8 %.
En tenant compte de toutes les autres technologies de fabrication possibles, le moulage par injection de ces quatre matériaux représente à lui seul plus de 40 % de toutes les pièces en plastique produites chaque année dans le monde.
L’automobile fait partie des industries qui participent à sa croissance puisque presque tous les composants en plastique de l’intérieur d’une voiture sont moulés par injection. L’industrie exploite particulièrement :
- le polypropylène (PP) pour les pièces non critiques,
- le PVC pour sa bonne résistance aux intempéries,
- l’ABS pour sa grande résistance aux chocs.
Au moins une de ces matières s’intègre à plus de la moitié des parties en plastique d’un véhicule, notamment les pare-chocs, les pans intérieurs de la carrosserie et les tableaux de bord.
Dans un autre domaine, les boîtiers de la plupart des appareils électroniques grand public sont moulés par injection. L’ABS et le polystyrène (PS) sont les plus populaires en raison de leur excellente robustesse et leur bonne isolation électrique.
Ce procédé se démocratise en raison de son coût unitaire extrêmement bas lors de la production de gros volumes. Par exemple, cette technologie peut produire 1 000 à 100 000 unités pour 1 à 5 dollars pièce. Il offre une grande répétabilité et une bonne flexibilité de conception.
Le moulage par soufflage
Le moulage par soufflage est un procédé par lequel on forme et on assemble des pièces creuses en plastique, verre ou autres.
Il existe trois principaux types de moulage par soufflage : par extrusion-soufflage, injection-soufflage et injection-étirage-soufflage.
Cette technique commence par la fusion du plastique et sa mise en forme en une paraison. Ce terme désigne un morceau de plastique en forme de tube, dont une extrémité est percée d’un trou par lequel l’air comprimé peut passer.
On serre ensuite la paraison dans un moule avant d’y souffler de l’air. La pression pousse alors le matériau à l’extérieur pour qu’il s’ajuste au moule. Celui-ci s’ouvre une fois que le plastique a refroidi et durci. Enfin, on éjecte la pièce.
Le moulage par compression
Le moulage par compression est une technique par laquelle le matériau, généralement préchauffé, se place dans une cavité de moule ouverte et chauffée. Le moule reste fermé par une force supérieure ou un bouchon. Une pression s’applique pour forcer le matériau à entrer en contact avec toutes les zones de la matrice jusqu’à ce que le matériau ait durci.
Ce procédé à l’avantage de mouler des pièces de grande taille et assez complexes. De plus, cette méthode de moulage demeure l’une des moins coûteuses. En outre, elle gaspille relativement peu de matière.
Le moulage par compression se développe en premier lieu pour fabriquer des pièces composites, en remplacement du métal. On emploie généralement cette technique pour concevoir des pièces plates ou modérément courbées de plus grande taille. Le secteur automobile y a largement recours pour confectionner des pièces automobiles telles que les capots, les ailes, les ailerons, ainsi que des objets plus petits et plus complexes.
Le moulage sous vide
Le moulage sous vide est une version simplifiée du thermoformage, dans laquelle on chauffe une feuille de plastique, on l’étire sur un moule à une seule surface et on la pousse contre lui par un vide. Grâce à ce procédé, on transforme le plastique en objets permanents tels que des panneaux de signalisation et des housses de protection.
On peut former des pièces relativement profondes si on étire la feuille mécaniquement ou pneumatiquement avant de la mettre en contact avec la surface du moule et d’appliquer le vide.
Les matériaux appropriés pour le moulage sous vide sont généralement des thermoplastiques. Le plus courant et le plus facile à utiliser reste la feuille de polystyrène à haute résistance aux chocs. Celle-ci se moule et peut prendre presque toutes les formes. Elle peut retenir la chaleur et sa forme lorsque de l’eau chaude est appliquée. Ainsi, elle constitue un choix privilégié pour emballer des produits sensibles au goût et à l’odeur. Cette technique convient également aux matériaux transparents tels que l’acrylique, que l’aérospatial exploite largement, comme les auvents des fenêtres des cabines passagers des avions militaires à voilure fixe et les compartiments des avions à voilure tournante.
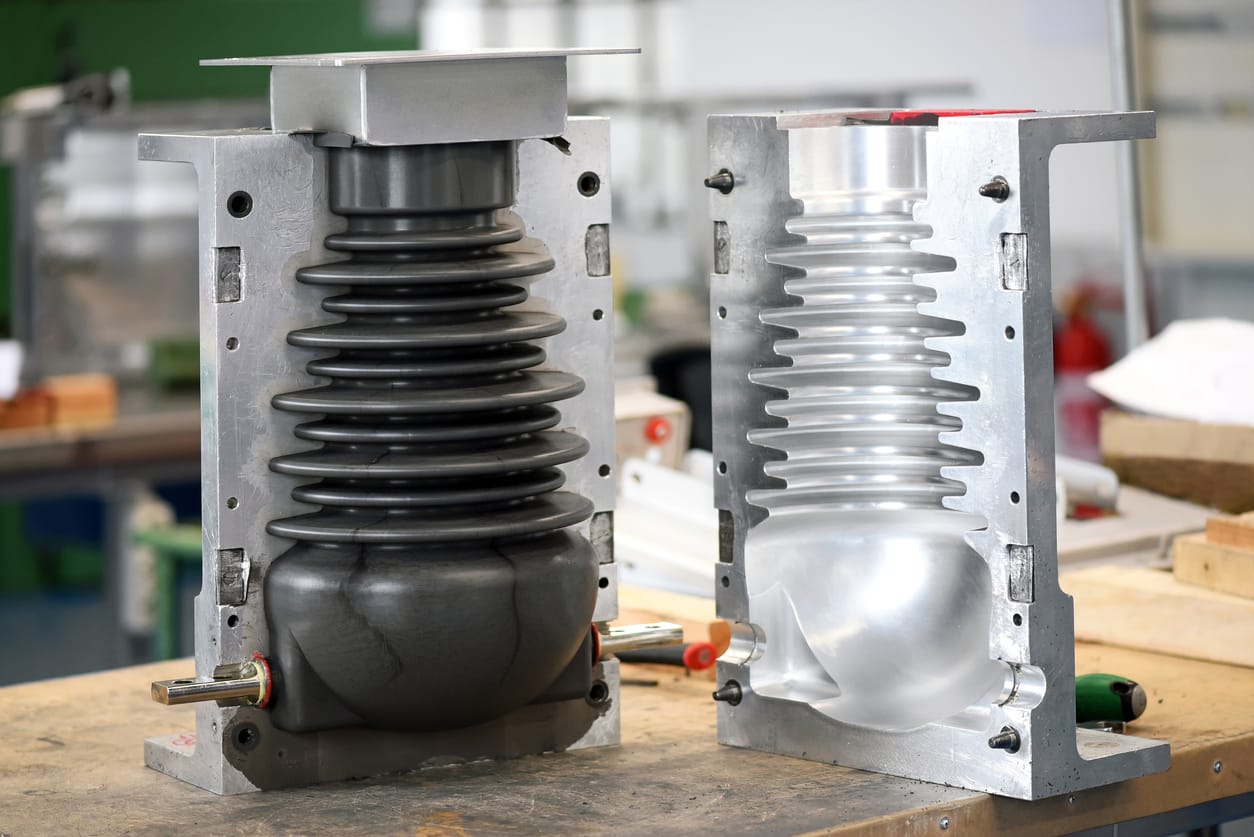
Obtenez plusieurs devis pour vos projets en quelques secondes