Anodisation
Découvrez comment l'anodisation, un procédé de finition, fonctionne et les usages de ce procédé de fabrication.
Introduction à l'anodisation
L’anodisation permet d’augmenter l’épaisseur des couches naturelles d’oxyde sur la surface des pièces en métal. Cette technique s’applique le plus souvent à des substrats en alliage d’aluminium, mais peut également s’appliquer au titane, zinc, magnésium, niobium, zirconium, hafnium et tantale. Le processus d’anodisation emploie la passivation électrolytique pour acquérir les propriétés souhaitées telles que la résistance à la corrosion et à l’usure, une meilleure adhésion de la peinture et de la colle ou des propriétés esthétiques. Dans un but esthétique, des revêtements poreux épais permettent d’absorber une teinture pendant que les revêtements transparents fins créent des effets d’interférence avec la lumière reflétée.
Le processus est appelé anodisation, car le substrat en aluminium forme l’électrode anode d’un circuit électrique. L’anodisation s’utilise également pour empêcher le grippage ou l’usure des composants filetés, mais aussi pour créer des couches diélectriques pour des condensateurs électrolytiques. La texture microscopique d’une pièce et la structure en cristal du métal près de la surface subissent des modifications lors de l’anodisation. Les revêtements épais nécessitent généralement un processus de scellement pour éviter la corrosion liée à leur nature poreuse. Les couches anodiques s’avèrent bénéfiques, car elles présentent des propriétés de solidité et d’adhésion plus importantes que la plupart des types de plaquage de métal. Cependant, elles sont également plus fragiles et susceptibles de se fissurer à cause de la contrainte thermique.
Voici les principaux avantages de l’anodisation : un revêtement beaucoup plus fin que la peinture ou la poudre, extrêmement résistant, solide, résistant à l’abrasion, durable, ne s’écaille pas, ne s’ébrèche pas, possède une surface plus solide que la peinture, la couleur ne s’estompe pas, une excellente protection contre la corrosion, écologique, un bon isolant électrique et abordable.
L'histoire de l'anodisation
L’anodisation a fait son apparition dans le contexte industriel de 1923 et avait pour but de protéger les pièces de duralumin utilisées pour les hydravions contre la corrosion. À l’origine, l’utilisation d’acide chromique faisait partie de ce processus appelé le processus Bengough-Stuart. L’acide sulfurique a fini par être adopté. Il est vite devenu et demeure aujourd’hui l’électrolyte d’anodisation le plus courant. En 1923, l’anodisation à l’acide oxalique est brevetée au Japon et est très utilisée en Allemagne, notamment pour les applications architecturales. Dans les années 1960 et 1970, l’extrusion d’aluminium anodisé devient un matériau d’architecture extrêmement populaire, mais a aujourd’hui été remplacée par des plastiques et du revêtement par poudre qui sont plus abordables. Plus récemment, l’acide phosphorique est intégré au domaine de l’anodisation et, pour l’instant, il est uniquement utilisé en prétraitement pour des adhésifs et de la peinture naturelle.
La spécification d’anodisation la plus répandue aux États-Unis est une spécification militaire américaine. Elle définit trois types d’aluminium d’anodisation : l’anodisation à l’acide chromique (type I) et l’anodisation à l’acide sulfurique (types II et III). L’acide chromique est le processus d’anodisation par revêtement le plus ancien, mais l’acide sulfurique est la solution la plus utilisée dans l’anodisation par revêtement. L’anodisation peut être réalisée à l’aide de bains d’acide organique, d’acide phosphorique, de borate et de tartrate, mais aussi au moyen de l’oxydation électrolytique par plasma.
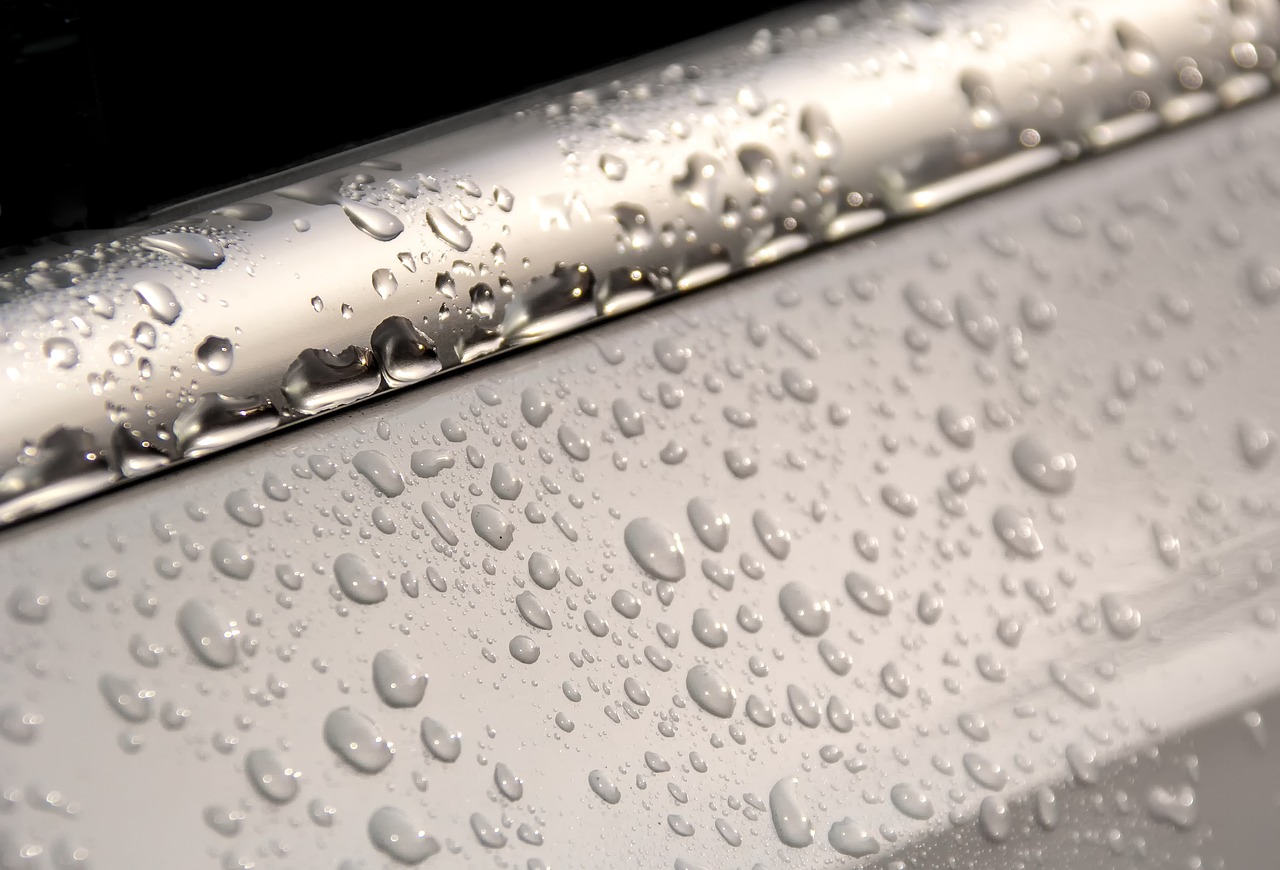
Obtenez plusieurs devis pour vos projets en quelques secondes