Wind Farms Fit for the Future: Ensuring Offshore Wind Is Seaworthy
Offshore wind is a powerful supplement to other renewable energy practices. Digital tools can help you make the most of it.
What is Offshore Wind Energy?
An offshore wind farm consists of numerous turbines spanning a vast ocean area. Each turbine is securely anchored to a seafloor foundation, featuring a tower that extends into the air to harness stronger wind speeds for blade rotation.
What Are the Advantages and Disadvantages of Offshore Wind Farms?
Offshore wind has several distinct advantages compared to onshore installations.
Bigger turbines
Larger blades capture more wind, so larger turbines are more efficient. One of the main advantages of moving offshore is that turbines are less constrained by size.
The construction and installation of wind turbines rely on existing infrastructure. Components must be built in a factory, then carried to site using road and rail networks. But road and rail have difficulties accommodating the latest giant blades, which can measure more than 100m.
Offshore wind does not share this problem. Here, blades and other turbine components can be manufactured close to ports, then easily loaded onto specialized boats, sailed into position, and erected.
In the case of floating turbines (a rapidly maturing technology where the base of the turbine is not fixed to the sea floor, but a free-floating raft), jack-up vessels with cranes can also be eliminated, with the assembled turbines being towed out to position directly, helping ease wind farm installation challenges.
Better quality wind
Wind speeds are higher and more consistent at sea than they are on land, meaning that offshore wind can generate power more efficiently than onshore wind. This doesn’t just mean that more power can be generated in total, but it also means that the power generation is more predictable.
Renewables have a problem with intermittency, which has been an impediment to our relying on them. Higher levels of reliability reduce this problem, which means that offshore wind generation can be more easily integrated into existing grid-scale energy generation.
Less restriction
Despite growing public enthusiasm for wind farms (a 2021 survey found support for wind in the UK grew by a third in five years), they are still subject to criticisms as being noisy or unsightly.
By building out at sea, far from inhabited areas, offshore wind farms sidestep these objections. Additionally, offshore wind farms can be built larger, as more space is available.
Offshore wind energy has become increasingly central to the global green energy landscape – it is estimated that across 2022 alone, 10GW of new offshore wind capacity will be installed.
But there’s still headroom for growth. In fact, according to a 2019 report from the International Energy Agency, wind power, if fully exploited, could supply more than 18 times the global energy demand.
If solar power and onshore wind drove renewable uptake over the last twenty years, offshore wind is set to lead the next decade of renewable power.
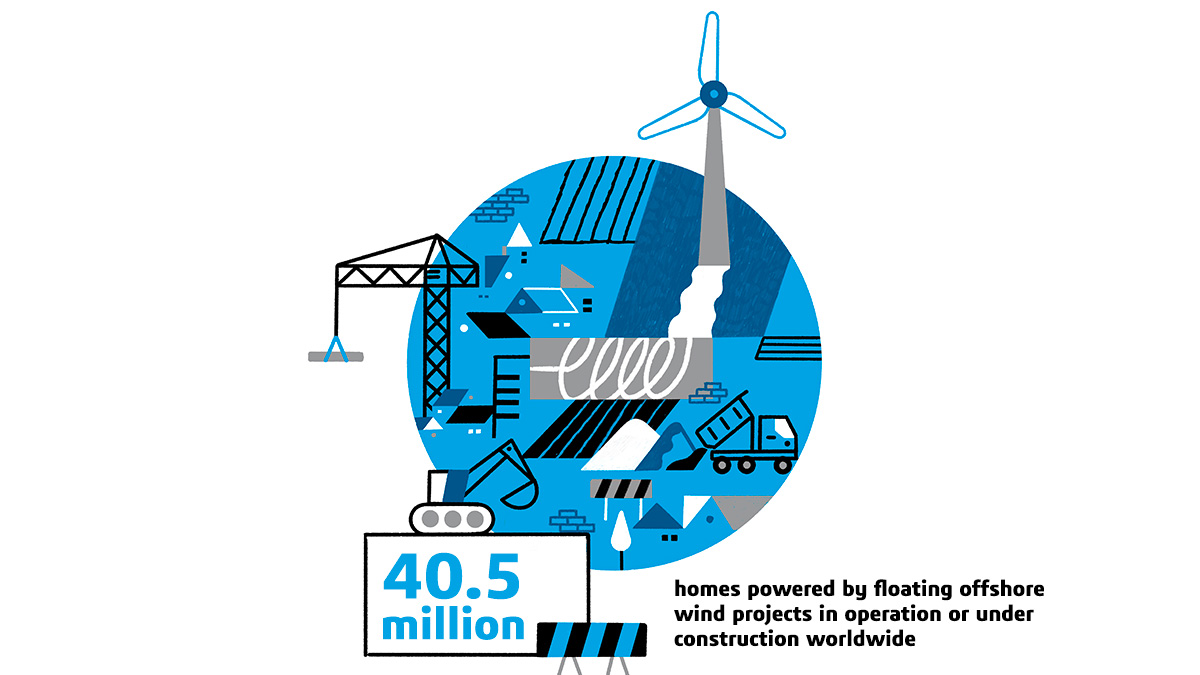
The Obstacles to Offshore
Despite these benefits, designing, building, operating and maintaining offshore wind farms can involve significant challenges that are not always faced by onshore wind.
High costs
While they are effective, offshore wind farms can be expensive. Large and expensive specialty ships and ports are needed in construction and installation, and once farms are built, maintenance is more expensive because ships and helicopters are required for access.
Environmental stresses
Offshore wind turbines are designed for a lifespan of 20 years. The foundations are designed for about 40 years. Over the lifetime, the turbines and foundations are subjected to high degrees of environmental stress. These stressors can be anything from waves and tidal forces that erode their bases, to salt water and air corroding metal parts, to a shifting seabed that can alter how things like vibrations travel through and affect turbine components.
Regulatory blocks
Just as with onshore wind farms, offshore projects are substantial installations that need to pass a range of regulatory checks before they can be safely and legally installed. For offshore wind farms, one unique but significant challenge is managing the objections of the fishing industry. In addition, underwater radiated noise has to be limited during construction in order not to harm wildlife.
Digital Transformation of Wind Turbine Manufacturing and Operations
Learn how to gain a leading edge in the wind turbine manufacturing
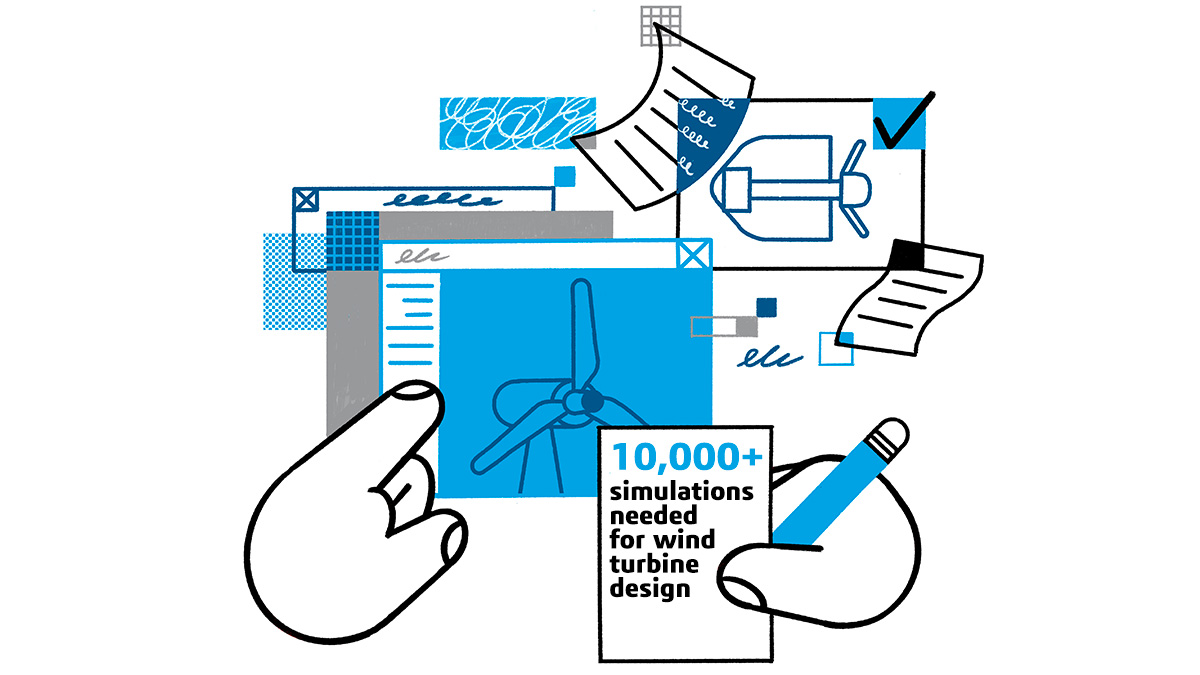
The Simulation Game
An increasingly powerful tool in helping address these challenges is simulation – in the design of cutting-edge wind turbines, the logistics of implementation, and in ensuring reliable and efficient operation.
Paramount is being able to model the stresses turbines will undergo during their lifetimes. For regular turbines, this can include normal wear and tear of parts and machinery. A regular wind turbine needs more than 10,000 simulations during the design stage. But offshore wind turbines, with their unique environmental challenges, and with loading from waves, need many times more.
By creating a virtual twin with Dassault Systèmes’ 3DEXPERIENCE® platform, designers and analysts can create a vast array of wind turbine simulation scenarios to see how a given turbine would perform. They can also use the same virtual twin to develop and test unique materials that could improve a turbine’s operation, such as blade coatings that are more resistant to maritime conditions.
The number of simulations that you must consider for offshore turbines just keeps getting larger. The models keep getting more detailed. That's the advantage of our solutions, there's no upper fidelity limit they can handle.
The Power of Simulation for Offshore Wind Design and Collaboration
Accessing the virtual twin on a shared cloud-based platform also provides a single, consistent source of truth where different findings and insights from across the value chain can be pulled together into a single holistic model.
“You can easily simulate and predict the dynamics – the motions, the forces and the strains and stresses of the entire turbine,” says Steve MULSKI, Strategic Business Development Execution, Dassault Systèmes.
“And this goes right down to even the smallest components, such as the gearbox bearings and gear teeth. You can even do detailed designs of the generators and model the electromagnetic forces within those generators.”
Shared models can also ensure components from different vendors fit smoothly together and facilitate effective collaboration between design teams or between designers and manufacturers.
“There are so many different sub-components, which are typically made by separate vendors. Our software can combine these different vendor products into a multi-body solution,” adds Wouter van der Velden, SIMULIA Specialist, Dassault Systèmes. “This establishes visibility at the whole-system level, which is critical for effective design.”
In addition to improving design efficiency – and thereby reducing prototyping needs – simulation can also help extend operational life. For example, by analyzing the lifetime stress data of a wind turbine, an operator might find less stress than expected.
In turn, this data can be used to get the turbine to be recertified and continue operations. Solutions like this are particularly important for offshore turbines, given the size of the machinery and strength of the environmental forces.
“In the past, you'd only consider the tower and the blades as flexible bodies. That's no longer sufficient with these larger turbines,” says Steve. “Now to accurately predict loading on the major components, you need to consider many additional components as flexible, such as the bedplate and main shafts.”
The potential of offshore wind is incredibly exciting, and it starts with simulation.