Production of One
Leverage flexible manufacturing to unlock lead time reduction and production scalability.
Delivering Customization Through Flexible Manufacturing
With today’s demand for mass customization and shorter product lifecycles, manufacturers are challenged to deliver highly customized specifications faster and more sustainably. As production volumes decrease and complexity increases, they must adapt their existing systems to maintain throughput and quality.
The era of one-off production is over. To thrive in this competitive landscape, manufacturers must scale personalized production with flexibility and agility. This drives the adoption of modular systems and 3D configuration experiences that support scalable and flexible manufacturing.
The 3DEXPERIENCE® platform offers manufacturers multi-site collaboration and full visibility across operations, enabling seamless collaboration to deliver quality products at a lower cost. By supporting modular manufacturing with marketing-defined variants, the platform aligns engineering and manufacturing processes to accelerate market responsiveness and maintain healthy margins at scale.
Modular Design: The Key To Flexible Manufacturing
Modularity at the product level plays a critical role in enabling flexible manufacturing and business resilience. By designing modular products with pre-defined variants, manufacturers can swiftly adapt product development to market demands while improving manufacturing efficiency and protecting margins.
These modular systems, developed through close collaboration between marketing, engineering and manufacturing teams, allow rapid batch customization without re-engineering core components. This results in reduced production complexity, shorter development cycles and more efficient resource planning. Moreover, modularity helps manufacturers in supporting sustainable practices, such as the reuse of parts and improved lifecycle management.
Sustainability Starts With Flexible Manufacturing
Sustainability has become a strategic imperative for manufacturing companies. Flexible manufacturing supports manufacturers’ sustainability commitments by reducing overproduction, minimizing waste, optimizing resource allocation and improving market responsiveness to eco-conscious consumer demands. By enabling smaller, on-demand production runs, local sourcing and energy-efficient processes, it creates an efficient production process that minimizes environmental impact.
Leveraging Virtual Twins for Flexible Manufacturing
In an era where rapid adaptation drives success, our virtual twin technology redefines how manufacturers design, operate and evolve their production systems by leveraging manufacturing intelligence. Dassault Systèmes’ 3DEXPERIENCE platform enables companies to work in a fully virtual environment, where teams can simulate, validate and optimize flexible production lines before any physical implementation.
This digital transformation also allows for seamless robotics integration, process automation and modular machinery to support efficient reconfiguration and optimized resource allocation. Manufacturers can test a variety of scenarios, such as shifting product variants, optimizing robot coordination or introducing sustainable materials without interrupting operations.
By simulating everything from machine performance to line bottlenecks and energy consumption, virtual twins enable continuous improvement and on-the-fly, rapid adaptation. The result is a future-ready production system capable of mass customization, faster time to market and smarter decision-making while minimizing waste and downtime.
Key Advantages of Flexible Manufacturing With Virtual Twins
Manufacturers can unlock key advantages by harnessing the power of virtual twins for continuous improvement, including:
Achieving mass customization at speed
Adapt quickly to demand fluctuations while achieving lead time reduction for faster market responsiveness
Optimizing engineering with modular lines
Enable quick changeovers and improve production scalability based on order variations
Improving cost control for low-volume runs
Reduce downtime and improve resource allocation through cost-effective
Enhancing agility with real-time data
Make informed decisions faster with digital monitoring and simulation
Explore Our Customers' Stories
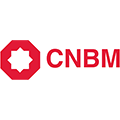
CNBM Triumph Robotics
This Shanghai-based robotic line builder enhanced precision and performance in highly customized production processes by leveraging virtual twin technology.
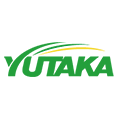
Yutaka Electronics
This Japanese robotic assembly line builder improved traceability and flexibility in its robotic assembly lines through digital continuity and real-time data integration.
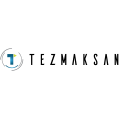
Tezmaksan
Tezmaksan Robot Technologies boosted agility by integrating robotic automation with real-time data, streamlining production and enhancing operational responsiveness.
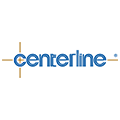
CenterLine Windsor
This Canadian industrial automation process and technology company streamlined digital design processes to support flexible tooling and robotic solutions, enhancing efficiency and reducing deployment time.
Transform Your Business With Us
Flexible Manufacturing: The Backbone of Smart Factories
Explore our Industry Solution Experiences
Learn more about how our industry solutions can help you to achieve your professional ambition and business objectives.