Transforming Manufacturing Technologies
Today’s factories are undergoing a profound transformation, and new technologies and solutions mean new ways of making things.
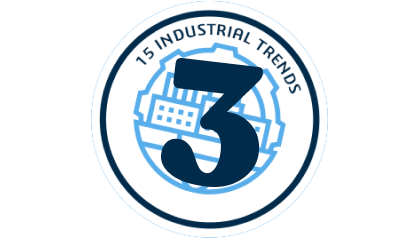
What are the technologies that will shape your operations across the next decade?
What’s happening?
The history of manufacturing is, to a great extent, a history of technology. From the steam engine, to electricity, to robotics, to computers and the internet, the factory floor has continually been driven forward by great surges of technological change.
Sometimes that change moves at an accelerated rate. In particular, the pace and power of the modern, digitally connected world, led WEF Founder and Executive Klaus Schwab in 2015 to dub the current epoch as the “Fourth Industrial revolution”.
This revolution is characterized in part by the technologies driving it, like internet, IoT, AI, machine learning, and other forms of advanced technology. But it is also characterized by a more fundamental transformation in industry as a whole – in how products are made, how value is generated, and how manufacturing value chains operate at a macro scale.
Investment in making manufacturing even more technologically sophisticated continues. Research from Forrester has found that global R&D investment for high-value manufacturing is set to grow by 15% in 2022 alone.
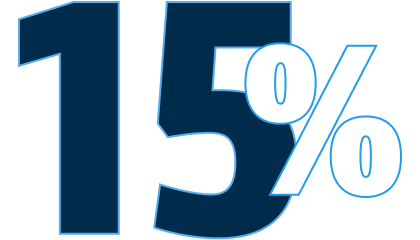
All this investment and enthusiasm brings substantial opportunities for manufacturing industries, but the practical implementation and management of these technologies across real-world factory floors can be a challenge. How can manufacturing industries best respond?
Curious about how other manufacturing industries respond?
Respond to today's challenges with our bespoke solutions
Why does it matter
Companies have more technological tools than ever before to transform manufacturing shopfloor management, realize new operational efficiencies, and serve customers in brand new ways:
1. Modularity: Adopting modular approaches for everything, from arranging the factory floor to your supply chain operations, allows manufacturers to improve speed and agility, scale rapidly, and better meet the shift to more personalized products.
2. Robotics: Robots have been a key part of factories since the 1960s, and their relevance only continues to grow; the CAGR (compound annual growth rate) of the North American robotics industry’s revenue is set to be 11.67% through to 2026.
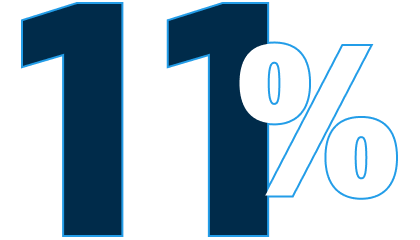
“The robot market will completely change in the next eight years,” says Philippe Bartissol, Vice President, Industrial Equipment, Dassault Systèmes. “Right now, the vast majority of robots are stationary, caged robots, which just move stuff from one spot to the other. But the improvement of connectivity and safety technologies means we’re increasingly seeing autonomous mobile robots (AMRs) on factory floors.”
He is optimistic about their applications. “These robots are a lot more powerful, and can perform many more tasks – they could ultimately completely transform manufacturing logistics. In the future we might have seven or eight times more AMRs than you have caged robots.”
3. Additive manufacture: For some time, 3D printing (or additive manufacture) was the preserve of hobbyists or highly specialized component developers. But increasingly manufacturers are waking up to its substantial industrial applications. The global 3D printing market size was valued at USD 13.84 billion in 2021 and is expected to expand at a CAGR of 20.8% from 2022 to 2030, according to Grand View Research.
This opens up tremendous opportunities for manufacturers. 3D printing enables the production of complex components, often involving moving parts, from a single piece of material. It has applications in everything from prototyping to machine tooling to medical devices, and can be a critical element in mass customization. It can even assist in the pursuit of sustainability goals, helping cut down on things like transport and minimizing the need for multiple factory processes.
4. IoT: The growth of industrial IoT applications is helping to transform the factory floor, making manufacturing operations smarter and more efficient, while generating a huge amount of highly valuable data. This information enables the development and implementation of predictive maintenance techniques, as well as the ability to model more effective operational approaches.
“IoT allows you to quickly identify part numbers of malfunctioning components,” says Bartissol. “It sounds trivial, but failure to do this leads to a lot of time wasted because operators cannot precisely tell the OEM which one it is to get a replacement. Knowing the part numbers instantly allows operators to save an enormous amount of work time. And by improving the maintenance processes around capital equipment, you can also extend the life cycles of products and machinery.”
Manufacturing Industries on the Edge: Transformation from the inside out
Having established what manufacturers can do embrace innovation, we now look at what they can do with technology once they have it, and how it can be used to address risk and pursue new kinds of value.
How can I prepare?
An increasingly digital factory needs increasingly digital solutions to tie together disparate systems, processes, and technologies. Factory operators are increasingly using a model-based systems engineering (MBSE) approach, incorporating technologies like virtual twins and full life cycle assessment (LCA), to make informed, strategic decisions around the technologies they acquire, and how they set up and manage that equipment.
“Let's take capital equipment buying,” says Bartissol. “Imagine you have a new production line being installed. This production line is supplied by the OEM. When that OEM is proposing a quotation to a plant operator based around the additional capabilities required, right now they will make that quotation in 2D layout drawing. What I believe will be the norm in five years is that the line builder will sell through animated 3D experiences.”
By utilizing virtual modelling, as part of a MBSE approach, as well as virtual reality training processes, the line builder can simulate how that specific piece of equipment would operate within the existing production line so the plant operator can be confident it will do the job they intend.
Digital technologies are increasingly focused on providing real-time, highly detailed information on factories and how their components operate as a whole. This enables companies to make far more informed decisions about how they should evolve their business, and drive superior operational optimization outcomes.
And it is precisely the mastery of this emerging landscape of transformative manufacturing technologies that will determine which companies thrive, and which companies don’t, in the coming decade.
New generations of robots could ultimately completely transform manufacturing logistics.
Other Trends
Discover more with our Manufacturing Industries
- Aerospace & Defense
- Consumer Packaged Goods & Retail
- Home & Lifestyle
- High-Tech
- Industrial Equipment
- Marine & Offshore
- Transportation & Mobility
Bridge the gap between the virtual and real world to accelerate from concept to operations
When consumers want it yesterday, be first to make it and first to market.
As complexities increase, future readiness is needed to establish agile and resilient operations from end to end. Discover how the virtual twin roadmap can help.
Virtual Twin Experiences for Sustainable Innovation – Helping Manufacturers Improve Consumer Products
Integrate product innovation with sustainable design practices on a single platform to lower a product’s environmental footprint with Sustainable Innovation Intelligence.
Simplify and accelerate innovation to create more valuable consumer experiences.
Secure an advantage to deliver best-in-class batteries with the power of virtual twins.
Digitalize manufacturing to deliver made-to-order innovation.
Go beyond digital twin technology and discover the future of your manufacturing operations
Accelerate the sustainable transformation of the Marine & Offshore industry.
Driving vehicle innovation toward the mobility of the future
Get better prepared for the supplier collaboration revolution, with strategic capabilities and resources
Get personal with cutting-edge manufacturing inspired by time-honored craftsmanship
THE WORLD NEEDS MANUFACTURERS
A MANIFESTO FOR CHANGE
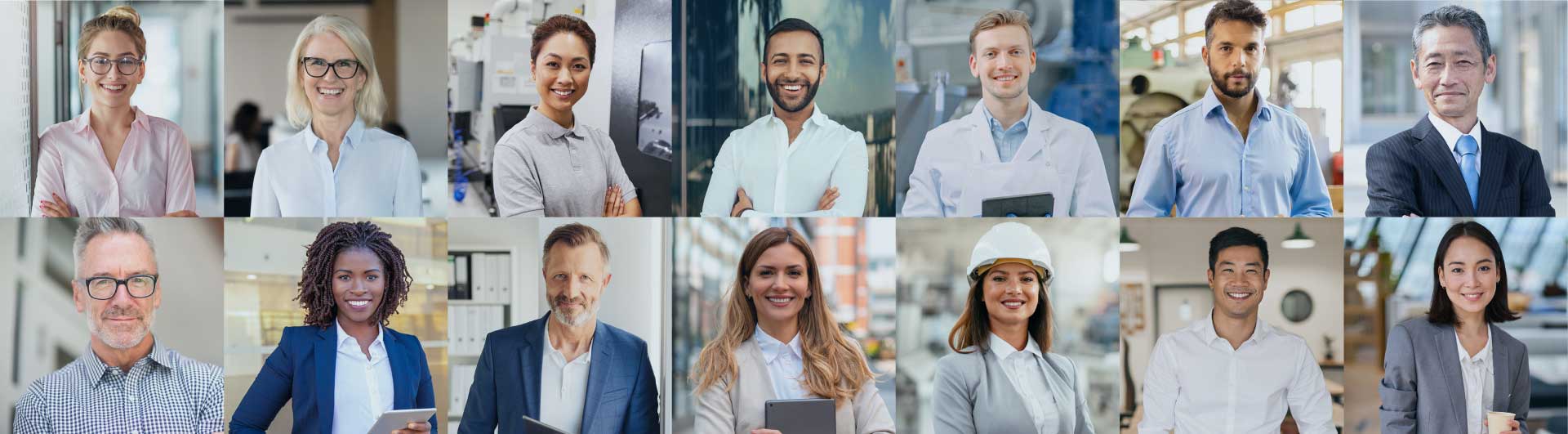