Unlock Flexible Production Lines With Industrial Automation
Develop, integrate, manage and maintain flexible production lines with autonomous mobile robots (AMRs).
Shrinking product lifecycles and customer demand for mass customization are pushing line builders to shift from mass production to flexible, smart manufacturing. Escalating competitive forces and skills shortages accentuate the need for the comprehensive modernization of production facilities in today's manufacturing industries — central to the digital transformation in manufacturing.
In the next five years, 86% of manufacturers will invest in industrial automation solutions¹ to drive business competitiveness. As such, companies striving to maintain a competitive edge must integrate virtual twin technology and industrial robotics into manufacturing processes. As a digital replica of production lines, Dassault Systèmes' virtual twins offer a sandbox for experimentation and optimization — helping improve first-time-right rates, minimize commissioning delays and drive production line optimization significantly.
Flexibility, Modularity and Efficiency: The Next Frontier for Line Builders
1. Development
Accelerate the line development phase by:
- Creating virtual twins of lines with AMRs
- Sizing the number of AMRs needed in lines
- Virtually testing different scenarios before the physical build
- Identifying potential bottlenecks and optimizing AMR routes
2. Integration
Simulate AMR behaviors in the plant before implementation to:
- Test multiple scenarios for different production requirements
- Improve commissioning time
- Reduce total installation time
3. Management
Manage and monitor the status of the line and AMR fleet in real time to:
- Reduce downtime and unexpected shutdowns
- Improve resource utilization and increase productivity
4. After-Sales
Enhance after-sales service with the field service twin for:
- Improved maintainability to ensure the sustainability of service operations
- Performance and health monitoring leading to on-condition maintenance
- Predictive maintenance to deploy proactive actions
Proven Results From Industry Leaders
Powered by the cutting-edge 3DEXPERIENCE® platform, virtual twins empower line builders with unparalleled efficiency – to develop flexible and modular lines – and reduce commissioning time and costs by up to 70%.
With the ability to optimally monitor operational data and execute predictive maintenance, virtual twins enable manufacturers to operate at peak efficiency while minimizing production downtime. These advantages have allowed industry leaders to transform their operations with intelligent automation and robotics integration to break competitive frontiers.
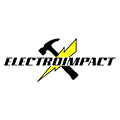
Electroimpact
"Are we able to meet our customers' needs and provide the information they need seamlessly? Can we run the business better and more productively? Can our engineers collaborate and work effectively and efficiently? On all three counts, the 3DEXPERIENCE platform is helping us achieve those goals."
Ben Hempstead
Mechanical Engineering Lead and Chief of Staff
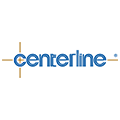
CenterLineLimited
"Dassault Systèmes' solutions have helped us design equipment to simulate the assembly in a virtual setting and anticipate problems we could run into when selling the equipment and programming the robots. It really gives us a leg up before we put the steel to the floor."
Marc Levesque
Director of Corporate Marketing
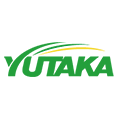
Yutaka Electronics
"The virtual twin experience by Dassault Systèmes enables us to integrate the commissioning process into the design work itself. While doing 3D modelling, we can carry out comprehensive operational checks of an entire system, including multiple robots. This will help us to eliminate early design flaws that have sometimes been overlooked in the past."
Daisuke Matsuo
General Manager of Advanced Technology Division
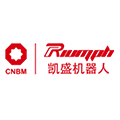
CNBM Triumph Robotics
"The 3DEXPERIENCE platform offered a holistic solution, with diverse modules covering all aspects of our digital scenarios. This is very appealing to us. Everything we do is now based on the PLM’s unified database, without causing duplicate designs or incorrect references."
Gao Changqi
Chief Engineer
What Leading Line Builders Have Achieved
- Up to 50% shorter development lead time
- Up to 50% faster commissioning time
- Up to 25% faster time to market
- Up to 20% reduction in service execution time
Dassault Systèmes' Executive Brief: Flexible Production For Line Builders contains the full strategy to help you develop, integrate, manage and maintain futureproof production lines with AMRs.
Flexible Production Lines Explained
¹Source: “2025 Manufacturing Industry Outlook” by Deloitte (November 2024)