Yutaka Electronics
Japanese robotic assembly line builder Yutaka Electronics chose Dassault Systèmes’ 3DEXPERIENCE platform on the cloud and its industry solution experience Digital Equipment Continuity to ensure that the systems it has designed for its customers are operating correctly and efficiently before it begins physical commissioning.
Efficient robotic assembly lines through virtual comissioning
Step inside a modern manufacturing facility and it’s highly likely you’ll find all kinds of tasks being performed on a variety of robotic assembly lines, from welding and assembly, through to material handling and product packing.
But how do manufacturers ensure they are getting the most from their automated assembly lines? One answer is to call on the expertise of line builders like Japanese firm Yutaka Electronics.
“Yutaka was founded as a mechatronics technology company in 1964,” said Takashi Morita, the company’s president and CEO. “In 1979, it became one of the first companies in Japan to enter the field of industrial robot systems. Since then, we have evolved into a total system integrator. Our goal is to become the best in the world at what we do.”
Yutaka analyzes how industrial robot systems are used in the production lines of its clients, including automotive, aerospace and defense firms, and original equipment manufacturers. It then looks at how best to optimize the assembly process in that line, often with the help of artificial intelligence (AI) and internet of things (IoT) technology. To date, Yutaka has delivered more than 20,000 robot systems to customers in over 40 countries.
“We closely examine our customers’ requirements and specifications, then design the most effective production lines, incorporating robotic systems from prominent robot manufacturers to automate the assembly process,” said Daisuke Matsuo, general manager in the advanced technology division of Yutaka Electronics. “The final step is to deliver the equipment to site and check that the various parts work properly before handing it over.”
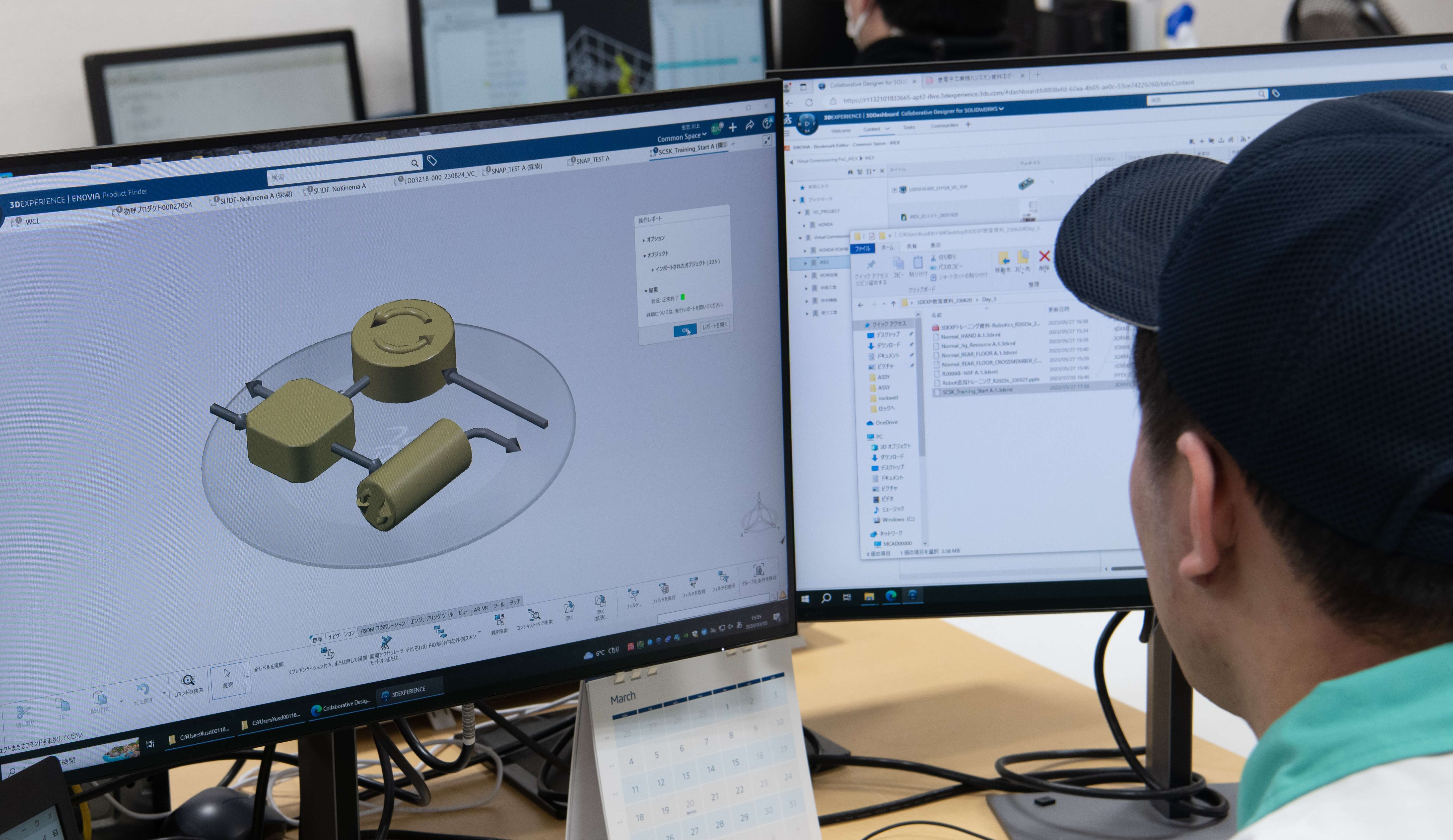
A need for faster and more seamless processes
In an increasingly competitive market, Yutaka needs to be quick and efficient at commissioning – an engineering process to check, test and verify the components of its customers’ robotic assembly lines. Typically, the commissioning stage is cumbersome and can be responsible for up to 70% of project delays. Yutaka was experiencing this issue: its design and commissioning works were conducted separately.
“In the past, our draftsman had to imagine a lot of processes in his head,” said Matsuo. “The mechanical design was then drafted in SOLIDWORKS using the manufacturer’s data. But there were often mistakes in this data, which led to frequent rework and backtracking. To check the robot's operating program, we had to export it to third party software. This wasn’t very seamless.”
Yutaka realized it needed a new approach that would enable virtual commissioning and help it achieve its vision for wider digital transformation. Yutaka already used Dassault Systèmes’ SOLIDWORKS CAD software, and so decided to complement it with the 3DEXPERIENCE platform on the cloud.
“We found that the 3DEXPERIENCE platform would allow us to manage all of our data centrally, including that from SOLIDWORKS,” Matsuo said. “This would make a big difference to us. It would enable us to complete all processes in a shorter timeframe, expediting our time to delivery.”
The virtual twin experience enables us to integrate the commissioning process into the design work itself… This will help us to eliminate early design flaws that have sometimes been overlooked in the past.
A single solution to verify robotic assembly lines
Yutaka can achieve virtual commissioning of robotic production lines through DELMIA on the 3DEXPERIENCE platform since it can now verify feasibility before installing the physical equipment at a customer’s manufacturing site. Previously the company was unable to determine the takt time (the production speed required to meet customer demand) until the line was fully assembled. This led to additional on-site rework and missed deadlines.
“The virtual twin experience enables us to integrate the commissioning work into the design work itself,” said Matsuo. “While doing 3D modelling, we can carry out comprehensive operational checks of an entire system including multiple robots. This will help us to eliminate early design flaws that have sometimes been overlooked in the past and reduce rework as a result.”
Cloud-based collaboration
Yutaka is using the POWER’BY application to connect its designs created in SOLIDWORKS to the 3DEXPERIENCE platform, while mechanical design and physical model simulation is now done within CATIA. The company can link computer aided design (CAD) and the engineering bill of materials (EBOM), and improve collaboration on changes and issue reviews using the product lifecycle management (PLM) and data management capabilities within ENOVIA.
With all data stored in a single, cloud-based solution, Yutaka can also collaborate with customers directly within the platform, sharing and managing data in a secure way. This also reduces the need for teams to travel to check the production lines on-site.
“Having data managed centrally in the cloud brings strong collaboration capabilities and this makes a huge difference,” said Matsuo. “It means we can work together more effectively as a company. Different locations can see the same information by connecting to each other over the internet. As a result of this more efficient way of working, we expect to save 20-30% of our time.”
Using the 3DEXPERIENCE platform on the cloud is also improving uptime. “In the past, when we were using a file-based system, we would often copy data from one project to another,” said Mitsuhikio Ohtake, who works in Yutaka’s new technology verification office. “The copied data links were sometimes broken and this could cause problems when we tested the assembly line – sometimes it would even break and stop. Now that we are in the cloud we have a single source of information. We can access accurate data and this has led to smoother operations. Data storage access and read/write speeds have also become much faster.”
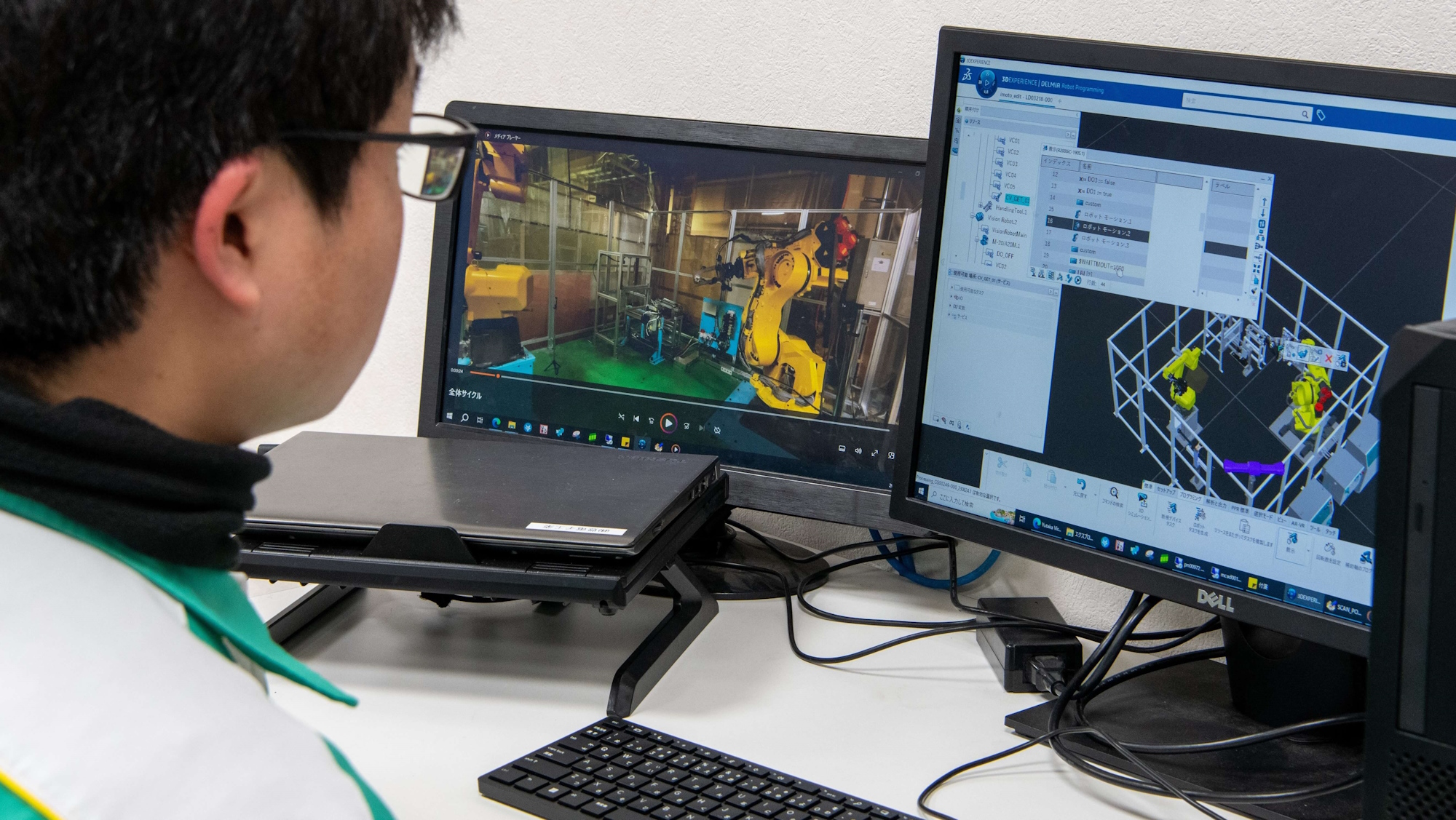
Putting virtual comissioning to work
The first opportunity to leverage the virtual commissioning capabilities of the 3DEXPERIENCE platform on the cloud came at a robot exhibition, where Yutaka created a line that could be used to demonstrate the potential of a robotic assembly process. Without virtual commissioning, this typically takes Yutaka a full day to set up. However, by first creating digital replicas of its robots and simulating their behavior and integration, installation only took four hours.
Ohtake offers an example: “If a robot’s arm is operating a very complex jig, we can see very easily – in a 3D virtual model – whether there is any interference,” he said. “Before, we might not have picked up this type of issue until the line was built, so we would have to start over again.”
This project demonstrated the added value Yutaka can deliver with virtual twins, by configuring work quality, cycle times, space layouts and workflows to customers’ needs before physical commissioning takes place. “By pre-verifying feasibility and takt time before on-site assembly, physical testing could be reduced,” Ohtake said. “As a result, we have shortened our prototyping lead times by 50%.”
Once Yutaka is fully utilizing the capabilities of Dassault Systèmes’ tools, it expects to further improve visualization of its operations and debug systems while reusing knowledge and past learnings in future projects.
Ultimately, Morita believes that the combination of Yutaka’s expertise and the capabilities afforded by the 3DEXPERIENCE platform have fortified its position in the market. “Our strength lies in the fact that we have contacts with all industries and can propose the latest robotic system automation incorporating customer requirements for production processes in all industries,” he said. “As digital transformation advances in all industries, our strength will remain unchanged. As a system integrator, we can and will continue to combine the latest technologies such as the 3DEXPERIENCE platform to provide superior added value to our customers.”
FAQs
Discover more about the Digital Equipment Continuity industry solution experience.
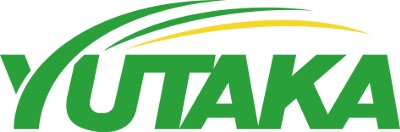
Focus on Yutaka Electronics
Yutaka Electronics is one of Japan’s largest system integrators. Employing over 700 people and operating day and night, the company offers a wide range of services, including not only the manufacturing of robot systems and distribution control systems, but also comprehensive support from pre-design development proposals to post-delivery maintenance and after-sales service. Yutaka Electronics operates business units in seven countries and, as a development-oriented systems engineering company, provides strong support to its customers worldwide with its advanced technological expertise and innovative ideas.
For more information: https://www.ytk-e.com/
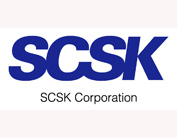
Focus on SCSK
Founded in 1969, SCSK Corporation offers a wide range of system integration services to companies not only in Japan but worldwide. SCSK aims to be in the first tier in the IT services industry, focusing on five strategic business domains; industry, finance, solutions, products and services, and mobility.