Electroimpact
As a supplier to global aircraft manufacturers, Electroimpact’s customers are demanding a more streamlined and integrated digital design environment.
Transforming business operations and standardization in aircraft manufacturing
When the world’s leading aircraft manufacturers develop a new aircraft, more often than not Electroimpact is involved long before the first CAD line is drawn. Electroimpact develops machines that build commercial aircraft, and is one of a handful of players performing a critical role in the aircraft-manufacturing ecosystem.
Founded in 1986 as a supplier of machine tools to Boeing, today Electroimpact designs, manufactures, maintains and supports aerospace machines, tools, jigs, riveters, specialty machines and manufacturing equipment, including advanced Automated Fiber Placement machines. It is the largest integrator of aircraft assembly lines in the world and a leader in equipment for wing manufacturing, developing wing assembly systems for the Airbus A350 and A380, Boeing 777x and the Bombardier C-Series.
But more than that, Electroimpact is involved in the early stages of project planning to help manufacturers plan factory space, production processes and workflows. For example, Electroimpact supplied a complete assembly line system to a UK plant in Burnley for its new engine program.
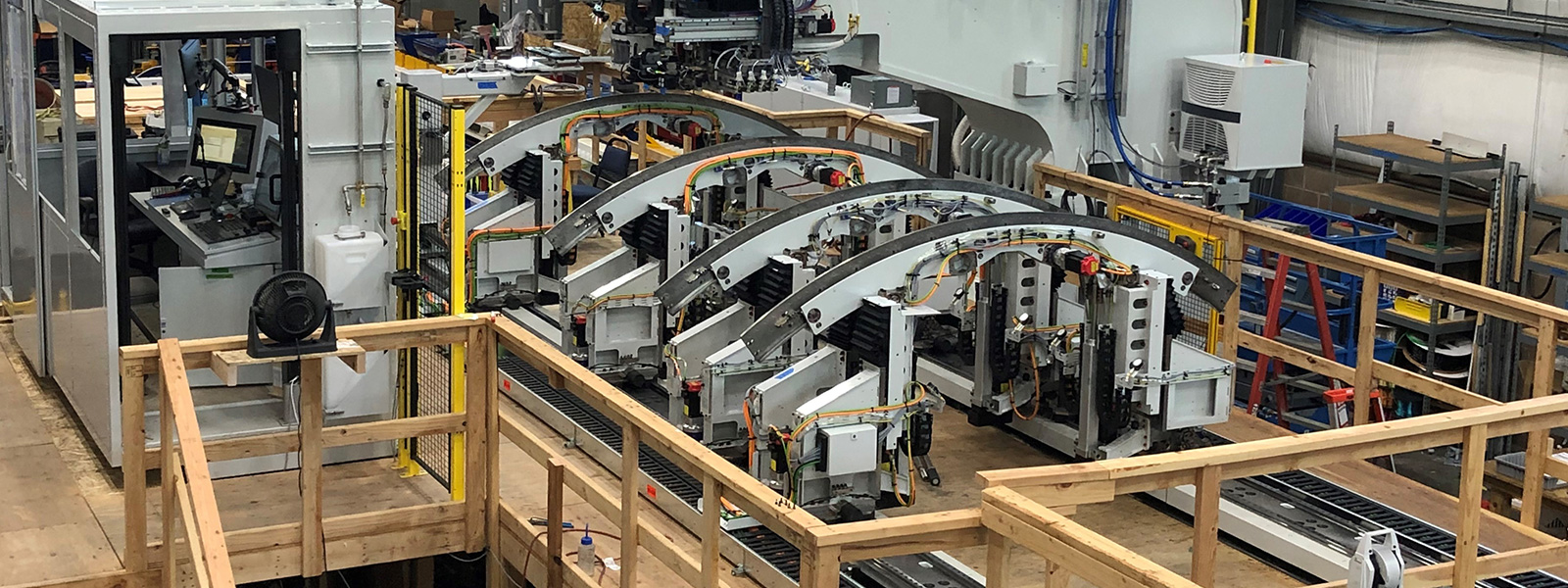
Electroimpact’s business ethos is unique among manufacturers, described by Ben Hempstead, mechanical engineering lead and chief of staff at Electroimpact, as “the ultimate engineer’s company.” It is an engineering-driven business and most of its 430 employees, including senior management, are highly skilled engineers. A small team owns each project—through the complete lifecycle—and is responsible for first customer contact and concept planning through design, build, installation and support, which includes finance, sales and marketing.
On day one, Electroimpact empowers and motivates its engineers with a company checkbook and keys to all the buildings. Project ownership is important to individual engineers and the business, and enables continuous improvement.
“If you design something without enough wrench clearance to tighten a nut and you bang your knuckles during assembly, you learn not to do that again,” Hempstead said. “This helps the design and development process and ultimately leads to better-built products.”
3DEXPERIENCE supports market-leading position
At Electroimpact, it is critical for engineers to help decide what software the business needs to improve operations and enable movement up the value chain. To maintain its market-leading position and continuity of service quality throughout the design process, Electroimpact chose Dassault Systèmes’ 3DEXPERIENCE® platform to replace its previous set of legacy design applications.
“Our various applications did integrate, but not quite in a seamless and interconnected way,” Hempstead said. “We had one situation where we developed a robotic arm for an assembly. When the time came for installation, redesign was needed because there was a mismatch in product and factory design files.”
One main driver for change was demand from customers who used 3DEXPERIENCE and wanted better compatibility with suppliers. The issue was evident when engineers presented different designs in incompatible file formats during a project for a leading aircraft manufacturer.
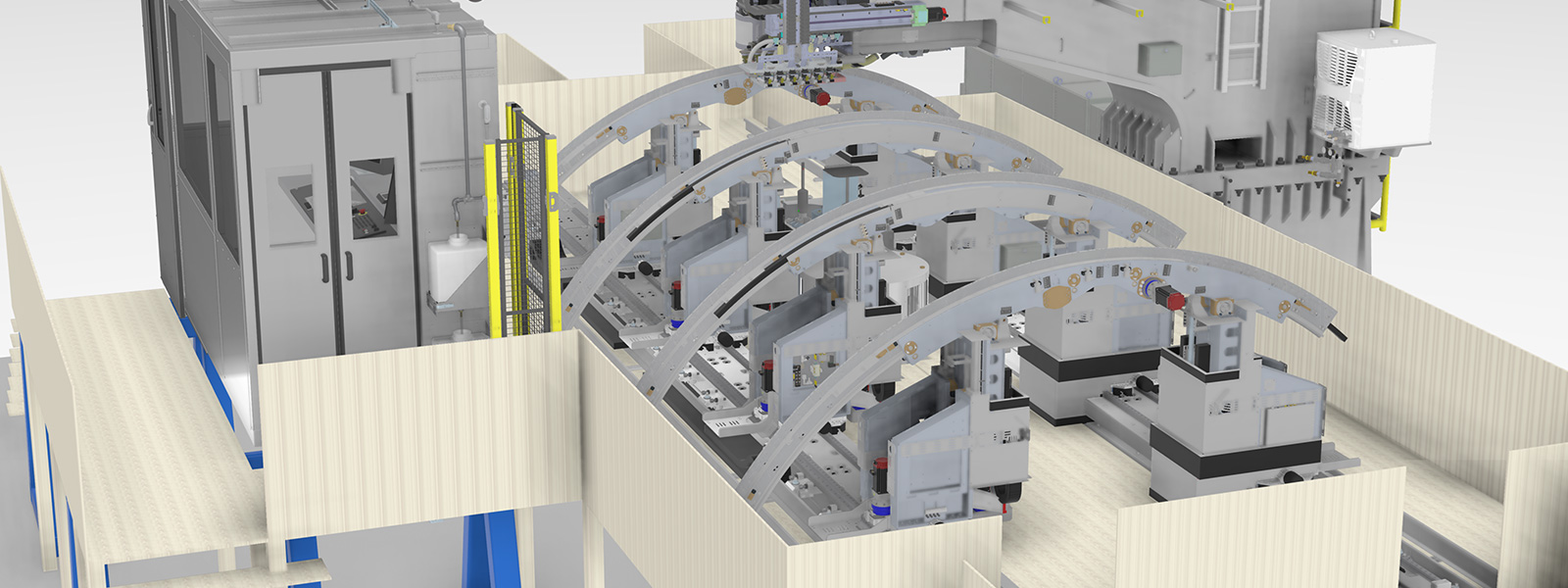
"Our largest commercial aviation customers have initiatives to adopt the platform, so we needed to respond to that,” Hempstead said. “We wanted to consolidate designs on the same platform, and it fits well with the type of design we do. The final issue is: How can we stay ahead of the competition? There are alternative solutions in the market, but we found they are not as comprehensive and integrated as 3DEXPERIENCE.”
Electroimpact extended its long relationship with Inceptra, a Dassault Systèmes business partner who managed installation, onboarding and training, and set up an on-premise production server.
“We value our partnership with Inceptra, and it has been key to our successful deployment,” Hempstead said. “Their response to technical issues is efficient and nimble. Prior to engaging with Inceptra, we did not have a relationship with Dassault Systèmes, but Inceptra helped us make the right connections, got us a voice at the table and enabled us to forge a strong relationship with Dassault Systèmes.”
In 2020, Electroimpact started deployment of the 3DEXPERIENCE platform, including CATIA for product design, ENOVIA for collaborative innovation and DELMIA for global operations such as off-line programing, robotics, mechanical design and factory planning.
Enabling seamless integration
In addition to adopting the platform, Electroimpact also decided to implement a new ERP (Enterprise Resource Planning) system, Microsoft Dynamics 365, and integrated it with 3DEXPERIENCE for a seamless two-way exchange of data between the two applications.
Unlike many industrial products—such as a car—the machines that Electroimpact builds do not have a standard catalog of parts. The seamless interchange between 3DEXPERIENCE and Dynamics helps develop libraries of parts to improve procurement processes. Since Electroimpact is one of the first to integrate 3DEXPERIENCE with Dynamics, it uses Connectivity Studio from To-Increase to establish a bi-directional data exchange between the two systems and its legacy PDM, Keytech.
“This kind of integration and connectivity is important because it reduces the need for customization,” said Hempstead. “But more importantly, it allows continuous, real-time bill of material data from 3DEXPERIENCE into Dynamics. Most ERP systems need the bill of materials completed before data is exchanged.”
Achieving critical business goals
3DEXPERIENCE sits at the core of Electroimpact’s business operations, connecting with key business systems to provide a holistic and integrated workflow process for product design and development. This helps Electroimpact improve operations, productivity, standardization and customer service.
“Are we able to meet our customer needs and provide the information they need in a seamless way?” Hempstead said. “Can we run the business better and more productively? Can our engineers collaborate and work effectively and efficiently? On all three counts, 3DEXPERIENCE is helping achieve those goals.”
3DEXPERIENCE also influences business performance. “We are looking at using 3DEXPERIENCE to deliver key business metrics,” he said. “It is going to help us run projects with fewer engineers, which means we can get products to market faster for less cost and give Electroimpact a competitive advantage.”
Approximately one third of each new product is designed from scratch. We are using 3DEXPERIENCE to help standardize products and reuse existing designs so we’re not repeating work, and can increase productivity and efficiency.
An original driver for deploying a new platform was standardization. ENOVIA on the 3DEXPERIENCE platform is helping to bring teams together, use different applications within the same platform and improve collaboration. The other important area is product standardization. Hempstead cites an example of a car where the light switch part is the same on every brand of car, but Electroimpact products are different.
“Approximately one third of each new product is designed from scratch,” Hempstead said. “We are using CATIA and ENOVIA to help standardize products and reuse existing designs so we’re not repeating work, and can increase productivity and efficiency.”
3DEXPERIENCE fundamental to Electroimpact's future
Although Electroimpact is still rolling out the 3DEXPERIENCE platform, two projects with a European business jet customer and a Japanese fuselage manufacturer utilized the platform. The European-destined project involves developing and supplying a robotic fastening assembly system for wings and fuselage on the company's just-launched latest generation of business jets. The customer recently commissioned Electroimpact to start the second phase of the project for five more robots for planned production rates.
For a Japanese Tier 1 supplier, Electroimpact designed and built a large C-frame riveter for fuselage panels on a commercial aircraft. The design team on the project was comprised of early 3DEXPERIENCE adopters who have imported existing parts assembly designs using ENOVIA POWER'BY, with around 50 percent of designs modified.
Deploying 3DEXPERIENCE also is important in supporting Electroimpact’s involvement in future strategic industry initiatives.
“Having 3DEXPERIENCE puts Electroimpact in a much better position to participate in these programs," Hempstead said. “As early adopters, we have a chance to forge a new way of working that will set the standards for other suppliers in the industry to follow.”
In the future, Electroimpact plans to develop virtual twins using 3DEXPERIENCE, which will allow its engineers to virtually simulate, test and correct errors for parts and products before incurring high production costs.
“Because we are still migrating several projects from our old platform, today 3DEXPERIENCE probably represents about 20 percent of our business,” Hempstead said. “But as we consolidate on 3DEXPERIENCE over the next few years, its importance to the business is going to be huge. 3DEXPERIENCE will be fundamental to how we work and the quality of products and services we deliver to customers.”

Focus on Electroimpact
Electroimpact is a world leader in aerospace tooling and automation design and manufacturing. The company has become the largest integrator of aircraft assembly lines in the world. The company’s headquarters are located in Mukilteo, Washington, with development operations in the UK and France, and additional offices around the world.
Revenue: $96.3M
Employees: 430
Headquarters: Mukilteo, Washington (US)
For more information: www.electroimpact.com
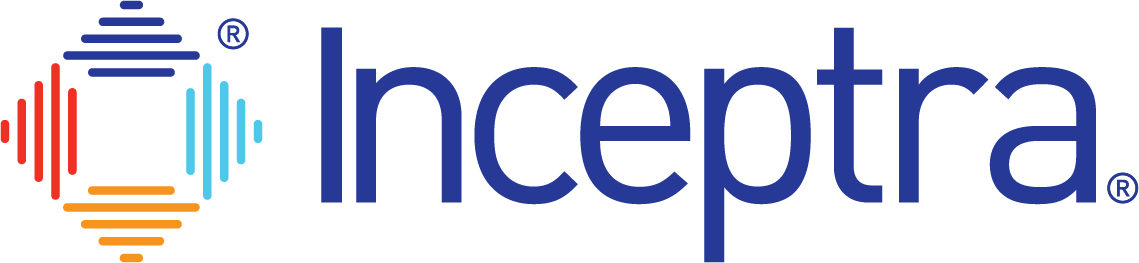
Focus on Inceptra
Inceptra helps engineering and manufacturing enterprises of all sizes across a variety of industries with best fit solutions to digitally design, simulate, produce, and manage their products and processes, enabling enhanced innovation and productivity. We are dedicated to Dassault Systèmes’ product portfolio, plus complementary software and internally developed PLM acceleration solutions. Inceptra’s offerings include software, support, training, and consulting services, including integration services, automation services, and industry best practices.