Increased Awareness Of Supply Chain Risk
Supply chains around the world are under unprecedented pressure, and building resilient, flexible, and transparent supply chains is of critical importance.
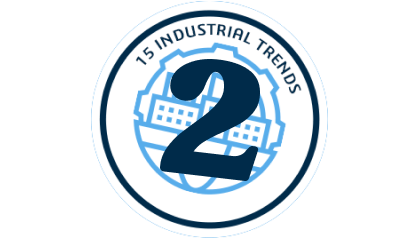
In an age of unprecedented disruption, are your supply chains safe?
What's happening?
For a week in March 2021, the 400m-long Ever Given container ship was stuck in the Suez Canal. As teams worked to free the vessel, 369 ships waited for passage through the canal, costing around $9.6 billion in disruptions to global trade.
If this was a tragicomic illustration of just how fragile our global supply chains can be, then COVID-19, the Russian invasion of Ukraine, and the recent flooding in Pakistan serve as more serious cautionary tales.
These difficulties pile up. Since 2020, the price of sending a container from Asia to Europe has risen by a factor of ten, and 80% of companies report that they expect disruptions to affect their supply chains, according to a 2020 IDC whitepaper.
This trend has prompted governments around the world to increasingly look to encourage localizing production or reshoring. Whether through regulation or subsidies, there has been a political push to minimize dependency on external suppliers and trade routes. However, this would only work to a certain extent with many in-demand materials and components available from a few specific regions.
Supply chain resilience is also not just about reacting to present problems. The speed of market and technological transformation means that for businesses to remain resilient, they need to keep an eye on where their sectors are going and what that means for their supply chains in the future.
“Developments over the next five to ten years will necessitate a massive shift in the aerospace supply chain, for example,” says David Ziegler, Vice President, Aerospace and Defense Industry. “There will need to be the sourcing of alternative suppliers for new sustainable technologies, and that means the supply chain will have to be completely reshuffled.”
In the face of these present and future challenges, ensuring resilience in your supply chain is business critical for manufacturing industries. As Gartner found in its 2021 Supply Chain Study, 87% of the companies they surveyed said they planned to invest in supply chain resilience.

Curious about how other manufacturing industries respond?
Respond to today's challenges with our bespoke solutions
Why does it matter?
There’s an old saying in military strategy – “no plan survives contact with the enemy”; or, as Mike Tyson more simply put it: “Everyone has a plan until they get punched in the face.”
Plans change constantly. Supply chains get broken. The key differentiator in today’s fast-moving environment is not just having a plan, but having the ability to adapt, react, and modify that plan when disaster strikes. There lies the path to supply chain resiliency.
Even small supply chain disruptions can be critical ones. “There are 6,000 parts in a car, and you need every one of them,” says Laurence Montanari, Vice President, Transport & Mobility, Dassault Systèmes. “If just one part is missing, you can’t complete the car.”
The route to supply chain resilience has several elements, and some of this includes simply working with trustworthy partners. “The first concern is to restructure your supply chain to have more tier one suppliers that you can rely on,” says Ziegler. “You need suppliers that can find you the parts you need, and that have the finances lined up to pay for them.”
Perhaps most crucial, though, is for manufacturers to establish clear supply chain visibility, so potential disruptions can be effectively identified and addressed.
“It is about being able to monitor the full supply chain, across its whole length, with full supply chain transparency,” says Ziegler. “That means ensuring that you watch for signals and catch any that may indicate a drop in quality, a problem in logistics, a lack of investment, or anything else that could cause disruptions.”
However, different timescales entail different challenges, and will necessitate different approaches. Over the next five years, the focus will understandably be on building more resilience into existing supply chains and reassessing approaches to sourcing to make sure suppliers are financially viable and operate in areas that are less likely to get disrupted.
Beyond this time period, new technologies will necessitate new materials and alternative suppliers, meaning the ecosystem will need to be reshuffled once more. This tech-driven transformation can already be seen in the shift to electric vehicles in the auto industry and is currently underway in the aerospace and maritime sectors.
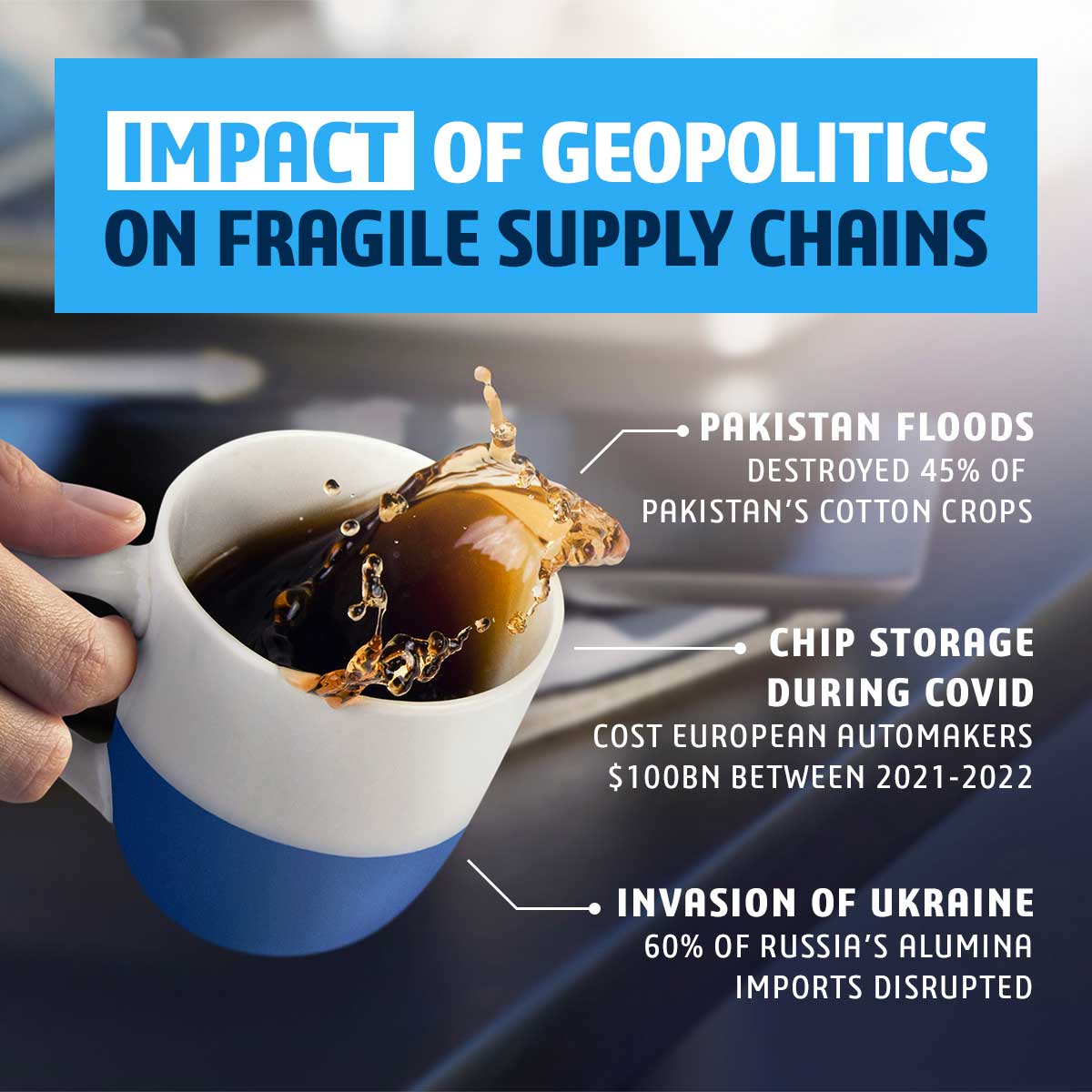
How can I prepare?
Whether it is integrating greater accountability and flexibility into an existing supply chain or creating new ones to meet the demands of a changing industry landscape, total visibility is essential for effective and sustainable supply chain management.
Digital solutions are playing an increasingly important role in enabling this oversight. By sharing and monitoring real-time information, better decisions can be made further down the value chain and plans adapted accordingly.
But in order to be able to preempt rather than react, businesses need to be able to model and test scenarios. This is where the rise of virtual twins of supply chains, like the ones Dassault Systèmes are developing, are set to be a game changer.
While there have been virtual versions of products for some time, a virtual twin of the industrial system is something new. The challenge lies in persuading your OEMs and their suppliers to provide a constant stream of information on their operations. But the upside for all parties is considerable.
By combining a virtual supply chain with Model Based Systems Engineering (MBSE), you can model any disruptions into your supply chain, build ‘what-if’ scenarios, and make sure that there are contingency plans at every stage of production, from extraction to the last mile.
“It’s very complex to model the supply chain, and understand your suppliers, and your suppliers’ suppliers, because that information is very diffused” says Montanari. “But if you can do that modeling, then you can build truly resilient businesses, with full supply chain agility and supply chain flexibility.”
The hyper-efficiency but intrinsic vulnerability of global supply chains has come to the fore in recent years and businesses have been scrambling to build greater resilience into their operations. Digital technology will play an increasingly important role in helping them predict and adapt to whatever.
Other Trends
Discover more with our Manufacturing Industries
- Aerospace & Defense
- Consumer Packaged Goods & Retail
- Home & Lifestyle
- High-Tech
- Industrial Equipment
- Marine & Offshore
- Transportation & Mobility
Bridge the gap between the virtual and real world to accelerate from concept to operations
When consumers want it yesterday, be first to make it and first to market.
As complexities increase, future readiness is needed to establish agile and resilient operations from end to end. Discover how the virtual twin roadmap can help.
Virtual Twin Experiences for Sustainable Innovation – Helping Manufacturers Improve Consumer Products
Simplify and accelerate innovation to create more valuable consumer experiences.
Modular supply chains make it easier for manufacturers to master complexity and strengthen their supply chain resilience against volatility.
Accelerate the sustainable transformation of the Marine & Offshore industry.
Driving vehicle innovation toward the mobility of the future
THE WORLD NEEDS MANUFACTURERS
A MANIFESTO FOR CHANGE
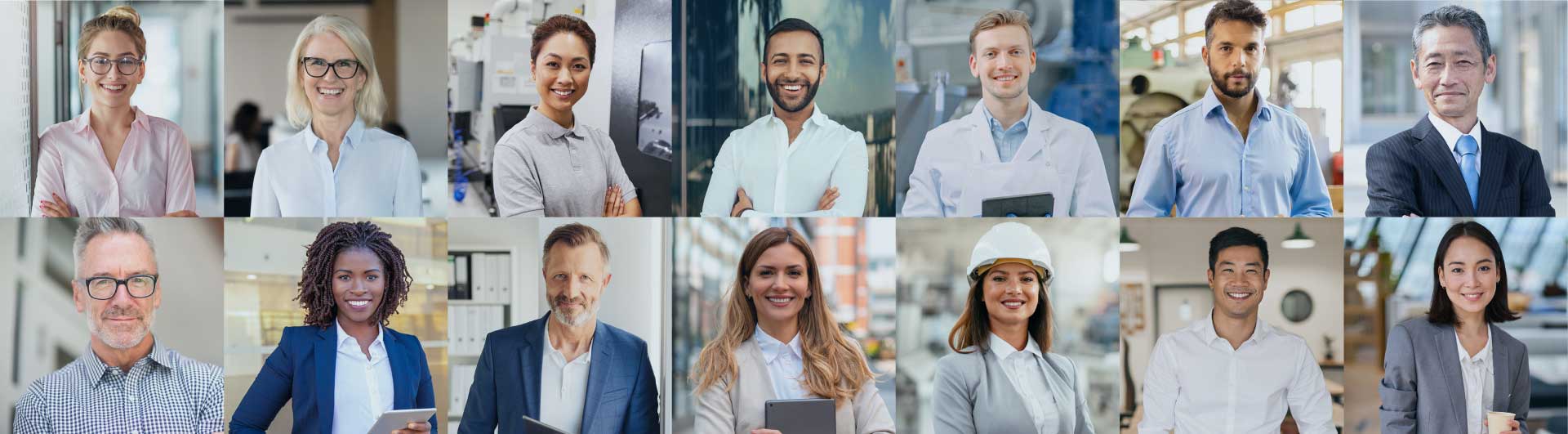