What is solid modeling and why is it so essential to design?
Solid modeling is a computer aided design technique that transforms 2D designs into 3D images using 3D solid modeling software. It is used to generate geometrically correct digital representations of planned or existing products, structures, machines, or components.
What is solid modeling?
A basic solid modeling definition is that it is a process used to create geometrically realistic digital objects in three dimensions from a two dimensional draft. Although commonly used across a wide range of industries, solid modeling is considered to be one of the most difficult CAD skills to master.
In most cases, a design for a product, structure, or machine will first be done as a rough 2D sketch. This sketch will contain the physical dimensions of the object, what materials are to be used, and depicts how the components will work together and what the object should look like when it is manufactured.
Using solid modeling software, a designer can take this rough sketch and transform it into a highly realistic three dimensional digital representation that has volume, boundary surfaces, holes, and voids. A solid model can be viewed from any angle, it can be sliced into sections, and it can be used to simulate how an object will react to real world stresses.
Discover our solid modeling solutions in the Dassault Systèmes store
The solid modeling solutions from Dassault Systèmes have been used by leading engineers and designers for over 40 years. Visit the Dassault Systèmes online store today to explore our range of powerful CAD software.
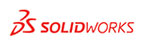
SOLIDWORKS xDesign
Get ready for the next generation of design solution, developed by the same team that brought you SOLIDWORKS 3D CAD
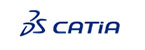
CATIA Mechanical Designer
Design on your terms with expert applications that cover the end-to-end mechanical design process
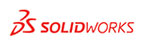
3DEXPERIENCE SOLIDWORKS
From mechanical 2D or 3D design to manufacturing, accelerate your processes at an affordable price.
What is the difference between solid modeling and surface modeling?
There are two main techniques used in creating CAD models: solid modeling and surface modeling. While both of these models are created using CAD software, the processes used to create these types of models and how they are used in practice are quite different.
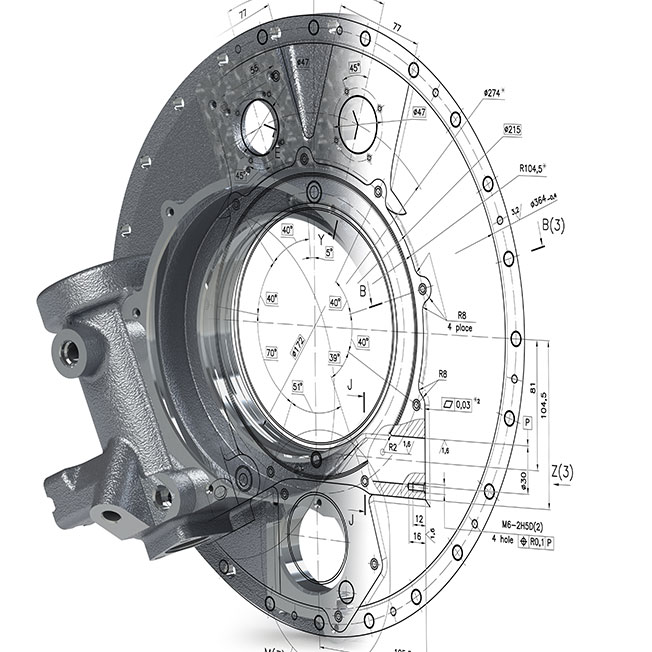
Solid modeling vs surface modeling
The main difference between wireframe surface and solid modeling is the depth of information that they convey. A solid model is a precise depiction of an object. The object may already exist in the real world, or it may be theoretical in nature.
A solid model is based on the details provided by a designer or engineer’s 2D plan. Solid models are intended to be as realistic as possible with volume, boundary surfaces, perforations and holes, and voids. Solid models can be viewed, manipulated, tested, and sectioned just like physical objects.
Surface modeling is mainly used for visualization purposes. It provides designers and engineers with information on the surface geometry of an object. Surface models are used to improve the ergonomics, aerodynamics, or aesthetic appeal of an object. Unlike solid models, surface models cannot be sliced into sections and do not need to be as precise.
Browse all the Dassault Systèmes store applications
We feature in our store some of our best software to design, collaborate and innovate throughout the entire product lifecycle.
Content related to solid modeling
Making 3D models with solid modeling techniques
What does the process of making 3D models with solid modeling techniques look like? While every designer or engineer will have their unique process and workflow, there are general steps that professionals follow when creating a 3D model with solid modeling techniques.
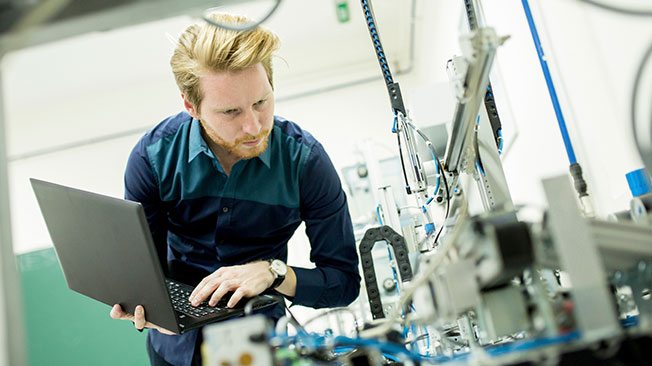
Define the design intent
Designers and engineers begin the process of creating a solid model by first establishing the intent of their design. To do this, they must consider questions such as:
- What is the desired function of the object?
- What will its physical form look like? What will it be made from? How will it react in its environment?
- How will it operate in communication with other parts or objects?
Sketch the object
Once the design intent has been established, a rough plan of the object should be completed. Some designers and engineers sketch manually, but the majority now use 2D CAD software.
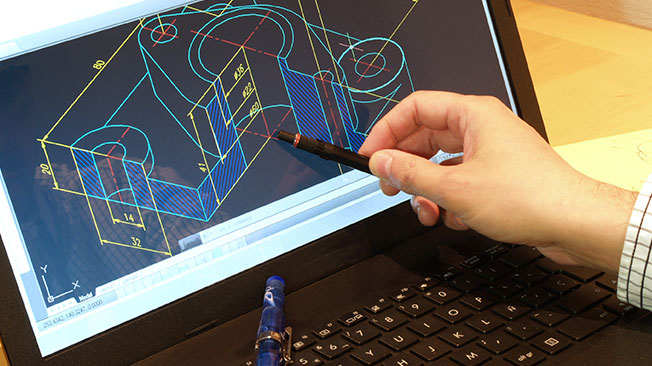

Convert the 2D sketch into a 3D model
Assuming the designer produces a 2D file, the actual modeling process is done using a CAD program to convert it into a detailed 3D solid model. The 2D sketch is converted into a 3D model by using commands in solid modeling software such as:
- Extrude
- Revolve
- Sweep
- Loft
Refine the 3D model and add textures
A designer can further enhance their 3D solid model by adding textures to it. Textures make the model seem more lifelike and are crucial for designs that include repeating geometric features or patterns.
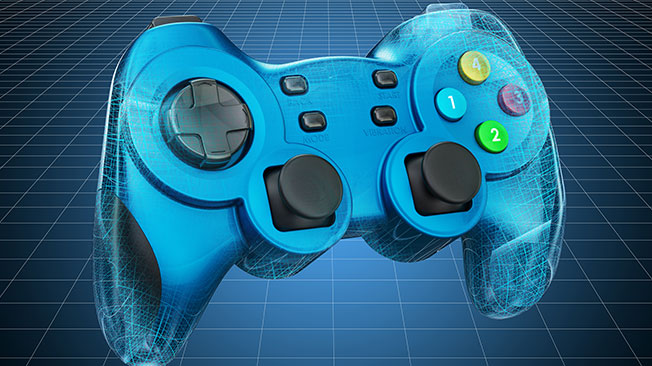
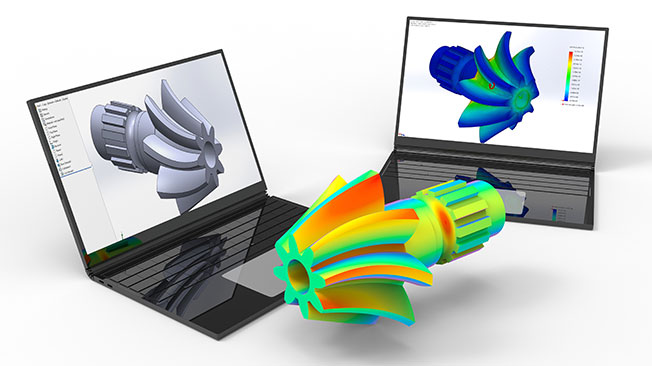
Simulation and analysis
When a solid model has been sufficiently refined, it then enters the prototyping phase. Different materials, components, environmental stresses, or assemblies may be tested to arrive at an optimal design.
Manufacturing
The finalized 3D solid model can then be converted into a machine file and used for Computerized Numerical Control (CNC) manufacturing.
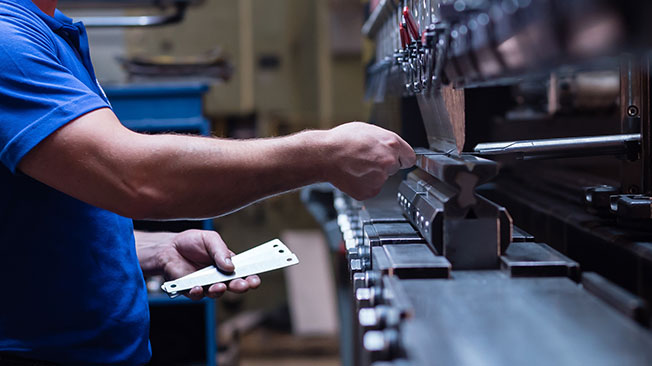
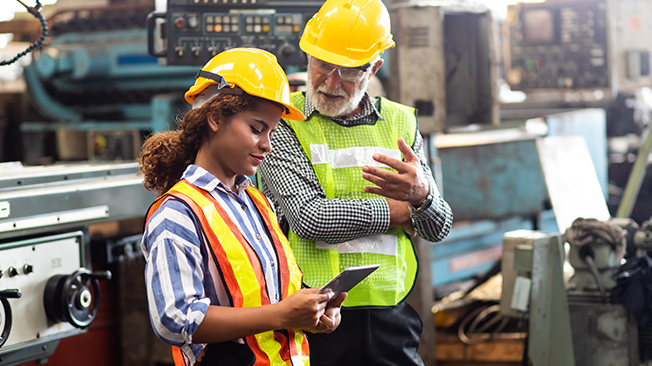
Review and validation
Once manufacturing is complete, designers and engineers conduct a thorough review of the entire process. All aspects of the process are analyzed to identify ways to improve efficiency and cost-effectiveness.
What industries use solid modeling?
As we can see from the above example, solid modeling is used comprehensively in the manufacturing industry. However, solid modeling is also vital for many other sectors.
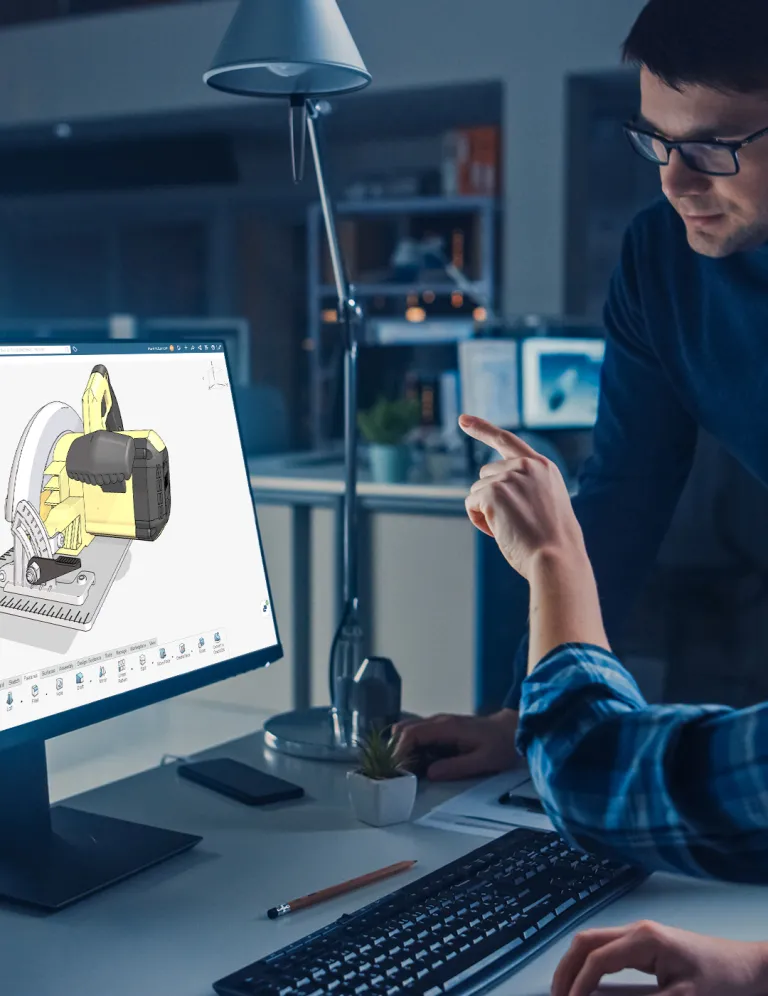
Is solid modeling difficult to learn?
Solid modeling is considered to be one of the more challenging CAD skills to master. To come to grips with the intricacies of solid modeling, beginners need to allow themselves enough time to learn the complexities of solid modeling principles and how to best use solid modeling software.
Although it may seem a daunting task, with the right mindset and the right tools, it is possible to become highly proficient in solid modeling in a relatively short amount of time.
Choosing the right software is important for anyone who wants to learn solid modeling techniques. Just as professionals do, students should look for a solution that is flexible, powerful, and affordable.
If you are thinking about learning 3D solid modeling, you should look for a software solution that is compatible with a range of files and devices, is powerful enough to meet your needs, is used by industry professionals, and allows you to store and share your work securely.
The essentials of parametric solid modeling
- Precise mathematical parameters
- Consistent structural integrity
- A realistic, complete depiction of a physical object
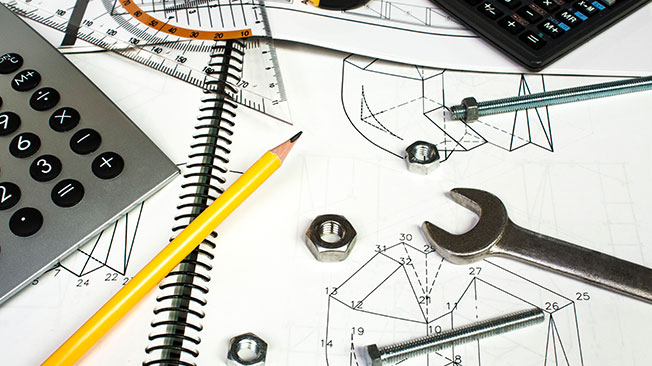
Precise mathematical parameters
Mathematical precision is one of the essentials of parametric solid modeling. A solid model is created using specialized mathematical algorithms to subtract and add mass to a digital object.
The shapes that are added and subtracted are defined and controlled by preprogrammed dimensions, known as parameters. A designer can use these parameters to automate changes as the design progresses. All provided parameters must be exact in order to avoid design and manufacturing errors.
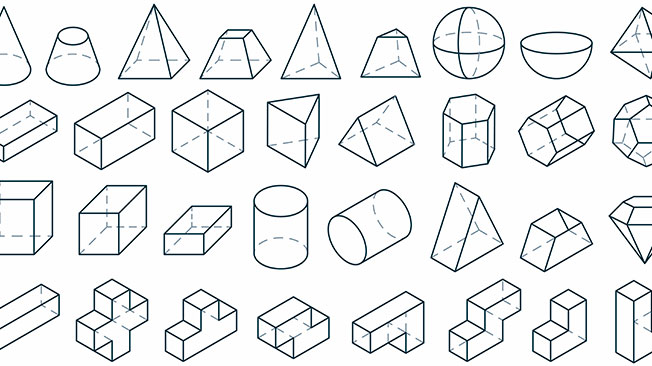
Consistent structural integrity
A mechanical engineer or designer will create a solid model using spheres, cylinders, and cubes. These shapes are added or subtracted from the model without the model losing the integrity of its original structure.
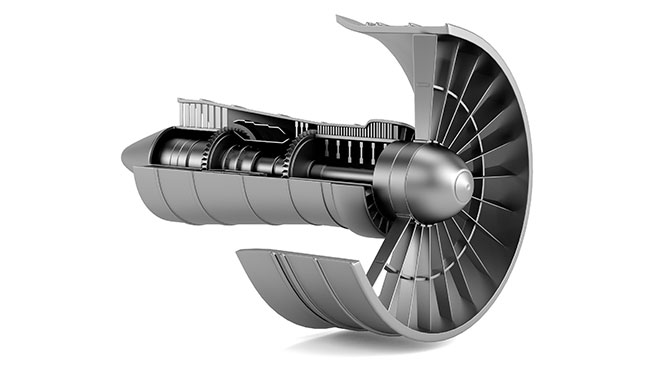
A realistic, complete depiction of a physical object
Solid models are complete representations. That is, they depict both the inside and outside of an object. All vertices, edges, and faces of the model fit together perfectly so the model can be viewed from any angle. All geometric and topological information represented by the model should conform exactly to its physical form.
Solid modeling : conclusion and perspectives
Solid modeling was a milestone in the evolution of engineering and design. Designers and engineers are now able to produce designs in less time, generate highly accurate representations that can be viewed in three dimensions, and test their designs without the expense of having to produce numerous drafts or build several physical prototypes.
Everything from the homes that we live in, to the movies that we see, the cars we drive, and the equipment that doctors use to save lives has been made possible because of solid modeling techniques. Solid modeling software enhances the ability of design and engineering professionals to create, innovate, and inspire.
The designers and engineers of today and the future will continue to turn to innovative and dynamic companies such as Dassault Systèmes to provide them with the tools they need.
Why choose Dassault Systèmes for your solid modeling needs ?
The power of the 3DEXPERIENCE platform
Stay on top of your project and ensure the highest levels of collaboration, security, and flexibility with the 3DEXPERIENCE platform. You can track the progress and monitor the productivity of your team with personalized dashboards. Automatic back-ups and syncing ensure that you never have to worry about losing work and that users are always working on the most up-to-date file.
As your business grows, you can scale the 3DEXPERIENCE platform to meet your needs. Individual roles can be purchased to suit each team member’s needs for precisely the amount of time that they require them.
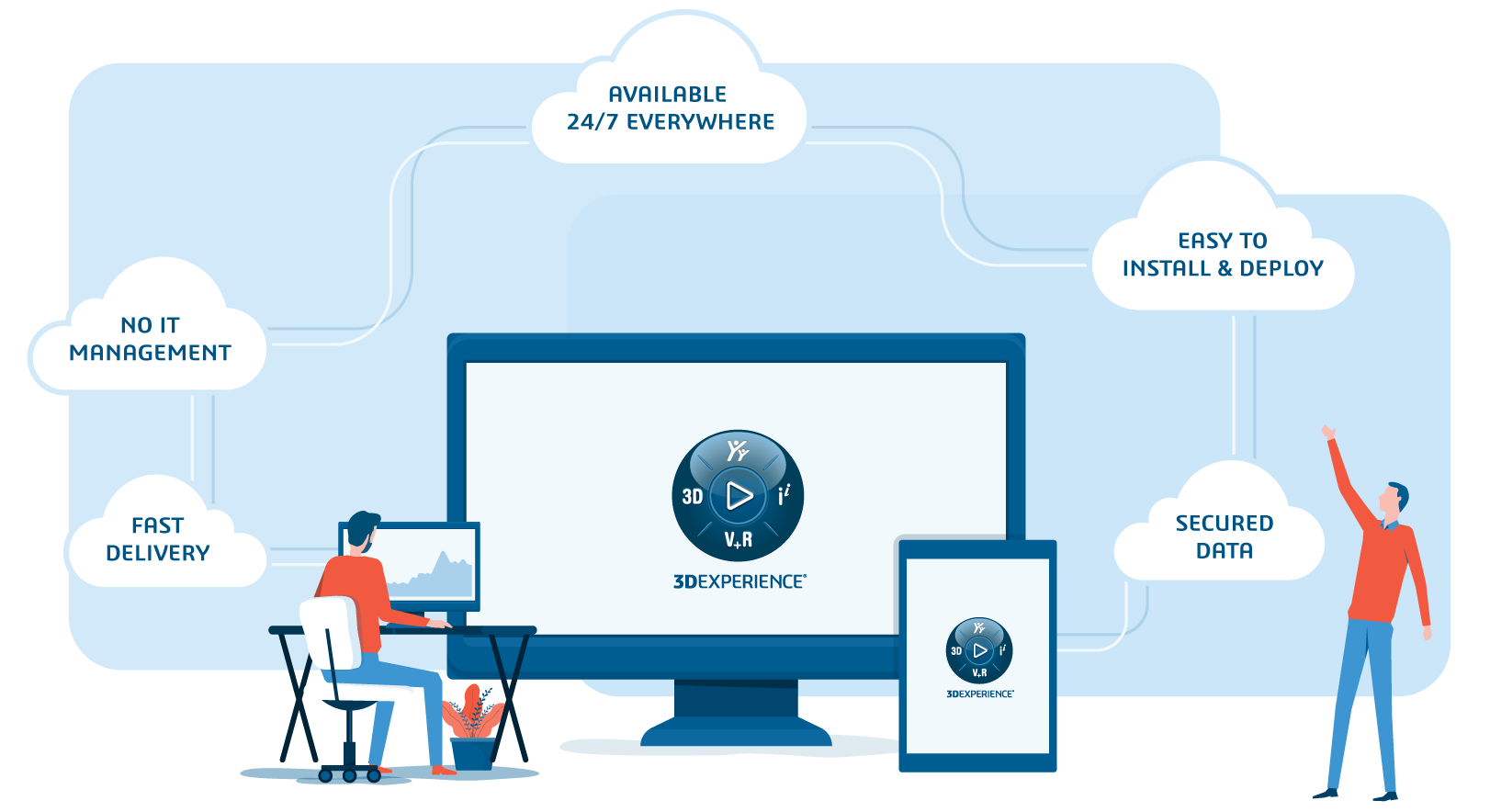
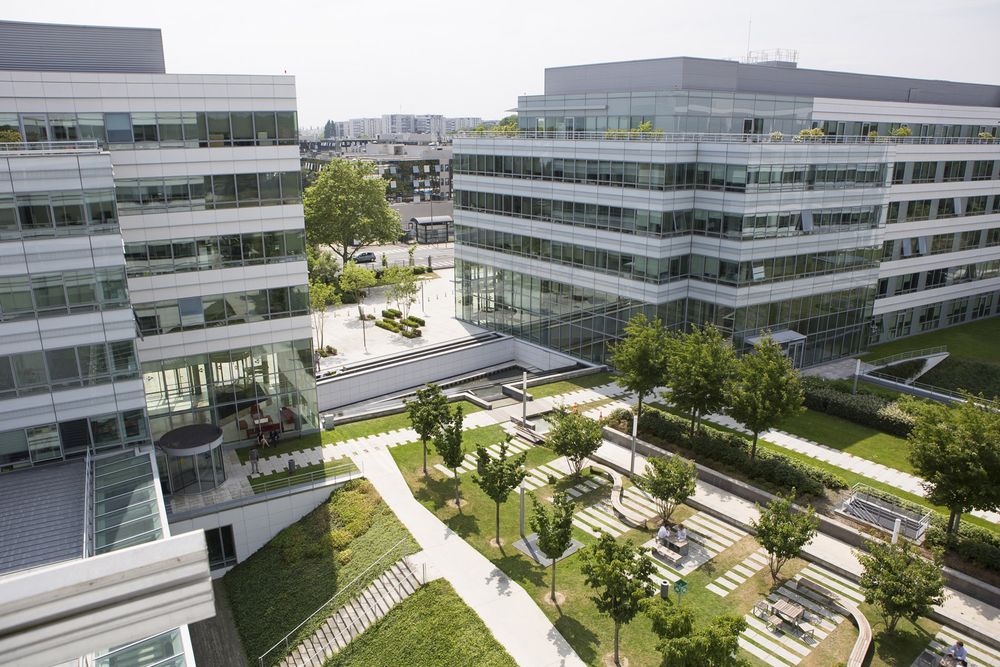
More than 40 years of experience
With more than four decades of experience, Dassault Systèmes is trusted and respected by 3D modeling professionals the world over. Engineers and designers from diverse industries know that we are the team to turn to for reliable, versatile, and powerful CAD solutions.
From a background in the aerospace industry, Dassault Systèmes first established itself as a force to be reckoned with the creation of CATIA in the early 1980s. CATIA is still widely recognized as the preeminent CAD design program in the world today.