Von Prozessoptimierung bis Produktentwicklung – die Möglichkeiten von Digital Manufacturing
Heben Sie Ihre Entwicklungs- und Fertigungsprozesse mit Digital Manufacturing auf die nächste Stufe
Digital Manufacturing ist der Einsatz digitaler Technologien zur Verbesserung von Fertigungsprozessen durch Integration von virtuellen Modellen, Simulationen und Datenanalysen. Es zielt darauf ab, Effizienz, Qualität und Flexibilität in der Produktion zu steigern und die Zusammenarbeit zwischen Design, Produktentwicklung und Produktion zu optimieren.
Kurz ausgedrückt steht Digital Manufacturing für die Digitalisierung in der Produktion.
Was ist Digital Manufacturing und was unterscheidet es von der konventionellen Fertigung?
Digital Manufacturing ist eine moderne Optimierungsmethode, die sich von der konventionellen, nicht digitalisierten Fertigung unterscheidet. Bei Digital Manufacturing werden virtuelle Technologien und computergesteuerte Prozesse genutzt, um die Produktentwicklung voranzutreiben. Sie helfen dabei, Produkte zu entwerfen, zu testen und zu produzieren.
Im Gegensatz zur konventionellen Fertigung, die oft auf physischen Prototypen und manuellen Arbeitsabläufen basiert, ermöglicht Digital Manufacturing den Einsatz von virtuellen Umgebungen und Simulationen. Dies eröffnet völlig neue Möglichkeiten in der Prozessoptimierung, sei es zur Förderung von Innovationen oder zur effizienten Nutzung von Ressourcen. Zudem ist die Fehlerbehebung weniger kostenintensiv, da Änderungen im Engineering-Prozess einfacher und vor allem kostengünstiger umzusetzen sind, als am Ende der Fertigungskette. Durch den Einsatz digitaler Technologien produzieren Unternehmen flexibler, schneller, preiswerter sowie nachhaltiger und stellen sich somit den Herausforderungen einer zunehmend digitalisierten Welt.
Die Vorteile von Digital Manufacturing
- Effizienzsteigerung durch Prozessoptimierung
- Produktentwicklung und Produktdesign
- Nachhaltige Produktion und reduzierter Materialverbrauch
Digital Manufacturing revolutioniert den Produktionsprozess, indem es Unternehmen die Möglichkeit gibt, ihre Abläufe effizienter zu gestalten. Dank fortschrittlicher Softwarelösungen und virtueller Simulationen können verschiedene Szenarien durchgespielt werden, um potenzielle Engpässe frühzeitig zu erkennen und Fehler zu vermeiden. Diese Prozessoptimierung führt zu einer erheblichen Verkürzung der Time-to-Market und minimiert teure Iterationsschleifen. Darüber hinaus ermöglicht die präzise Planung von Ressourcen und Kapazitäten die Produktentwicklung sowie eine reibungslose Produktion.
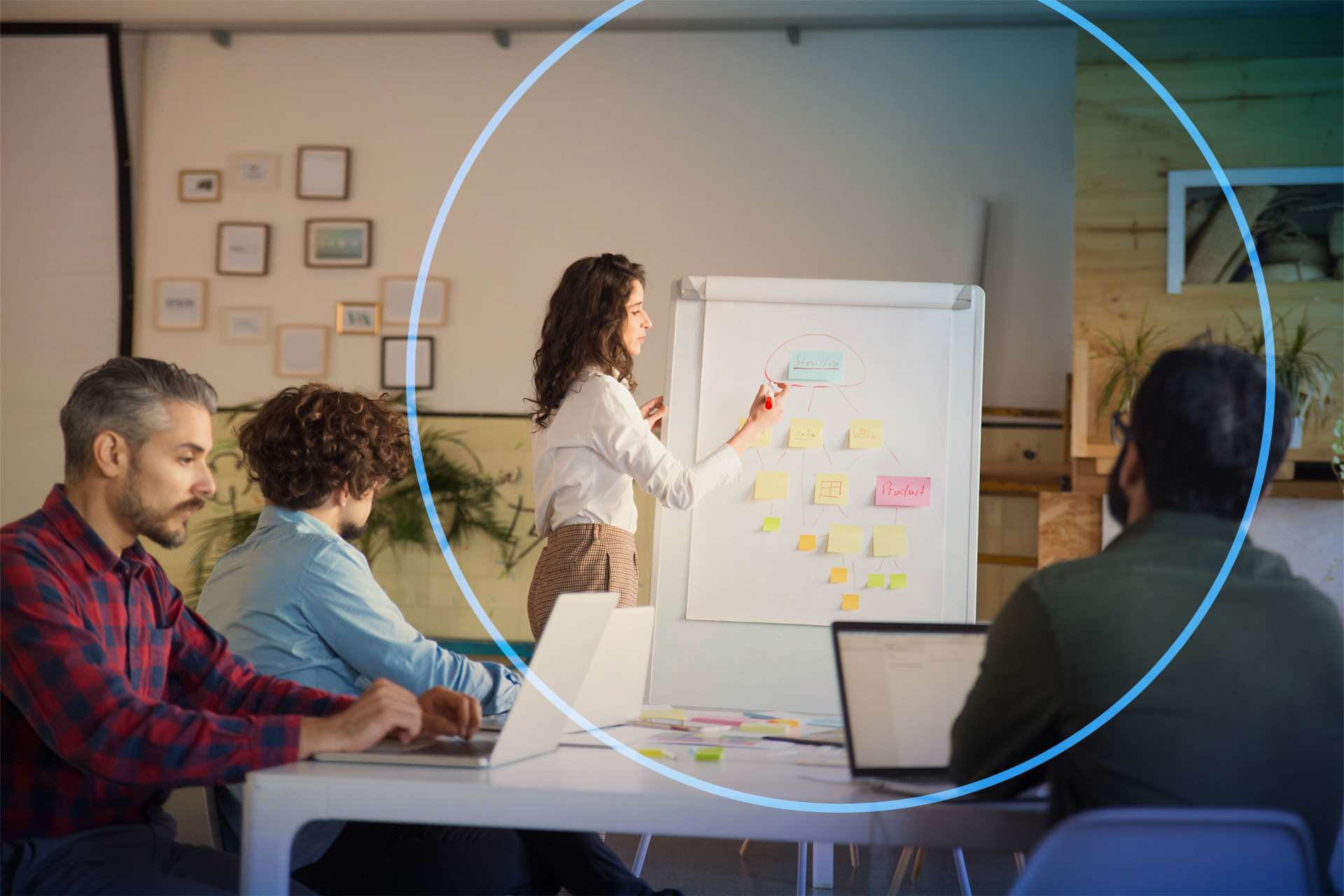
Digital Manufacturing eröffnet Unternehmen völlig neue Wege für die Produktentwicklung und das Produktdesign. Mithilfe von virtuellen Umgebungen werden Produkte bereits in einem frühen Stadium des Produktdesign-Prozesses getestet und optimiert. Dadurch setzen Unternehmen kreative Ideen schneller um und entwickeln innovative Lösungen.
Durch die nahtlose Integration von 3D-Modellierung, Simulation und virtueller Realität können Entwickler ihre Produkte visualisieren, analysieren und verbessern, bevor sie physisch produziert werden. Dies minimiert Risiken der Produktentwicklung und maximiert das Potenzial für bahnbrechende Innovationen.
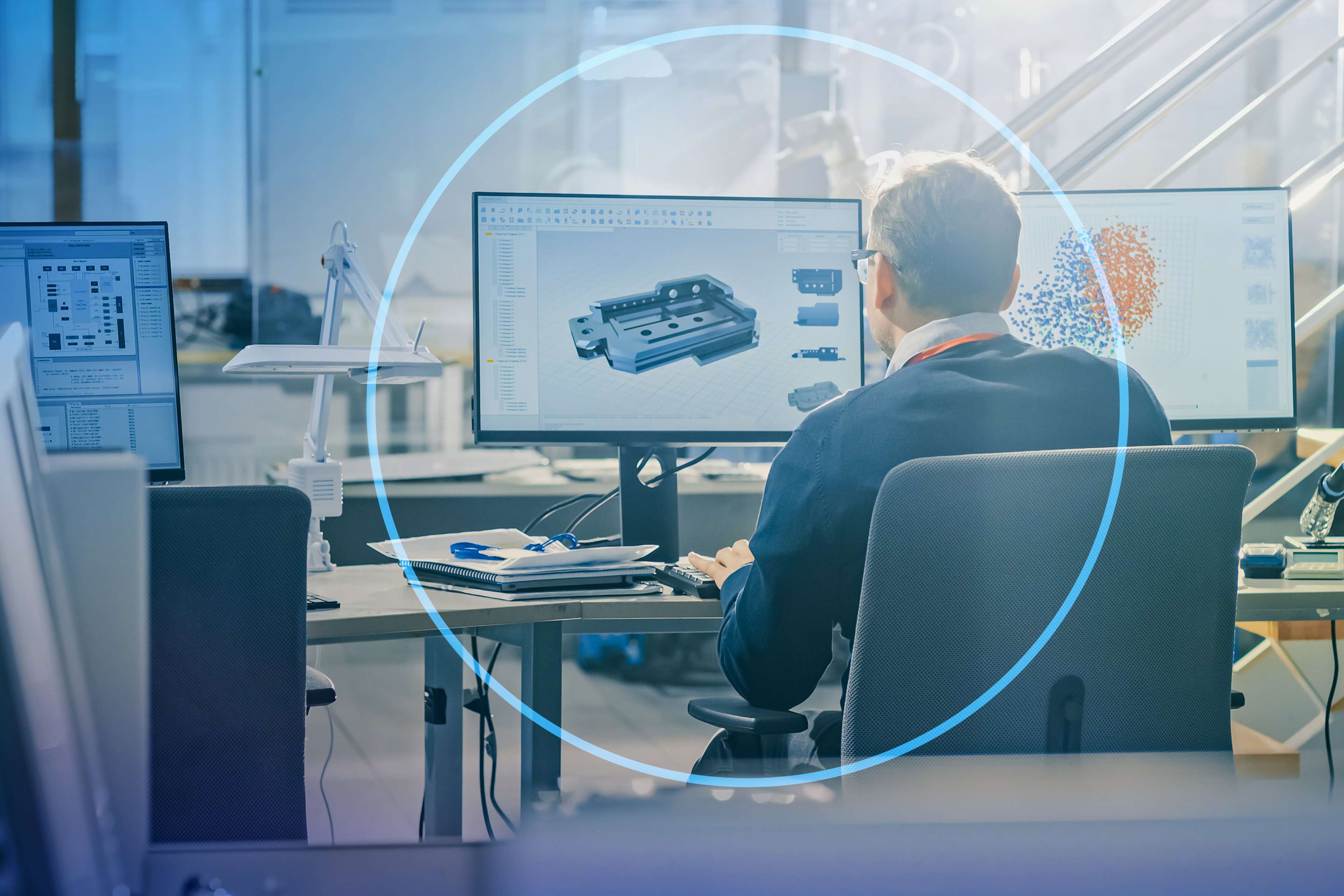
Digital Manufacturing spielt eine Schlüsselrolle bei der Förderung von Nachhaltigkeit in der Produktion. Unternehmen nutzen dank Prozessoptimierung und dem Einsatz virtueller Umgebungen Ressourcen wie Material, Energie und Zeit effizienter. Die Möglichkeit, Produkte virtuell zu testen und zu simulieren, reduziert den Bedarf an physischen Prototypen und verringert somit den Material- und Abfallaufwand. Darüber hinaus ermöglicht die digitale Steuerung und Überwachung der Produktion eine präzisere Planung und Ressourcenzuweisung, was zu einer Reduzierung des ökologischen Fußabdrucks führt und eine nachhaltige Produktion ermöglicht.
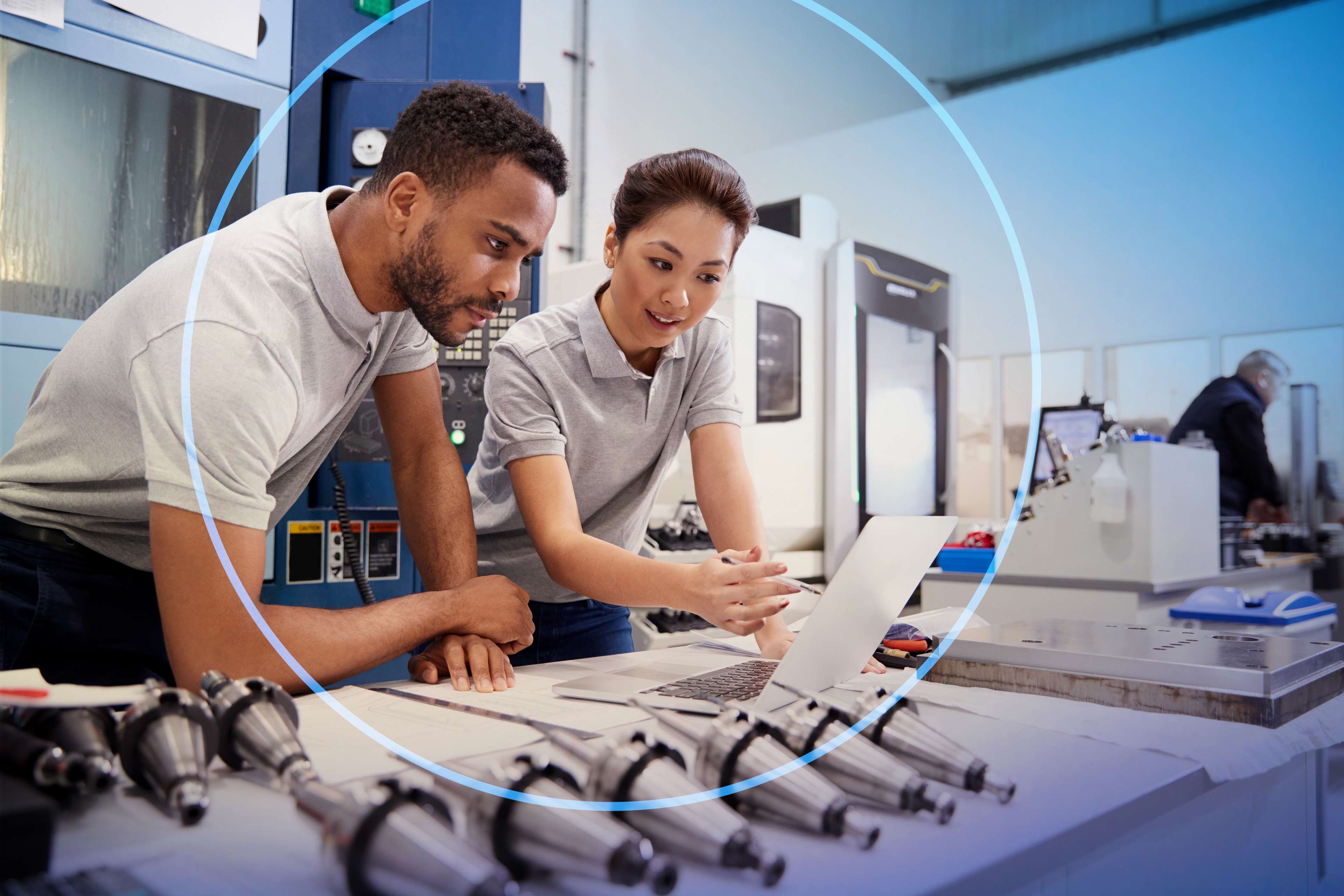
Digitale Prozessplanung im Unternehmen
Die digitale Prozessplanung ist der Einsatz digitaler Tools und Methoden zur Planung und Optimierung von Unternehmensprozessen. Sie ermöglicht eine detaillierte Modellierung, Simulation und Analyse von Abläufen, um Durchlaufzeiten zu verkürzen, Ressourcen effizient einzusetzen und Fehler zu vermeiden. Die Nutzung von Prozessplanung Software ist ein Schritt in die Richtung von Industrie 4.0 und der digitalen Transformation.
Die Digitalisierung der Prozesse mit Hilfe von Prozessplanungs Tools erfolgt durch den Einsatz von spezialisierten Softwarelösungen und Technologien. Diese fördern die digitale Prozessplanung der Produktion und ermöglichen die Integration von Echtzeitdaten und die Zusammenarbeit zwischen verschiedenen Abteilungen und Mitarbeitern. Durch den Einsatz von digitalen und cloudbasierten Plattformen werden relevante Informationen und Daten transparent und in Echtzeit geteilt, was die Kommunikation und Koordination verbessert. Ebenso ist es Unternehmen dank digitaler Software & Operations Planning möglich, auf kurzfristige Komplikationen wie Lieferschwierigkeiten zu reagieren. Dank S&OP Planning können so Produktionsprozesse flexibel, automatisiert und kurzfristig umgeplant werden. Das ermöglicht Unternehmen, mit Hilfe von digitalen Tools einen umfassenden und flexiblen Prozessplan zu erstellen, der Eventualitäten abdeckt, ohne jedoch die Produktion zu vernachlässigen.
Von der Prozessplanung zur digitalisierten Prozessoptimierung
In der heutigen Geschäftswelt spielt die Optimierung von Prozessen eine entscheidende Rolle für den Erfolg eines Unternehmens. Durch die Integration digitaler Technologien und innovativer Lösungen gestalten Unternehmen ihre bestehenden Prozesse effizienter und sparen wertvolle Ressourcen. Digital Manufacturing und Prozessoptimierung Software ermöglicht eine umfassende Prozessoptimierung, bei der traditionelle manuelle Abläufe durch automatisierte, virtuelle Umgebungen ersetzt werden.
Erfolgreiche Prozessoptimierung im Unternehmen ermöglicht es, Produktionsprozesse zu analysieren, Schwachstellen zu identifizieren und zu optimieren. Ziele der Prozessoptimierung sind die Senkung der Kosten, das frühzeitige Erkennen von Fehlern, die Verbesserung der Qualität und das Verkürzen der Produktionszeit.
Die digitale Prozessoptimierung der Produktion ermöglicht es Unternehmen, schnellere Entscheidungen zu treffen, die Flexibilität zu erhöhen und den gesamten Produktlebenszyklus in einem fortlaufenden Prozess effektiv zu verwalten. Durch die nahtlose Integration von Prozessplanung, Produktentwicklung und Produktdesign erzielen Unternehmen Wettbewerbsvorteile und bringen innovative Produkte effizient auf den Markt.
Digitalisierung von Produktentwicklung und Produktdesign
Bei der Digitalisierung von Produktentwicklung und Produktdesign werden traditionelle analoge Prozesse und Methoden durch digitale Werkzeuge ersetzt oder ergänzt. Die Digitalisierung ermöglicht die Erstellung präziser 3D-Modelle, virtueller Prototypen und Simulationen. Diese sind die Basis für eine realitätsnahe Darstellung des Produkts und dessen Verhalten.
Durch den Einsatz von Computer Aided Design (CAD) und Computer Aided Engineering (CAE) werden Produkte detailliert entworfen, analysiert und optimiert. Die Digitalisierung von Produktentwicklung und Produktdesign erleichtert zudem die Integration von Daten und Informationen aus verschiedenen Quellen, wie beispielsweise Kundenfeedback, Markttrends und Produktionsdaten. Dies ermöglicht eine datengetriebene Entscheidungsfindung und eine schnellere Anpassung an sich ändernde Anforderungen und Kundenbedürfnisse.
Die digitale Transformation in der Produktion
Die digitale Transformation und damit die Digitalisierung in der Fertigung ist ein umfassender Wandel, den die Fertigungsindustrie durch den Einsatz digitaler Technologien und datenbasierter Prozesse erfährt. Es handelt sich um einen ganzheitlichen Ansatz, bei dem nicht nur einzelne Aspekte, sondern das gesamte Unternehmen in seiner Organisationsstruktur, seinen Prozessen und seiner Kultur transformiert wird.
Im Kontext der digitalen Transformation spielt die digitale Fertigung eine entscheidende Rolle. Dabei werden traditionelle Fertigungsprozesse durch den Einsatz von Technologien wie Robotik, Automatisierung, künstlicher Intelligenz und Internet of Things (IoT) digitalisiert und optimiert. Der Einsatz fortschrittlicher Analysen und Datenmanagement Lösungen ermöglicht eine engere Integration von Lieferanten, Kunden und Partnern entlang der Wertschöpfungskette.
Insgesamt zielt die digitale Transformation in der Fertigung darauf ab, die Produktivität, Flexibilität und Agilität von Unternehmen zu verbessern, Kosten zu senken, die Produktqualität zu steigern und den Kundenanforderungen gerecht zu werden.
Wichtige Begriffe rund um Digital Manufacturing
DFM
Bei der Produktentwicklung und dem mechanischen Design spielt Design for Manufacturing (DFM) eine entscheidende Rolle. Es steht für die Gestaltung von Produkten und Bauteilen unter Berücksichtigung einer vereinfachten und optimierten Fertigung und Montageprozesse.
Design for Manufacturing beginnt bereits in den frühen Phasen der Produktentwicklung, noch bevor Werkzeugbau oder Montage stattfinden. Die genauen Schritte im DFM-Prozess hängen von der Art des herzustellenden Produktes oder Bauteils ab.
Bei der Umsetzung von Design for Manufacturing stehen wir unseren Kunden als erfahrener Partner zur Seite, um die optimale Balance zwischen Design und Fertigbarkeit zu finden und so herausragende Ergebnisse in der Produktentwicklung zu erzielen.
Manufacturing Simulation
Manufacturing Simulation ist die virtuelle Nachbildung und Analyse von Produktionsprozessen mithilfe von Computersimulationen. Es ist eine Methode, bei der verschiedene Aspekte der Fertigung, wie Maschinen, Materialfluss, Arbeitsabläufe und Ressourcen, in einem digitalen Modell detailliert abgebildet werden.
Durch die Nutzung von Manufacturing Simulation Software und fortschrittlicher Simulationswerkzeuge können Hersteller verschiedene Szenarien, wie die Zusammenbaureihenfolge, Toleranzanalyse oder Cobotik simulieren. So werden die Auswirkungen von Veränderungen und Entscheidungen analysiert, bevor sie in der realen Produktion umgesetzt werden.
Durch den Einsatz von Simulationsmethoden werden virtuelle Umgebungen geschaffen, um den gesamten Fertigungsprozess digital zu optimieren. Durch die Prozessoptimierung werden Leistung, Zuverlässigkeit und Sicherheit von Werkstoffen und Produkten bewertet, ohne kostspielige und zeitaufwendige physische Prototypen herzustellen.
Digital Twin
Ein Digital Twin ist eine virtuelle Repräsentation eines realen Produkts, Systems oder Prozesses. Durch die Integration von Daten und Informationen in Echtzeit ermöglicht der Digital Twin eine genaue Darstellung und Analyse des Verhaltens und der Leistung des physischen Gegenstücks.
Der Digital Twin ermöglicht eine bessere Vorhersage von Problemen, die Optimierung von Betriebsabläufen und die Entwicklung Innovationen. Durch den Einsatz von fortschrittlicher Technologie wie IoT-Sensoren und Datenanalyse kann der Digital Twin einen wertvollen Beitrag zur digitalen Transformation und zum Erfolg im Bereich des Digital Manufacturing leisten.
Virtual Twin
Mit den Virtual Twin Experiences von Dassault Systèmes gehen wir über die rein digitale Darstellung von Objekten hinaus. Ein digitaler Zwilling ist lediglich eine virtuelle Repräsentation eines realen Objekts oder Systems. Unsere Virtual Twin Experiences hingegen erlauben es, diese Softwaremodelle zum Leben zu erwecken und in einer relevanten Umgebung zu kontextualisieren.
Durch die Verbindung von 3D-Modellen mit Simulationen bieten wir die Möglichkeit, virtuelle Zwillinge zu erstellen, die weit über die einfache Abbildung hinausgehen. Mit unseren Virtual Twin Experiences können Unternehmen ihre Produkte und Prozesse vollständig modellieren, testen, analysieren und optimieren.
Dadurch ermöglichen wir eine präzisere Produktentwicklung, eine effizientere Prozessoptimierung und ein fortschrittliches Produktdesign. Unsere ganzheitliche Herangehensweise an den Virtual Twin trägt dazu bei, die digitale Transformation im Bereich des Digital Manufacturing voranzutreiben und Unternehmen dabei zu unterstützen, ihre Innovationskraft zu stärken und Wettbewerbsvorteile zu erzielen. Zudem bietet der Virtual Twin die Möglichkeit, nach Fertigstellung und Auslieferung der Produkte, Reparaturen im Service nachzuvollziehen und Optimierungen am Produkt zu vereinheitlichen, um die nächste Generation zu perfektionieren.
CAM
Computer-Aided Manufacturing beschreibt die Nutzung von computergestützten Systemen und Softwaretools zur Steuerung und Automatisierung von Fertigungsprozessen. CAM-Software ermöglicht es, den gesamten Fertigungsprozess digital zu planen, zu simulieren und zu optimieren.
Computer-Aided Manufacturing beschreibt die Einzelteilfertigung mit (Computer) numerischer Steuerung von Fertigungsmaschinen für Drehen, Fräsen und Schleifen. CAM-Software ermöglicht es, Produkte in der Herstellung zu planen und dank Werkzeugproduktion umzusetzen.
Dank einer direkten Umwandlung von digitalen Modellen und Konstruktionsdaten in Produktionsanweisungen ist ein nahtloser Übergang vom Design in die Fertigung möglich. Darüber hinaus ermöglicht die Software eine automatische Generierung von Werkzeugwegen, eine Optimierung des Materialverbrauchs, eine Simulation von Bearbeitungsprozessen sowie eine Überprüfung auf Kollisionen oder Fehlern, noch bevor der eigentliche Produktionsprozess beginnt.
Robotik
Durch den Einsatz von Robotern in der Produktion steigern Unternehmen ihre Effizienz, erhöhen die Produktionsgeschwindigkeit und verbessern die Genauigkeit. Robotik ermöglicht es auch, gefährliche oder monotone Aufgaben zu automatisieren, was die Sicherheit am Arbeitsplatz erhöht. In der digitalen Fertigungsumgebung werden Roboter durch präzise 3D-Modelle und Simulationen gesteuert. Diese Modelle machen es möglich, die Bewegungen und Aktivitäten der Roboter im Voraus zu planen und zu optimieren, um einen reibungslosen Ablauf des Produktionsprozesses zu gewährleisten. Darüber hinaus bieten Roboter in der digitalen Fertigungsumgebung die Möglichkeit des sogenannten "Collaborative Robotics" oder "Cobotics". Hier arbeiten Roboter und menschliche Arbeitskräfte Hand in Hand, um komplexe Aufgaben zu erledigen.
Prozessplanung
Durch die Anwendung von digitalen Technologien können detaillierte virtuelle Modelle von Produktionsprozessen erstellt und simuliert werden, um deren Abläufe zu optimieren und Effizienzsteigerungen zu erzielen. Dabei werden auch die einzelnen Schritte des Zusammenbaus berücksichtigt, um eine nahtlose und effiziente Produktion zu gewährleisten.
Ein wichtiger Aspekt der Prozessplanung im digital Manufacturing ist die Unterscheidung zwischen Engineering Bill of Materials (EBOM) und Manufacturing Bill of Materials (MBOM). Das eBOM beschreibt die Struktur des Produkts auf der Konstruktions- und Engineering-Ebene, während das mBOM die Struktur auf der Fertigungsebene abbildet. Durch die Integration digitaler Technologien werden diese beiden Bill of Materials miteinander verknüpft, um einen reibungslosen Informationsfluss zwischen den Konstruktions- und Fertigungsteams zu ermöglichen. So können Produkte auch an verschiedenen Standorten hergestellt werden, ohne dabei an Qualität und Kompatibilität zu verlieren. In der Prozessplanung kann jedes Einzelteil individuell zusammengesetzt werden, unter Berücksichtigung der jeweiligen Bedingungen.
Digitale Transformation
Die Digitale Transformation behandelt den umfassenden Wandel von traditionellen, manuellen und isolierten Fertigungsprozessen hin zu hochautomatisierten, vernetzten und datengetriebenen Produktionsumgebungen.
Diese ermöglichen eine Prozessoptimierung und Produktentwicklung durch die Integration digitaler Technologien wie Internet of Things (IoT), künstliche Intelligenz (KI), maschinelles Lernen, Big Data-Analyse und Cloud Computing.
Die Digitale Transformation in der Fertigung umfasst die Einzelteilfertigung mit numerischer Steuerung sowie den Einsatz von Robotik in einer ganzheitlichen Prozessplanung. Die Digitale Transformation ermöglicht außerdem eine nahtlose Integration von Prozessen und Daten entlang der gesamten Wertschöpfungskette, ohne dabei an Qualität und Kompatibilität zu verlieren. Das führt zu einer effizienten Kommunikation, verbesserten Lieferkettenmanagement und individuellen Kundenlösungen.
Model Based Enterprises
Statt sich auf traditionelle zweidimensionale Zeichnungen und separate Dokumente zu verlassen, werden bei Model Based Enterprises alle Informationen in einem digitalen 3D-Modell gespeichert, das alle relevanten Daten, wie Geometrie, Materialien, Toleranzen, Fertigungsprozesse und andere relevante Informationen enthält. Dies ermöglicht eine nahtlose Kommunikation und Zusammenarbeit zwischen den verschiedenen Abteilungen eines Unternehmens, einschließlich Konstruktion, Fertigung, Qualitätssicherung und Instandhaltung. MBE fördert die Effizienz, reduziert Fehler und Missverständnisse und beschleunigt den Produktentwicklungsprozess, was zu kostengünstigeren und qualitativ hochwertigeren Produkten führt. Es spielt eine entscheidende Rolle im Rahmen des Digital Manufacturing und der intelligenten Fertigung, da es den Übergang von der Konzeption über die Fertigung bis hin zur Wartung und Entsorgung eines Produkts nahtlos unterstützt.
Die 3DEXPERIENCE Plattform als ganzheitliche Lösung für Digital Manufacturing
Die 3DEXPERIENCE Plattform bietet Unternehmen eine umfassende Lösung, um ihre Produktentwicklung zu optimieren, ihre Fertigungsprozesse zu digitalisieren und die Zusammenarbeit zu verbessern. Die Softwareplattform unterstützt Unternehmen dabei, effizienter zu arbeiten, innovative Produkte schneller auf den Markt zu bringen und eine führende Rolle in einer digitalen und vernetzten Welt einzunehmen. Die Plattform bietet eine umfassende Auswahl an Werkzeugen, um den gesamten Produktlebenszyklus abzudecken und innovative, hochwertige Produkte zu entwickeln.
- Integrierte Produktentwicklung
- Digitale Fertigung und Prozessoptimierung
- Kollaboration und globale Zusammenarbeit
Die 3DEXPERIENCE Plattform ermöglicht Unternehmen eine ganzheitliche und integrierte Produktentwicklung. Durch die nahtlose Integration von CAD-Modellierung, Simulation, Materialauswahl und Produktionsdetails können Unternehmen den gesamten Produktentwicklungsprozess optimieren. Teams können effektiv zusammenarbeiten, Designänderungen in Echtzeit verfolgen und gleichzeitig sowohl die Produktqualität verbessern als auch die Markteinführungszeit verkürzen.
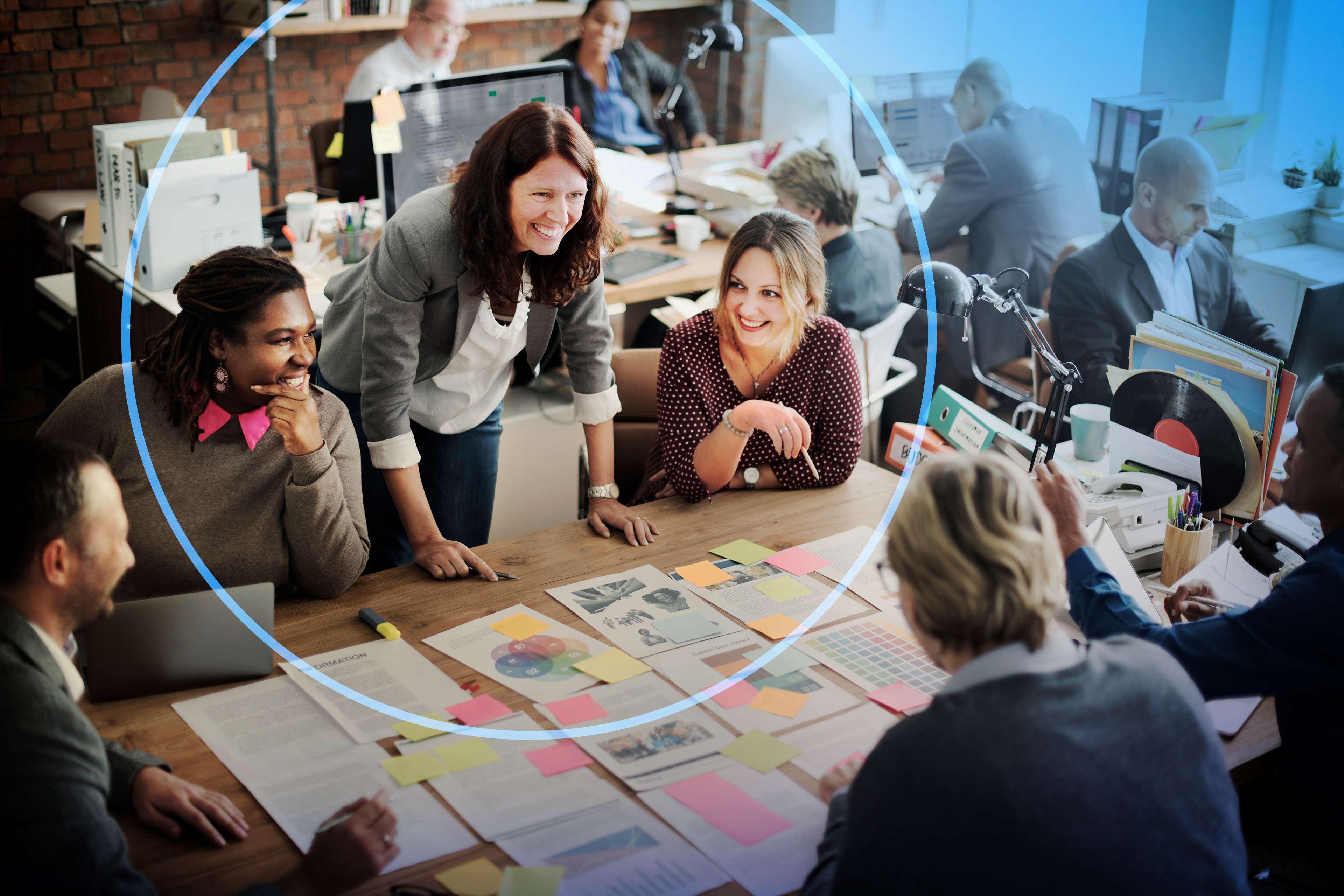
Die 3DEXPERIENCE Plattform unterstützt Unternehmen bei der Digitalisierung ihrer Fertigungsprozesse. Durch die Integration von Fertigungstechnologien können Unternehmen die Effizienz steigern, Materialverschwendung reduzieren und die Produktqualität verbessern. Die Plattform bietet fortschrittliche Werkzeuge zur virtuellen Simulation und Optimierung von Fertigungsprozessen, um Engpässe zu identifizieren, Durchlaufzeiten zu verkürzen und die Gesamtproduktivität zu steigern.
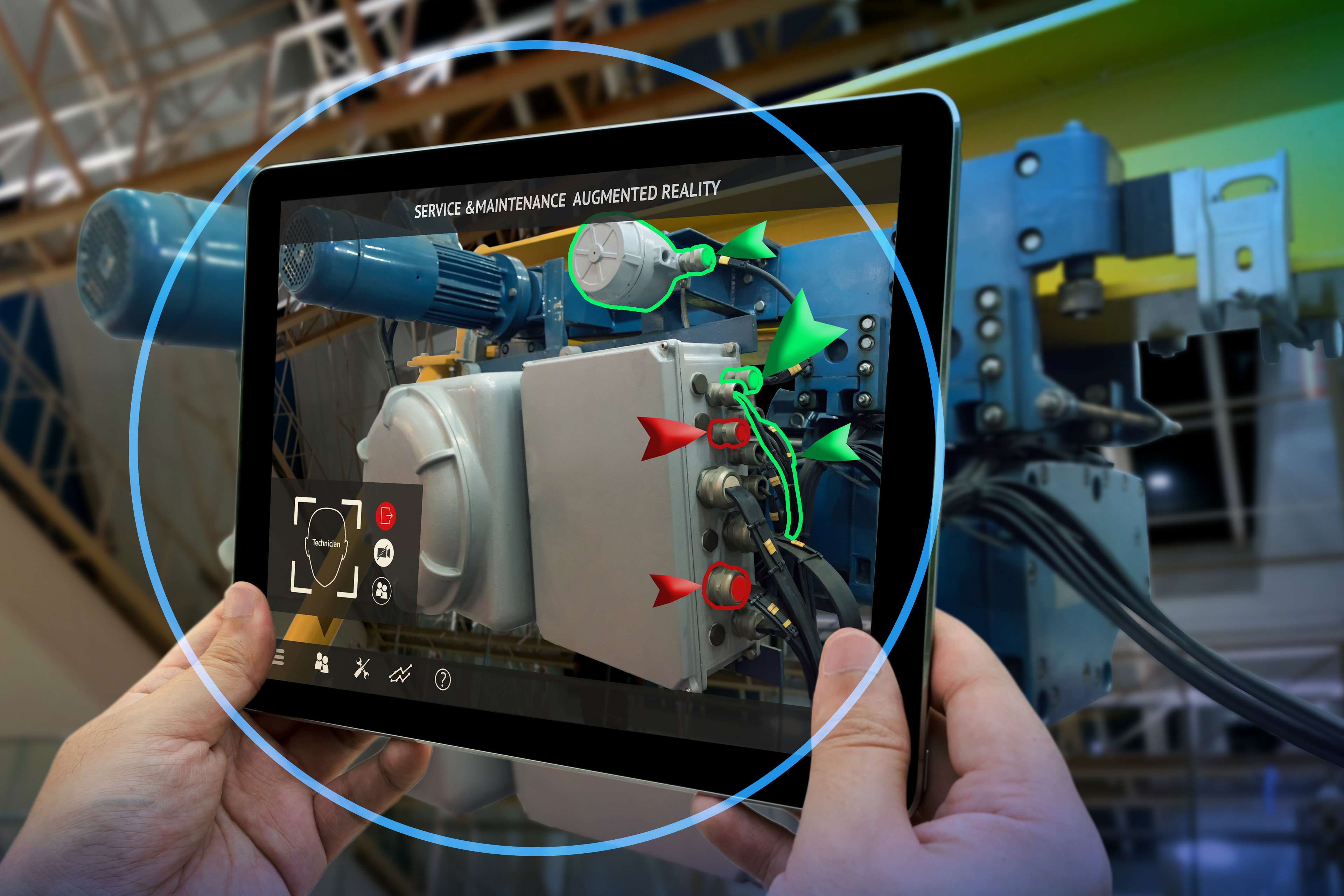
Die 3DEXPERIENCE Plattform fördert die Zusammenarbeit und den Wissensaustausch zwischen verschiedenen Teams, Abteilungen und Standorten. Projektbeteiligte können in Echtzeit auf gemeinsame Daten zugreifen, Designs überprüfen, Aufgaben verfolgen und Feedback austauschen. Die Plattform bietet eine zentrale Datenquelle, die einheitliche und konsistente Informationen gewährleistet. Durch die globale Zusammenarbeit können Unternehmen ihre Innovationen beschleunigen, effektiver auf Kundenanforderungen eingehen und ihre Wettbewerbsfähigkeit stärken.
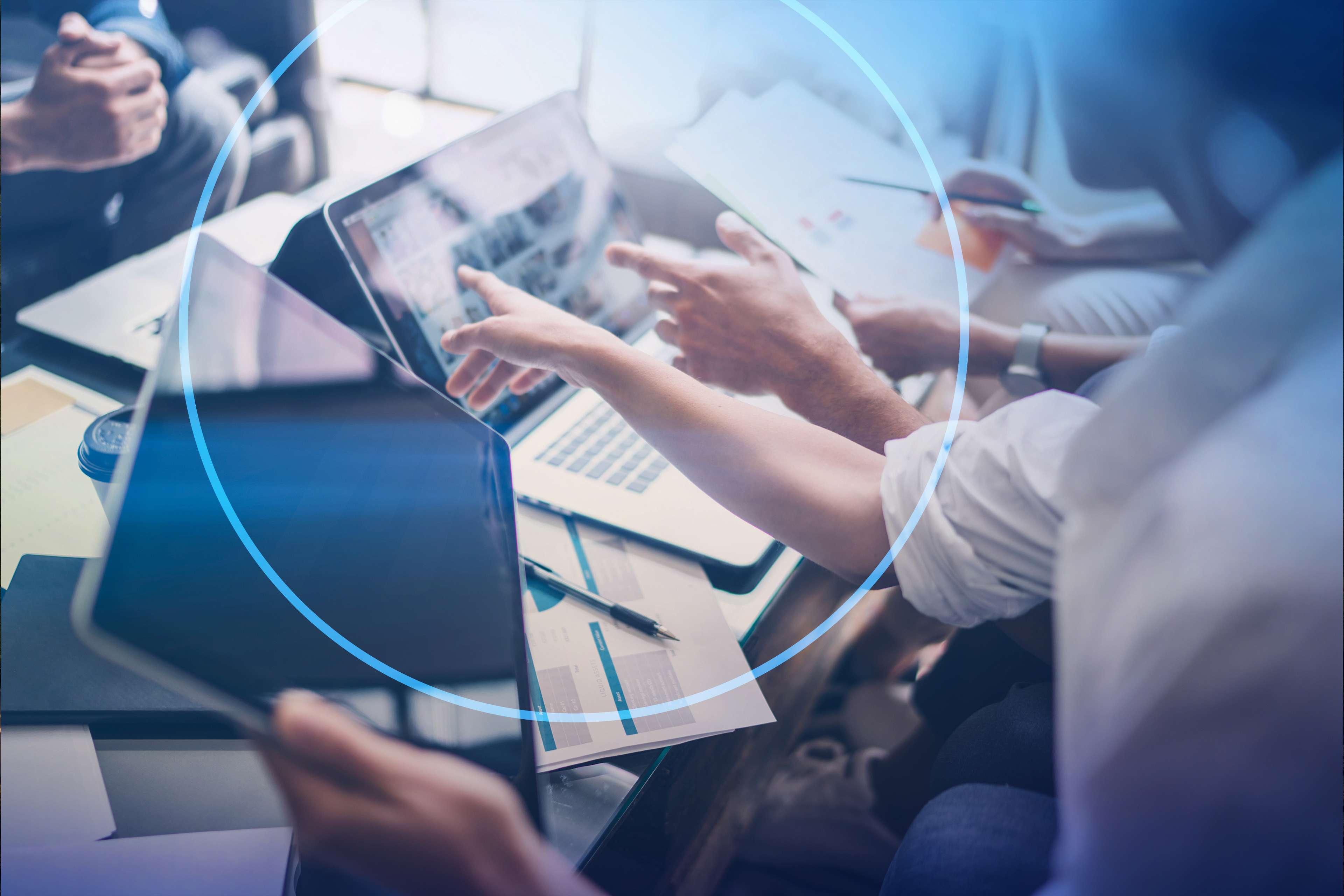
Digital Manufacturing und die 3DEXPERIENCE Plattform: Cloud oder on Premise?
In der heutigen digitalen Welt suchen Unternehmen nach effizienten Lösungen, um ihre Prozesse zu optimieren, die Produktentwicklung zu beschleunigen und innovatives Produktdesign zu ermöglichen. Die 3DEXPERIENCE Plattform von Dassault Systèmes bietet hierfür eine leistungsstarke Lösung.
Zunächst stehen zwei Grundsätze zur Debatte: Cloud oder on Premise. Cloud-basierte Lösungen bieten Flexibilität, Skalierbarkeit und schnelle Bereitstellung über das Internet, während On-Premise-Modelle mehr Kontrolle und Sicherheit bieten, jedoch höhere Investitionen erfordern. Cloud-Lösungen eignen sich gut für Unternehmen, die eine agile, flexible und kosteneffiziente IT-Infrastruktur benötigen, während On-Premise-Modelle für Unternehmen geeignet sind, die eine umfassende Kontrolle über ihre Daten und IT-Systeme wünschen und bereit sind, in die entsprechende Hardware und Wartung zu investieren.
Die Cloud-basierte 3DEXPERIENCE Plattform ermöglicht Unternehmen eine flexible und skalierbare Nutzung. Dadurch entfallen hohe Anfangsinvestitionen und die Belastung für die interne IT-Abteilung wird reduziert. Außerdem kann die Plattform schnell und einfach bereitgestellt, aktualisiert und erweitert werden. Ein weiterer wichtiger Punkt ist die Verfügbarkeit von Daten. Durch eine on Premise Lösung können Updates nicht regelmäßig eingespielt werden, was zu Sicherheitslücken und Anfälligkeiten führen kann. Bei einer Cloud basierten Lösung, werden tagesaktuell Updates durchgeführt, was Schäden, Verzögerungen und Abweichungen vorbeugt.
Mit ihren Vorteilen in Bezug auf Flexibilität, Zusammenarbeit, Skalierbarkeit und Sicherheit ermöglicht die 3DEXPERIENCE Plattform in der Cloud eine effektive Prozessoptimierung, beschleunigte Produktentwicklung und innovatives Produktdesign. Indem Unternehmen auf die Cloud setzen, können sie sich auf ihr Kerngeschäft konzentrieren und von den Vorteilen einer modernen und agilen Plattform profitieren.
Cloud-Lösungen verfügen über redundante Datenzentren und Notfallwiederherstellungsoptionen, um den Schutz von Unternehmensdaten zu gewährleisten. Ausreichende Sicherheitsmaßnahmen sind unerlässlich, um den SChutz sensibler Unternehmensdaten und -prozesse zu gewährleisten und die Vorteile des Digital Manufacturing voll auszuschöpfen.
Die 3DEXPERIENCE Plattform im Einsatz bei unseren Kunden
- CLAAS - Intelligente Landwirtschaftliche Maschinen
- V-ZUG - Innovative Haushaltsgeräte
- Vesper - Spezialwerkzeuge für die Automobilindustrie
CLAAS hat überall auf der Welt Entwicklungsstandorte, die über globale Grenzen hinweg zusammenarbeiten müssen. Zudem erzeugt die enorme Produktvielfalt des Unternehmens große Mengen komplexer Daten, die entsprechend verwaltet werden müssen. Um die globale Zusammenarbeit zu erleichtern und die steigende Datenkomplexität zu bewältigen, setzt CLAAS auf die 3DEXPERIENCE® Plattform von Dassault Systèmes.
Mit der 3DEXPERIENCE Plattform haben wir die Basis geschaffen für die Zukunft. Die Plattform gibt uns die Möglichkeit, die Anforderungen an ein Produkt vom Start der Entwicklung bis zur Serienreife abzubilden und die entsprechenden Spezifikationen und Modelle zu erarbeiten und zu managen. - Ernst Dober, Head of Development and Services bei V-ZUG
Dank der 3DEXPERIENCE Plattform werden alle vorhandenen Konstruktionsdaten direkt integriert. Wir haben jetzt sofortigen Zugriff auf aktuelle Informationen und optimierte Prozesse in unserer gesamten Organisation. Die zentrale Erfassung aller Daten und Prozesse ermöglicht es uns, unser Unternehmen zukunftssicher zu machen und unseren Kunden das hohe Niveau zu bieten, das sie von uns erwarten. - Jochen Kelzenberg, Konstruktionsleiter bei Vesper