ROBOT AT WORK
Mit Virtual Twin Experience auf der cloudbasierten 3DEXPERIENCE Plattform konnte Robot at Work den Aufbau seiner Produktionslinien optimieren und Produktionskapazitäten exakt vorausberechnen.
Roboter in einer virtuellen Umgebung optimieren
Stellen Sie sich vor, Sie könnten Ihre Produktionslinie so einrichten, dass sie mit weniger Ressourcen auskommt, aber weiterhin maximalen Output liefert. Und stellen Sie sich ebenfalls vor, Sie könnten alles in einer virtuellen Fabrik testen, unendlich viele Szenarien durchspielen, um einen Entwurf zu prüfen, bevor Sie ihn bauen oder die physische Produktionslinie bzw. Zelle neu konfigurieren. Genau das ermöglicht Robot at Work seinen Industriekunden, seit das Unternehmen für Robotik die Virtual Twin Experience Technologie nutzt.
Die seit 2017 auf Lösungen für Produktionslinien spezialisierte italienische Firma hatte ursprünglich mit dem Verkauf und der Integration von Cobots begonnen – Roboterarmen, die neben Menschen in der Produktion zur Platinenbestückung, Metallverarbeitung, Verpackung sowie für Be- und Entladevorgänge eingesetzt werden. Schon bald wurde Robot at Work von Kunden nach komplexeren Produktionslösungen für Standardroboter gefragt. Da die großen Player in der Automobilindustrie gerade auf virtuelle Inbetriebnahmetechnologien umstiegen, beschloss Robot at Work, das auch zu tun.
„Wir haben in den letzten Jahren gesehen, dass die führenden Automobilhersteller in den Schweißanlagen, etc. auf virtuelle Inbetriebnahme umgestellt haben“, sagt Alessandro Tecchia, kaufmännischer Leiter bei Robot at Work. „Wir wussten, dass wir alle Automatisierungsanforderungen unserer Kunden erfüllen könnten, wenn wir die Fähigkeiten von Robotern testen, ihre Funktionalität bewerten und Probleme sowie Verbesserungsmöglichkeiten auf der Grundlage virtueller Modelle identifizieren könnten. Unserer Auffassung nach wird der Markt alle Anlagenbauer früher oder später in diese Richtung drängen.“
Für sein neues virtuelles Inbetriebnahmekonzept nutzt Robot at Work DELMIA auf der 3DEXPERIENCE Plattform. Vorher hatte das Unternehmen die Bedarfsermittlung, das Produktionsdesign und die Validierung der Roboterlösung für Kunden im 2D-Layout durchgeführt. Erst wenn die gesamte Zelle gebaut war, war es möglich, die Lösung zu testen und Schwachstellen zu erkennen.
„Wir wussten, da gibt es eine bessere Möglichkeit“, so Tecchia. „Wir prüften, wie man diese Probleme mit Hilfe einer virtuellen Umgebung lösen könnte und fanden heraus, dass die 3DEXPERIENCE Plattform mit der DELMIA-Anwendung alle Funktionen bietet, die wir brauchen. Jetzt können wir die Lösungen für unsere Kunden viel schneller entwickeln, weil wir die gesamte Roboterzelle komplett gestalten können, noch bevor sie gebaut wird.“
Durch die virtuelle Inbetriebnahme kann Robot at Work die zunehmend komplexeren Anforderungen seiner Kunden heute viel einfacher erfüllen und sie beim effizienteren Betrieb ihrer Produktionsanlagen unterstützten.
„Wir hatten gerade erst die Gelegenheit, eine Fabrik mit mehr als zwölf Zellen zu simulieren“, berichtet Tecchia. „Der Kunde wollte die Logistik auf fahrerlose Transportfahrzeuge umstellen und wir konnten ihm zeigen, dass er nur drei Viertel der ursprünglich geplanten Hallenfläche dafür braucht. Jetzt kann er seine Teile bei weniger Raumbedarf herstellen und deutlich effizienter arbeiten.“
Das Unternehmen konnte auch neue Kunden gewinnen.
„Da wir unseren kompletten Angebotsprozess verändert haben, heben wir uns jetzt von anderen Standard-Anlagenbauern auf dem Markt ab“, sagt Lorenzo Codini, Sachbearbeiter bei Robot at Work. „Unsere Kunden können vorab eine komplette Simulation ihrer Produktionslinie sehen, bevor sie sich verbindlich für die Investition und den tatsächlichen Bau der Anlage entscheiden. In Italien gibt es nicht viele Unternehmen, die so arbeiten. Das hat unseren Umgang mit neuen Projekten völlig verändert.“
Unsere Kunden können vorab eine komplette Simulation ihrer Produktionslinie sehen und wissen genau, ob sich ihre Investition lohnen wird. Das hat uns unseren Kunden sehr viel näher gebracht.
Komplettlösung in der Cloud
Das Team von Robot at Work prüfte mehrere virtuelle Inbetriebnahmelösungen, bevor es sich für die 3DEXPERIENCE Plattform und DELMIA entschied.
„Wir waren auf der Suche nach einer Software, die alle unsere Ansprüche an die virtuelle Inbetriebnahme erfüllt”, so Codini. „Wir hatten in unserem Planungsbüro bereits die SOLIDWORKS-Software von Dassault Systèmes genutzt, und als unser IT-Partner Nuovamacut uns DELMIA und die Plattform vorschlug, erschien uns das als die perfekte Lösung.“
Robot at Work war beeindruckt von den ausgefeilten Roboterfunktionen von DELMIA, mit denen Roboter für eine spezifische Produktionslinie programmiert und das Verhalten aller Roboter detailliert simuliert werden können. Zudem wollte das Unternehmen gerne eine cloudbasierte Lösung nutzen.
„Dass es die Lösung als cloudbasierte Version gibt, war für uns ein Pluspunkt“, so Tecchia. „Wir sind keine große Firma, wir haben also keine riesige IT-Infrastruktur. Für uns war die Cloud daher ein echter Vorteil. So konnten wir die Lösung implementieren, ohne vorher groß investieren zu müssen. Was uns ebenfalls gefallen hat war, dass die Updates automatisch laufen, wir also immer mit der neuesten Softwareversion arbeiten würden. Wenn wir einen Kunden besuchen, nehmen wir einfach einen Laptop mit und können von überall einfach auf die 3DEXPERIENCE Plattform zugreifen. Wir müssen keine externen Festplatten mehr mit uns herumschleppen.“
Mit Unterstützung durch das Nuovamacut-Team war DELMIA in wenigen Monaten bei Robot at Work betriebsbereit.
„Durch die enge Zusammenarbeit mit dem Nuovamacut-Team konnten wir das Rollout erfolgreich durchführen,” sagt Codini. „Es ging wirklich schnell, und der Support war großartig. Nuovamacut entwickelte eine Schulung, um uns auf den Stand der Dinge zu bringen, sodass wir DELMIA selbstständig nutzen können. Wir wissen, dass wir uns immer auf ihre Unterstützung verlassen können. Wenn wir neue Anfragen von Kunden für Simulationen erhalten, die vom Standard abweichen, wissen wir, dass sie die Expertise haben, uns dabei zu helfen.“
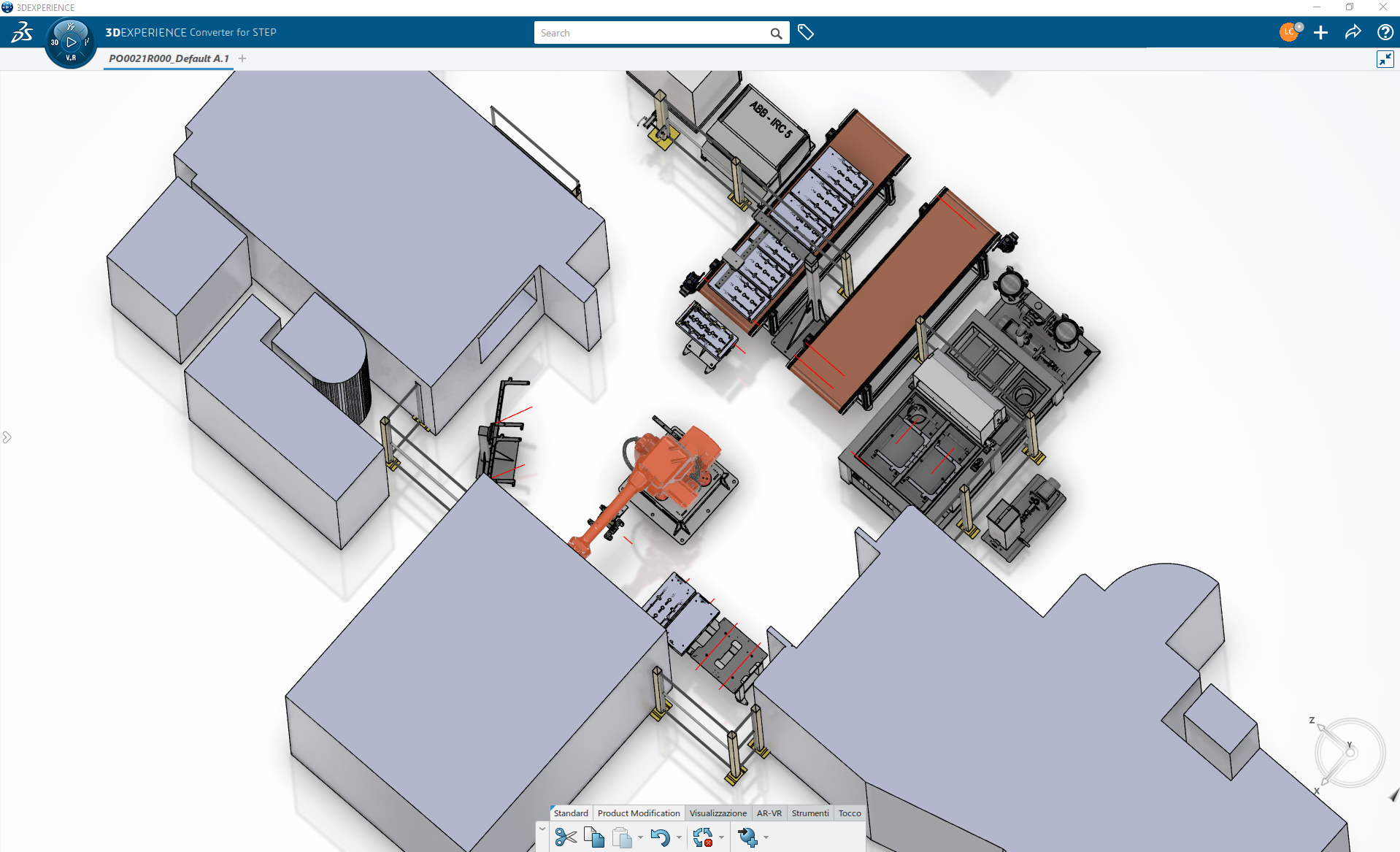
Komplexität dank Simulation beherrschen
Seit Einführung der Lösung ist die Kundennachfrage bei Robot at Work stetig gestiegen, weil die Fertigungsunternehmen selbst immer mehr unter Druck stehen, flexibler zu werden, Produkte preisgünstiger zu produzieren, schneller auf den Markt zu bringen und höchste Qualitätsstandards einzuhalten.
„Es wurde immer schwieriger für uns, all diesen Anforderungen gerecht zu werden“, so Tecchia. „Kunden kamen mit sehr spezifischen Anfragen auf uns zu, für die es aber nicht immer eine offenkundige Lösung gab. Und sie wollten sehen, wie die Roboterzelle in den Gesamtbetrieb eingebettet funktionieren würde. Mit Simulationen können wir solche Fragen klären. Wir haben die virtuelle Inbetriebnahme bereits für viele unserer Kunden aus der Automobilbranche genutzt und konnten damit ihre Anforderungen an die Produktionslinie besser umsetzen.“
Ein Bereich, in dem das einen großen Unterschied gemacht hat, ist die Art und Weise, in der Robot at Work jetzt Roboterapplikationen und SPS, also den Maschinencode, der die Produktionsprozesse steuert, programmiert.
„Wir entwickeln für unsere Automobilkunden viele Roboter und SPS”, fügt Codini hinzu. „Jetzt können wir die automatisierte Lösung in Simulationen bewerten und noch vor dem Anlagenbau genau demonstrieren, wie die Roboter und SPS-Prozesse die Bewegung der Fabrikwerkzeuge und Maschinen steuern werden. Das war vorher nicht möglich.“
Wir verkaufen jetzt komplette Logistiklösungen auf DELMIA und allein im letzten Jahr konnten wir den Umsatz unseres Robotik-Bereichs verdoppeln.
Die richtigen Roboter wählen
Weil jede einzelne Produktionslinie höchst detailliert definiert werden kann, kann Robot at Work ermitteln, welche Roboter für welche Aufgaben am besten geeignet sind und mehrere Funktionen in einer Zelle kombinieren. Gleichzeitig sparen die Kunden des Unternehmens Kosten und Zeit, vermeiden aber auch Fehler, die entstehen, wenn eine neue Linie nach klassischer Vorgehensweise installiert und anschließend in der Produktion fehlerbereinigt und optimiert wird.
„Mit DELMIA können wir das Verhalten aller Roboter detailliert simulieren“, so Codini. „Der Vorteil ist, dass wir in nur einem Programm alle führenden Robotermarken verwenden, sie programmieren, versetzen, mechanische Teile ändern und dann ganze Roboter tauschen können. So können wir mühelos verschiedenste Robotermarken integrieren und vergleichen, um herauszufinden, welche für die Anforderungen unseres Kunden am besten geeignet sind. Wir sehen ganz genau, wie sie in die Umgebung des Kunden passen. Und wir können mit DELMIA auch vorhandene Roboter testen, die wir umbauen wollen.“
Mit dieser Herangehensweise ist Robot at Work in der Lage, für alle Kundenanforderungen die optimale Lösung zu finden und den Kunden dabei zu helfen, Kosten zu sparen.
„Da war zum Beispiel ein Automobilkunde“, berichtet Tecchia. „Er hatte eine Montagestraße mit einem Vision-Control-System zur Qualitätskontrolle. Früher brauchte er fünf Kameras, um die Straße zu überwachen. Wir haben virtuell eine neue Roboteranordnung entwickelt, mit der das gleiche Bauteil genauso gut mit nur einer Kamera überwacht werden kann. In unserer Simulation konnten wir den Roboter bei der Bauteilmontage zeigen, und wie die einzige Kamera den gesamten Prozess überwacht, ohne dass Qualitätseinbußen entstehen. Der Kunde hat diese Anordnung für andere Produktionslinien übernommen und konnte dadurch eine Menge Geld sparen.“
Output maximieren
Eine der häufigsten Anfragen der Kunden von Robot at Work ist die Maximierung des Outputs.
„Der Output ist die erste Information, die der Kunde sehen will“, so Tecchia. „Früher konnten wir die Zykluszeiten auf Basis unserer Berechnungen und Erfahrung nur schätzen. Teilweise hat das beim finalen Output zu Fehlern geführt, weil wir nicht jedes Szenario durchspielen konnten. Dank Simulationen sind wir jetzt viel genauer. Wir können dem Kunden die Arbeitsleistung der Roboter in der virtuellen Umgebung zeigen und diese Ergebnisse sind sehr nah an der Realität der tatsächlichen Produktion. Es gibt keine Überraschungen mehr.“
Die Virtual Twin Experience kann auch Systeme simulieren, die bereits in Betrieb sind. So können Robot at Work und seine Produktionskunden das System überwachen, Modelle für Anpassungen entwickeln und automatisch Änderungen am System durchführen, um einen maximal effizienten Betrieb sicherzustellen.
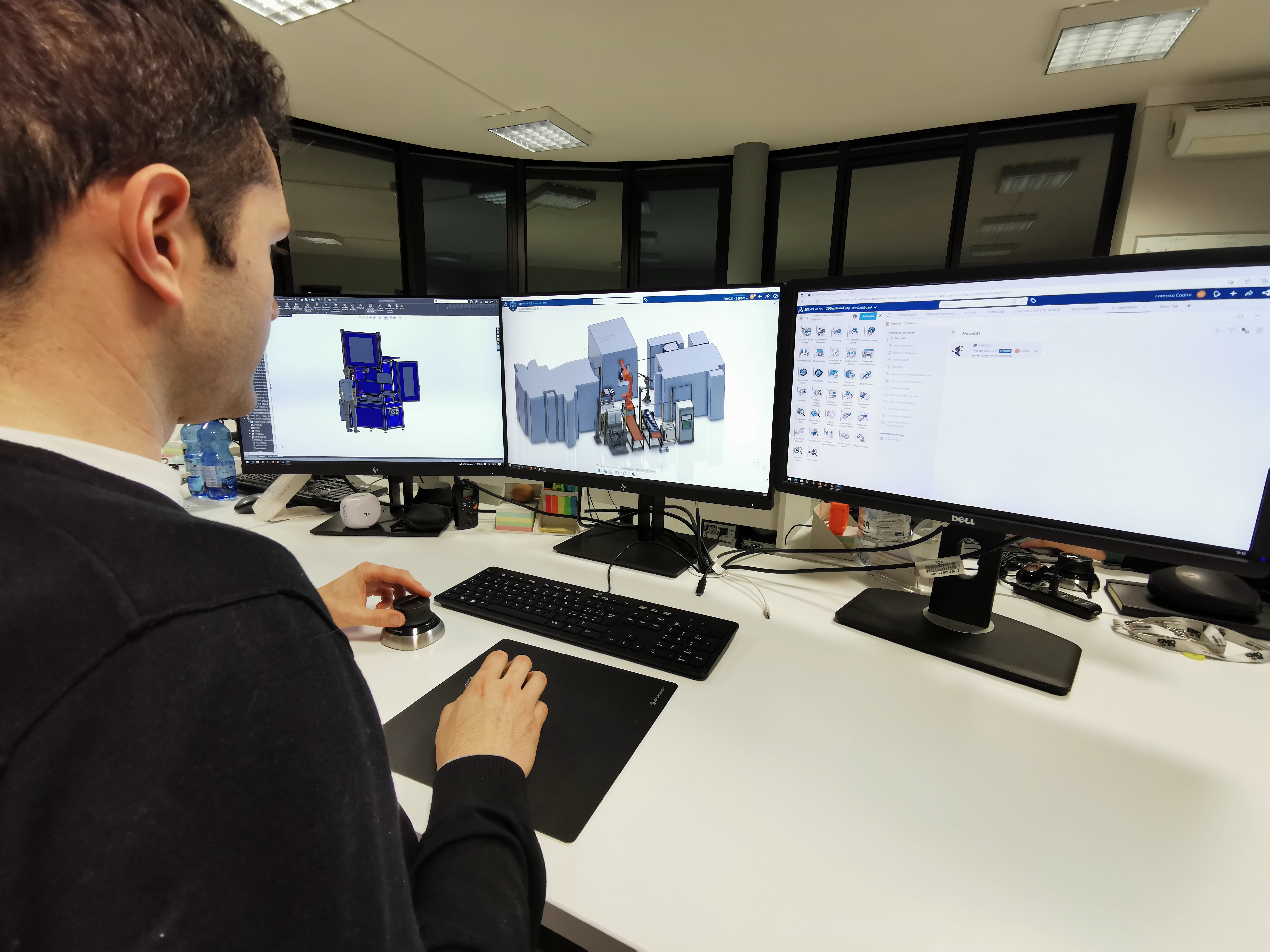
Ein neues Service-Geschäftsmodell
Für Robot at Work war der Übergang zur virtuellen Inbetriebnahme eine echte Transformation, sowohl im Hinblick darauf, wie das Unternehmen die gestellten Anforderungen seiner Kunden erfüllt als auch darauf, wie es die Kunden weiter betreut, wenn die Produktionslösung installiert und in Betrieb ist.
„Was sich mit am meisten verändert hat, ist unser After-Sales-Geschäft“, so Codini. „Viele unserer Kunden stellen die Produktion zwei bis drei Mal im Monat um und brauchen unsere Hilfe, um die Programme umzuschreiben. Durch die Plattform und DELMIA können wir eine neue Zelle viel schneller betriebsbereit machen. Wenn ein Kunde die Produktion oder einen Roboterzyklus ändern will, können wir dies im Vorhinein simulieren, ihm zeigen, wie es funktioniert und den Wechsel dann bei minimaler Ausfallzeit vollziehen. Wir können einen neuen Produktionszyklus innerhalb eines Tages zum Laufen bekommen.“
Seit Robot at Work die 3DEXPERIENCE Plattform nutzt, floriert das Geschäft.
„Wir verkaufen inzwischen komplette Logistiklösungen mit DELMIA und konnten den Umsatz unserer Robotersparte alleine im letzten Jahr verdoppeln“, sagt Tecchia. „In Zukunft erwarten wir sogar ein noch größeres Wachstum und die Plattform treibt das wirklich voran.“
„Sie hat uns eine völlig neue Arbeitsweise ermöglicht“, fügt Codini hinzu. „Unsere Kunden verlassen sich auf uns und unser Know-how. Sie können jetzt sehen, dass wir die beste Lösung liefern, noch bevor sie den Anlagenbau in Auftrag geben. Sie wissen genau, wie sich ihre Investition rentieren wird. Das hat uns unseren Kunden sehr viel näher gebracht.“
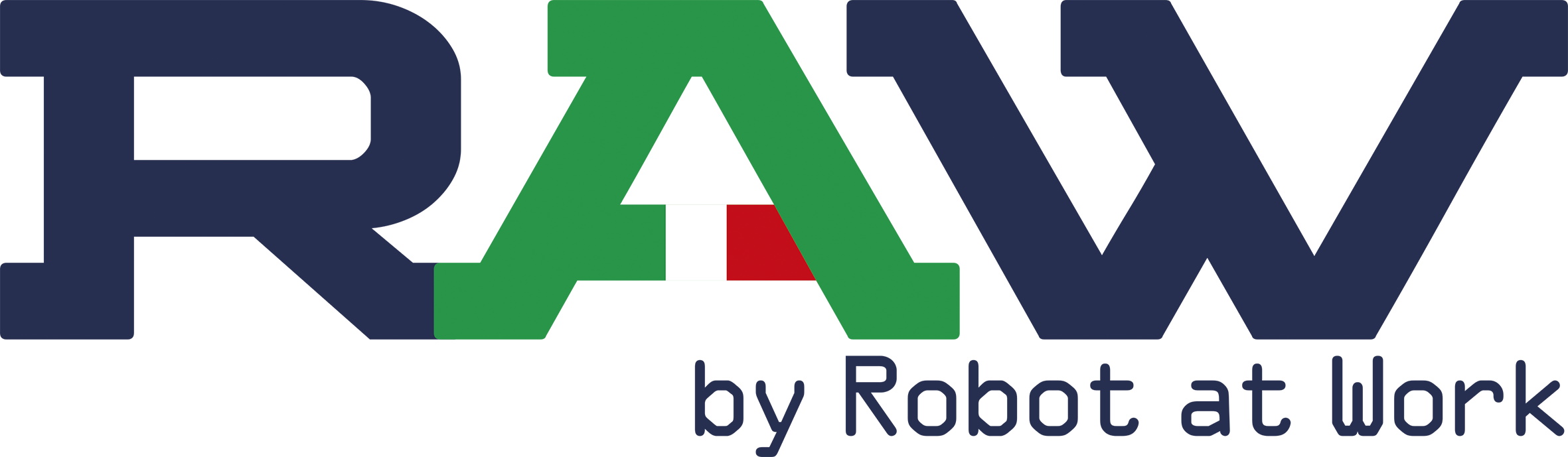
Über Robot at Work
Robot at Work wurde als innovatives Start-up in Rovato gegründet und begann mit dem Vertrieb von kollaborativen Robotern (Cobots). Ziel des Unternehmens war, Anlagenbauer, Endverbraucher, Forschungs- und Entwicklungszentren sowie Ausbildungsinstitute mit den innovativen Cobots auszustatten.
Das Unternehmen hat sich weiterentwickelt, indem es klassische Industrieroboter mit in sein Portfolio aufgenommen hat und ist derzeit dabei, die Kompetenzen und Ressourcen aufzubauen, um Virtual Twins und virtuelle Inbetriebnahmen zu seinen wichtigsten internen Designwerkzeugen zu machen.
Weitere Informationen finden Sie hier: www.robotatwork.it
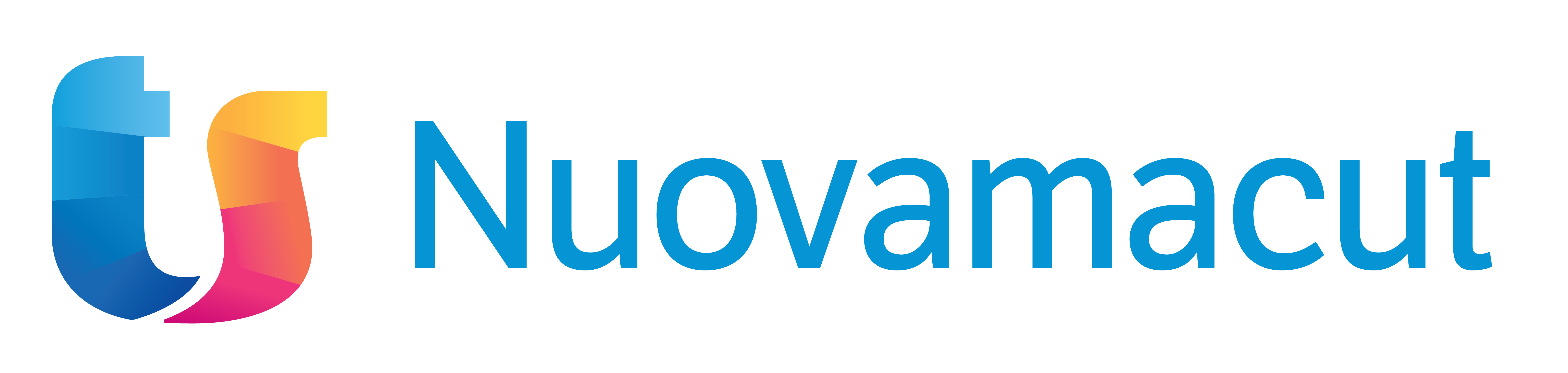
Über Nuovamacut
Nuovamacut ist ein italienisches Unternehmen und Partner von Dassault Systèmes mit einer hohen Fachkompetenz in den Bereichen CAD, CAM, CAE und PLM. Das Unternehmen ist in ganz Italien tätig und unterstützt Kunden jeglicher Größe und Komplexität aus ganz verschiedenen Bereichen wie mechanischer Industrie, Design, Werkzeugbau, Konsumgüter oder technische Anlagen, aber auch Luftfahrt, Transport sowie Planungs- und Konstruktionsbüros.