CNC-Fräsen Schlichten und Designrichtlinien
Planen Sie Ihr nächstes Projekt zur Teilefertigung? Stellen Sie sicher, dass Sie die Richtlinien für die CNC-Fräsbearbeitung und das Design kennen, die berücksichtigt werden sollten.
Einführung in die CNC-Fräsbearbeitung und Designrichtlinien
CNC-Fräsen ist ein Bearbeitungsprozess, bei dem Material vom Rohmaterial abgetragen wird, um das endgültige Design zu realisieren. Beim CNC-Fräsen werden runde Fräser verwendet, die das Material seitlich abtragen. Beim 3-Achsen-CNC-Fräsen wird das Werkstück fixiert, während sich das Werkzeug dreht und beim Abtragen von Material auf und ab bewegt. Außerdem bewegt sich das Bett der 3-Achsen-CNC-Fräsmaschine von hinten nach vorne und von Seite zu Seite.
Da es sich beim CNC-Fräsen um eine Form der subtraktiven Fertigung handelt, sind die Werkzeugspuren auf Ihrem Teil zu sehen, wenn es die Maschine verlässt. Die gute Nachricht ist, dass verschiedene Nachbearbeitungsmethoden eingesetzt werden können, um die Glätte, Verschleißfestigkeit, Korrosionsbeständigkeit und Ästhetik von CNC-gefrästen Teilen zu verbessern.
In diesem Artikel werfen wir einen genaueren Blick auf einige wichtige Designrichtlinien für das CNC-Fräsen sowie auf die gängigsten Optionen für die Endbearbeitung von CNC-Frästeilen, die Sie bei der Planung Ihres nächsten Produktionsprojekts beachten sollten.
CNC-Fräsen Designrichtlinien
Stellen Sie sicher, dass die Merkmale mit den gängigen CNC-Fräswerkzeugen kompatibel sind
Wenn Sie sich Gedanken über das Design Ihres Teils machen, ist es von Vorteil zu wissen, welche Werkzeuge beim CNC-Fräsen am häufigsten verwendet werden. Idealerweise sollten Sie Merkmale und Geometrien in Ihrem Teil entwerfen, die mit den Standardfräswerkzeugen kompatibel sind. So können Sie die Durchlaufzeit und die Kosten insgesamt senken. Schließlich muss der Hersteller kein Geld und keine Zeit für die Herstellung oder Beschaffung spezieller Fräswerkzeuge aufwenden.
Vermeiden Sie scharfe Innenecken
Beim CNC-Fräsen werden runde Werkzeuge verwendet. Daher müssen scharfe Innenecken bei der Konstruktion Ihrer Teile vermieden werden. Außerdem müssen abgerundete Ecken größer sein als das Fräswerkzeug. Der Radius der Ecke entspricht der Hälfte des Durchmessers des Fräswerkzeugs. Außerdem ist zu beachten, dass Verrundungen verwendet werden, wenn eine schräge oder verzogene Fläche auf eine scharfe Kante oder eine senkrechte Wand trifft.
Versuchen Sie, schmale, tiefe Schlitze aus Ihrem Entwurf herauszuhalten
Denken Sie bei der Konstruktion Ihres Teils daran, dass die endgültige Tiefe eines Schaftfräsers nicht größer sein darf als das Fünffache des Durchmessers bei Stahl, das Zehnfache des Durchmessers bei Aluminium und das 15-Fache des Durchmessers bei Kunststoffen. Das liegt daran, dass lange Werkzeuge während der Bearbeitung vibrieren und instabil werden können, was zu Oberflächen mit vielen Werkzeugspuren führt. Versuchen Sie alternativ, den Durchmesser des Schneidwerkzeugs zu vergrößern (was eine Vergrößerung der Breite des Merkmals erforderlich machen kann) oder die Tiefe des Merkmals oder der Nut zu verringern. Wenn der Hersteller von zwei Seiten auf das Merkmal zugreifen kann, könnte er außerdem die Länge des Werkzeugs verringern. Dies ist jedoch mit einem zusätzlichen Rüstaufwand verbunden, der die Durchlaufzeit und die Kosten Ihres Projekts erhöht.
Verwenden Sie die größtmöglichen Innenradien
Eine der besten Möglichkeiten, die Kosten für Ihr Projekt zu senken und die Durchlaufzeit zu verkürzen, besteht darin, Ihr Teil so zu konstruieren, dass es mit den größtmöglichen Innenradien kompatibel ist. Je größer der Fräser ist, desto mehr Material kann in einem Arbeitsgang entfernt werden, was zu einem geringeren Werkzeugbedarf und kürzeren Vorlaufzeiten führt. Als Faustregel gilt, dass Sie bei der Konstruktion Ihrer Teile nach Möglichkeit Radien von mindestens 0,8 mm anstreben sollten. Entwerfen Sie außerdem Verrundungen in Ihrem Teil, die etwas größer als der Radius des Schaftfräsers sind. Dadurch wird ein glatterer Weg für den Fräser geschaffen, wodurch Ihr Teil eine bessere Oberflächengüte erhält.
Achten Sie auf die korrekte Wandstärke
Achten Sie auf eine Wandstärke von mehr als 0,50 mm bei Kunststoffen und 0,25 mm bei Metallen. Der Grund dafür ist, dass zu dünne Wände schwer zu bearbeiten sind, da sie Probleme bei der Einhaltung von Toleranzen und Steifigkeit bereiten. Wenn der Hersteller zu viel Material abnimmt, können die Wände Ihres Teils außerdem zu dünn werden, was zu Verformungen und/oder beeinträchtigten Toleranzen führt.
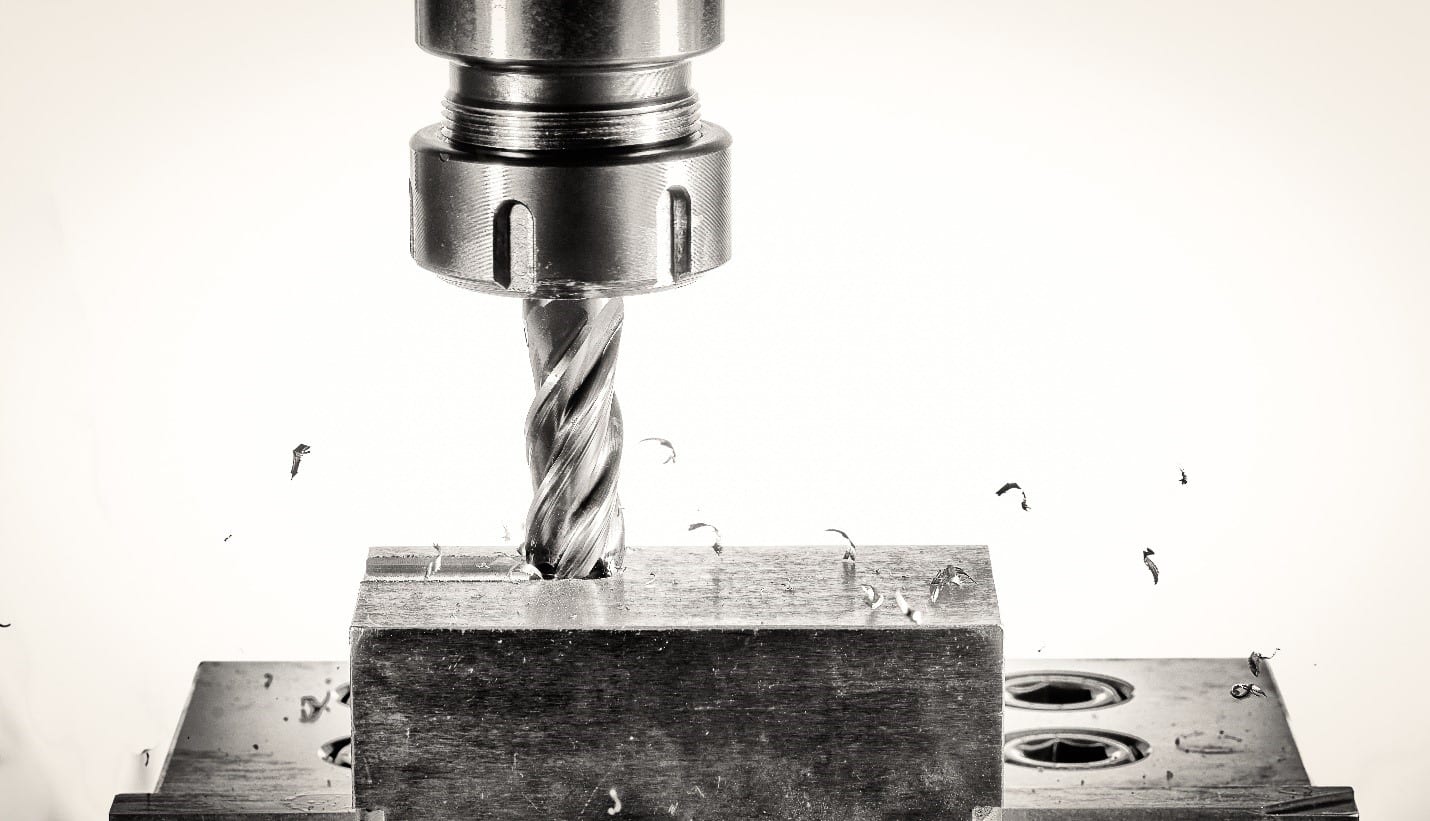
CNC-Fräsen Endbearbeitungsoptionen
Die Einfachheit der "Wie bearbeitet"-Bearbeitung
Bei der CNC-Fräsbearbeitung vieler Teile und Prototypen ist ein Finish "wie bearbeitet" mehr als ausreichend für ihre Bedürfnisse. Bei einem Finish "wie bearbeitet" kann das Schneidwerkzeug einen zusätzlichen Schlichtdurchgang durchführen, um die Rauheit zu verringern, oder das Teil wird einfach so akzeptiert, wie es ist, ohne einen Schlichtdurchgang und mit sichtbaren Werkzeugspuren. Die Standard-Oberflächenrauhigkeit im bearbeiteten Zustand beträgt im Allgemeinen 3,2 μm. Wenn ein Schlichtdurchgang durchgeführt wird, kann die Oberflächenrauheit auf 1,6, 0,8 oder sogar 0,4 μm sinken. Schlichtdurchgänge beim CNC-Fräsen erhöhen natürlich die Produktionskosten, da sie zusätzliche Arbeitsschritte erfordern.
Zusätzlich zu einem Schlichtdurchgang mit dem CNC-Fräswerkzeug können die bearbeiteten Teile auf Wunsch weiter poliert und geglättet werden, wobei jedoch etwas Oberflächenmaterial abgetragen wird, was sich auf die Endtoleranzen Ihres Teils auswirken könnte. Nichtsdestotrotz bieten bearbeitete Oberflächen im Allgemeinen die engsten Toleranzen aller Endbearbeitungsverfahren beim CNC-Fräsen.
Perlstrahlen sorgt für eine noch glattere Oberfläche
Manche Teilekonstrukteure wünschen sich für ihre Teile eine noch feinere Oberflächenbearbeitung als die unbearbeitete Ausführung. Für diese Konstrukteure ist das Perlstrahlen eine Option, da es eine glatte, satinierte oder matte Oberfläche erzeugt und außerdem die Werkzeugspuren entfernt.
Beim Perlstrahlen werden kleine Glasperlen unter hohem Luftdruck gegen die Oberfläche des Teils gepresst. Durch den starken Kontakt der Perlen wird Oberflächenmaterial abgetragen, was zu einem glatteren Finish führt. Wenn Ihr Teil Merkmale mit kritischen Toleranzen, wie z. B. Löcher, aufweist, können Sie diese während des Perlstrahlens abdecken, um zu verhindern, dass die Abmessungen verändert werden.
Pulverbeschichtung bietet zusätzlichen Schutz
Die Pulverbeschichtung ist eine weitere Option für die Endbearbeitung von CNC-Frästeilen. Bei diesem Endbearbeitungsverfahren wird eine dünne Polymerschicht auf das Teil aufgetragen, um seine Oberfläche zu schützen. Diese Polymerschicht ist haltbar und korrosionsbeständig, wodurch das Teil vor Verschleiß geschützt wird. Einer der Vorteile der Pulverbeschichtung ist, dass sie für alle Metallwerkstoffe geeignet ist. Außerdem kann das Perlstrahlen in Kombination mit der Pulverbeschichtung verwendet werden, um glatte Oberflächen zu erzielen.
Das Verfahren der Pulverbeschichtung ähnelt dem der Spritzlackierung, nur dass statt flüssiger Farbe trockenes Pulver versprüht wird. Zu Beginn des Pulverbeschichtungsprozesses wird das Teil häufig grundiert, um die Korrosionsbeständigkeit zu erhöhen. Nach der Grundierung beschichtet ein elektrostatisches Sprühgerät das Teil mit Trockenpulver. Schließlich wird das Teil in einem Hochtemperaturofen ausgehärtet. Ähnlich wie beim Eloxieren des Typs II kann die Pulverbeschichtung erforderlich sein, um eine Vielzahl von Farben für ästhetische Zwecke zu erzielen.
Typ II- und Typ III-Eloxieren für Schutz und Ästhetik
Eine weitere Möglichkeit der CNC-Fräsbearbeitung von Teilen ist das Eloxieren. Beim Eloxieren wird eine dünne keramische Oberflächenschicht erzeugt, die Schutz vor Verschleiß und Korrosion bietet. Die daraus resultierende Beschichtung ist sehr haltbar, leitet keine Elektrizität und kann zu ästhetischen Zwecken in vielen verschiedenen Farben ausgeführt werden. Konstrukteure und Ingenieure müssen wissen, dass Eloxieren nur bei Aluminium- und Titanlegierungen möglich ist.
Beim Eloxieren wird das Teil in eine Schwefelsäurelösung getaucht, und eine elektrische Ladung fließt zwischen dem Bauteil und der Kathode. Die daraus resultierende elektrochemische Reaktion wandelt die Oberfläche des Teils in gehärtetes Titan- oder Aluminiumoxid um. Vor dem Eloxieren können toleranzempfindliche oder elektrisch leitende Bereiche des Teils abgedeckt werden, damit die Maßhaltigkeit nicht beeinträchtigt wird und diese Bereiche auch nach dem Eloxieren noch Strom leiten können.
Es gibt zwei Arten des Eloxierens: Typ II oder Typ III. Hier finden Sie einen Überblick über die beiden Typen:
- Beim Eloxieren des Typs II - gemeinhin als "dekoratives" Eloxieren bezeichnet - können Schichten mit einer Dicke von bis zu 25 μm erzeugt werden. Bei dieser Form des Eloxierens werden Teile mit einer glatten Oberfläche in verschiedenen Farben hergestellt, die dennoch eine gute Korrosionsbeständigkeit aufweisen.
- Beim Eloxieren des Typs III - üblicherweise als "Hartanodisieren" bezeichnet - können Beschichtungen mit einer Dicke von bis zu 125 μm erzeugt werden. Diese Form des Eloxierens bietet eine hervorragende Verschleiß- und Korrosionsbeständigkeit. Dank dieser überragenden Haltbarkeit eignen sich diese Beschichtungen hervorragend für funktionelle Anwendungen.
Erhalten Sie sekundenschnell Angebote für Ihre Bauteile