Biegen von Blechen: Die Grundlagen
Das Blechbiegen ist ein äußerst effektives Verfahren zur Herstellung von Teilen. Erfahren Sie noch heute mehr über das Blechbiegen!
Einführung in das Biegen von Blechen
Das Biegen von Blechen ist eine hervorragende Methode zur Herstellung einer Vielzahl von Teilen. Biegeverfahren können für die Herstellung neuer Teile sehr effizient sein, da die Verfahren relativ einfach durchzuführen sind. Beim Blechbiegen werden äußere Kräfte eingesetzt, um die Form des Blechs zu verändern. Aufgrund seiner Formbarkeit lässt sich Blech in eine breite Palette von Biegungen und Formen bringen.
Das Biegen von Blechen ist eine der weltweit am häufigsten angewandten Praktiken in der Metallverarbeitung. Obwohl es viele Variablen gibt, die bei der Planung eines Blechteils berücksichtigt werden müssen, gibt es einige Standardbiegemethoden, die Sie kennen sollten, um sicherzustellen, dass Ihr nächstes Blechverarbeitungsprojekt das gewünschte Ergebnis bringt. In diesem Artikel erläutern wir die gängigsten Blechbiegemethoden, erklären, was Biegezugabe und K-Faktor bedeuten, und gehen auf einige sehr wichtige Konstruktionstipps für das Blechbiegen ein.
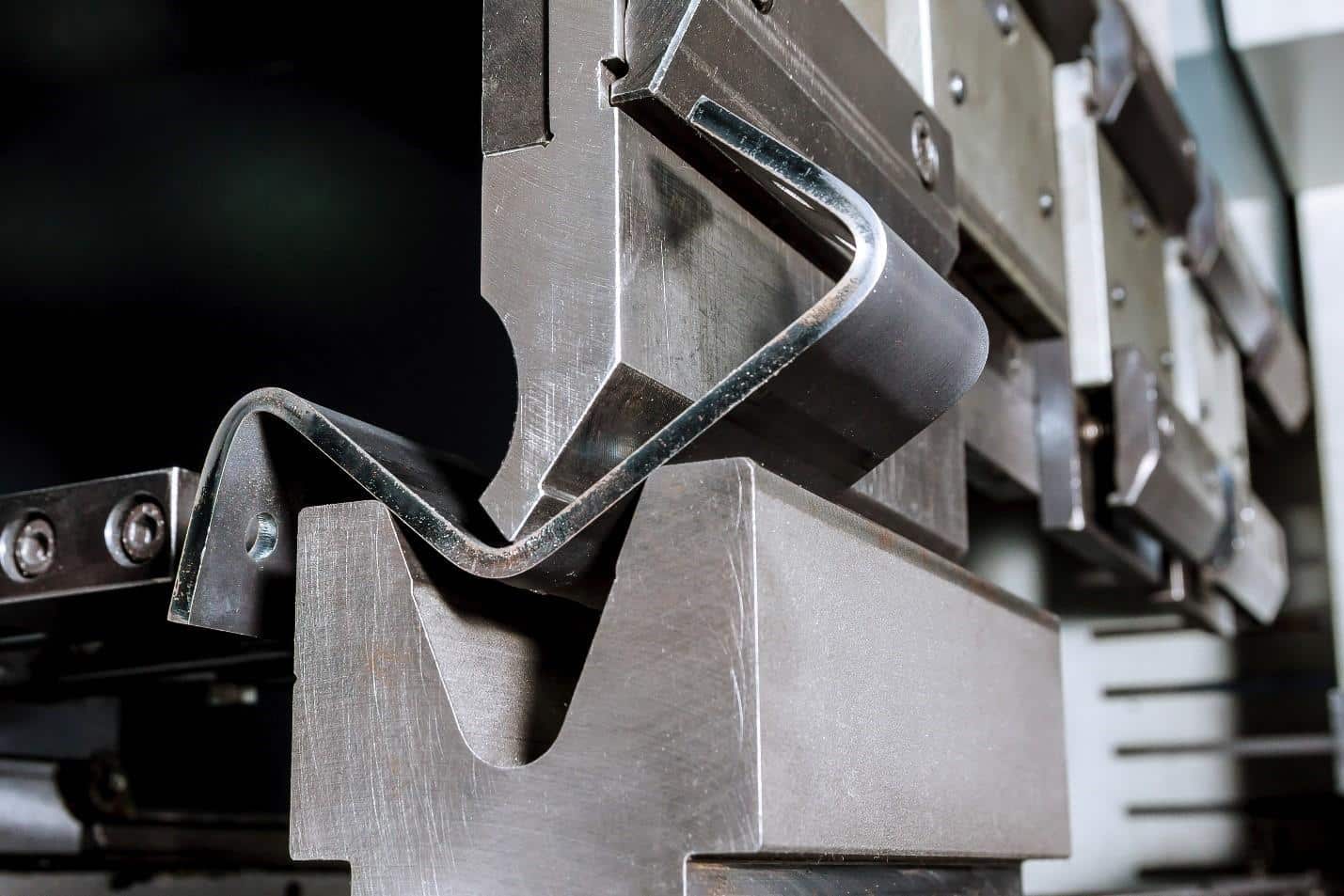
Biegeverfahren
Der Zweck der Blechbiegemethoden besteht darin, Bleche in die vorgesehenen Formen zu bringen. Bei der Entscheidung, welches Blechbiegeverfahren für ein bestimmtes Projekt optimal ist, spielen mehrere Faktoren eine Rolle. Zu diesen Faktoren gehören die Dicke des Blechs, der Biegeradius, die Gesamtgröße der Biegung und die gewünschte Verwendung.
Um besser zu verstehen, welches Blechbiegeverfahren für Ihre Zwecke geeignet ist, werden hier einige der gängigsten Verfahren erläutert:
V-Biegen:
Diese Methode ist sehr verbreitet und wird für die meisten Biegeanforderungen verwendet. Bei dieser Methode werden ein Stempel" und eine V-Matrize" verwendet, um das Blech in bestimmten Winkeln zu biegen. Bei diesem Verfahren übt der Stempel an der Stelle über der V-Matrize Kraft auf das Blech aus. Durch die Kraft des Stempels wird ein Winkel im Blech geformt. Die V-Biegemethode ist relativ effizient, da sie zum Biegen von Stahlblechen verwendet werden kann, ohne dass deren Position verändert werden muss.
Es gibt drei gängige Arten des V-Biegens:
Bodenbiegen
Beim Gesenkbiegen wird das Blech auf den Boden der Matrize gepresst, um die gewünschte Form und den gewünschten Winkel zu erzeugen. Die Form und die Position des Matrizenwinkels bestimmen die endgültige Form der Biegung. Einer der Vorteile des Bodenpressens besteht darin, dass ein Zurückfedern (das später in diesem Artikel besprochen wird) des gepressten Blechs nicht möglich ist. Der Grund dafür ist, dass die starke Kraft des Stempels in Verbindung mit dem Winkel der Matrize eine dauerhafte Übereinstimmung in der endgültigen Struktur des Blechs bewirkt.
Prägen
Das Prägen ist eine Form des V-Biegens, die wegen ihrer Präzision und ihrer Fähigkeit, zwischen Blechen zu unterscheiden, wünschenswert ist. Wie beim Senkbiegen gibt es auch beim Prägen keine Rückfederung des Blechs.
Luftbiegen
Das Luftbiegen - auch partielles Biegen genannt - ist nicht so genau wie das Prägen oder das Tiefziehen. Das Luftbiegen wird in der Regel verwendet, wenn eine einfachere Lösung benötigt wird, da es keine Werkzeuge erfordert. Einer der größten Nachteile des Luftbiegens ist, dass Rückfederung auftreten kann. Beim Luftbiegen übt der Stempel Kraft auf das Blech aus, das auf beiden Seiten der Öffnung der Matrize aufliegt. Beim Luftbiegen wird in der Regel eine Abkantpresse verwendet, da das Blech keinen Kontakt mit dem Boden der Matrize hat.
Walzenbiegen
Das Walzenbiegen ist eine gute Möglichkeit, um gekrümmte Formen oder Rollen im Blech herzustellen. Beim Walzenbiegen werden eine Abkantpresse, eine hydraulische Presse und drei Rollensätze verwendet, um verschiedene Arten von Biegungen zu erzeugen. Daher wird das Walzbiegen häufig für die Herstellung von Rohren, Kegeln und sogar Hohlkörpern verwendet, da es den Abstand zwischen den Walzen nutzt, um Kurven und Biegungen zu erzeugen.
U-Biegen
Das U-Biegen ist dem V-Biegen konzeptionell sehr ähnlich. Der Unterschied besteht darin, dass bei dieser Methode eine U-Form im Blech erzeugt wird und nicht eine V-Form. Wie das V-Biegen wird auch das U-Biegen sehr häufig eingesetzt.
Wischbiegen
Das Wischbiegen ist eine Methode, die häufig zum Biegen der Blechkanten verwendet wird. Bei diesem Verfahren wird das Blech auf eine Wischmatrize gelegt und dort durch ein Druckkissen festgehalten. Ein Stempel übt dann Kraft auf die Kante des Blechs aus, um die resultierende Biegung zu erzeugen. Die Matrize ist wichtig, da sie den Innenradius der Biegung bestimmt.
Rotationsbiegen
Das Rotationsbiegen ist vorteilhaft, weil es keine Kratzer auf der Blechoberfläche verursacht, wie es beim Wischbiegen und V-Biegen der Fall ist. Außerdem ist das Rotationsbiegen vorteilhaft, weil es das Blech in scharfe Ecken biegen kann.
Biegung Rückfederung
Einer der wichtigsten Faktoren, der bei einigen Blechbiegemethoden eine Rolle spielen kann, ist die Rückfederung. Wenn es nicht richtig gehandhabt wird, kann das Blech nach dem Biegen wieder in seine ursprüngliche Form "zurückfedern". Aus diesem Grund muss die Rückfederung berücksichtigt werden, indem das Blech etwas über die beabsichtigte Position oder den beabsichtigten Winkel hinaus gebogen wird.
Biegetoleranz und K-Faktor
Die Biegezugabe beschreibt die Anpassung, die vorgenommen wird, um der Tendenz des Blechs Rechnung zu tragen, sich wieder in seine ursprüngliche Form zu biegen. Wenn Bleche aus ihrer ursprünglichen Form gebogen werden, ändern sich ihre Abmessungen. Die Kraft, die zum Biegen des Blechs aufgebracht wird, bewirkt, dass es sich innen und außen dehnt und staucht. Dadurch ändert sich die Gesamtlänge des Blechs aufgrund des Drucks und der Dehnung im Bereich der Biegung. Die Länge, gemessen von der Dicke der Biegung zwischen der äußeren und der inneren zusammengedrückten Fläche unter Spannung, bleibt jedoch konstant. Dies wird durch eine Linie dargestellt, die allgemein als neutrale Achse bezeichnet wird.
Die Biegezugabe berücksichtigt den Winkel der Biegung, die Blechdicke, die spezifische Biegemethode und den K-Faktor (eine Konstante, die in Biegeberechnungen verwendet wird und die Abschätzung der Dehnung des Blechs ermöglicht). Es handelt sich um das Verhältnis zwischen der Kompression auf der Innenseite der Biegung und der Spannung außerhalb der Biegung. Wenn sich die Innenseite des Blechs zusammenzieht, dehnt sich die Außenseite aus und der K-Faktor bleibt konstant. Der K-Faktor liegt normalerweise zwischen 0,25 und 0,5. Er hilft bei der Bestimmung der spezifischen Art von Materialien, die vor Beginn des Beschneidens benötigt werden, und wird auch in der Tabelle für den Biegeradius verwendet.
Tipps für die Blechkonstruktion beim Biegen
Bei der Planung der Biegung Ihres Blechs gibt es einige wichtige Design-Tipps zu beachten, wenn Sie eine Verformung Ihrer Blechbiegungen vermeiden wollen:
Gleichmäßige Wanddicke
Es ist unbedingt erforderlich, dass Ihre Teile eine einheitliche Wandstärke haben.
Abstände zwischen Nuten und Löchern
Der Abstand zwischen den Löchern und der Biegung muss mindestens das 2,5-fache der Blechdicke betragen. Für Schlitze sind größere Abstände erforderlich. Schlitze müssen mindestens das 4-fache der Blechdicke von den Kanten der Biegung entfernt sein. Der Grund für diesen Abstand ist, dass sich Löcher und Schlitze verformen, wenn sie sich zu nahe an einer Biegung befinden. Außerdem sollten Löcher und Schlitze mindestens das 2-fache der Materialdicke von der Kante des Teils entfernt sein, wenn Sie Ausbeulungen vermeiden wollen.
Biegeradius
Die Biegeradien müssen mindestens so groß sein wie die Blechdicke. Diese Anforderung verhindert, dass sich Ihr Blechteil verformt oder gar bricht. Außerdem sollten Sie Ihre Biegeradien gleichmäßig halten, um Kosten zu sparen. Außerdem sollten alle Biegungen in einer Ebene in derselben Richtung ausgeführt werden, um eine Umorientierung des Teils zu vermeiden. Die Vermeidung einer Neuausrichtung von Teilen senkt die Kosten und verkürzt die Vorlaufzeiten für Ihr Projekt. Ein wichtiger Faktor ist, dass Sie es vermeiden sollten, kleine Biegungen in sehr dicken Teilen zu konstruieren, da diese anfällig für Ungenauigkeiten sind.
Biegungen
Eine wichtige Faustregel besagt, dass der Außenradius von Biegungen mindestens das Doppelte der Blechdicke betragen muss. Außerdem muss der Abstand der Löcher von den Biegungen mindestens dem Radius der Biegung zuzüglich der Blechdicke entsprechen. Darüber hinaus sollte der Abstand anderer Biegungen von der Krümmung mindestens das Sechsfache der Blechdicke zuzüglich des Krümmungsradius betragen.
Senkungstiefen und Abstände
In den meisten Fällen werden Senkungen an Blechteilen mit Handwerkzeugen angebracht. Aus diesem Grund ist es wichtig zu beachten, dass Senkungen nicht tiefer als 60 % der Blechdicke sein dürfen. Außerdem müssen Senkungen mindestens den 4-fachen Abstand der Blechdicke zu einer Kante, den 3-fachen Abstand zu einer Biegung und den 8-fachen Abstand zu einer anderen Senkung haben.
Säume
Säume sind einfach Falten an den Kanten von Teilen, die für abgerundete Kanten sorgen. Es gibt drei Arten von Säumen, für die jeweils eigene Gestaltungsregeln gelten. Bei offenen Säumen muss der Innendurchmesser mindestens der Blechdicke entsprechen, da ein zu großer Durchmesser die Rundheit beeinträchtigt. Außerdem muss für eine perfekte Biegung die Rücklauflänge das Vierfache der Blechdicke betragen. Ebenso muss der Innendurchmesser von Tränensäumen mindestens gleich der Blechdicke sein. Außerdem sollte die Öffnung mindestens 25 % der Blechdicke betragen und die auf den Radius folgende Lauflänge muss mindestens das 4-fache der Blechdicke betragen.
Abgeschrägte Seiten
Vereinfacht gesagt, sind Fasen an Flanschen erforderlich, um ausreichend Platz für Biegungen zu haben, damit die Teile nicht verformt werden.
Aufeinanderfolgende Biegungen
Generell sollte es nach Möglichkeit vermieden werden, Biegungen direkt nebeneinander zu platzieren. Wenn der Abstand zwischen den Biegungen nicht ausreichend ist, kann es sehr schwierig sein, die bereits gebogenen Teile in die Matrize einzupassen. In Fällen, in denen Biegungen nahe beieinander liegen müssen, muss die Länge des Zwischenteils größer sein als die Länge der Flansche.
Abstände zwischen Laschen und Kerben
Der Abstand zwischen einer Biegung und einer Ausklinkung muss mindestens das Dreifache der Blechdicke zuzüglich des Biegeradius betragen. Laschen müssen die Blechdicke oder 1 mm Abstand voneinander haben, je nachdem, welcher Wert größer ist.
Entlastungsschnitte
Entlastungsschnitte sind unerlässlich, um ein Ausbeulen und sogar ein Reißen an Biegungen zu verhindern. Die Breite der Entlastungsschnitte muss gleich oder größer als die Blechdicke sein. Außerdem darf die Länge der Entlastungsschnitte nicht länger als der Biegeradius sein.
Erhalten Sie sekundenschnell Angebote für Ihre Bauteile