Spritzgießens
Erfahren Sie, was Spritzgießen ist, wie es funktioniert und wie es in der Industrie eingesetzt wird.
Was ist die Geschichte des Spritzgießens?
Spritzgießens ist der Prozess, bei dem ein flüssiger oder flexibler Rohstoff unter Verwendung eines starren Rahmens, einer sogenannten Gussform, geformt wird. Dieses Verfahren, das heute in vielen Industriezweigen sehr beliebt ist, setzte sich auf dem Höhepunkt des Zweiten Weltkriegs durch, als der Bedarf an massenproduzierten Gütern stieg.
Der industrielle Aufstieg des Spritzgießens: Massenproduktion
1872 schufen der amerikanische Erfinder John Wesley Hyatt und sein Bruder Jesaja die erste Spritzgussmaschine. Es handelte sich um eine einfache Maschine, die einen Kolben benutzte, um Kunststoff durch einen heißen Zylinder in eine Form zu drücken. Die Maschine wurde in erster Linie für die Massenproduktion von Produkten wie Knöpfen und Kämmen eingesetzt.
Der deutsche Chemiker Arthur Eichengrün entwickelte 1919 die erste Spritzgusspresse. Er meldete 1939 ein Patent für das Spritzgießen von plastifiziertem Zelluloseacetat an, das wesentlich schwerer entflammbar war als die damals gebräuchlichen Lösungen.
Mit Ausbruch des Zweiten Weltkriegs stieg der Bedarf an massenproduzierten preiswerten Gütern. Der Krieg in Asien und Angriffe auf See behinderten die Gummiproduktion. Panzer und andere Kriegsausrüstungen schufen eine enorme Nachfrage nach Metall. Um diese Lücken zu füllen, wurden Kunststoffe verwendet, die einen erschwinglichen Ersatz boten. James Watson Hendry schuf daraufhin das erste Schneckenspritzgusswerkzeug, das wegen seines Präzisions- und Kontrollgrades und der damit verbundenen besseren Produktionsqualität schnell populär wurde.
Während der gesamten Nachkriegszeit blieben Kunststoffe populär. Als führende Unternehmer die enormen Kostenvorteile gegenüber konkurrierenden Materialien erkannten, bewerteten sie die globalen Lieferketten neu. Kunststoffe etablierten sich fest in der Wirtschaft und den Herstellungsprozessen der Mitte des zwanzigsten Jahrhunderts.
Die Erfindung des Spritzgießens bis zum heutigen Tag
In den 1970er Jahren entwickelte Hendry dann das erste gasunterstützte Spritzgusssystem. Mit dieser Technik war es möglich, komplexe Teile herzustellen, die schnell gekühlt werden konnten. Dadurch wurden die Flexibilität und Festigkeit der hergestellten Objekte erheblich verbessert und gleichzeitig die Produktionszeit und -kosten reduziert. Im Jahr 1979 überholte die Kunststoffproduktion die Stahlproduktion, und ab 1990 wurden beim Spritzgießen weitgehend Aluminiumformen verwendet. Heute stellen Schneckenspritzgussmaschinen die überwiegende Mehrheit der Spritzgussmaschinen dar. Andere heute noch weit verbreitete Formverfahren sind Blasformen, Formpressen oder Vakuumformen (Thermoformen).
Heute repräsentieren Spritzgießverfahren einen Markt von 300 Milliarden Dollar. Mit diesem Verfahren werden weltweit jedes Jahr mehr als 5 Millionen Tonnen Kunststoffteile hergestellt. Nahezu alle Sektoren des verarbeitenden Gewerbes verwenden es: Elektronik, Automobilbau, Haushaltswaren und -geräte usw. Das Kunststoff-Spritzgießen ist nach wie vor eine erschwingliche und effiziente Methode zur Herstellung qualitativ hochwertiger Teile und Produkte. In jüngster Zeit hat die Nachfrage nach biologisch abbaubaren Materialien aus Umweltgründen zugenommen.
Die heute verwendete Technologie ist der vorherigen sehr ähnlich. Allerdings haben Computer den gesamten Entwurfs- und Herstellungsprozess erleichtert. Die Ergebnisse sind genauer, und Kunststoffteile sind heute oft die bevorzugte Wahl für fortschrittliche technologische und wissenschaftliche Anwendungen.
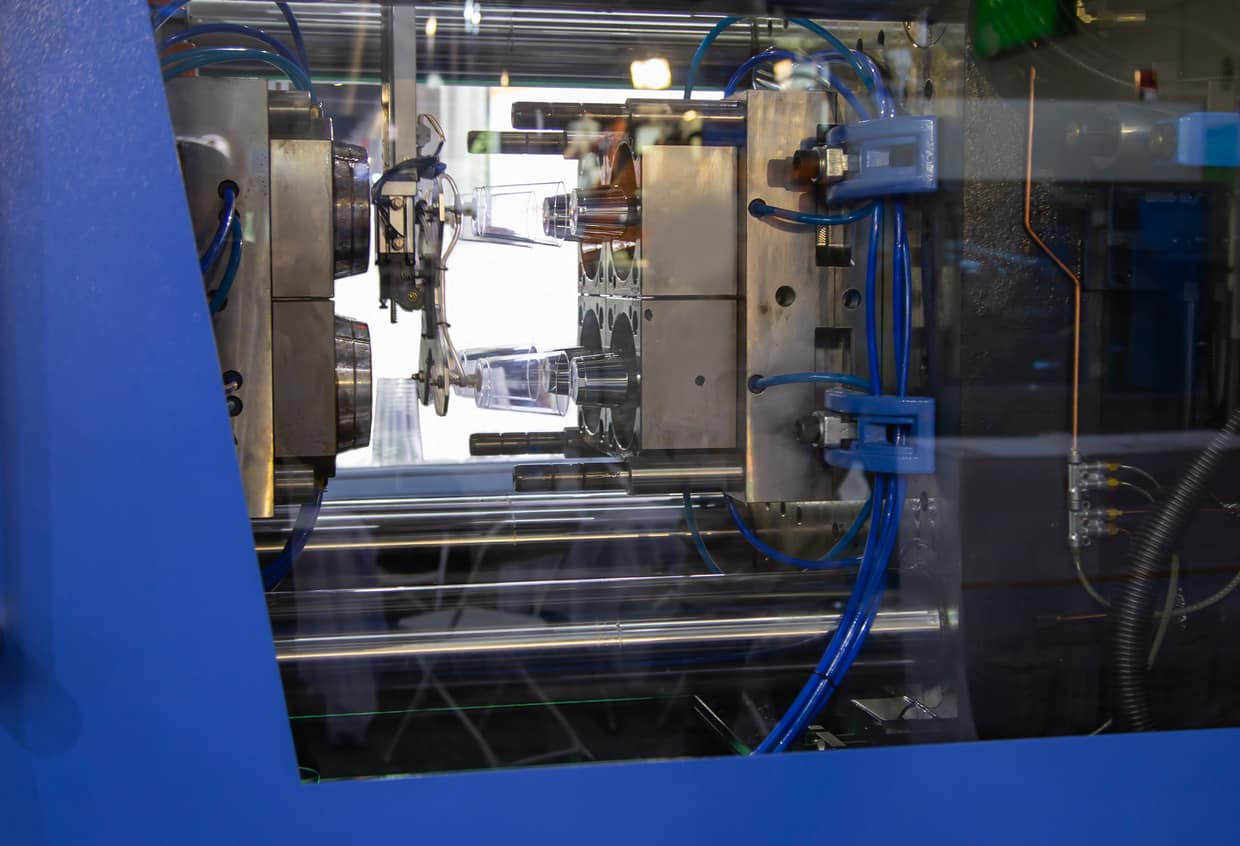
Was ist Gießen?
Beim Gießen wird einem flüssigen oder flexiblen Rohmaterial mit Hilfe eines starren Rahmens, einer Gussform, eine Form gegeben. Die Gussform ist ein Hohlblock, der mit einem Material wie Kunststoff, Glas, Metall oder keramischen Rohstoffen gefüllt ist. Dieses härtet im Inneren der Form aus oder gefriert und nimmt so sein endgültiges Aussehen an. Die gebräuchlichsten Verfahren sind das Spritzgießen, Blasen, Pressen und Vakuumformen. Während der Entwurf von Formen und ihren Prototypen in Bezug auf Komplexität und Finanzierung ein Hindernis darstellen kann, wird der 3D-Druck dank seiner Schnelligkeit in der Ausführung und seiner Präzision bei der Realisierung zu einer relevanten Lösung.
Spritzgießen
Beim Spritzgießen schmilzt das Material und wird dann unter Druck in eine Gussform gespritzt. Der flüssige Kunststoff kühlt ab und verfestigt sich. Dieser Vorgang kann mit einer Vielzahl von Materialien (Metalle, Glas, Thermoplaste usw.) durchgeführt werden. Die am häufigsten verwendeten Materialien sind jedoch:
- Polypropylen (PP), das etwa 38% der Weltproduktion ausmacht. Es wird zum Beispiel für Flaschenverschlüsse verwendet, da es für den Kontakt mit Lebensmitteln geeignet ist,
- ABS, das 27% der Produktion ausmacht. Lego schätzt es aufgrund seiner hohen Schlagfestigkeit. So wird jeder Baustein mit Toleranzen von bis zu 10 Mikrometern ausgelegt,
- Polyethylen (PE), 15%,
- Polystyrol (PS), 8%.
Unter Berücksichtigung aller anderen möglichen Herstellungstechnologien macht allein das Spritzgießen dieser vier Materialien jährlich mehr als 40% aller weltweit produzierten Kunststoffteile aus.
Die Automobilindustrie ist eine der Branchen, die zum Wachstum des Marktes beiträgt, da fast alle Kunststoffteile im Innenraum eines Autos im Spritzgussverfahren hergestellt werden. Die Industrie nutzt besonders:
- Polypropylen (PP) für unkritische Teile,
- PVC wegen seiner guten Wetterbeständigkeit,
- ABS für seine hohe Schlagfestigkeit.
Mindestens eines dieser Materialien kann in mehr als der Hälfte der Kunststoffteile eines Fahrzeugs eingearbeitet werden, darunter Stoßstangen, Innenverkleidungen und Armaturenbretter.
Die Gehäuse der meisten Geräte der Unterhaltungselektronik werden ebenfalls im Spritzgussverfahren hergestellt. ABS und Polystyrol (PS) sind wegen ihrer hohen Beständigkeit und guten elektrischen Isolierung am beliebtesten.
Dieses Verfahren wird wegen seiner extrem niedrigen Stückkosten in der Produktion großer Serien immer beliebter. Beispielsweise können mit dieser Technologie 1.000 bis 100.000 Einheiten für jeweils 1 bis 5 Dollar hergestellt werden. Sie bietet eine gute Wiederholbarkeit und flexible Gestaltungsmöglichkeiten.
Blasformen
Blasformen ist ein Verfahren, bei dem Hohlkörper aus Kunststoff, Glas oder anderen Materialien geformt und zusammengefügt werden.
Es gibt drei Hauptarten des Blasformens: Extrusionsblasformen, Spritzblasformen und Spritzstreckblasformen.
Bei dieser Technik wird der Kunststoff zunächst geschmolzen und zu einem Vorformling geformt wird. Dieser Begriff bezieht sich auf ein röhrenförmiges Stück Kunststoff mit einem Loch an einem Ende, durch das Druckluft strömen kann.
Der Vorformling wird dann in eine Form eingespannt, bevor Luft eingeblasen wird. Der Druck drückt das Material dann nach außen, damit es in die Form passt. Die Form öffnet sich, sobald der Kunststoff abgekühlt und ausgehärtet ist. Schließlich wird das Teil ausgeworfen.
Formpressen
Das Formpressen ist eine Technik, bei der das Material, normalerweise vorgewärmt, in einen offenen, beheizten Formhohlraum eingebracht wird. Die Form wird durch ein Oberdruck- oder Stopfenelement geschlossen. Es wird Druck ausgeübt, um das Material mit allen Formbereichen in Kontakt zu bringen, bis das Material ausgehärtet ist.
Dieses Verfahren hat den Vorteil, dass große und ziemlich komplexe Teile geformt werden können. Darüber hinaus ist dies eine der kostengünstigsten Methoden der Formgebung und verschwendet relativ wenig Material.
Das Formpressen wird in erster Linie zur Herstellung von Verbundwerkstoffteilen entwickelt, die Metall ersetzen. Diese Technik wird im Allgemeinen verwendet, um größere, flache oder moderat gekrümmte Teile zu konstruieren. In der Automobilbranche wird es häufig zur Herstellung von Autoteilen wie Motorhauben, Stoßstangen, Kotflügeln und kleineren, komplexeren Objekte verwendet.
Vakuum-Gießen
Das Vakuum-Gießen bzw. -formen ist eine vereinfachte Version des Thermoformens, bei der eine Kunststoffplatte erhitzt, über eine Formoberfläche gestreckt und durch ein Vakuum gegen diese gedrückt wird. Dieser Prozess verwandelt den Kunststoff in dauerhafte Objekte wie Verkehrsschilder und Schutzabdeckungen.
Es ist möglich, relativ tiefe Teile zu formen, wenn die Platte mechanisch oder pneumatisch gedehnt wird, bevor sie mit der Formoberfläche in Kontakt gebracht und das Vakuum angelegt wird.
Für das Vakuumformen geeignete Materialien sind in der Regel Thermoplaste. Das gebräuchlichste und am einfachsten zu verwendende Material ist die Polystyrolplatte, die eine hohe Schlagfestigkeit aufweist. Sie kann in fast jede Form gebracht werden. Sie kann sowohl Wärme als auch Form behalten, wenn heißes Wasser angewendet wird. Dies macht sie zu einer bevorzugten Wahl für die Verpackung von Produkten, die geschmacks- und geruchsempfindlich sind. Die Technik eignet sich ebenfalls für transparente Materialien wie Acryl. Diese Material ist in der Luft- und Raumfahrtindustrie z.B. für Fensterabdeckungen in den Passagierkabinen von starrflügeligen Militärflugzeugen und in den Abteilen von Drehflüglern weit verbreitet.
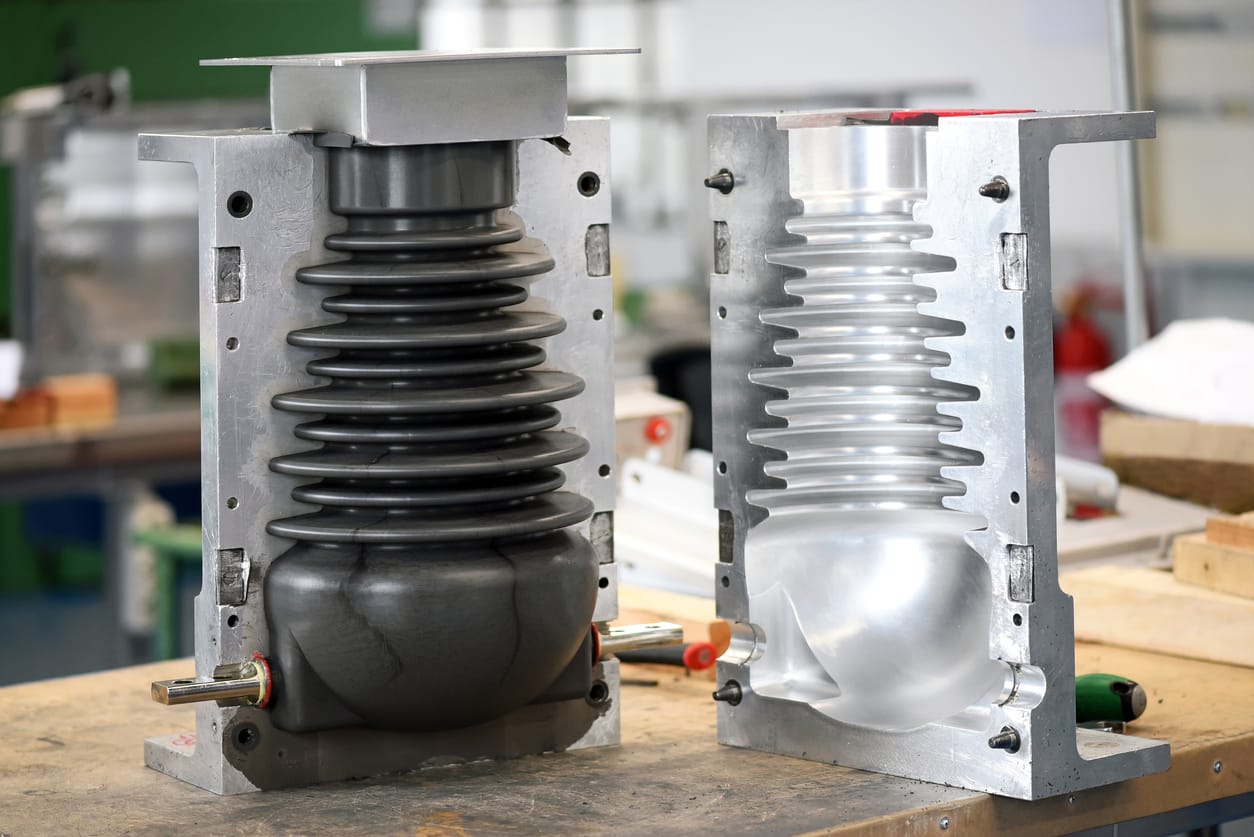
Erhalten Sie sekundenschnell Angebote für Ihre Bauteile