Gerichtete Energiedeposition – DED, LENS, EBAM
Entdecken Sie, wie das 3D-Druckverfahren Gerichtete Energiedeposition, auch bekannt als Directed Energy Deposition, DED, LENS, EBAM, funktioniert.
Gerichtete Energiedeposition
Mit der 3D-Printing-Technologie der gerichteten Energiedeposition (Directed Energy Deposition, DED), auch bekannt als direkte Energiedeposition (Direct Energy Deposition), werden Teile durch direktes Schmelzen von Materialien und schichtweises Ablegen auf dem Werkstück erzeugt. Dieses Verfahren der additiven Fertigung wird hauptsächlich bei Metallpulvern oder Drahtquellmaterialien verwendet. Weitere beliebte Begriffe für DED sind lasergefertigte Formgebung, gerichtete Lichtfertigung, direkte Metalldeposition und Laserauftragsschweißen (Laser Deposition Welding, LDW). Zusätzlich zur Möglichkeit, Teile von Grund auf neu zu bauen (häufig mit einem CNC-Hybridwerkzeug Fräsen/Drehen), besteht mit DED auch die Möglichkeit, komplexe beschädigte Teile wie Turbinenschaufeln oder Propeller zu reparieren.
Die meisten DED-3D-Drucker sind Industriemaschinen mit sehr großen Abmessungen, die eine geschlossene und kontrollierte Umgebung erfordern. Daher besteht eine typische gerichtete Energiedeposition aus einer Düse, die auf einem Mehrachsen-Arm in einem geschlossenen Rahmen montiert ist und geschmolzenes Material auf der Werkstückoberfläche ablagert, wo es sich verfestigt. Der Prozess ähnelt im Prinzip der 3D-Drucktechnik bei der Materialextrusion. Bei DED kann sich eine Düse aber in mehrere Richtungen bewegen, mit bis zu fünf verschiedenen Achsen im Vergleich zu nur drei bei den meisten FFF-Maschinen.
Die verschiedenen Technologien der Gerichtete Energiedeposition
Der Begriff „gerichtete Energiedeposition“ kann mehrere verschiedene Technologien umfassen. Sie unterscheiden sich durch die Art und Weise, in der das Material verschmolzen wird, die jeweils für unterschiedliche und spezifische Zwecke geeignet sind. Die beliebtesten Produkte sind:
- LENS-Technologie von Optomec. LENS 3D-Fertigungssysteme verwenden Laser, um Objekte schichtweise direkt aus pulverförmigen Metallen, Legierungen, Keramik oder Verbundstoffen zu erstellen. Der LENS-Prozess muss in einer hermetisch abgedichteten Kammer erfolgen, die mit Argon gefüllt ist, damit der Sauerstoff- und Feuchtigkeitsgehalt sehr gering bleibt. Dadurch bleibt das Teil sauber und Oxidation wird verhindert. Das Metallpulvermaterial wird direkt an den Materialablagerungskopf geliefert. Sobald eine einzelne Schicht abgelegt wurde, geht der Materialablagerungskopf zur nächsten Schicht über. Durch das Erstellen aufeinander folgender Schichten wird das gesamte Teil erstellt. Nach Abschluss des Vorgangs wird die Komponente entfernt und kann auf beliebige Weise wärmebehandelt, heißisostatisch gepresst, bearbeitet oder fertig gestellt werden.
- Aerosol Jet-Technologie von Optomec. Die Aerosol Jet 3D-Printing-Technologie von Optomec bietet einen kostengünstigen, skalierbaren Prozess zum Drucken funktionaler Antennen und Sensoren direkt auf Verbraucher- und Industriekomponenten, wodurch sie zu intelligenten IoT-Geräten (Internet of Things) werden. Zu den möglichen gedruckten Antennen gehören LTE, NFC, GPS, Wi-Fi, WLAN und BT. Diese Technik ist den einfachen Ablagerungstechniken näher, eignet sich jedoch für komplexe, zusammengesetzte und gekrümmte Oberflächen.
Aerosol Jet-Systeme eignen sich ideal für die Entwicklung, Herstellung, Verbesserung und Reparatur von elektronischen und biologischen Hochleistungsgeräten für Konsumenten, Halbleiterverpackungen, Displays sowie Endprodukte in den Bereichen Luft- und Raumfahrt/Verteidigung, Automobil und Life Sciences. Die Aerosol Jet-Technologie kann bei einer Vielzahl von Materialien eingesetzt werden, darunter leitfähige Nanopartikel aus Metall, dielektrische Pasten, Halbleiter und andere funktionelle Materialien. - Electron Beam Additive Manufacturing (EBAM). 3D-Printing-Technologie von Sciaky. EBAM (Electron Beam Additive Manufacturing) ist eine Technologie der additiven Fertigung, mit der große Metallstrukturen produziert werden. Die firmeneigene Electron-Beam-Pistole (EB) von Sciaky dient zum schichtweisen Ablagern von Metall über einen Drahtvorlauf, bis das Teil fast die Netzform erreicht und für die abschließende Bearbeitung bereit ist. Die Ablagerungsraten reichen von 3 bis 9 kg Metall pro Stunde. Zu den kompatiblen Metallen gehören Titan, Tantal und Nickel. Dieses DED-Verfahren kann auch zur Reparatur beschädigter Teile verwendet werden.
- Laserauftragschweißen (Laser Deposition Welding, LDW) und Hybrid Manufacturing von DMG MORI. Beim additiven Fertigungsprozess des Laserauftragschweißens (LPW) wird die Metallablagerung durch eine Pulverdüse erreicht, die bis zu 10 Mal schneller sein kann als die PBF-Technologie. Darüber hinaus hat das Unternehmen DMG MORI seine additive LDW-Fertigungstechnologie in eine 5-Achs-Fräsmaschine integriert. Diese innovative Hybridlösung kombiniert die Flexibilität des Lasermetallabscheideprozesses mit der Präzision des Schneidvorgangs und ermöglicht so die additive Fertigung in Fräsqualität. Diese Kombination ermöglicht die Herstellung von hochpräzisen Metallteilen für verschiedene Größen.
> Metalle können mit der additiven DED-Fertigungstechnik in 3D gedruckt werden und umfassen insbesondere Aluminium, Kupfer, Titan, Edelstahl, Werkzeugstahl, Kupfer-Nickel-Legierungen und mehrere Stahllegierungen. Jede Untertechnik der gerichteten Energiedeposition hat ihre eigenen Einschränkungen und Kompatibilitäten.
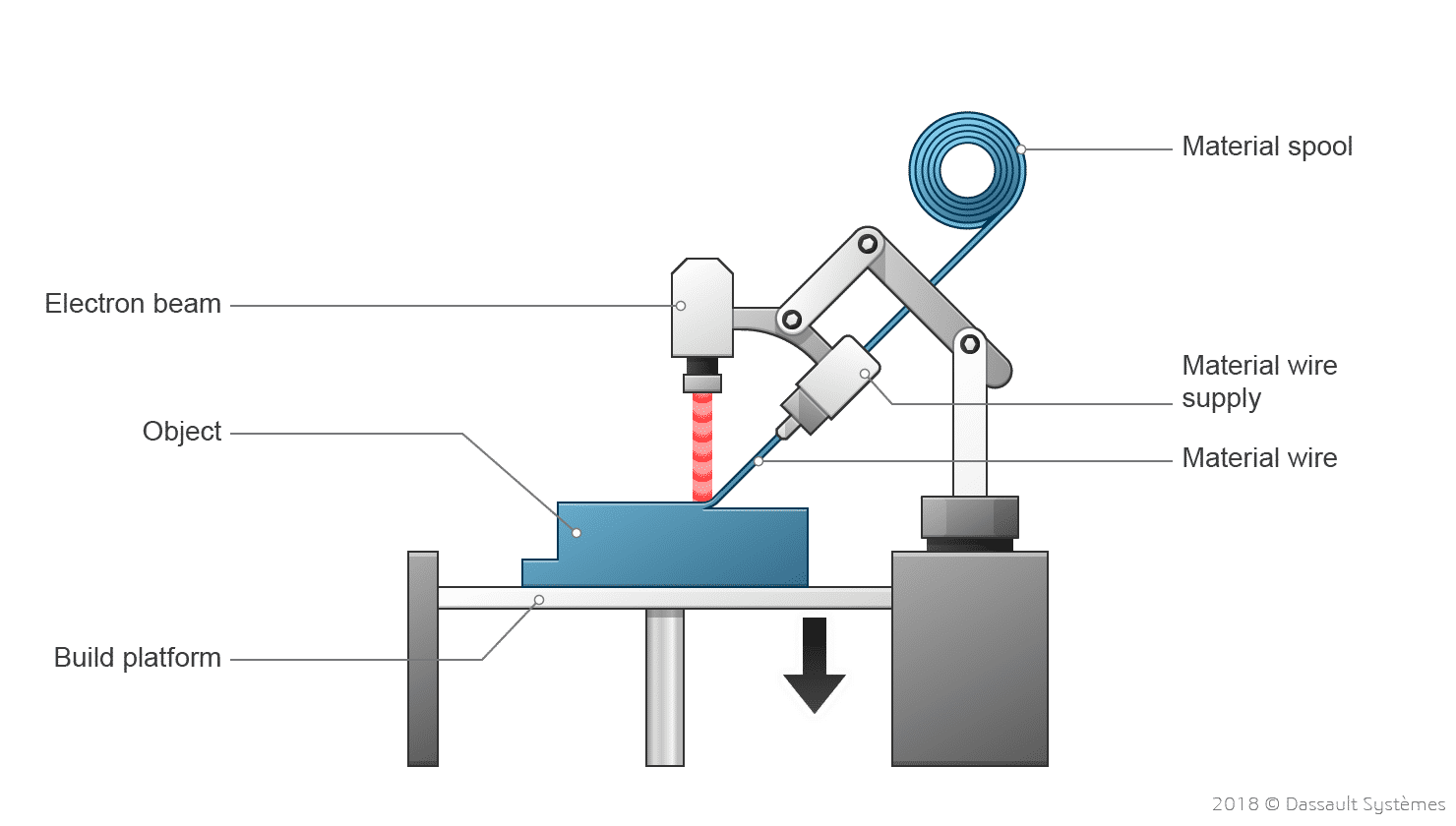
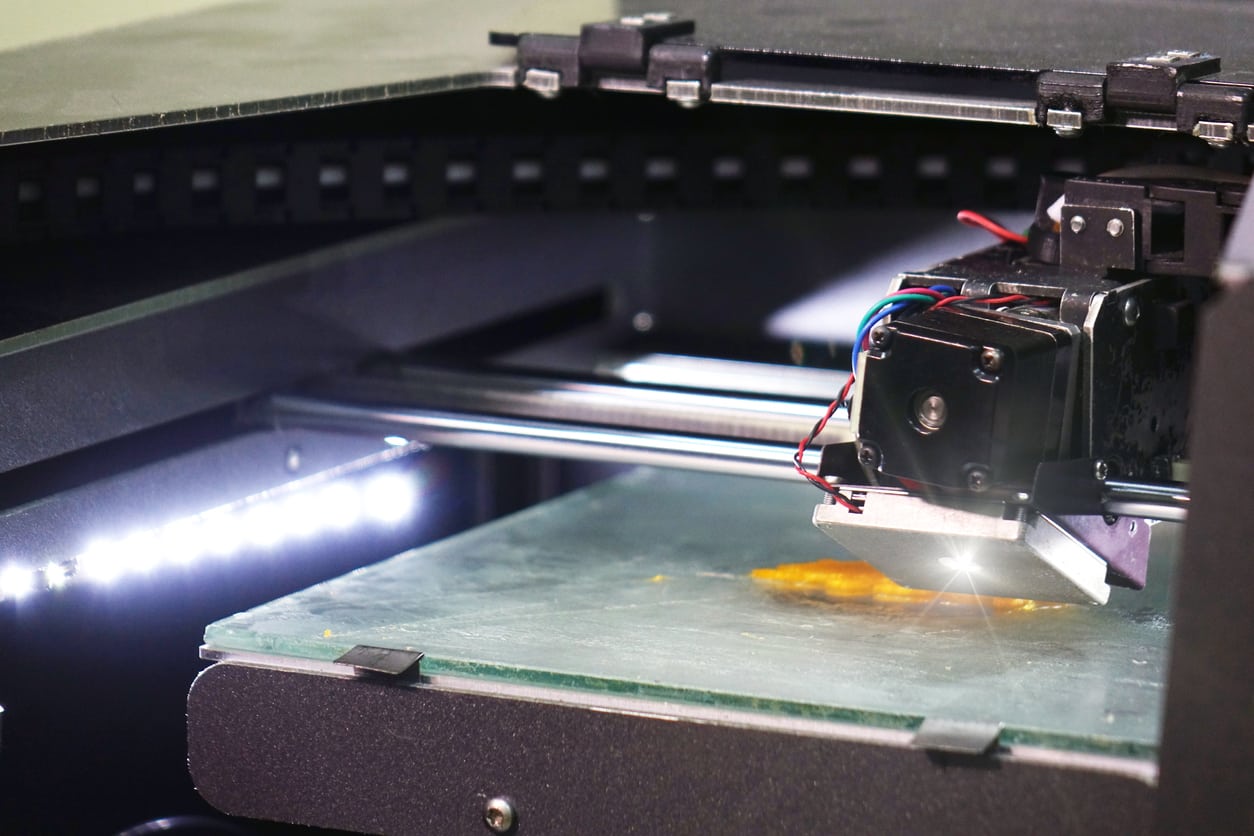
Erhalten Sie sekundenschnell Angebote für Ihre Bauteile