Helix
Electric powertrain developer Helix has broken records and won awards for its high-performance electric motors and inverters. It is driving continuous improvements with 3DEXPERIENCE to achieve a finely tuned design and streamline engineering process from concept to manufacturing.
The next-generation electric powertrains
At first glance, the Triumph TE-1 is instantly recognizable as a performance bike from the iconic British motorcycle brand. It rides and handles like a Triumph triple cylinder internal combustion sports motorcycle too. Yet the TE-1 is no ordinary Triumph. It’s the company’s first foray into the world of electric vehicles. And it’s the final prototype in a ground-breaking collaboration between Triumph and Helix that has the power to challenge assumptions about what electric motorbikes can really do.
Helix is the company behind the TE-1’s electric powertrain. Its Scalable Integrated Motor and Inverter (SIMI) technology delivers an impressive 130kW (177PS/175bhp) of peak power that allows the bike to reach 0-60mph (0-96 km/h) in 3.6 seconds and travel 161 kilometers on a single charge. Delivering this kind of world-class engine performance is exactly what the UK electric powertrain engineering and manufacturing specialist is known for.
“We have been producing electric motors since 2009 and our products have the best power density you can buy,” said Darren Cairns, director and chief executive officer at Helix. “If you’re looking for an application where you need a motor that’s very compact, with very high power output, we have the leading products in the market.”
A full-service supplier of premium electric powertrains, Helix delivers everything from off-the-shelf electric motors and inverters to tailored engineering and technology packages like the ones used by Triumph, the NIO 333 Formula-E team and Lotus for its all-electric Lotus Evija hypercar. Operating at the cutting edge of the industry, the company continuously refines its own processes and systems to meet its customers’ specific requirements for configurable products while continuously bringing down associated development costs. It’s one of the main reasons that Helix has switched to a centralized collaborative, model-based, multidisciplinary environment for product lifecycle management (PLM) – the 3DEXPERIENCE platform.
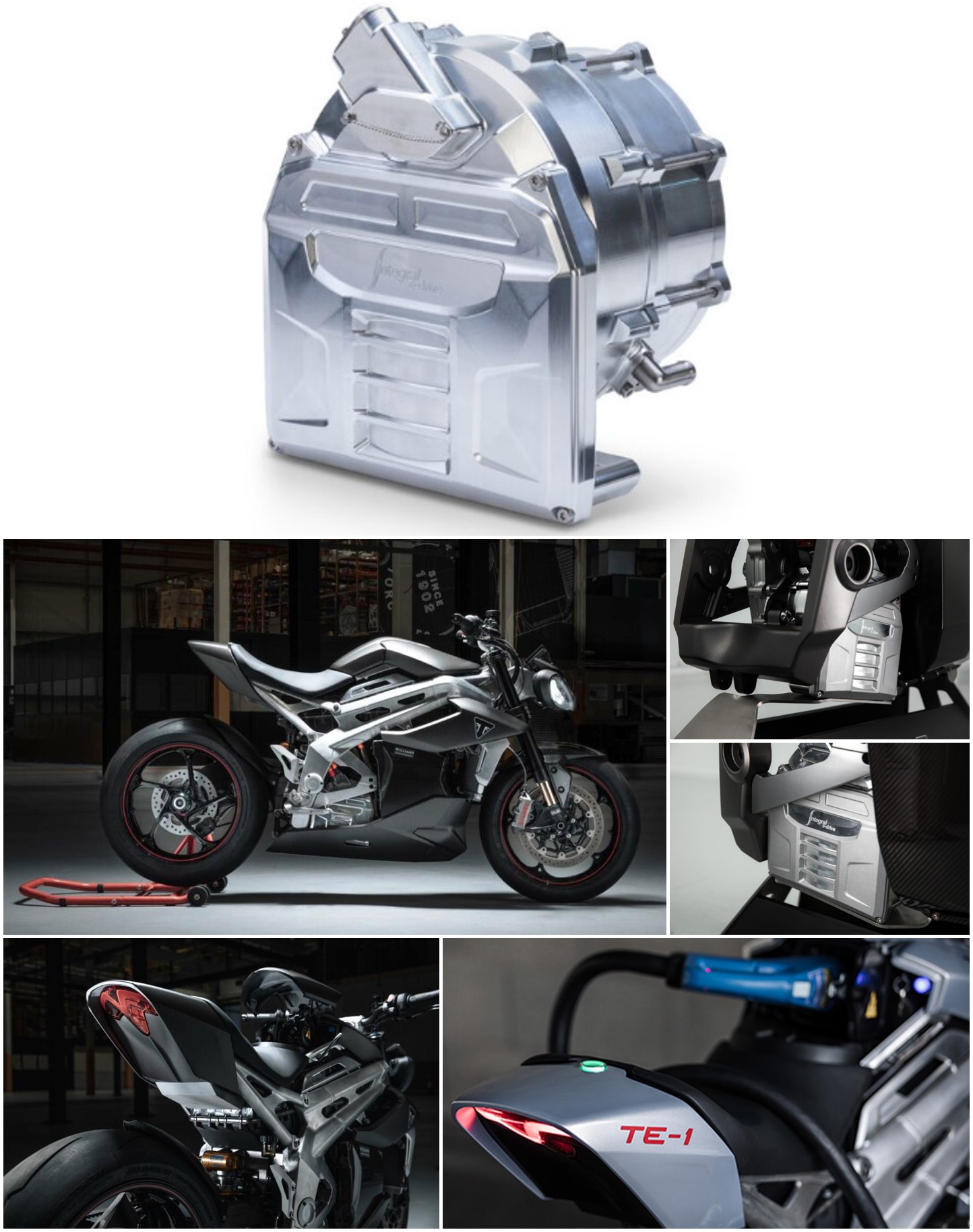
The journey to robust PLM
The success of projects such as the Triumph TE-1 relies on Helix’s ability to innovate at speed. From the start, then, Helix’s mission with the 3DEXPERIENCE platform was to digitalize its engineering management processes and break down hurdles, particularly the siloed workflows and separate line of business tools that stood in the way of letting its design and engineering teams work as efficiently as possible.
“We have a marvelous set of employees, but what’s key is letting them spend their time doing the most important things where they add value,” Cairns said. “The 3DEXPERIENCE platform lets them do that so we can create the most innovative products.”
Helix has been working through a program of PLM improvement projects to take advantage of the rich capabilities on offer within the 3DEXPERIENCE platform. Its roadmap involves digitalizing its engineering management processes, particularly issue and change management, which before was handled by multiple disparate spreadsheets. The company worked closely with its technology partner TECHNIA to configure the 3DEXPERIENCE platform to suit its specific needs and achieve the success it has realized so far.
“The continuous improvements that we’ve made wouldn’t be possible without this close working relationship,” said Nigel Powell, business systems manager at Helix. “TECHNIA delivers all the support we need for the 3DEXPERIENCE platform. They’re innovative in how they help us and flex to suit our needs, including configuring and customizing the platform to deliver the specific functionality we require. So far, it’s given us flexibility and agility in the way we work.”
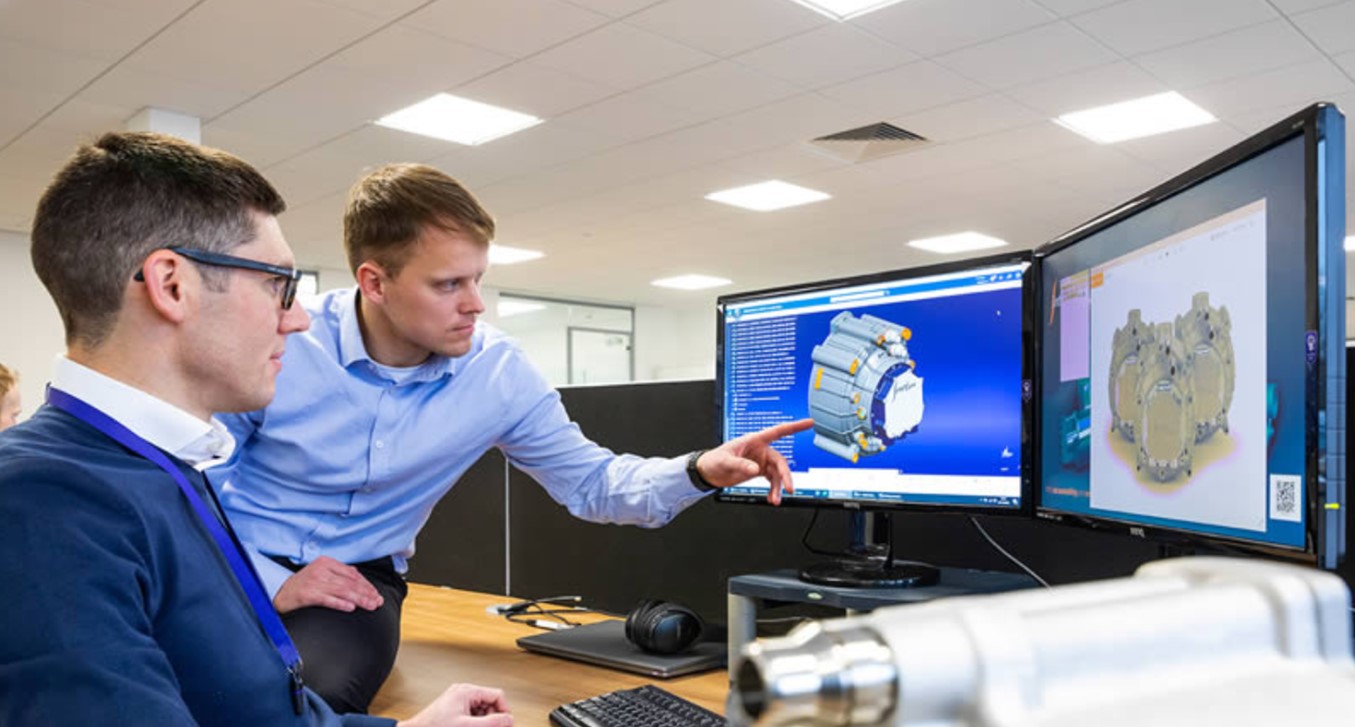
Advanced modeling reduces design cycles
Compact, light and powerful, Helix’s electric motors are known for delivering unrivalled power density.
A long-term user of CATIA, Helix now takes advantage of the latest version of the design software in the 3DEXPERIENCE platform, using it to design all parts, including those with complex manufacturing processes such as additive manufacturing, or that require significant investment for tooling, such as casting or injection molding.
“Whether we’re designing parts to be cast, machined, injection molded or realized by any other manufacturing process, CATIA gives us the toolset to produce high-quality, production ready models and associated technical drawings quickly and efficiently,” Powell explained. “Features such as Wall Thickness Analysis and Draft Analysis help us reduce the number of design cycles and improve the final part quality.”
CATIA’s rich functionality and seamless connectivity to other apps on the 3DEXPERIENCE platform allows Helix’s designers to rapidly progress through the product definition process from initial concept designs to fully detailed production designs.
“The 3DEXPERIENCE is integral to how we create things,” said Steve Walker, principal design engineer at Helix. “It’s at the center of everything we do in terms of design and then following through to production. It has been fundamental to delivering challenging concepts like the Triumph TE-1 as it allows us to get to the prototype motorcycles as fast as possible. We simply wouldn’t be able to operate the way we do without it.”
Helix captures design and engineering experience in the 3DEXPERIENCE platform too, which allows it to carry out knowledge-driven design and use template models to guide new projects.
“It means we can see previously encountered issues and avoid making the same mistakes,” Powell said. “Without the system, you rely on people having the time and inclination to share that information. This way, we have a unified product structure and know we can rely on our master CATIA bill of materials (BOM), which drives all our downstream processes.”
The 3DEXPERIENCE is at the center of everything we do in terms of design and then following through to production.
Change management moves away from spreadsheets
Another key area Helix wanted to improve through the 3DEXPERIENCE platform was change management – a process that was previously burdensome for designers, filled with mouse clicks to release information.
“Not being able to release engineering definitions in a timely manner can have a significant impact on downstream processes,” Powell said. “We needed to move away from spreadsheets.”
Before, the engineering change and BOM release process was disconnected from the CAD and PLM system, which meant that engineering had to manually export a new engineering BOM every time a change was made to the 3D model. This took time but also increased the risk of discrepancies between the engineering and procurement BOM.
“We now manage changes with ENOVIA on the 3DEXPERIENCE platform to release our product BOMs into our existing enterprise resource planning (ERP) system,” Powell explained. “The additional controls enforced by change management workflows, and the direct link between CAD/PLM and ERP, ensures that only released drawings can be purchased.”
Helix also has the capability to review live data from its ERP system in the 3DEXPERIENCE platform to check part/assembly attributes are compatible before a BOM release.
“This has further improved efficiency and BOM quality, and eliminated rework,” Powell said. “Everything is much more controlled and auditable.”
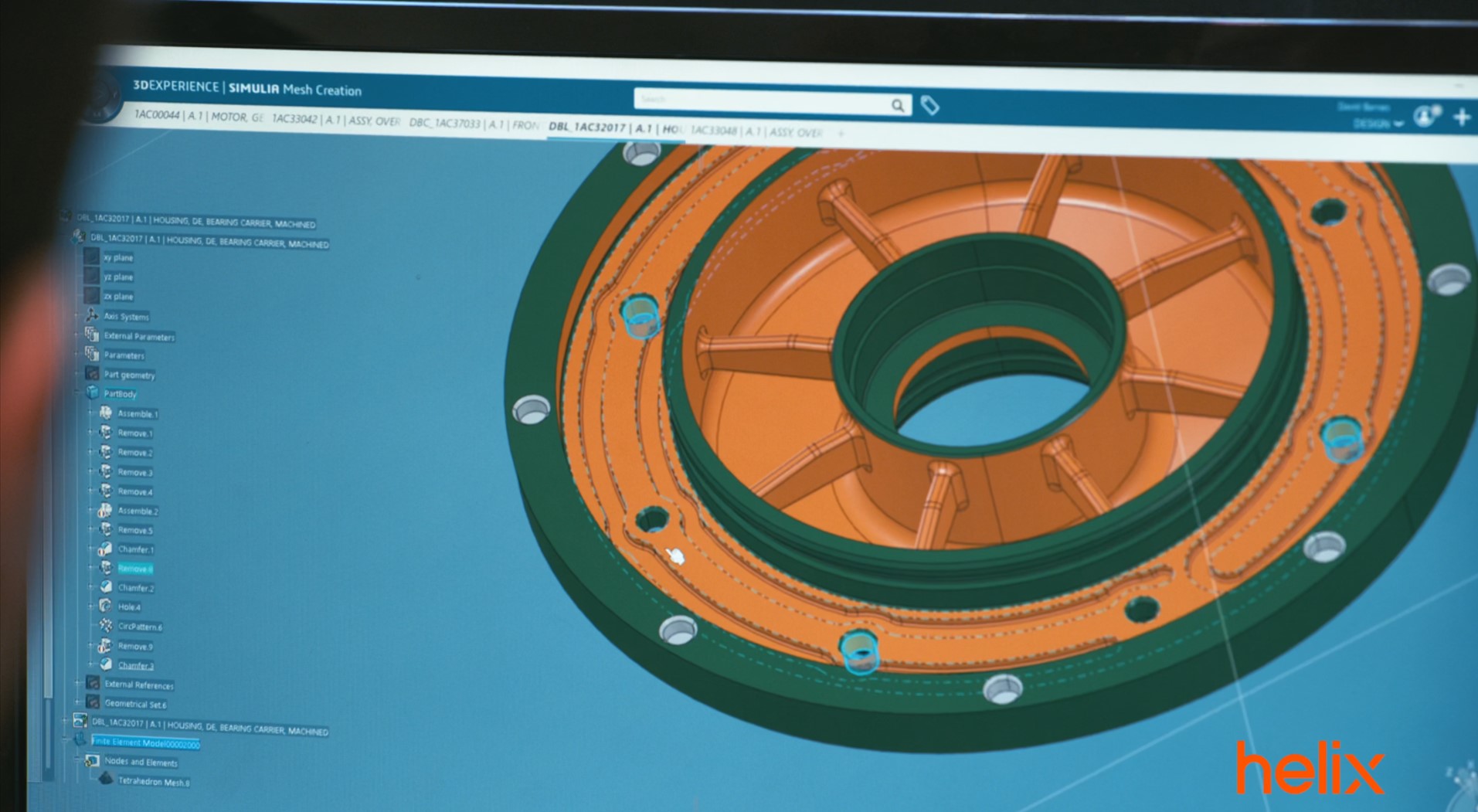
MODSIM keeps quality on track
Unified modelling and simulation are becoming an increasingly essential part of Helix’s workflow. Bringing simulation into the design process earlier on supports Helix’s right first time principle and allows its engineers to get a better understanding of the product they’re working on.
“There are certain things that you can’t obtain through testing alone, or you can’t obtain fast enough through testing,” said Alex Morley, principal analysis engineer at Helix. “Our designers can jump into the finite element analysis simulation apps on the 3DEXPERIENCE quickly, change their designs, run another analysis, and see how it compares to previous analysis and designs. It prevents parts that aren’t fit for service making their way through to the more complex analysis and testing phases, which can be very costly.”
Morley and his team particularly value the ability to carry out multi-step and multi physics simulations in SIMULIA for testing complex load cases on parts and assemblies.
“With multistep simulations we can jump from a static load to a dynamic load, or we can simulate electrical thermal and structural loads at the same time or in the same set of analysis,” Morley said. “We can test several different designs, understand what loads they can survive, how they’ll perform and then we can go on and select the best designs.”
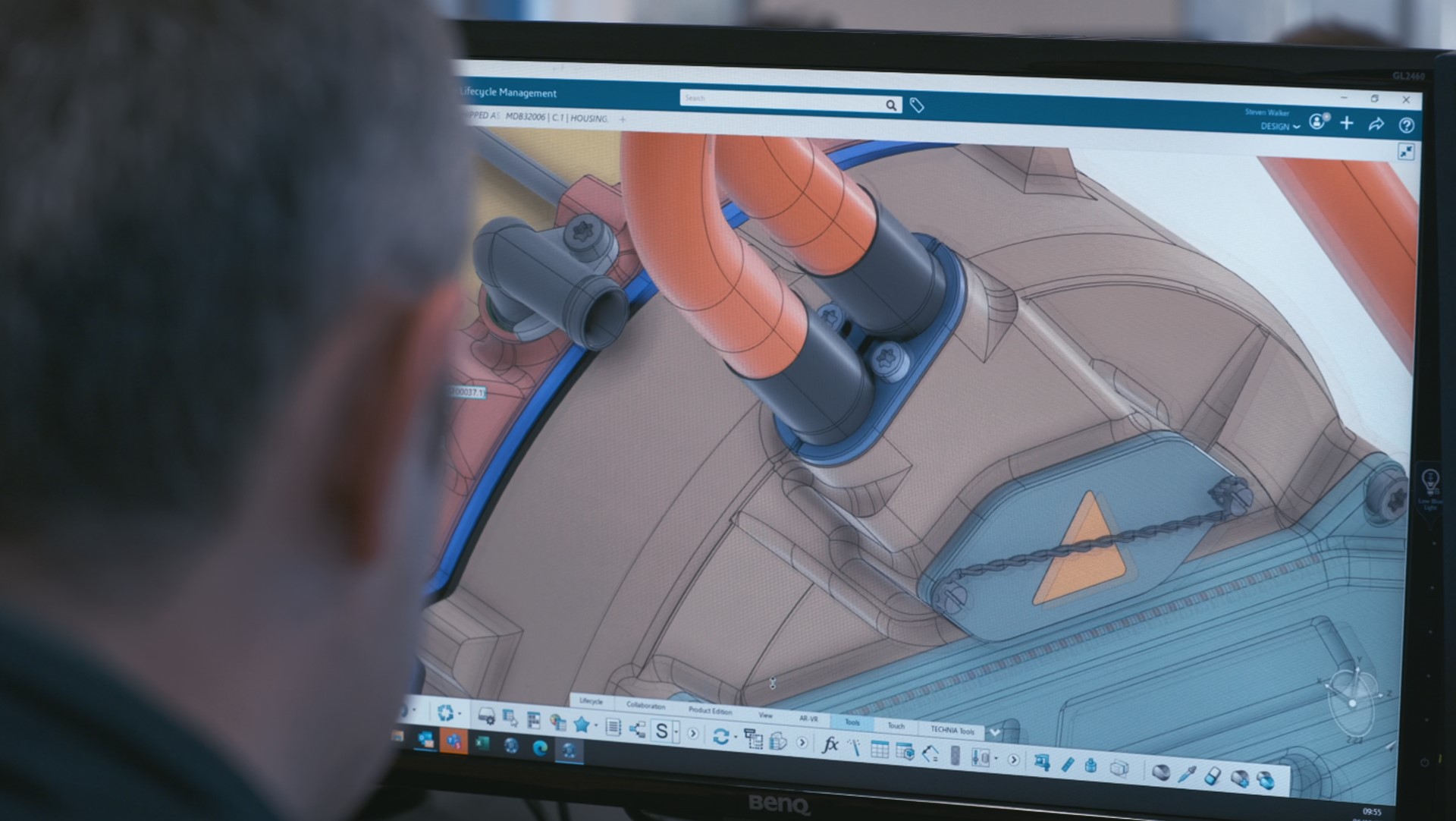
Full visibility down to the shopfloor
All roles involved in the product definition process now work within the 3DEXPERIENCE platform, creating and consuming information digitally.
“The big difference for us is the ability to share design data across the company more easily,” Cairns said. “Before, this data was really only accessible within the design function and if people in other disciplines wanted to access that information, it had to be copied and sent to them.”
Because everyone across the company can securely access the information they need, design changes no longer need to be manually updated and shared, and downstream functions can provide feedback earlier on in the design process.
“For example, our build team can manipulate and interrogate product designs during the concept phase and propose how to assemble them before parts are detailed and released,” Powell said. “This way of working improves our product quality while also increasing efficiency.”
On the shop floor, workers benefit from the ability to view 3D models to ensure production runs as smoothly as possible. Assembly technicians check 3D models and drawings digitally alongside the manufacturing execution system, which provides digital work assembly instructions.
“I think our biggest improvement is that the build team can see all our original models,” Walker said. “It has saved us an awful lot of time because we don’t need to do as many assembly drawings as we used to. The team on the shop floor can work from the same CAD models that we’ve already created.”
Helix and TECHNIA are now extending the 3DEXPERIENCE platform’s out-of-the-box features to transform the project management process, including adding forecasting functionality to see where it’s going across several projects and plan in advance. They’re also looking to set up a supplier portal within the 3DEXPERIENCE platform to improve collaboration with external partners.
“It will allow us to share data with our suppliers,” Cairns said. “They will be able to dive into our company, connect with us and securely access information. It will give us a much more effective way of working with our supply base.”
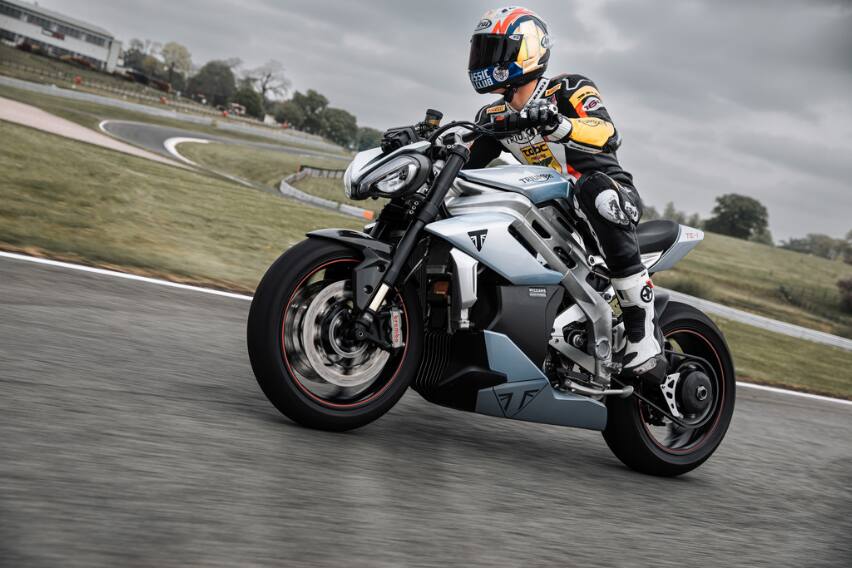
Riding the electrification wave
Demand for Helix’s expertise continues to rise as the wider mobility industry seeks more sustainable modes of transport. The electrification market alone is predicted to increase by at least 25% per annum over the next five years and Helix is ideally placed to capitalize on this growth.
“There’s an insatiable demand for electric powertrains in vehicles,” Cairns said. “Before, the technology was very capable but also very expensive. In the last couple of years, we’ve been working to bring the cost down so our products are more accessible to a wider market.”
With a strong and reliable innovation platform, the company is confident in its ability to deliver the next generation of electric powertrains that its industry customers demand.
“The 3DEXPERIENCE and our partnership with TECHNIA and Dassault Systèmes is now engrained in our business,” Powell said. “We owe our very existence to the overwhelming need for sustainability and, together, we are doing our part to engineer a better world for present and future generations.”
“If you develop great products and invest in them and your people, you will be successful,” Cherrington concluded.
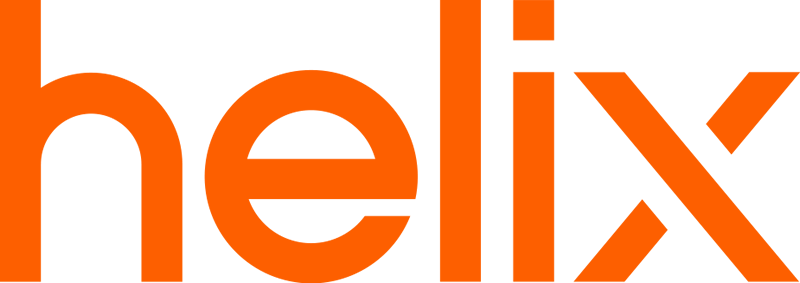
Focus on Helix
Helix (formerly Integral e-Drive) is a full-service supplier of premium electric powertrains. The UK-based company provides access to outstanding performance for makers of electric and hybrid cars, motorcycles and boats, as well as next-gen industrial and aerospace applications, through its proprietary Scalable Core Technology. With over 20 years of experience, Helix combines in-depth powertrain expertise with a proven track record to undertake key design, development and manufacturing projects supporting OEMs and Tier 1 suppliers in delivering exciting sustainable products to market.
For more information: https://ehelix.com
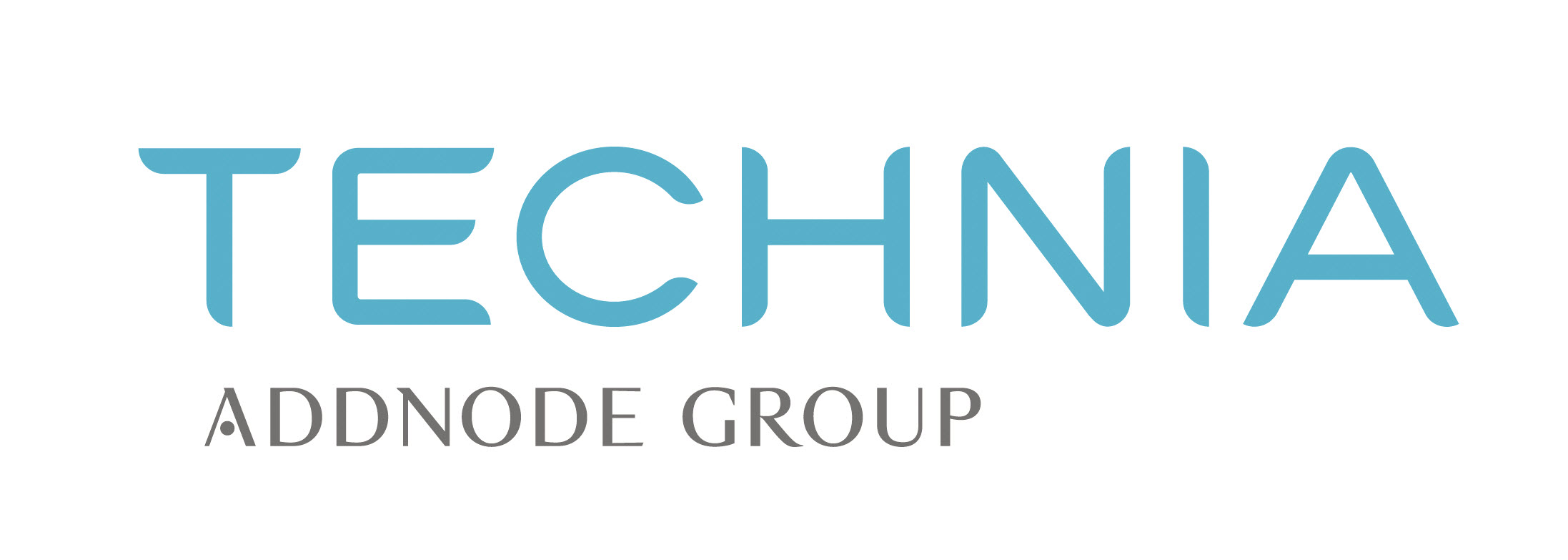
Focus on TECHNIA
At TECHNIA, we pave the way for your innovation, creativity and profitability. We combine industry-leading Product Lifecycle Management tools with specialist knowledge, so you can enjoy the journey from product concept to implementation. Our experience makes it possible to keep things simple, personal and accessible so that together we transform your vision into value. With over 30 years’ experience, more than 6000 Customers worldwide and world-class knowledge in PLM & Intelligent Engineering, we work together as true partner and extension of your team to create an exceptional PLM experience. Our 650 people strong teamwork from 27 locations around the world, across vertical industries, delivering a premium service with a global infrastructure and a local presence. We adopt the latest technology and agile methodologies so, even as technology changes, our relationships last a lifetime.