Estrusione
Scoprite cos'è il processo produttivo di formatura dell'estrusione e il suo utilizzo nell'industria.
Introduzione all'estrusione
Il processo di estrusione consente di creare oggetti con profili trasversali fissi spingendo un materiale, generalmente metalli, polimeri, ceramiche, calcestruzzo, argilla da modellazione e alimenti, attraverso una matrice della sezione trasversale desiderata. Questa procedura è vantaggiosa per la creazione di sezioni trasversali molto complesse e per i materiali fragili, poiché il materiale è esposto solo a sollecitazioni di compressione e di taglio. Un vantaggio fondamentale è l'eccellente finitura superficiale. Un altro è la maggiore resistenza degli oggetti metallici prodotti con l'estrusione.
Esistono due tipi di estrusione: continua o semicontinua. L'estrusione continua prevede la produzione di un materiale di lunghezza indefinita; quella semicontinua prevede la produzione di molti pezzi. Il materiale può essere caldo o freddo. Estrusi è il termine che indica gli oggetti prodotti con l'estrusione.
Nel 1797, l'inventore inglese Joseph Bramah brevettò il primo processo di estrusione per la produzione di tubi da metalli morbidi. Il metallo veniva preriscaldato e forzato attraverso una matrice mediante uno stantuffo azionato a mano. Più tardi, nel 1820, Thomas Burr implementò questo processo con un tubo di piombo e una pressa idraulica chiamata "squirting". Nel 1894 Alexander Dick estese il processo di estrusione alle leghe di rame e ottone.
Il processo di estrusione presenta anche alcuni inconvenienti. Tra questi vi sono le cricche superficiali e interne, le linee superficiali e il "tubo", ovvero un modello di flusso che attira gli ossidi superficiali e le impurità verso il centro del prodotto.
Cinque processi di estrusione
I cinque diversi processi di estrusione sono:
- L'estrusione a caldo viene eseguita al di sopra della temperatura di ricristallizzazione di un materiale per evitare che il materiale si indurisca e per facilitare la spinta del materiale attraverso la matrice.
- L'estrusione a freddo viene eseguita al di sopra della temperatura ambiente, ma al di sotto della temperatura di ricristallizzazione del materiale. La temperatura può variare da 800 °F a 1800 °F (da 424 °C a 975 °C). L'uso comune è quello di bilanciare le forze richieste, la duttilità e le proprietà finali dell'estrusione.
- L'estrusione a bassa viene eseguita a temperatura ambiente o quasi. I vantaggi principali dell'estrusione a freddo sono l'assenza di ossidazione, la maggiore resistenza dovuta alla lavorazione a freddo, le tolleranze più strette, la migliore finitura superficiale e la velocità di estrusione, se il materiale è soggetto a cortocircuito a caldo.
- Il Welding Institute del Regno Unito ha inventato l'estrusione per attrito e l'ha brevettata nel 1991. Inizialmente, l'uso era quello di produrre microstrutture e distribuzioni di particelle omogenee nei materiali compositi a matrice metallica. L'estrusione per attrito differisce dall'estrusione convenzionale in quanto la carica (billetta o altri precursori) ruota attorno alla matrice di estrusione. Viene applicata una forza di estrusione per spingere la carica contro la matrice. In pratica, sia la matrice che la carica possono ruotare o controruotare.
- La microestrusione è un processo di estrusione a microfilm eseguito a livello submillimetrico. Come per l'estrusione, il metallo viene spinto attraverso l'apertura di una matrice, ma la sezione trasversale del prodotto risultante può rientrare in un quadrato di 1 mm.
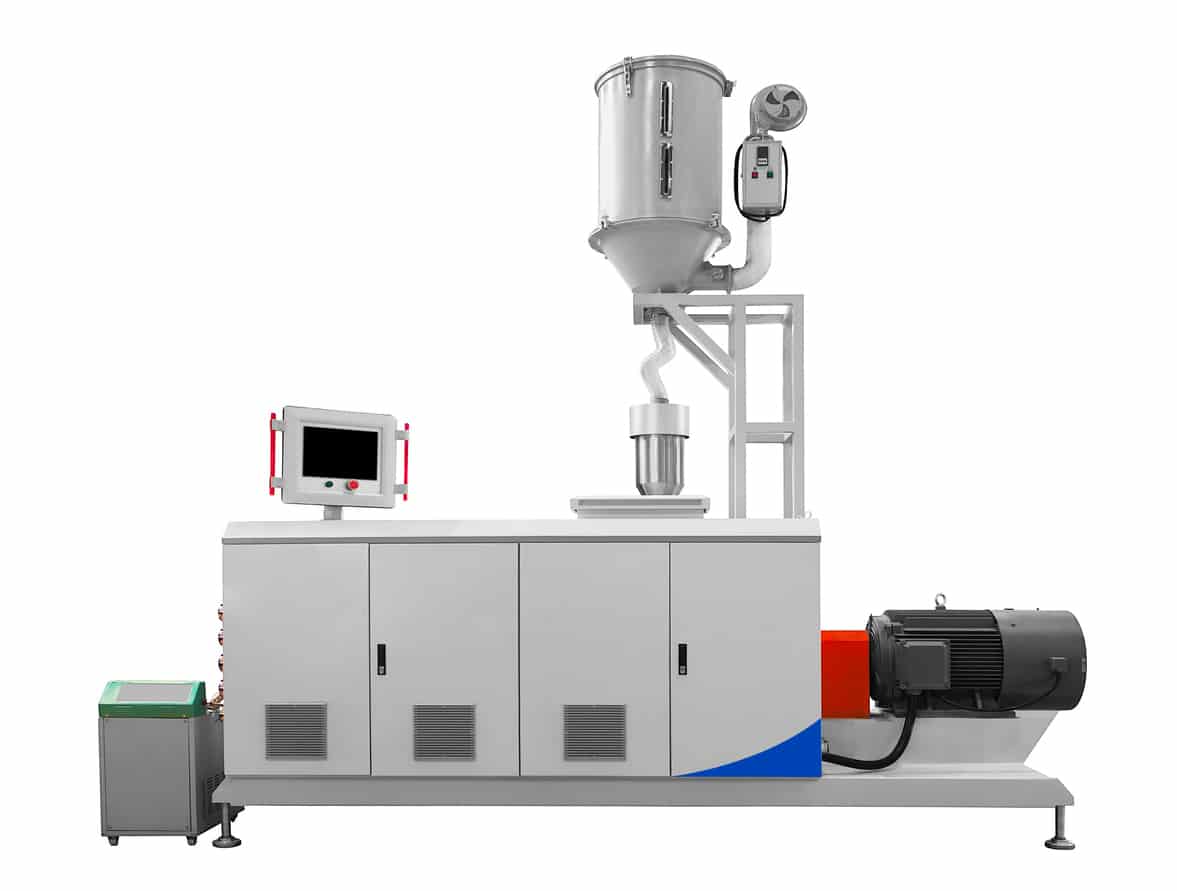
Ricevi più preventivi per le tue parti in pochi secondi
Ottenete più preventivi per i vostri pezzi in pochi secondi