Latecoere
Latecoere leverages DELMIA Augmented Experience to enhance aerostructures' quality inspection and drive zero-defect manufacturing.
(Photo © Arnaud Spani)
With DELMIA Augmented Experience we are reducing inspection time by 20% to 30% and it makes our inspection methods more reliable.
Boosting quality inspection with augmented reality
In aerospace, zero-defect manufacturing isn’t just an aspiration – it’s essential. Every flight, whether carrying passengers or freight, depends on the precise assembly of thousands of components. Even the tiniest error, such as a single misplaced bracket or undetected flaw, can disrupt operations further down the final assembly line.
“The major risk related to a quality defect is the potential for delays in the assembly line to fix the problem, and ultimately, a loss of customer trust,” said Grégory Marrocco, aerostructures industrial system digitalization manager at Latecoere, a France-based Tier 1 supplier of aerostructures and interconnection systems to major aerospace companies. “We must ensure that what we install is compliant and meets our clients’ standards and requirements.”
For every fuselage, support structure and bracket, Latecoere’s commitment to quality is uncompromising. To ensure flawless execution across global operations, the company deploys best-of-breed solutions to prevent errors.
Latecoere’s technology of choice is DELMIA Augmented Experience from Dassault Systèmes – a solution that provides digital instructions through augmented reality (AR) technology, helping shop floor operators with inspection tasks.
Turning complexity into clarity
Latecoere has been at the forefront of aerospace innovation for over 100 years. Today, the company operates through three main divisions: Aerostructures, which is responsible for the structural components of aircraft; Interconnection Systems, which covers wiring, avionics and onboard systems; and Services and Special Products, which is dedicated to aftermarket, customer support and video systems.
“What sets Latecoere apart is its ability to deliver complete products by integrating the expertise of all three divisions,” Marrocco said. “We’re not just an equipment manufacturer; we design and build the structures, equip them via our interconnection systems division and then support the products through our services arm.”
At its Toulouse plant, Latecoere currently assembles several aircraft fuselages every month, including those used in both passenger and freight services. Each fuselage is made up of seven sections and requires the precise installation of around 500 structural brackets. The quality control of these supports to ensure they are placed correctly and have zero defects is carried out manually – and this can be incredibly time intensive.
“The inspection time for a complete aircraft is measured in tens of hours, reflecting the scale and complexity of the task,” said Florent Lahaye, Latecoere’s program quality manager. “I have three full time operators to control these aircraft fuselages per month. They must control each of the 500 brackets that a structure can have.”
The process also involves a lot of paper documentation. Every time an inspection is carried out, a production order is used to track all assembly and inspection steps up to the final check. For each step, there are instruction sheets for both operators and quality inspectors, typically in Word or Excel format. These documents might include checklists that refer to annotated layouts or forms used to record values. This information is currently printed and attached to the paper production order. Latecoere sought a solution that could help it reduce the manual nature of these inspections and, in turn, create a more accurate and efficient process.
“We needed a robust digital solution – one that was easy to implement and simple to use – that could help us eliminate paper, make inspections more reliable and support our zero-defect mission,” Marrocco said. “DELMIA Augmented Experience perfectly met our needs. And since we already used the Dassault Systèmes’ 3DEXPERIENCE platform, including CATIA for the design and customization of fuselages, we knew it would be straightforward to implement.”
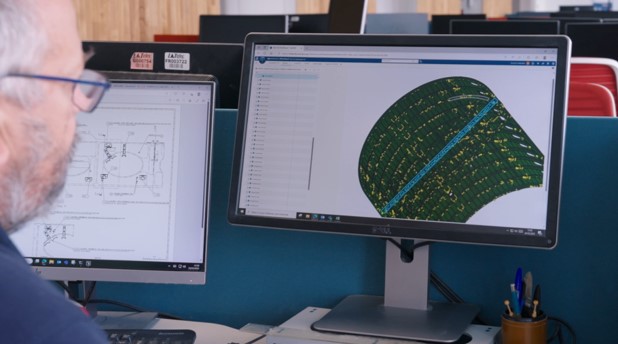
Enhancing inspection accuracy and traceability
After proving its value at its Gimont site in France, Latecoere rolled out the AR-enabled inspection process to its facility in Plovdiv, Bulgaria, which adopted the technology from the outset – nearly three years ago. Today, it is reliably used across all aircraft lines in Bulgaria. The company is now expanding the process for its Toulouse site, starting with initial user training and procedure development provided by the DELMIA Augmented Experience team.
Having received fuselage specifications from the client, Latecoere’s design office creates the 3D model of a fuselage with CATIA on the 3DEXPERIENCE platform, which is then used by the technicians to generate inspection plans. The data from these plans includes the correct positioning of each element composing a configuration. The plan is made available to the inspector on the DELMIA Augmented Experience application which overlays this plan to the real airframe and identifies any deviation.
“In Bulgaria’s open fuselage environment, we use a camera on a mobile workstation,” Marrocco said. “In Toulouse, we have a confined fuselage. So instead, we’re using tablets with AR to film the product and superimpose digital elements – checking for correct orientation, position and alignment. So, it’s the same solution, adapted to different contexts. This flexibility opens possibilities for other applications, such as the production of aircraft doors – a specialist area for Latecoere.”
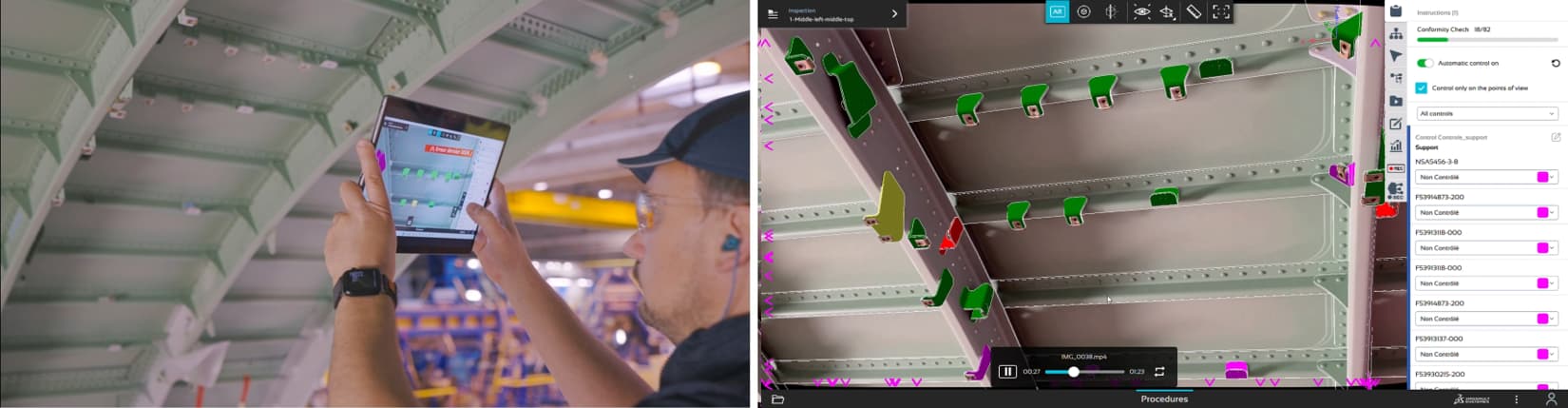
In this scenario, data indicating where the brackets should be positioned is uploaded to a tablet. The operator uses the tablet’s camera to visualize a section of the fuselage, while DELMIA Augmented Experience automatically superimposes the virtual part placement onto the live camera view.
Thanks to algorithms leveraging artificial intelligence (AI) and computer vision, the inspection process is performed automatically as the system analyzes the live feed in real time. The operator simply follows the AR guidance to ensure all control points are scanned. If needed, the operator can also manually add annotations, comments, or additional information on specific points.
“The screen displays different colors to indicate whether a part is correctly positioned, misaligned or missing,” Lahaye said. “The solution then automatically generates a report that can be used by the shop floor for compliance checks.”
When a bracket or part is confirmed as correctly installed, the system can automatically capture a screenshot. If there’s a defect, that’s captured too. This information is precisely referenced in the 3D model, images from which go into a PDF inspection report, which becomes part of the product’s delivery file. This process not only supports traceability but also provides customer trust.
“It’s about accountability,” Marrocco said. “When there’s a discussion between us and the customer, we can show proof that a part was installed properly and without damage.”
This saves time for the inspector, as it automatically populates a database. It helps analyze the number of defects that can occur per aircraft and helps implement associated action plans.
“Based on our return of experience from the Bulgarian site, we consider that we can achieve a 20% time saving during the inspection phase,” Marrocco said. “So, we're gaining in efficiency, productivity and also maturity in our product quality.”
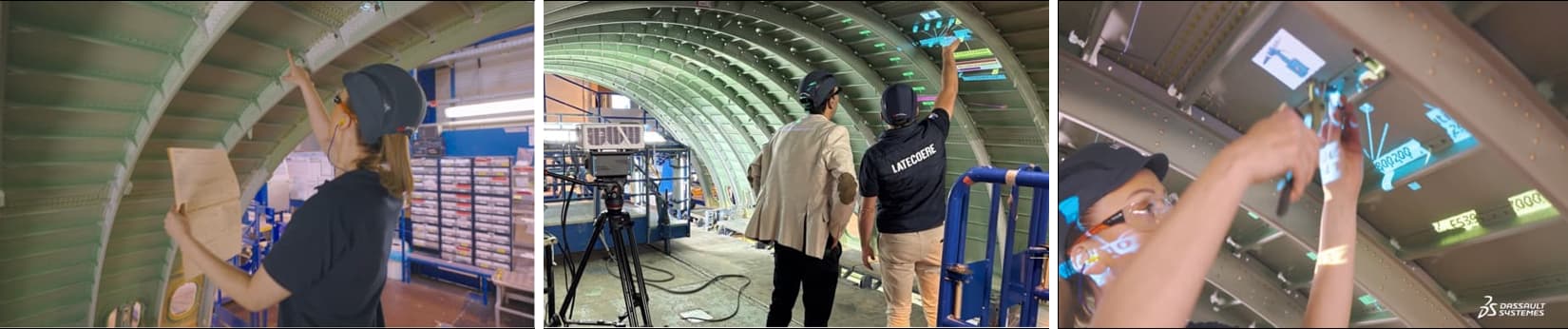
Leveraging digital projection to improve assembly instructions
This is only the beginning. In Toulouse, Latecoere aims to expand the use of DELMIA Augmented Experience beyond inspection, to also support assembly operations. Its vision involves projecting assembly instructions directly onto the product by using a camera positioned on a tripod: visualizing 3D parts, tools required, drilling diameters, rivet types, applicable standards – even tutorial videos. The camera then projects the virtual images of the parts directly on the fuselage so that the operator can check where to position them correctly.
“This would replace cumbersome paper instructions, especially in areas where reading while working is not practical,” Marrocco said. “Right now, our manufacturing guides are 30 pages long and hard to read. Moving toward video projection will limit the risk of misunderstanding when reading a 2D layout.”
“It currently takes hours to install the 500 supports on an aircraft fuselage, and this could be significantly reduced. The benefit of DELMIA Augmented Experience is that it makes our inspection method more reliable,” Lahaye added.
The use of AR will also enable faster on boarding of new employees. This could be a gamechanger for Latecoere, substantially improving current processes. Ultimately, this is a huge opportunity for Latecoere to modernize its operations.
“In the future, the operators will have everything they need, visually and in real time, overlaid directly on the product,” Marrocco concluded. “This will improve efficiency and comfort, and make work more engaging too.”
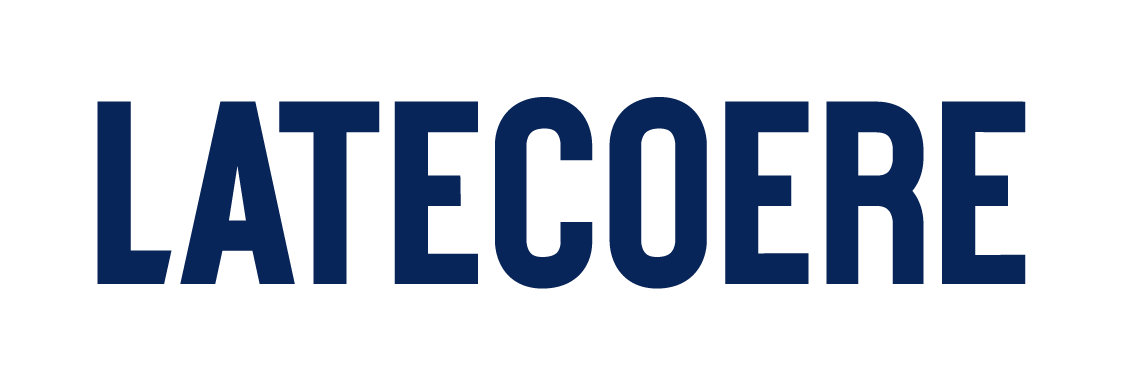
Focus on Latecoere
A leader in the field of aerostructures and interconnection systems, Latecoere works closely with major aircraft manufacturers and airlines, from design through to production and maintenance of its products. Operating for over 100 years, the company consistently invests in research and new technology to develop cutting-edge solutions that are increasingly tailored to custom requirements
For more information: https://latecoere.aero/en/