Hallberg-Rassy
Swedish yacht manufacturer Hallberg-Rassy has implemented the 3DEXPERIENCE platform on the cloud to deliver its world-renowned sailing yachts on time and meet its customers' expectations. By choosing the Sea Boat Builder industry solution experience, the company now has a single environment where all designers can collaborate on a virtual twin.
I’d go as far as to say we are working 50% faster with the virtual twin as we don’t have to create a physical mock-up. It also means our approach is more sustainable since we are not wasting materials.
Designing blue water sailing yachts
Obsessed with sailing from the age of four, it’s no wonder that Magnus Rassy would become CEO of one of the world’s most highly respected yacht manufacturers. “Each new Hallberg-Rassy model is a step forward,” Rassy said. “Our latest yacht – the 69 – is the greatest Hallberg-Rassy ever. Any successful business builds on giving customers what they want. Our customers want comfort and more space. And the 69 delivers on that.”
Hallberg-Rassy yachts are known far and wide for their sturdy construction, superb craftsmanship and easy handling – enabling effortless, long-distance sailing. Since 1987, Hallberg-Rassy has worked with Frers Naval Architecture and Engineering in Argentina, one of the most talented yacht designers of our time, to give each yacht its unique grace. The details are then designed in house by Hallberg-Rassy in cooperation with Frers.
“You can spot a Hallberg-Rassy, even from a distance and regardless of whether it’s a new design or several decades old," Rassy said. "Thanks to the blue stripe around the hull and the windscreen, Hallberg-Rassy sailing yachts are instantly recognizable. The brand has a special charisma. We are careful to keep a magic balance between the long history of tradition we are famous for and contemporary features. There should never be too much of either.”
This balance is most definitely achieved in the Hallberg-Rassy 69. The deck is flushed forward of the mast, and the large interior benefits from an unusual amount of natural light, giving the crew full contact with the outside world. Like all Hallberg-Rassy yachts, the 69 also includes PushButtonSailing, which means that the sail can be set or the anchor can be lowered with a push of a button.
Hallberg-Rassy’s designs are not just unique, they are incredibly personal. “Our desire is to create yachts that are both well-built and comfortable, but also still nice and quick to sail,” he said. “There are a lot of interesting developments in racing that we can adapt in cruising. For example, the 69’s hull shape philosophy is inspired by racing. Nobody would think it would be good for cruising, but the reality is that you get more living space, more storage and a better sailing performance all at the same time.”
Hallberg-Rassy’s small design team remains incredibly close to its products to this day. Most of the engineering and manufacturing processes – including the lamination, woodwork and all the technical installations – take place in-house in Sweden, and a huge amount of work is still done by hand – just as it has been for over 50 years.
What is different, however, is how the company uses technology to ensure that it can eliminate waste, verify its designs and ensure that its sailing yachts are built right the first time – with no need for physical prototypes.
“We use the 3DEXPERIENCE platform to look at the yacht before we actually build it,” Rassy said. “We can test different looks and different proportions, and we can build many different prototypes in the digital world. Once we start to build the real yacht, it’s not a prototype, it’s hull number one in the serial production. That’s really good.”
Building on success
Hallberg-Rassy’s relationship with Dassault Systèmes goes back many years. In 2005, the company replaced various CAD tools with CATIA V5 for Yachting. While this served the company well for almost two decades, Hallberg-Rassy wanted to modernize its technology environment by moving to the cloud.
“We wanted to get rid of our servers and reduce the cost of our in-house technology environment,” said Eric Segerlind, Hallberg-Rassy’s head of in-house design and development. “When we heard about Dassault Systèmes’ 3DEXPERIENCE platform on the cloud, it seemed like an obvious move for us. It provides us with the most modern iteration of the tools we were already using, but without the burden of maintaining our own infrastructure. In addition, the cloud enables us to securely work from anywhere.”
Hallberg-Rassy turned to local Dassault Systèmes business partner PLM Group for help with the implementation. “The PLM Group team made everything easy for us,” Segerlind said. “They took the time to understand and deliver on our requirements exactly. They’ve helped us with the cloud installation and provided ongoing training and support. We regularly attend the education days that the PLM Group hosts – they are incredibly useful.”
The Hallberg-Rassy team was up and running on the 3DEXPERIENCE platform in a matter of weeks – and quickly reaped the rewards. “The platform is so intuitive,” Segerlind said. “Within a week, I was using it to model complex surfaces.
“We also saw the benefits of the cloud straight away. When we were hosting our infrastructure, we had to connect to our servers to work from home. It was a clunky process. Today, because everything is in the cloud, we can work wherever we like – always safe in the knowledge that we are accessing the latest designs. With the click of a few buttons, I can bring up the design of a yacht in its entirety. This has reduced the planning I need to do before meetings – I pick up my laptop and go.”
While individual team members have the freedom to work from any location, internal collaboration has gotten better. “That’s because we are all working in the same virtual environment,” Segerlind said. “We can work collectively to solve issues.”
By working with a virtual twin on the 3DEXPERIENCE platform, the team can run simulations and calculations for the design of the interior and exterior of the yacht. This has allowed Hallberg-Rassy to work 50% faster and more sustainably, as there is no longer any reason to use a physical model and therefore no material is wasted.
Modern design meets traditional craftsmanship
The design process has also improved. Instead of using three or four different solutions – one for each part of the process – the 3DEXPERIENCE platform enables Hallberg-Rassy’s designers to carry out the entire development of their yachts in a single environment.
“When I started with the platform, I realized just how easy it was to change between different apps and functions,” said Patrik Wikström, an in-house engineer at Hallberg-Rassy. “The switch is seamless – in just a click of the mouse, you can change from parts to surfaces, to drawings, to simulations.”
Because modeling and simulation (MODSIM), once totally separate entities, have been brought together into a unified design approach within the platform, verification and validation of the yacht happens dynamically.
At the earliest stage of the development process, designers can explore ideas and experiment with different weights, loads, surfaces and dimensions to find the optimal combination of parts. They can then adapt the geometry later.
“In the beginning, I tend to use the Surface app to sketch out my ideas,” said Wikström. “I’ll then change to a different app, such as Sheet Metal Design, to produce the detail. At this point, I’ll share my ideas with Eric, who will then make a frame analysis and run simulations to verify the design of the various parts. For example, he’ll be able to work out the flex of a particular part and whether it will withstand operation at sea. He may suggest we make a part bigger or stronger, depending on these simulations.”
“I create big shapes, such as the hull deck structure, using surface modeling,” said Segerlind. “The more involved stainless-steel parts and the wooden interior are done with solid modeling. I can run calculations directly in the 3DEXPERIENCE platform, which saves a huge amount of time – in the past I’d have to export the design to a different program, run the calculations and then take the design back. It’s much quicker and easier now.”
We have already delivered almost 10,000 yachts. Every single one of those has been on time. We have never been late on any delivery. We can only keep this record if we maintain full control over production – and that means keeping all processes close. That’s what the 3DEXPERIENCE platform enables for us.
A streamlined approach to design to production
Once Segerlind and his colleagues develop the functional parts, they combine them into a fully assembled 3D virtual twin of the sailing yachts. “The virtual twin helps us make the right product development decisions,” Segerlind said.
For example, when the Hallberg-Rassy team had to engineer a way to fold out the bathing platform on one of its yachts without hydraulics or electricity, it used the 3DEXPERIENCE platform to work out a practical approach. “If we were doing this in the real world, we would have to produce steel parts which would have to be welded, taken apart, modified and then re-welded,” said Wikström. “By being able to change the shape and function of the various parts in the digital world, we save a lot of time and costs.”
The virtual twin can also be shared with suppliers, customers and other key stakeholders. “We can easily put virtual people into the model too,” Segerlind said. “This helps stakeholders to visualize the scale of various features, and also to help us understand whether it is possible to reach certain installations.”
If a customer requests a specific setup or configuration, the Hallberg-Rassy team can quickly adapt existing designs instead of starting from scratch. This saves further time and effort. “If a customer requests that we change one of the surfaces, for example, we can easily adapt the model,” Segerlind said. “We now have the full design data for yachts in the platform – this is all knowledge that we can re-use in future projects.”
Because this approach sees customer feedback applied to the model long before manufacturing begins, time, waste and costs are reduced. “I’d go as far as to say we are working 50% faster with the virtual twin as we don’t have to create a physical mock-up,” Segerlind said. “It also means our approach is more sustainable since we are not wasting materials.”
Once any issues are ironed out virtually, Hallberg-Rassy jumps straight to production. The CATIA design files are sent directly to Hallberg-Rassy’s state-of-the-art CNC machines to precision cut parts. “Using the 3DEXPERIENCE platform means our 3D design is accurate right from the start,” said Wikström. “This means that the various parts will be made to precise measurements and, when it comes to production, they will fit together perfectly.”
Hallberg-Rassy 69
Perfection the future
Hallberg-Rassy will also continue to unlock the full capabilities of the Dassault Systèmes solution in the months and years to come. “We are starting to explore new features of the 3DEXPERIENCE platform, including the Piping and HVAC Engineering solution, so that we can better plan the routing ways to keep the yacht as solid as it should be, without damaging or impacting the overall structure of the yacht,” Segerlind said.
“In a yacht, the supply system is very large, so the piping needs more space than you think,” added Wikström. “The piping solution will help us make the best use of space.”
The company will also continue using the platform to test new ideas virtually. “The biggest challenge we face is making the right decisions for the products,” Segerlind said. “Our products have a long lifespan: we have models that we have been building up to 16 years. The 3DEXPERIENCE platform helps us decide which features are optimal for investment.”
Ultimately, Rassy is excited to see how Hallberg-Rassy can build on its success. “We have already delivered almost 10,000 sailing yachts,” he said. “Every single one of those has been on time. We have never been late on any delivery. We can only keep this record if we maintain full control over production – and that means keeping all processes close. That’s what the 3DEXPERIENCE platform enables for us.”
Using the 3DEXPERIENCE platform means our 3D design is accurate right from the start. This means that the various parts will be made to precise measurements and, when it comes to production, they will fit together perfectly.
Discover more about the Sea Boat Builder industry solution experience.
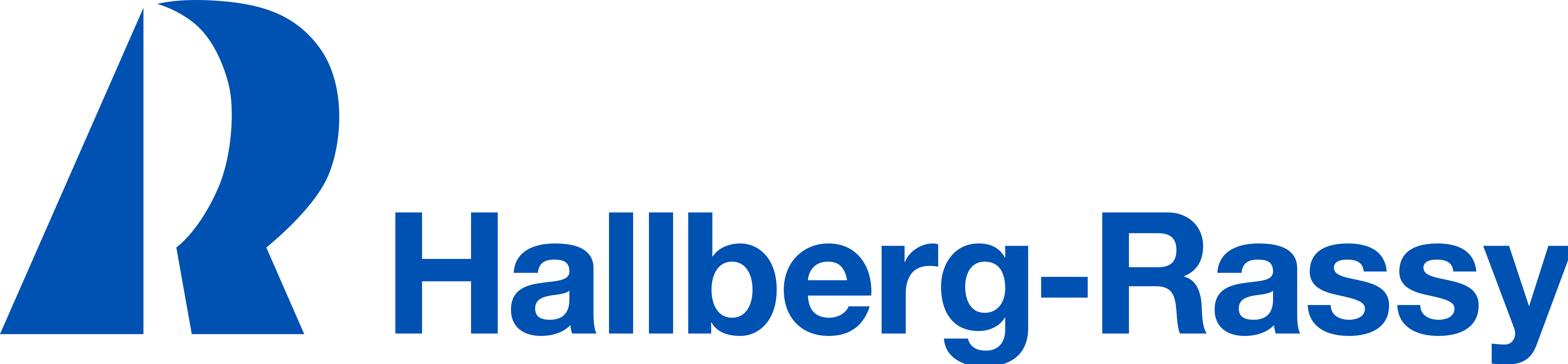
Focus on Hallberg-Rassy
Established in 1943, the Hallberg-Rassy group of companies remain 100% owned by the Rassy family. Today 9,700 Hallberg-Rassy yachts are delivered all over the world. The company has stayed true to the concept of sturdy craft, well protected cockpits, high endurance and good sailing qualities with a high degree of comfort. The yachts are easy to handle by a small crew, offering effortless and comfortable sailing.
For more information: https://hallberg-rassy.com/
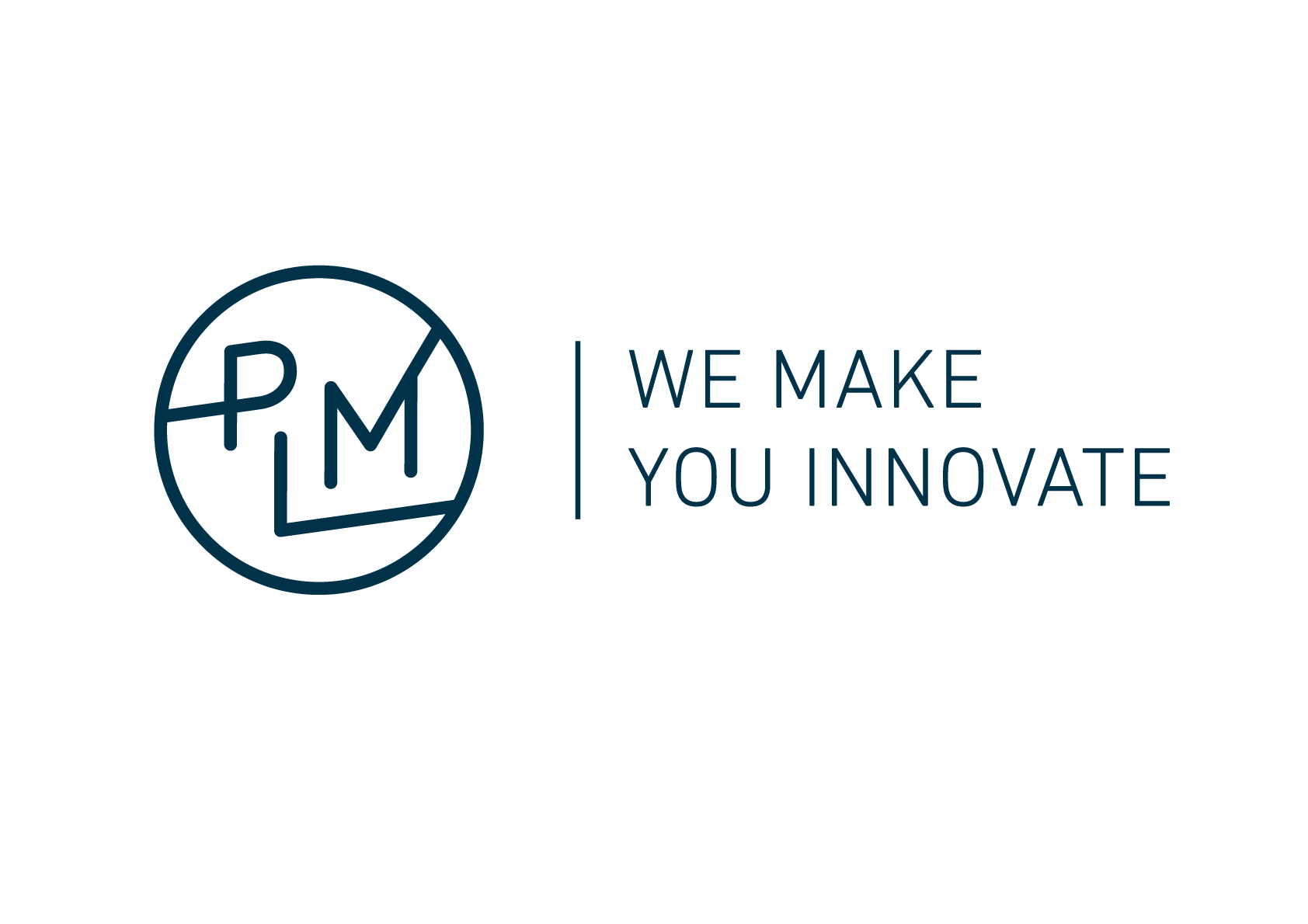
Focus on PLM Group
PLM Group has been collaborating with Dassault Systèmes for over 25 years as a value-adding partner. The company's expertise in 3DEXPERIENCE is helping companies connect people, processes, and ideas enabling them to pioneer the future and gain a competitive advantage in the market. PLM Group helps its customers transform their value chain by adding the latest technology including augmented reality, virtual testing, and generative design for a future-proof business.
For more information: https://plmgroup.eu