Chropyňská Group
Czech supplier of welding, assembly and transport equipment for the automotive industry, Chropyňská Group, adopted the 3DEXPERIENCE platform including the Digital Equipment Continuity Industry Solution Experience. The company expects this to provide a consistent source of data that will increase agility, facilitate planning and purchasing, and ultimately lead to a competitive advantage.
Delivering state-of-the-art robotic lines for the automotive industry
In 1913, Henry Ford’s adoption of assembly lines transformed the time it took to roll out a car from its factory from over 12 hours, to one hour and 33 minutes. Today, however, the innovative use of robotic assembly lines is enabling OEMs to deliver a car from their assembly line every 60 seconds.
This is all thanks to the efforts of companies like Chropyňská Group. Established in the Czech Republic in 1992, the company supplies welding, assembly and transport lines to major automotive companies including Audi, BMW, Opel, Porsche, Škoda and Volkswagen.
The process of building an assembly line begins with a 3D model of the body of a car, which Chropyňská Group receives from the automaker. A team of experts then develops a customized line that can assemble the various metal parts – a mammoth task when you consider that the average car has around four thousand welding points.
The process of optimizing the layout of the assembly line, selecting the appropriate components, integrating automation technology, testing the line and then delivering the final setup takes around eight months. Sourcing the various robots and other equipment can eat up much of this time, since only 15% of the components are manufactured by Chropyňská Group itself – the rest are purchased or manufactured to bespoke requirements from specialist suppliers across the globe.
We operate a complex business, comprising many distributed teams and third parties. Thanks to the 3DEXPERIENCE platform, we will now be able to operate collaboratively as one. We will be more efficient, have a more standardized way of working and will be able to plan far more effectively. This will pave the way for a more successful future.
Challenge
Over the past few years, Chropyňská Group has grown its business significantly, mainly through the acquisition of eight facilities in locations including Germany, India, Poland, Romania, and Slovakia.
Associates from all these sites are bidding for new business. However, without standardized processes and procedures in place, there was no consistency – in fact, the different teams sometimes found themselves bidding for the same job.
Without a unified engineering bill of materials (eBOM), the disconnected teams struggled to manage the various OEMs’ different naming conventions for components, including the robots. This led to problems in the design, production and assembly of the lines, not least because 50-70% of these processes are outsourced.
In fact, inconsistencies in data lead to ambiguity and duplication of effort by design, production and assembly teams, all of which had a direct impact on cost. The company found it was regularly facing additional charges from suppliers because it had to place urgent, last-minute orders to fulfil unforeseen production needs.
Chropyňská Group realized it needed a standardized, connected system that could give it access to accurate information, and a centralized eBOM. This would also facilitate a consistent way of working across all sites. It wanted to optimize its contracting and procurement process using enterprise resource planning (ERP) and product lifecycle management (PLM) so that it could ultimately become the best supplier for large-scale turnkey robotic lines in Europe.
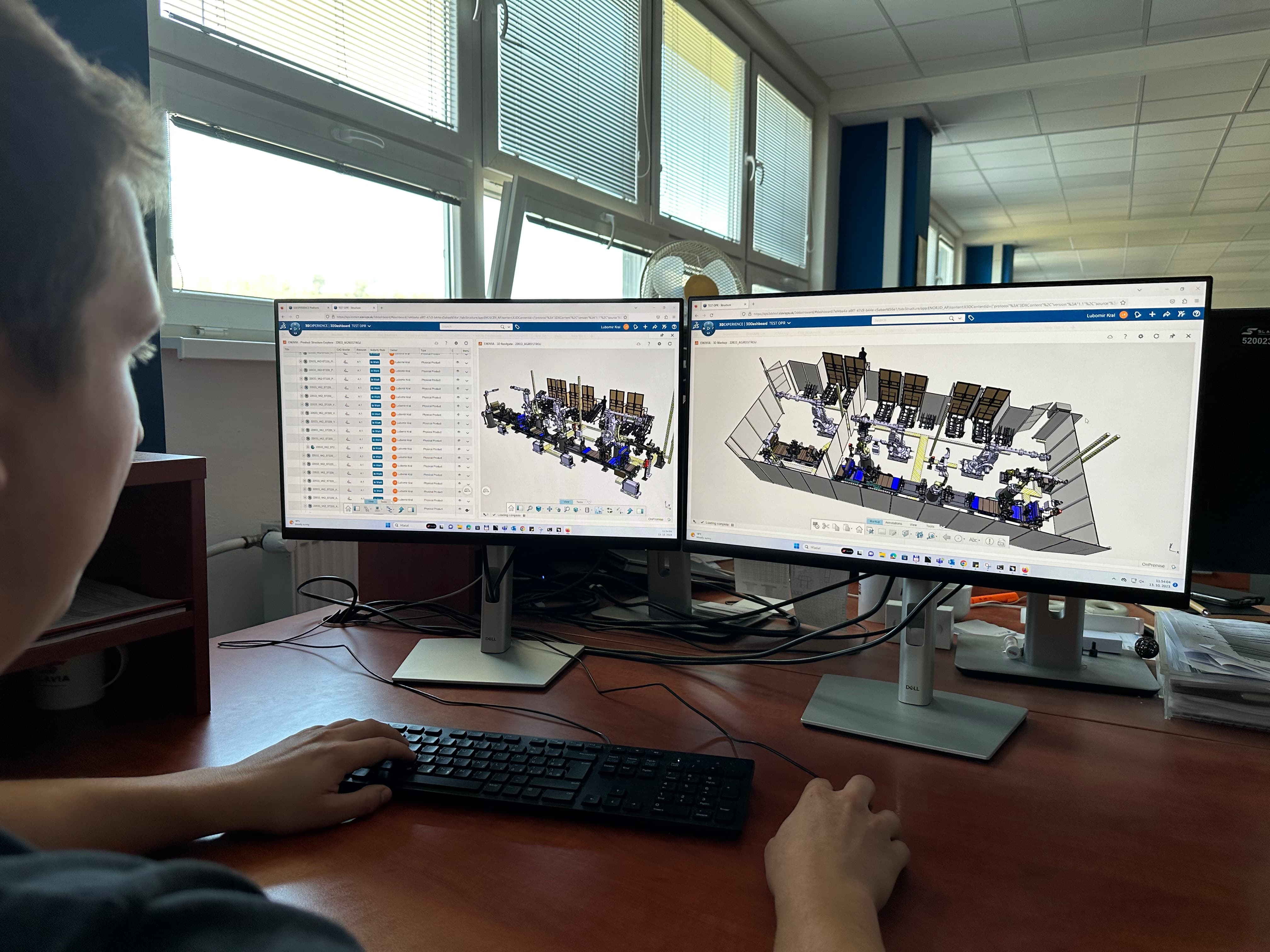
Solution
Chropyňská Group has been a prolific user of Dassault Systèmes’ CATIA V5, so adopting the 3DEXPERIENCE platform – and using Power‘By to link to existing CATIA V5 files – was the most logical next step, not least because one of its daughter companies was using the platform with great success.
Using the value engagement approach, Dassault Systèmes business partner TECHNODAT demonstrated what the 3DEXPERIENCE solution could deliver as a business platform compared with other competitive solutions. For example, it showcased its ability to act as a centralized source of information along with its ability to improve collaboration and improve efficiency. TECHNODAT worked alongside another business partner, Dytron, which showcased the value of DELMIA Ortems for agile planning, scheduling and production.
Benefits
Based on the value engagement activities conducted with TECHNODAT, Chropyňská Group expects to realize multiple benefits by adopting the 3DEXPERIENCE platform.
A unified eBOM which is accessible by all sub-contractors will facilitate the standardization of naming conventions for various parts, while also enabling a customer view that will show the OEM’s naming preference in parallel.
This, teamed with improved collaboration, will enable a more precise quoting process while also facilitating more strategic purchasing capabilities, helping to save at least 2% on material costs, which equates to around €1 million in savings each year.
Numerous benefits will be achieved by implementing a platform that will act as a single repository for all design-related data. Information quality and agility will improve, as will employee efficiency. As a direct result of designers and engineers having faster access to the latest information, Chropyňská Group expects to realize a minimum 10% increase in user effectivity.
Meanwhile, DELMIA Ortems will help Chropyňská Group to utilize its tooling machines more efficiently. With significantly better planning capabilities as well as online production status, the company is less likely to have to unforeseen production requirements, which means it will no longer face uplift payments from suppliers.
The combined benefits will better equip Chropyňská Group for the future, facilitating a more streamlined operation as well as a better experience for employees and customers alike.
Discover more about the Digital Equipment Continuity industry solution experience.
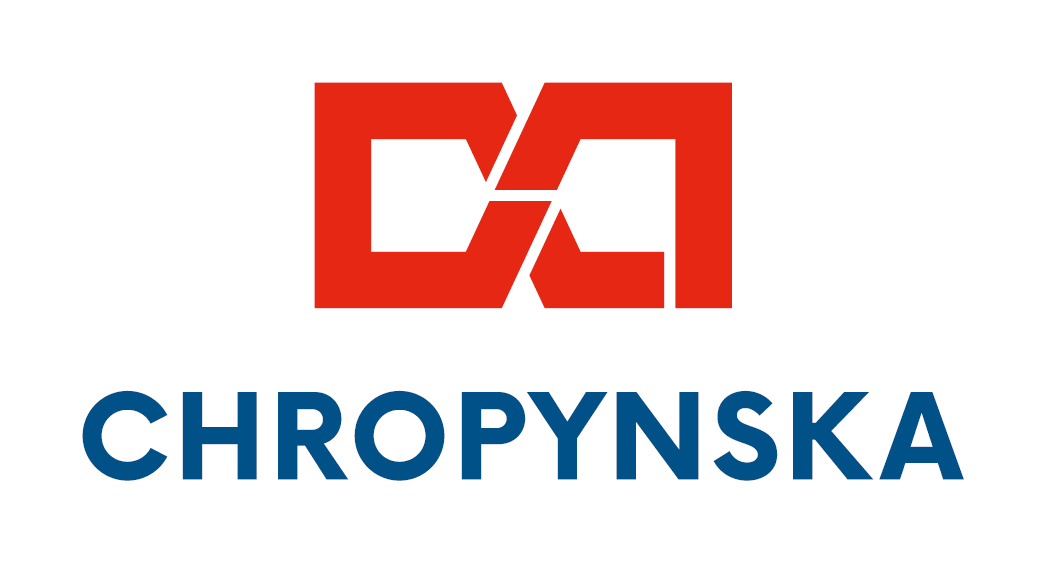
Focus on Chropyňská Group
Established in 1992, Chropyňská Group is a Czech engineering company that supplies industrial assembly lines for automotive companies. The company also provides engineering services and project management. With the biggest in-house fabrication and manufacturing facility in Central and Eastern Europe, the company employees 1,800 people across eight sites. It has installed over 2,000 robotic stations in the last three years, serving over 1,300 customers.
For more information: https://www.chropynska.cz/en/
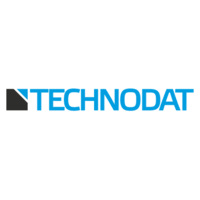
Focus on Technodat
For more than 30 years, TECHNODAT has been a preferred PLM and 3D solutions partner to customers of all sizes and in all industries, helping them develop and manufacture better products and innovative services faster. TECHNODAT provides value-added business consulting services, PLM project implementation and integration, training and support to its 250 customers in the Czech Republic and Slovakia. It is also a leading integrator and distributor of Dassault Systèmes solutions in these regions. TECHNODAT is a founding member of 3DX Alliance, a group of Dassault Systèmes partners with the mission to empower digital transformation for local and global customers across industries with the 3DEXPERIENCE platform.
For more information: https://www.technodat.cz