Test and Validate Your Products Faster with Simulation Solutions on the Cloud
Virtual prototyping and realistic simulation applications that enable users to reveal the world we live in.
Cloud-based simulation for enhanced engineering
What is the best way to help design engineers create the most competitive products?
As it continues to become harder and harder for products to stand out in our global economy, the engineering behind today’s modern products has become increasingly critical. At the same time, products have become increasingly complex, design cycles get shorter making those critical engineering decisions that much more difficult.
SIMULIA on 3DEXPERIENCE platform on the cloud addresses complex product engineering by evaluating the performance, reliability, and safety of materials and products before committing to physical prototypes.
As an integral part of the Dassault Systèmes 3DEXPERIENCE platform on the cloud, the simulation applications for product design can accelerate the product development process while reducing risk and chances of failures.
SIMULIA, powered by the 3DEXPERIENCE platform on the cloud delivers:
- Access to complete, most up to date simulation applications
- Access to virtual, secure, high-performance computing capacity
- Project run & data management capabilities
- Team collaboration tools
- Efficient simulation results analysis tools
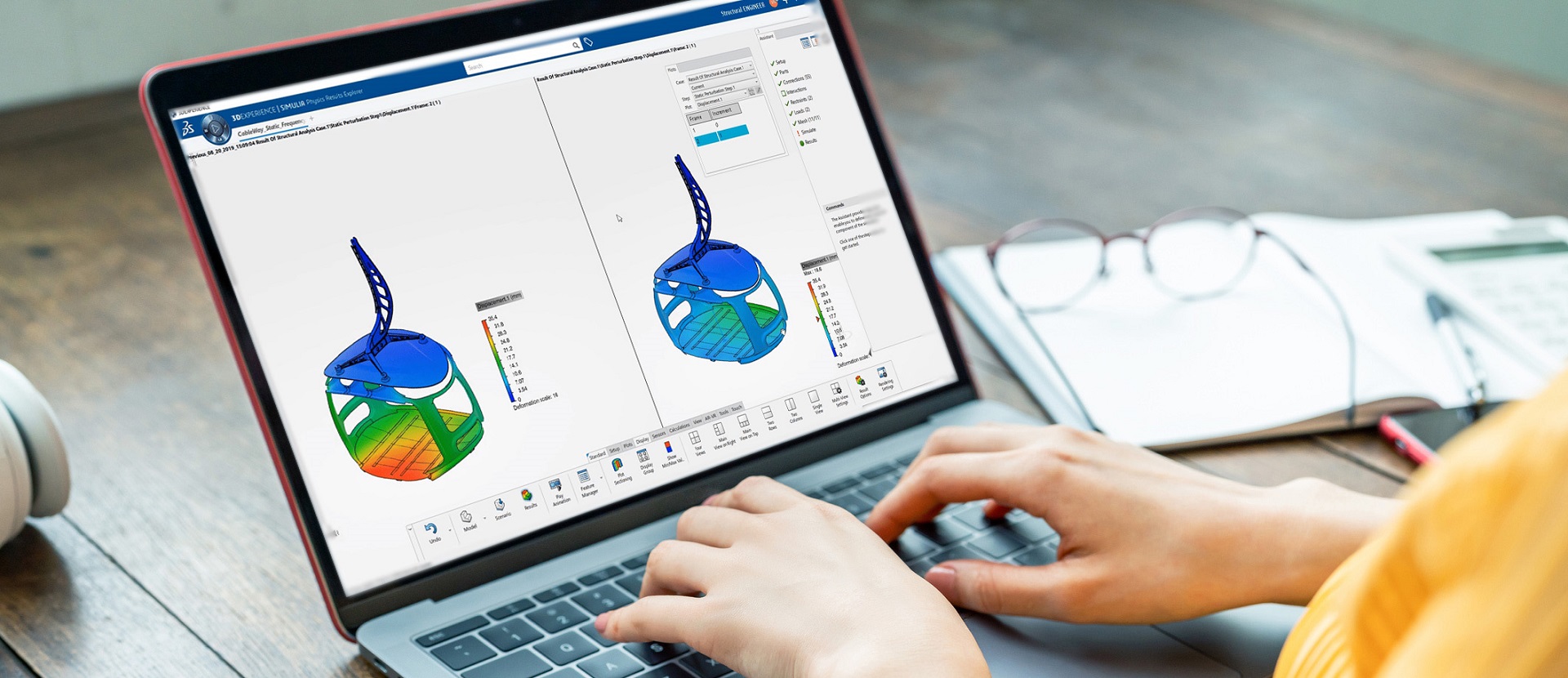
- Structure
- Computational Fluid Dynamics
- Plastic Injection
Structure Simulation
A comprehensive set of structural analysis solutions to guide design decisions and improve product performance and quality.
Assess the structural performance of products under a wide range of loading conditions using simulation.
Delivers unique design workflow in 3DEXPERIENCE with an access to robust simulation technology within an intuitive interface.
Provides a range of capabilities from a simple linear analysis of a single component to a complete simulation of the entire assembly with contact and other non-linearities.
Access up to hundreds of cores*, anywhere, anytime, with the freedom to solve on either local hardware, or free up your workstation and solve friction-free on our cloud compute infrastructure. *Compute configurations tailored to each domain are provided out of the box with no additional setup.
Computational fluid dynamics
Perform fluid flow and heat transfer simulations to improve quality and avoid manufacturing issues.
Explore fluid flow and thermal performance of products to accelerate product innovation.
Delivers unique engineering workflow in 3DEXPERIENCE within an intuitive interface.
Provides a range of capabilities for easily predicting steady-state and long transient flow and thermal behavior of products.
Fully integrated and collaborative multidisciplinary environment.
Access hundreds of compute cores anywhere, anytime with our cloud-computing infrastructure.
Plastic Injection
Validate and optimize injection molded part designs early in the product development process.
Virtually assess the manufacturability and quality of injection molded part designs and tooling.
Leverage easy-to-use simulation to reduce development time and costs.
One application to address the needs for multiple industries, materials, and workflows.
Evaluate effectiveness of mold cooling system designs for the right technical insights at the right time.
Immediate access to 8 compute cores available to use on both your own hardware, or on our compute infrastructure
More than simulation-driven design
The world is moving at a lightning pace and your product development process should move along with it. Across multiple industries, product design relies on multiple cycles of analysis and physical prototyping. Innovation can only happen as fast as silos will allow it. Let's change all of that with MODSIM – unified modeling and simulation-based design.
The strength of unified modeling and simulation
Discover why companies around the world choose SIMULIA 3DEXPERIENCE on the cloud
With simulation and additive manufacturing, it takes around three to four months to create a train… We estimate that our clients can save around 30% in development and running costs. From ideation to production, we are much faster.
Extreme Analyses Engineering
Extreme Analyses Engineering specializes in design and engineering services for the amusement parks and rides sector. The Italian company disrupted the traditional way of working in the industry, taking advantage of the 3DEXPERIENCE platform on cloud to create rollercoaster parts in entirely new ways using simulation and additive manufacturing.
Learn more about cloud simulation solutions
Ready to learn more about our online simulation solutions?
See how the 3DEXPERIENCE platform on the cloud can transform your business.