The Top Challenges in Additive Manufacturing and How to Overcome Them
The Top Challenges in Additive Manufacturing and How to Overcome Them. Learn more now!
Introduction
Additive manufacturing (AM) processes involve adding material until the product is finished. AM is the opposite of subtractive manufacturing (SM), the traditional machine shop methods of cutting away a solid material until the item is completed. 3-D printing is the activity most often linked with additive manufacturing, but it includes technologies such as:
- Extrusion – Material is pushed through a die or an orifice to create a desired shape. Frequent materials used in extrusion are metals, plastics, and composites. Examples of products fashioned by extrusion include pipes, wires, window frames, and aluminum cans.
- Lamination – Combining two or more layers of material. It is often used to protect and preserve documents, photographs, and other materials, adding strength and rigidity. The materials are bonded together using heat, pressure, or an adhesive. Lamination is used in a variety of industries, including printing, packaging, and manufacturing.
- Binder Jetting – A binding agent is incorporated into the process to combine metal, ceramic, or composite powder particles. The powder is spread thinly and then selectively bonded with the binding agent. Binder jetting is relatively quick and can yield complex parts with high accuracy and detail.
- Material Jetting – A 3D printing technology using liquid photopolymer resin cured with UV light. Similar to stereolithography (SLA), material jetting jets droplets of material onto a build platform layer by layer, per a 3D Cxomputer-Aided Design (CAD) file. After each layer is deposited, the material is cured with UV light, producing highly detailed and accurate parts. Material jetting can print in a wide range of materials, including transparent, rubber-like, and flexible resins.
- Direct Energy Deposition (DED) – High-energy beams, such as electron beams, laser beams, and plasma arcs, melt and deposit material in a controlled manner to construct a three-dimensional part layer by layer. This process offers several advantages over conventional subtractive or formative manufacturing methods, such as greater design flexibility, faster processing times, and the ability to produce parts with complex geometries and shapes.
- Powder Bed Fusion (PBF) – Another 3D printing technology that develops complex parts layer-by-layer from powdered metal or plastic. In PBF, a laser selectively melts and fuses small material particles in a powder bed. This process is repeated until the 3D part is produced. PBF can produce parts with complex geometries and intricate details with high accuracy and repeatability.
- Vat Polymerization - A bulk polymerization process in which monomers are added to a vat or container and heated under structured conditions. The heat causes the monomers to react or polymerize and form a polymer. This process allows for forming higher molecular weight polymers than other polymerization processes.
This article explores the challenges (primary, technical, operational, organizational) in the additive manufacturing sector, how to overcome them, and solving the challenges by working with an experienced additive manufacturing partner.
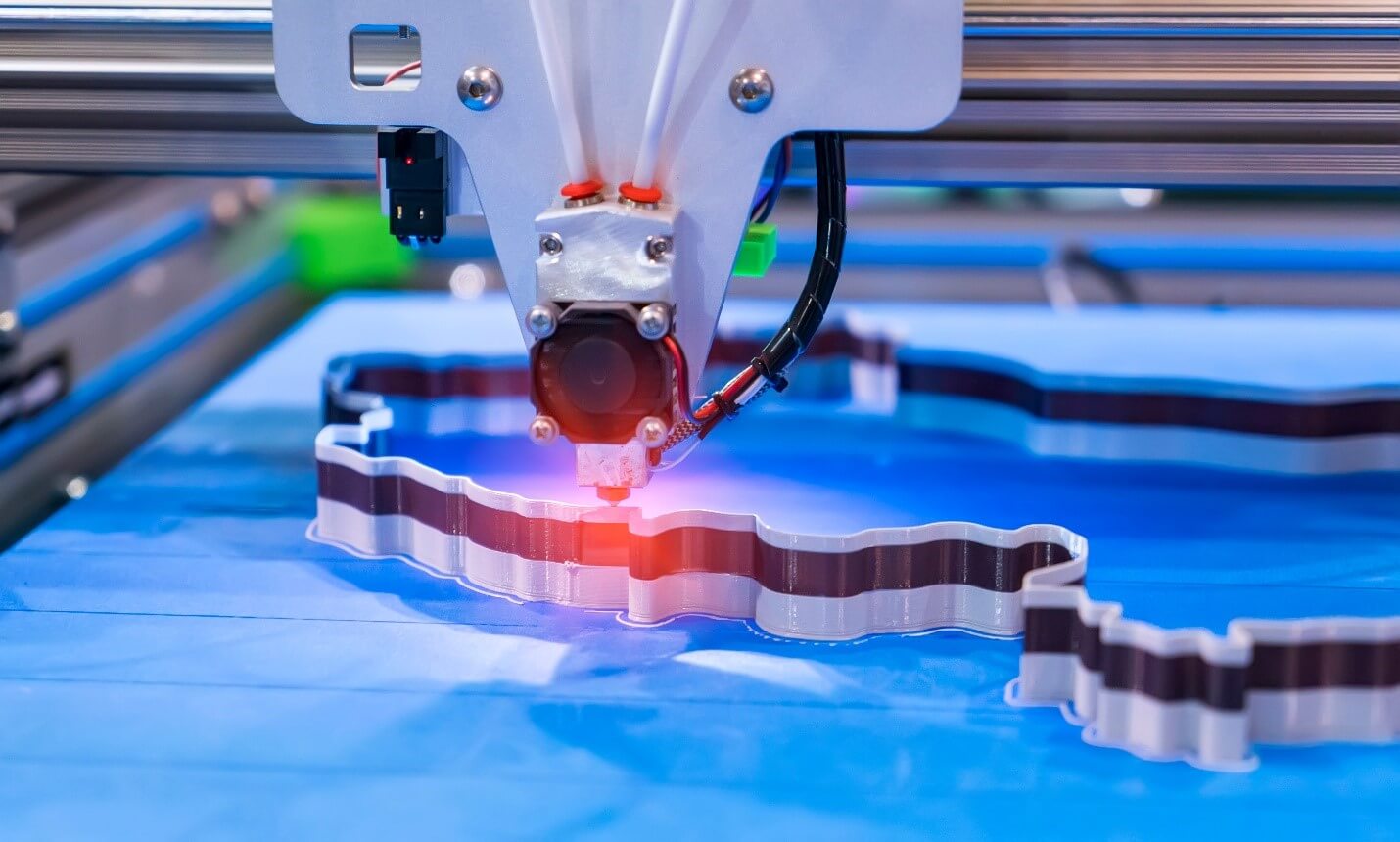
Common Challenges in Additive Manufacturing
There are several opportunities to improve the additive manufacturing arena. These challenges include the following:
- Capital Expenditure – The initial investment for 3D printing equipment is substantial but not nearly as large as traditional subtractive manufacturing methods. The current economic conditions also contribute to the aversion to large capital expenditures. Capital expenditures may be difficult to justify with a foray into a new and dynamic industry. If the intent is to expedite prototypes, traditional accounting methods often struggle to calculate a justifiable payback.
- Maintenance – 3D printer (3DP) technology is evolving, and breakdowns are not uncommon, even with regularly scheduled maintenance. Downtime and maintenance are potential costs that frighten investors. Essential parts may be maintained in inventory due to residual supply chain problems adding to carrying costs.
- Workforce Shortage – Another challenge is the technical expertise to manage and operate the equipment. The market has a huge demand for technical expertise to oversee and operate AM equipment. That expertise may have to be developed internally with outside training, which is a slow process when attempting to justify capital equipment. File conversions and equipment expertise are only a portion of the labor requirements. Depending upon the technology, an operator may need to be on hand to swap filaments mid-print, adjust the settings, remove any support structures ,and perform any post-processing operations.
- Material Availability – Given the relative youth of AM technologies, material availability is far less than traditional manufacturing services. With less material history and a more limited material selection, AM has a vast number of opportunities. Fortunately, AM material development is moving along at a significant pace.
- The AM Environment - For many, a paradigm shift is required to embrace new and rapidly developing technology. Many investors hold out until technological development plateaus and have ironed out all the kinks. These opinions will eventually shift with time and improved materials and technologies.
Technical Challenges to Additive Manufacturing
As with new technology, several technical challenges remain before most manufacturers embrace the AM industry. These include the following:
- Slow Production Speed – 3DP is known for slower manufacturing speeds, preventing the technology from high-scale production applications. Equipment manufacturers understand this shortcoming and are diligently looking at methods to improve production speeds. Selective Laser Sintering (SLS) printers have adopted two print heads to sinter powder faster. Other printer prototypes can reportedly print thirty layers simultaneously rather than one. And some printers have improved speed by as much as 2,000%.
- Automation of Post Processing – Most AM and 3D printed parts require some form of post-processing. This requires additional labor and contributes to overhead costs per unit. Some AM operations require support removal, sanding, cleaning, vapor smoothing, curing, etc. The challenge is to automate these operations with robotics and automated material handling systems.at this time, there has been little post-processing technological development.
- Software – There are limited capabilities in data preparation and design. Companies require the proper digital infrastructure to effectively manage their 3D printing operations. The result is that the industry has been developing workflow management software specifically for 3D printing. This software aids in managing the workflow, including requests, printability analysis, machine analytics, production scheduling, post-processing management, and supplier communication.
- Quality – The part-to-part variation is a concern for many AM technologies. Material composition is a crucial source of variation due to contamination. Some of this is material related, while improper storage and handling is another aspect. Standardized testing is needed to ensure material and handling quality. The ability to monitor the build in real-time with cameras and sensors embedded inside a 3D printer will allow the shift from an open-loop to a closed-loop control system. The closed-loop system enables monitoring of the build in real-time and contributes to consistent geometries, material properties, and surface finishes that support quality.
- Material – Material selection has increased significantly but has a long way to go for the AM sector to overtake existing technologies. There are deficiencies in material information with the lack of a comprehensive material database with established printing parameters and clearly defined specifications. Manufacturers are hesitant to use technology with such informational deficiencies.
- Standards – The industry lacks industry-wide guidelines, including universally understood and accepted standards. Some key players in standards development, like ISO and ASTM International, have established committees dedicated to AM standards development.
Operational and Organizational Challenges with Additive Manufacturing
The new technologies lack precedent for adopting additive manufacturing at the operational level, and there are few business- and cost-calculation models based on AM technology. Digital design ownership is another legal concern that frightens many companies, as does the severe shortage of skilled personnel in the AM fields.
The good news is that the popularity and adoption of AM are growing rapidly. The rapid development of new materials is helping AM to replace many conventional subtractive technologies. Establishing globally accepted AM standards will also help the industry increase its footprint in manufacturing.
Solving Challenges by Working with an Experienced Additive Manufacturing Partner
These concerns can be alleviated by partnering with an experienced 3D printing partner. This step eliminates capital expenditures and the learning curve. A partnership provides access to more additive materials and various post-processing options. In addition to direct partnerships with manufacturers, several distributed manufacturing companies vet local manufacturers and are available to oversee these services.
Get multiple quotes for your parts in seconds