
#01: What Does the Future of Manufacturing Look Like?
Discover how to reduce carbon emissions, adapt to customer needs and embrace manufacturing innovation with digital solutions and new materials.
#01: What Does the Future of Manufacturing Look Like?
Join us in this exciting episode where our experts dive deep into the ever-evolving world of manufacturing. We'll unravel the journey of this industry as it navigates through technological transformation, sustainability and innovation.
Learn how harnessing emerging technologies and nurturing a talented workforce are helping manufacturers tackle sustainability challenges head-on, especially in the era of climate change. Discover more
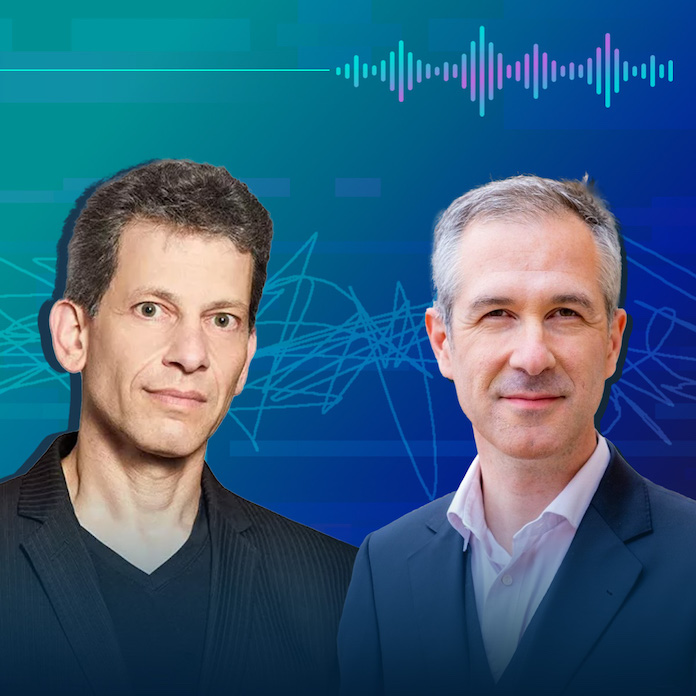
Meet our speakers
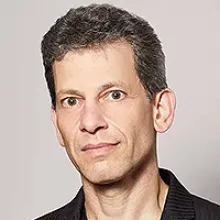
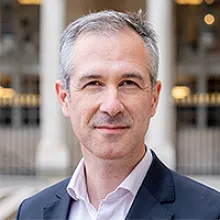
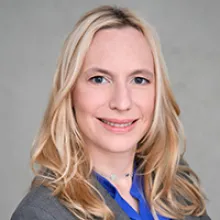
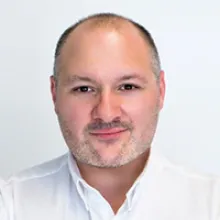
Read the transcript
Narrator: Welcome to Disruptors Unleashed, a new podcast series by Dassault Systèmes that showcases the disruptive technologies shaping our future, and the trailblazers redefining our industries. Every episode will seek to challenge your understanding of what’s possible — because on Disruptors Unleashed, we don’t just adapt to change, we ignite it.
In our first episode, we take a look at unconventional ways to innovate in the ever-evolving world of manufacturing, with our guests: Stéphane Sireau, David Rowan, Florence Verzelen, and Paul Armstrong.
Host: It's possible that no other era in living memory has experienced such radical, rapid and widespread technological change, as the one in which we are now living. It's a period of profound digital transformation. And it should come as no surprise that manufacturers are also finding the way they operate, transformed by new technology.
The possibilities can seem limitless — new materials, new processes, new products, even entirely new business models. In this first episode, we talked to leading industry experts to try and understand the nature of the technological changes, and the skills and attitudes manufacturing industries will need to cultivate if they're to turn new ideas into real innovation.
To start with, however, we must understand exactly what technologies are on the table, and what trends are shaping their deployment. For this, we turn to Stéphane Sireau. Stephane is vice president of high tech industry at Dassault Systèmes, and gives a taste of some of the new technological tools manufacturers are working with.
Stéphane: There are so many new changes happening in the economy today. New materials are a fantastic new scope. One of the items we're working on, for example, at Dassault Systèmes is how do you design a battery? In particular, with the advent of electric vehicles, how do you design the batteries that will power these today and tomorrow? And there's a lot of change here as we move from lithium-ion, typically, to solid state in a few years. And that's just one example of how new materials and new research, will really be able to build this new society that we're building with, in particular, electrification here.
So, we're looking at that, obviously. The semiconductor space is changing very quickly. As we come to the limits of Moore's law, we start looking into what's called more Moore and more than Moore. And here, when you build more advanced packaging, for example, the 3D stacking of wafers, that's yet another example of where new technologies, new modeling capabilities and new simulation capabilities will come into play. And just seeing these kinds of momentous shifts throughout industries.
Host: David Rowan is an investor, founding editor-in-chief at Wired UK, and the author of the book, “Non-bullshit Innovation," so he knows a thing or two about technological change. He too is effusive about the options available to manufacturing industries today.
David: We know that machine learning and artificial intelligence are becoming commodified. We know that there's pressure to create more sustainable materials. We know that there are new ways to interact — metaverses and virtual twins. What it needs is, first of all, creative thinking from hybrid teams on what can become a business. Secondly, new business models to make these businesses viable. And thirdly, behavior change: Adoption by enterprise but also by consumer, customers. And I think in the next decade, we're going to see a transformation in manufacturing.
Host: But how do we really get inside the nature of the opportunities this new technology brings? Well, a great starting point is to look at sustainability. The climate crisis arguably remains the defining challenge of our age and one that continues to provoke countless responses from individuals and businesses. In November 2022, US President Joe Biden identified it as such, vowing, “I will not take no for an answer. I will do everything in my power to clean our air and water, and protect our people's health to win the clean energy future.” The announcement went hand in hand with the Landmark Inflation Reduction Act, which made nearly $400 billion available for climate action. For years, the science of climate change has been clear. But now, the will and the resources needed to turn ideas into actions are beginning to materialize.
Host: Florence Verzelen is the Executive Vice President of Industry, Marketing and Sustainability at Dassault Systèmes. She argues that now is the moment for manufacturers to seize on this breakthrough and implement technologically-driven sustainability transformation.
Florence: First, I think sustainability has been finally understood as a very important issue. Now, we've been talking about sustainability since I was a child. But then, during the last two years in particular, we've seen that people really came to realize that we are in the decade to deliver — that unfortunate, catastrophic climate events are becoming more and more common.
So, if we don't transform where we manufacture and where we use our assets — we are bringing the planet to disaster, and we are not going to leave anything left to your child when he is going to be a grown-up. And I think people finally realized it and understood that they had to transform and that they understood that the transformation would not be so easy.
If you want to go from a product with a lot of carbon to another whole product – from a carbonated company to another whole company – well, it takes a lot of investment and technology to make it happen and make it possible. And then, I think we are seeing a new generation who wants to change the game. And I'm very confident in our children — in the way they want to change the world, to go from product to experience, from a carbon society to a net zero society, and basically, to innovate differently. And last but not least, the technology is finally arriving.
Host: But what technology, exactly? For David, the sky is the limit, and the opportunities for innovative companies to make major changes is growing day by day. He sees sustainability not as a challenge, but as a galvanizing force shaping the future of manufacturing.
David: The killer app at the moment is the urgency of the climate transformation. And I think any organization that wants to move quickly, just needs to tell the story, that what we're doing is going to take toxic materials out of the system, going to minimize energy usage, because I'm seeing so much amazing work in synthetic biology, in precision fermentation when it comes to making food, and using biomaterials, algae to replace leather and remove a lot of the toxic manufacturing process.
The creativity is there, the science is advancing super quickly, and the motivated teams want to come and kill the old way of doing things. The money is there, the capital is there — I think it's creating both that sense of urgency in the way we deploy resources, but also those hybrid teams that collectively know how to adapt these new methods to the old customer needs.
Host: However, if manufacturing industries are to make the most of technology, and transform their businesses to deliver a more sustainable future, then they need to have the skills and workforce to do it. And here we run into a problem. In a 2021 survey from McKinsey, it was found that 87% of businesses are currently facing skill shortages, or expected to do so within the next five years. Stéphane elaborates on the challenge.
Stéphane: The future of workers is the cornerstone of the discussion here. Because if we say, effectively, and if we assume that manufacturing is going through a momentous shift, the next question is, obviously, well, what is the workforce that we need to be able to drive this? Now, many people might say, yes, there's automation coming through; the workforce will increasingly be automated. But what we're really seeing here is that in the end, having a skilled, trained workforce is really what's going to make the difference.
Now, the question is, what should we skill— train that workforce in? And that brings us back effectively to the trend that we've seen over the past couple of decades, which is that manufacturing has... a little bit been left behind when it comes to talent attractiveness. Digital has been on the rise, really attracting a lot of talent here. So, we've really built this new digital continent, and people really have been yearning to work there, for one. Then we've seen a lot of the talents in manufacturing decline, as a lot of the manufacturing has shifted to Asia. But we're seeing a new renaissance in terms of effectively manufacturing in the West, and a lot of need in terms of new skills here. So, there really is a need here for new skills on the manufacturing side.
Host: The problem is, where do these skills come from? Older workers are retiring, and the younger generation is increasingly moving away from a sector they perceive as dirty and polluting, and towards lucrative and glamorous careers in high tech, just at the moment their skills are most in need to facilitate the green transition. And even when workers are willing, there's a gap between the skills produced and the skills the market needs. For example, it may take a student engineer five years to acquire a particular set of skills. In the same five years, the demand for those skills can be superseded by the demand for a different set. The economy never stays still, and traditional institutions can struggle to keep up.
Host: So, what can be done? Well, instead of waiting for graduates to come to them, one solution is for businesses to step in and cultivate the talent they need for themselves. David gives the example being set by corporates in Peru.
David: There is a fundamental gap, though, between the exponential speed of change in industry. You can't say, “I'm not ready for quantum computing.” You can't say, “AI, hold off, we have our old ways of doing things.” You have to move quickly to survive. And traditional institutions like universities and politics play a role because there is a certain way of thinking in allocating resources to universities. So, I'm fascinated by the opportunity for corporates, where the resources and the demand sit to create their own education processes.
For my book, I look at the ways successful incumbent organizations are transforming. I went to Peru and I went to see the biggest conglomerate in Peru called Intercorp, with about 80,000 people, about 4% of the GDP of Peru. They have banks and supermarkets. They have hotels and cinemas. And they couldn't find skilled workers to take the company to the next level. And also, Peru has been a bit of a troubled place and the education system has failed. The leader of this company decided if the state isn't producing education, we're going to have to do it ourselves inside the conglomerate.
So, they started a school system, for-profit, a tiny bit of profit, but affordable enough for the emerging middle class. And then they did the same to create a technical university, where they were teaching the skills that the conglomerate needed. They had the Head of the Telco and the Head of the Industrial Manufacturing part of the company, devising the curriculum, and making sure that the students were getting an education that was right, for tomorrow, not for yesterday. So, I wonder how we can create this incentive system within big industries, not simply to make products that keep the shareholders happy, but to invest in the next generation of talent to make sure in 10 years, the shareholders will be happy.
Host: However, on top of people to move the needle on innovation, manufacturers also need a culture that encourages it. One that finds the right balance between short-term business priorities and long-term transformative change. It's a challenge that can run for even the most successful companies, especially large manufacturers with firmly established processes and infrastructures.
Host: For Paul Armstrong, technology strategist, futurist and founder at a London-based advisory firm, HERE/FORTH, when it comes to encouraging innovation, companies should start by thinking differently, creating an environment where new ideas aren't curtailed by established ones.
Paul: I'm intrigued to see how these new technologies that are sort of emerging at the moment, very much feeling their way out, impact the world of business, because we are living with the potential that remote work is now more popular than ever. Lots of people have downgraded offices and that sort of stuff. So, we've got a lot of societal factors and sort of individual factors now impacting business. And I was doing sort of thought experiments planning for this. And I just thought to myself – wouldn’t it be interesting, if one day, we had a remote innovation arm that was completely decentralized, so their only job was completely removed from your business – they don't see anyone. They don't interact. Their job is just to come up fully remote.
So, you don't employ them full-time — it’s just literally for that for that project. There are a lot of interesting opportunities when you come out... when you sort of remove yourself from what we're used to thinking because of the technologies and what they're enabling to where we can go next. And that's, I think, a very exciting space.
Host: It is also the kind of agility and creativity that David sees in truly innovative organizations.
David: I'll tell you a few things I learned traveling to 20 countries whilst researching — really exciting innovation inside big corporates.
First, the really good ones didn't have an innovation department; they didn't have a Head of Innovation. Innovation was everybody's responsibility because if you were a salesperson, you had feedback on how the customer's needs were changing. So, how do you allow people at every level of the company to feed in these new ideas?
Secondly, they were bold enough to allocate resources to play and explore with no pressure of generating short-term revenue. And that's partly a way of understanding how technology may potentially create new future-facing revenue streams, but with no pressure quarter by quarter to do that.
And thirdly, I often notice that they'd have a small team of pirates inside the organization empowered to do things differently. But for some reason, they weren't shut down by the culture, because they had permission from the people at the top. And I just find it very challenging in a hierarchical organization to get people trying experiments because they're excited about how these new materials could be used to create new products. When the norm of the company is, “No, we use these old materials.”
Host: At Dassault Systèmes, this philosophy of embracing experimentation has been put into practice. The company has set up a dedicated incubator, which looks at developing and promoting startups that could be game changers in the years to come. Florence talks about how the company works to support and develop new and ambitious talent.
Florence: We have an incubator at Dassault Systèmes that's called the 3DEXPERIENCE Lab. And in this incubator, we are working with startups. But we are also asking our teams if they're willing to coach the startups. And the interest for us is that because our teams are coaching the startups, they are in contact with these new ideas, these new ambitions, this new system of thinking, and they bring back into the job these new ideas, and it is extremely powerful.
And of course, some of the startups we help are going to be big, some of them are not. But out of every startup we are approaching, we are going to get very interesting ideas. So that's a good way for us to learn from that system.
And what was super important in this incubator at the 3DEXPERIENCE Lab, is that we made sure it was not just French only — we have an Indian incubator, we have an American incubator and we are working on Asian incubators. Because startups all over the world, depending on where they are, they have different ideas, different ways of thinking, and they're in contact with different ecosystems. So, this connection is of incredible value to us.
Host: David identifies another potential hurdle to effective innovation: the demands of conservative shareholders and investors, whose short to medium-term goals could conflict with the necessities of long-term change.
David: The single biggest impediment to most successful organizations to thinking like this, is shareholders, who expect quarter by quarter, things to be a little better than they were last quarter. And of course, these startups don't have shareholders, they're struggling to raise their funding. And they need metrics that show some progress in order to raise their seed or their Series A round.
Inside an organization, you have to find a way to stop thinking about short-term needs. And maybe it's having a small team inside the company that has the resources to do that experimentation. Maybe it’s decision-making control inside the organization. Often, I've noticed that it's companies that still have a family member in the executive team, or that are still controlled by the founders that can take these old risks.
But it does take courage because essentially, what you're saying to your staff, your stakeholders, your shareholders, is, “Tomorrow, we're not going to be making money, the way we have been for the last X years. But trust me, I'm going to take you there.” That's a really brave thing to say. But this is the moment where you can capture people's excitement, where talent is motivated to build something new in different ways. We've realized that the planet is burning because the last century or two, we kind of got it wrong. This is our one chance, so let's not blow it.
Host: Ultimately, managing these concerns is going to be difficult. Manufacturing industries are large. By nature, it can be challenging to reorient it in the face of new pressures. Sometimes, it can feel like turning a container ship in a canal. But the world around us demands change and action: Action on the climate and sustainability, action on resilience and adaptability, action on meeting our ever-evolving expectations.
This is also a world positively fizzing with new ideas and technologies that will enable these actions. Manufacturing industries can create the right internal conditions and attract the right talent at the right time. Then, they can take advantage of this historic tipping point to become leaner, cleaner and more productive than ever before.
Disruptors Unleashed is produced by Dassault Systèmes. For more episodes, follow us on Apple Podcasts, Spotify, Deezer, or your nearest audio streaming platform. To learn more about Dassault Systèmes, visit us at 3ds.com.
Learn more
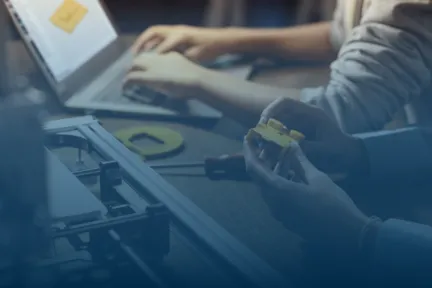
From biodegradable plastics to nanoscale structures, new materials will transform the way we live – if we can develop and produce them at scale.
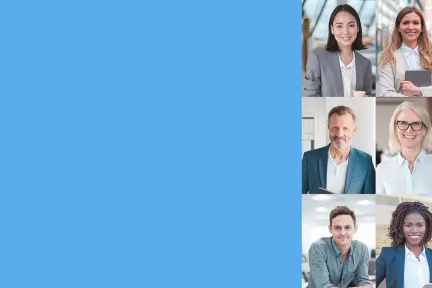
Manufacturers make the world. But the world is rapidly changing. Understanding how best to embrace these changes is crucial to driving innovation and growth over the next decade.
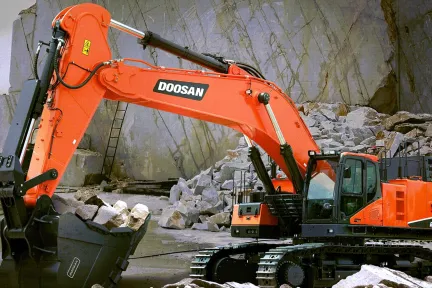
Hyundai Doosan Infracore succeeded in synchronizing manufacturing best practices across multiple global plants with DELMIA Apriso, as part of their journey to build the Factory of the Future.
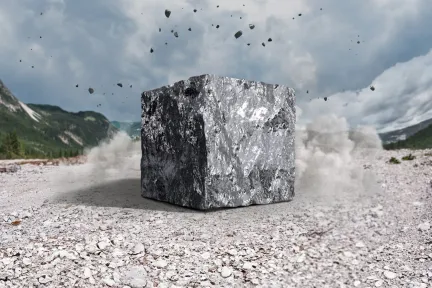
Steel manufacturing is one of the largest contributors to global carbon emissions. Digital solutions will be key in shifting towards green steel for a sustainable future.
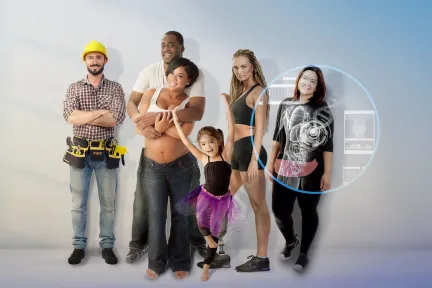
The age of precision medicine has already begun and inaction is not an option.