Identifying The Materials Of The Future
From biodegradable plastics to nanoscale structures, new materials will transform the way we live – if we can develop and produce them at scale.
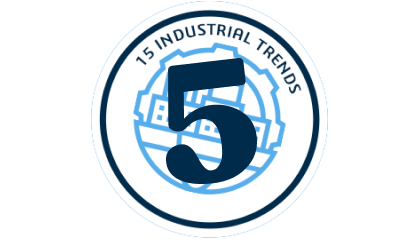
Why should you embrace the materials of tomorrow?
Manufacturing Industries on the Edge: Industries in the innovation age
We are in the midst of a technological revolution. If manufacturers want to be part of it, and reap the benefits, then they need to develop the talent and mindset needed to put innovation at the heart of their enterprise.
What’s happening?
From the stone age to the bronze age, from the iron age to the current silicon age, materials define, at the most fundamental level, what we can do as a technology-using species. There’s a reason that archaeology uses these terms to talk about the past, and that’s because materials define the shape and capabilities of civilization.
And in our present moment, advances in materials science can offer radical solutions to our most pressing challenges – by re-engineering the world up from the smallest possible particles, giving rise to brand new products and innovative manufacturing processes built on the back of new, futuristic materials.
“What is happening in materials innovation is going on at a very small atomic and molecular scale. But it is going to impact our lives on a global scale,” says Philippe Loeb, Vice President, Consumer Packaged Goods & Retail and Home & Lifestyle Industry, Dassault Systèmes. “The products are ultimately just going to be atoms and molecules which were already in existence. It’s just about how they are reimagined and reconfigured with science.”
It’s a field that has seen lively development. From plant-based plastics to cutting-edge nanoscale structures, oxygen-breathing ceramics to new uses for old stalwarts like wood, the materials landscape of the 2020s is an exciting and dynamic one.
It’s getting a big push from governments as well. In November 2022 alone, the UK government announced £95 million (roughly $108 million) in funding for new materials research, including 3D bioprinting for use in tissue engineering and casing for nuclear reactors.
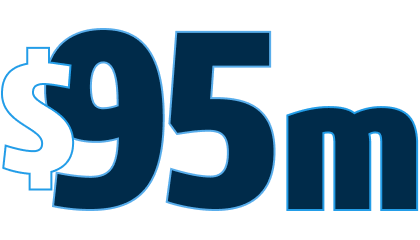
Curious about how other manufacturing industries respond?
Respond to today's challenges with our bespoke solutions
Why does it matter?
New materials aren’t just a gimmick. They are the basis of our future prosperity and will play a critical role in helping us overcome some of the biggest challenges we face today.
Consider sustainability, and the development of sustainable packaging. On a very fundamental level, sustainability is a materials issue: What are we consuming, how are we consuming it, and how can we make our resource use more efficient through the development of responsible product design?
Plastics, for example, are one of the most ubiquitous yet one of the most polluting products in our society – we produce more than 400 million tons of plastic waste every year. However, by transforming our approach to product packaging, we can make plastics and other sustainable materials that can be broken down by bacteria, or can be more readily reused.
It’s also a materials story in other ways. By making materials lighter, stronger, and more flexible, we can create longer lasting products, whilst minimizing emissions and waste.
“The link between materials and energy is an interesting one. Firstly, if we use lighter materials to build vehicles like trucks and planes, we can help limit their fuel use. But we can also change the ways we produce the materials themselves, and take advantage of lower-carbon manufacturing processes,” says Loeb.
Air travel, for instance, is notoriously carbon intensive and notoriously difficult to decarbonize. However, new materials could alleviate that burden – researchers from the University of Cambridge have found that planes built with composite materials (such as reinforced plastics) could emit 20% less CO2 than their aluminum equivalents.
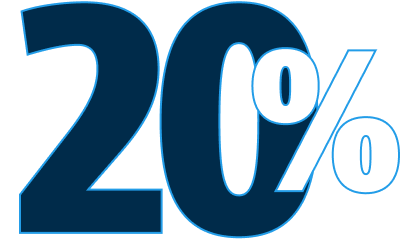
Similarly, Australian advanced composites manufacturer Quickstep has developed a process to produce complex composite materials to the same output standard as traditional methods without the need for slow, energy-intensive, and expensive autoclave machines. This makes it much more possible to utilize these advanced materials within existing aerospace production cycle times.

How can I prepare?
Change is not straightforward and experimenting with new materials is a delicate process: “Just as a chef fine-tunes a recipe with seasoning as they cook it, so too do developers experiment with substances while creating new materials,” says Loeb. “The trick is to understand and model what those changes in composition do, and how they will affect the performance of a material.”
New simulation technologies are helping materials discovery teams perform these experiments in controlled and cost-effective ways. In fact, when it comes to manipulating and working with the microscopic, elemental building blocks of new materials, manufacturers are better equipped than ever before.
“Thanks to modelling and simulation technologies, we are increasingly able to understand how materials react to certain conditions and forces, right down to the atomic scale,” says Loeb. “And thanks to AI and machine learning, these models are getting smarter and more accurate. It’s a pretty unique moment.”
Reformulation can also be critical in helping manufacturers stay ahead of emerging plastics regulations – France banned plastic packaging entirely in February 2022, and relevant industries need to adjust their output accordingly and at speed to stay in the game.
“The materials of the future are going to be much more diverse, and you need to have the capability to better forecast how they behave,” says Loeb. “If you think about metal, when you start to combine what we already know, with a developing knowledge of things like the nanostructure of carbons, there is huge potential.”
A company like Gerberit, for instance, was able to use simulation capabilities to test how it’s ceramic-based products would perform in the real world, and design appropriate molds and manufacturing techniques.
And by making things easier, we also speed up delivery times. Loeb argues, “Simulation technologies will speed up time-to-market for new materials. We will accelerate not only the discovery of new materials, but also the rate at which we scale up production, using new techniques like 3D printing. Which will be essential if they are to fulfill their potential in the industries of the next decade.”
Thanks to modeling and simulation technologies, we are increasingly able to understand how materials react to certain conditions and forces, right down to the atomic scale. And thanks to AI and machine learning, these models are getting smarter and more accurate. It’s a pretty unique moment.
Other Trends
Discover more with our Manufacturing Industries
- Aerospace & Defense
- Consumer Packaged Goods & Retail
- Home & Lifestyle
- High-Tech
- Industrial Equipment
- Marine & Offshore
- Transportation & Mobility
Bridge the gap between the virtual and real world to accelerate from concept to operations
When consumers want it yesterday, be first to make it and first to market.
Pressured to deliver eco-friendly packaging? Balance sustainability and packaging innovation while growing profits with the right strategy on the 3DEXPERIENCE® platform.
Virtual Twin Experiences for Sustainable Innovation – Helping Manufacturers Improve Consumer Products
Integrate product innovation with sustainable design practices on a single platform to lower a product’s environmental footprint with Sustainable Innovation Intelligence.
Simplify and accelerate innovation to create more valuable consumer experiences.
Advanced digitalization helps companies achieve their carbon neutral goals by not only measuring their current environmental impact, but also the impact of future decisions.
Digitalize manufacturing to deliver made-to-order innovation.
Accelerate the path to net-zero carbon with eco-friendly tires powered by the 3DEXPERIENCE® platform.
With optimized manufacturing waste management, Industrial Equipment manufacturers can better achieve their goals for sustainability and a circular economy.
Accelerate the sustainable transformation of the Marine & Offshore industry.
Driving vehicle innovation toward the mobility of the future
THE WORLD NEEDS MANUFACTURERS
A MANIFESTO FOR CHANGE
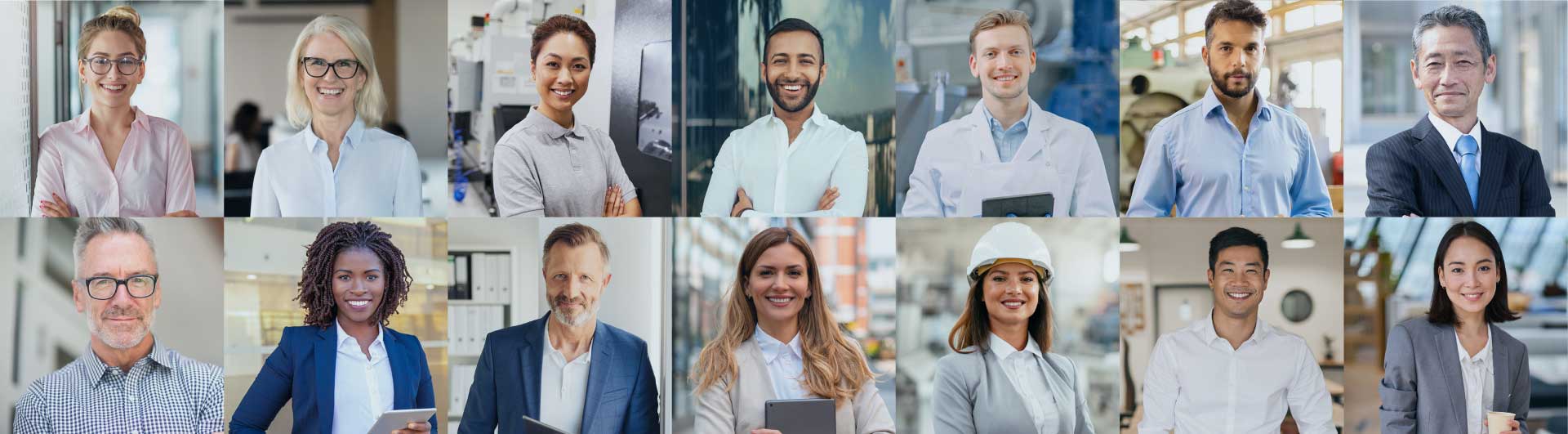